The art and technique of sandblasting, a process that uses high pressure to propel sand or other abrasive materials against a surface, is as much a science as it is a craft. One particular area of interest is sandblasting on glass. However, not all glass is created equal; different types of glass have different properties that affect how they interact with the sandblasting process. One key variable in this process is the sandblasting pressure. But what is the optimal sandblasting pressure for different glass types? This question is crucial for both professional sandblasters and hobbyists alike.
This article will explore this topic in detail, beginning with an overview of different glass types and their properties. Understanding the fundamental characteristics of glass types such as annealed, tempered, and laminated is essential in selecting the appropriate sandblasting pressure.
Following this, we will delve into the fundamentals of sandblasting pressure. Understanding its principles will provide a clear context for the relationship between this crucial variable and the type of glass being worked on.
The heart of the matter will be addressed in our discussion on the relationship between glass type and optimal sandblasting pressure. This section will provide insights into how different glass types respond to varying sandblasting pressures.
We will then provide specific optimal sandblasting pressures for different glass types. This will serve as a practical guide for those involved in the sandblasting process.
Lastly, we will discuss the risks and precautions when varying sandblasting pressure on different glass types. Safety should never be compromised, and understanding potential hazards is key to preventing unnecessary accidents. Prepare to delve into the fascinating world of sandblasting pressure and its role in working with various types of glass.
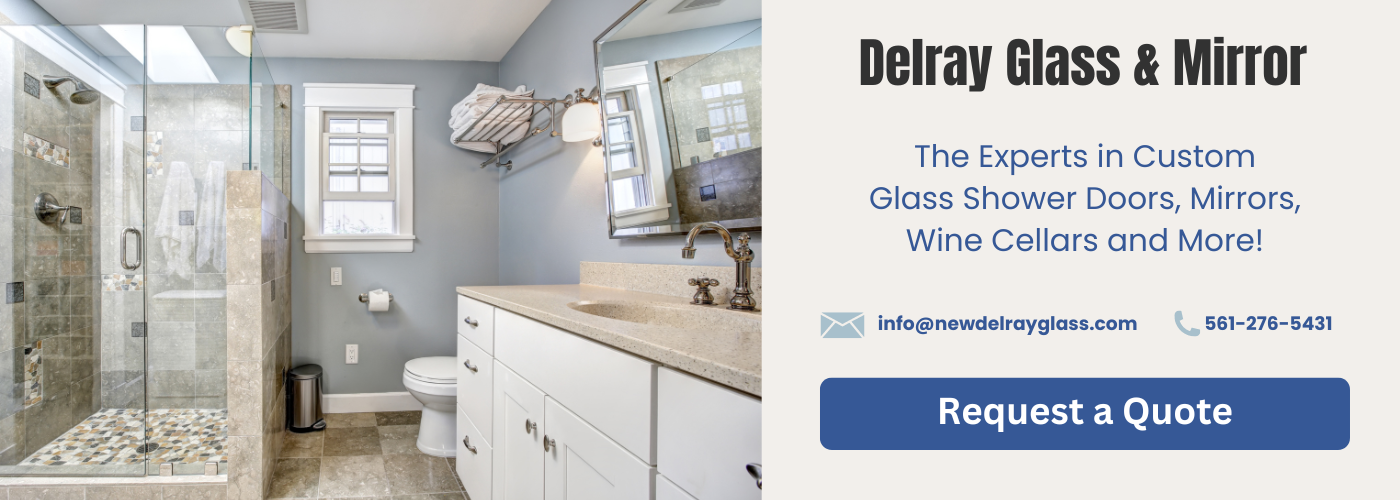
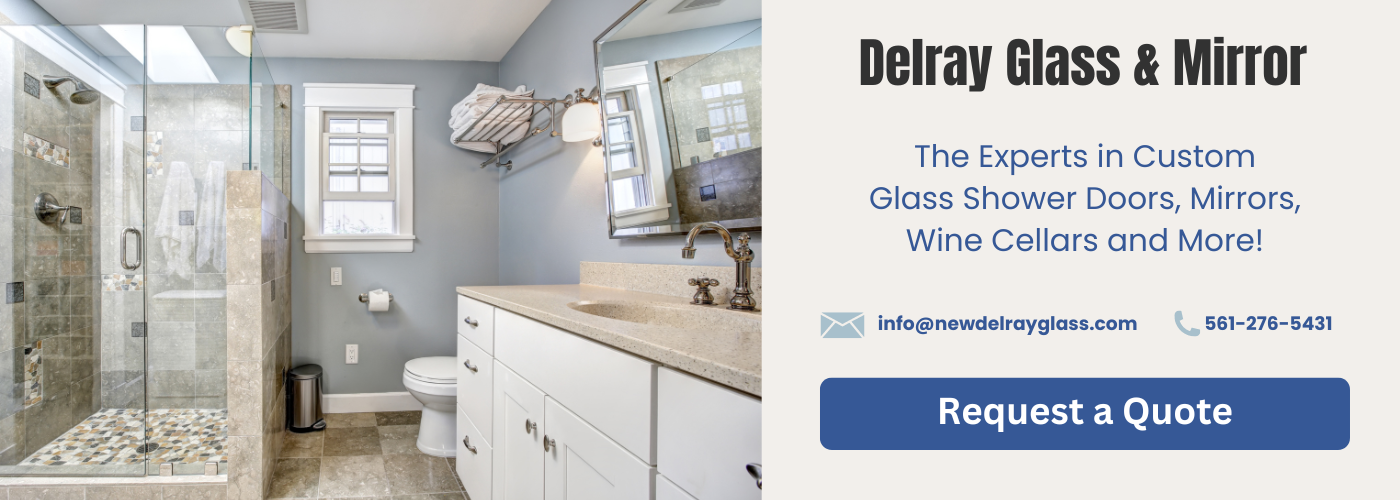
Overview of Different Glass Types and Their Properties
Glass, a versatile and ancient material that has been used for thousands of years, comes in a variety of types, each with their own unique properties. Understanding these different types of glass and their individual properties is critical for a wide range of applications, including sandblasting.
Firstly, there is soda-lime glass, the most commonly used type of glass, often seen in windows and bottles. This type of glass is known for its durability, but it’s also highly receptive to scratches and other forms of damage. It’s made from heating silica, sodium carbonate, and lime to high temperatures, and can be easily molded into a variety of shapes.
Then we have leaded glass, also known as crystal. This type of glass has a high lead oxide content, which gives it a high refractive index, making it sparkle and shine in the light. It’s also more delicate than other types of glass, making it less suitable for applications like sandblasting.
Borosilicate glass, often used in laboratory equipment and cookware, is highly resistant to thermal shock, meaning it can withstand sudden changes in temperature without cracking or breaking. This makes it a popular choice for many industrial applications.
Finally, there’s fused silica glass, which is pure silicon dioxide. This type of glass is extremