The customization of glass shower doors is a testament to the fusion of aesthetics and precision engineering. Leveraging advanced technologies, manufacturers can deliver products that not only elevate the visual appeal of bathrooms but also ensure safety and durability. As homeowners increasingly seek personalized bathroom designs, understanding the technological processes behind the production of custom glass shower doors becomes essential. This article will explore five key technologies that play a critical role in this manufacturing process.
First, we delve into glass cutting technology, where precise cuts are essential for achieving the desired specifications of a shower door. Next, we discuss glass tempering processes, which enhance the strength and safety of the glass, making it ideal for bathroom use. The role of CNC (Computer Numerical Control) machining is also crucial, as it allows for the meticulous crafting of glass edges and the creation of intricate designs. Additionally, waterjet cutting is highlighted for its ability to cut glass with high precision without introducing thermal stress. Finally, glass coating technologies are examined, which not only protect the glass but also add functional benefits like water repellence and resistance to staining. Each of these technologies contributes to the overall quality and functionality of custom glass shower doors, reflecting the intricate blend of industry expertise and innovative engineering.
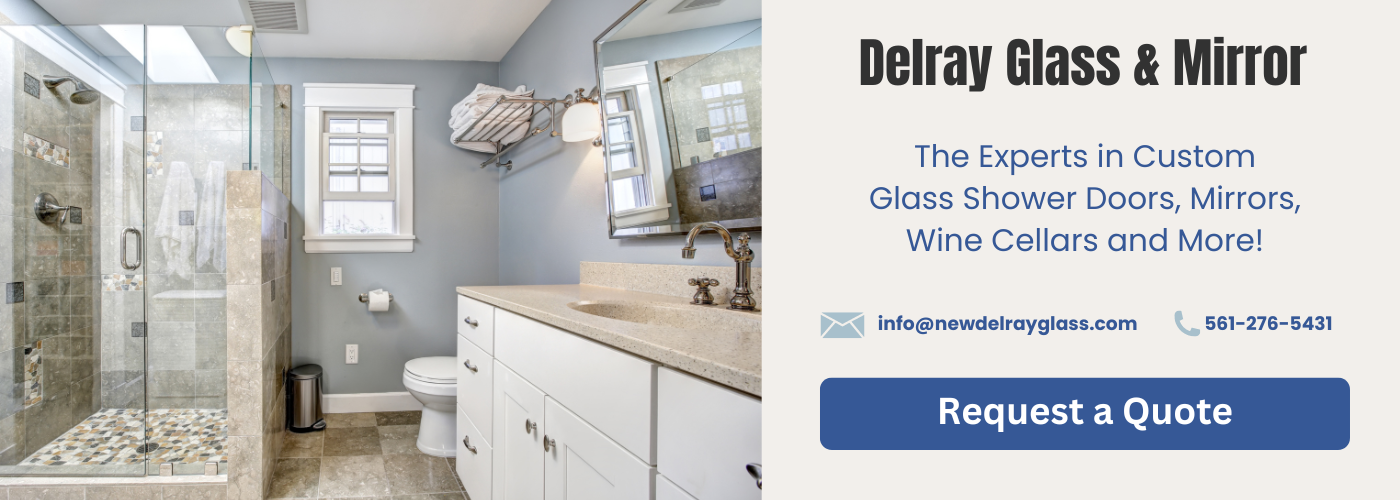
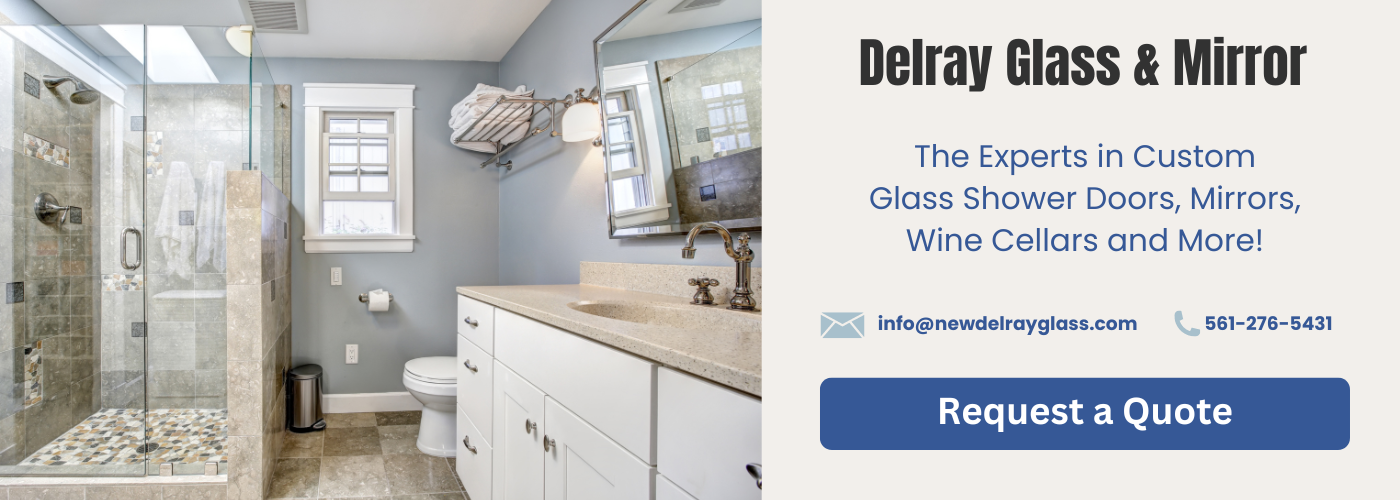
Glass Cutting Technology
Glass cutting technology is a fundamental aspect of manufacturing custom glass shower doors. This process begins with large sheets of glass that are precisely cut into smaller, specific shapes and sizes to fit the design requirements of a shower door. The accuracy of the cutting is crucial, as it ensures that the glass fits perfectly within the frame, maintaining both the aesthetics and the structural integrity of the door.
Modern glass cutting technologies utilize advanced machinery that can include laser cutters and computer-controlled cutting systems. These tools allow for high precision and minimal waste, which is essential for cost efficiency and environmental considerations. Lasers, for instance, can make fine cuts without causing cracks or significant material loss. The precision also allows for intricate designs and edges that are smooth and safe to handle.
Moreover, the introduction of computer-aided design (CAD) software in glass cutting processes has revolutionized the production of custom glass shower doors. CAD software enables designers to create detailed and accurate models of the doors before any physical cutting takes place. This not only minimizes errors but also allows for customization according to customer preferences without significant additional costs.
Overall, glass cutting technology is a key player in the production of custom glass shower doors, providing both the utility and aesthetic appeal that modern consumers demand. Its continual advancement promises even more efficient, creative, and cost-effective solutions in the future.
Glass Tempering Processes
Glass tempering is a crucial process in the manufacturing of custom glass shower doors, enhancing both the strength and safety of the glass. This process involves heating the glass to a very high temperature and then rapidly cooling it. The heating phase typically brings the glass up to around 600-650 degrees Celsius, which makes it malleable and ready for shaping if necessary. Following this, the cooling process is executed swiftly using blasts of air. This rapid cooling method is known as quenching.
The reason behind tempering glass is to imbue it with a balance of internal stresses which significantly increases its strength compared to normal glass. Tempered glass is much tougher and more resistant to impact than regular glass. In the event that it does break, it shatters into small, blunt pieces that are far less likely to cause injury, unlike the sharp shards of untreated glass. This safety feature is particularly important in applications like shower doors, where human contact is frequent and breakage risks must be minimized.
Moreover, tempered glass also withstands considerable variations in temperature, a key characteristic for environments where heating and cooling cycles are common, such as bathrooms. This makes tempered glass an ideal choice for shower doors, which may be exposed to different temperatures and humid conditions. The durability and safety attributes of tempered glass not only meet the strict regulations often required for bathroom fixtures but also assure the user of longevity and reliability in their use.
CNC (Computer Numerical Control) Machining
CNC (Computer Numerical Control) Machining is a pivotal technology in the manufacturing of custom glass shower doors. This process involves the use of computer-controlled machinery to achieve precise cutting and shaping of glass, which is crucial for creating high-quality, custom-fitted glass shower doors. CNC machining provides manufacturers with the ability to execute complex cuts and intricate designs with high precision, which traditional glass cutting methods cannot achieve.
The use of CNC technology in glass machining allows for the customization of shower doors to fit specific dimensions and shapes required by customers. This is particularly important in modern architecture and interior design, where custom glass solutions are often needed to fit unique spaces or achieve a desired aesthetic. CNC machining can handle a variety of glass thicknesses and types, ensuring versatility across different project requirements.
Moreover, the precision offered by CNC machining minimizes the risk of errors and material waste, making the manufacturing process more efficient and cost-effective. It also enhances the safety of the glass by ensuring smooth edges and exact fitment, reducing the likelihood of installation issues or breakages. As technology advances, the integration of CNC processes in glass manufacturing continues to evolve, pushing the boundaries of what can be achieved in custom glass work, including shower doors.
Waterjet Cutting
Waterjet cutting is a vital technology used in the manufacturing of custom glass shower doors. This method utilizes a high-pressure stream of water, often combined with an abrasive material, to cut through glass with precision and minimal risk of breakage. This technology stands out for its ability to cut intricate shapes and details without generating heat, thereby keeping the structural integrity of the glass intact.
One of the key advantages of waterjet cutting in the context of custom glass shower doors is its versatility. The technology can handle varying thicknesses of glass and is precise enough to create complex designs and edges that other cutting methods may struggle to achieve. This precision is particularly important in custom designs where unique patterns and exact dimensions are critical.
Additionally, waterjet cutting is environmentally friendly compared to other cutting technologies. It does not create any hazardous waste and the water used can often be recycled. This method also reduces the likelihood of producing airborne dust, smoke, or contaminants that could compromise the quality of the indoor environment where the glass is being cut.
In summary, waterjet cutting is an exceptional choice for manufacturing custom glass shower doors. It combines efficiency, precision, and environmental sustainability, making it an integral part of the production process for high-quality custom glass items.
Glass Coating Technologies
Glass coating technologies play a crucial role in the manufacturing of custom glass shower doors, enhancing both their aesthetic appeal and functionality. These coatings are applied to the glass surface to confer various beneficial properties such as water repellence, resistance to staining, and ease of cleaning. This technological advancement is vital in environments like bathrooms, where water and soap scum are prevalent.
One of the most popular coatings used is a nano-coating, which effectively makes the glass water-resistant. This type of coating minimizes the adhesion of water droplets to the glass surface by creating a microscopic layer that repels water. As a result, water beads up and rolls off the glass, taking with it dirt and limescale particles. This feature significantly reduces cleaning time and effort, as it prevents the buildup of soap scum and hard water stains.
Additionally, some coatings can also enhance the durability of glass shower doors by making them more scratch and impact resistant. These protective coatings help maintain the pristine appearance of the shower doors for a longer period, thereby extending their lifespan.
Moreover, advancements in glass coating technologies have also allowed for the customization of glass surfaces in terms of their aesthetic properties. Tinted coatings can be used to alter the color and transparency of the glass, enabling a personalized touch that can match any bathroom decor. Furthermore, some coatings offer anti-bacterial properties, which are especially beneficial in maintaining hygiene in the bathroom environment.
In summary, glass coating technologies are essential in the production of custom glass shower doors. They not only contribute to the functional performance by making the doors easier to clean and more durable but also offer a variety of finishing options that enhance the overall design of the bathroom.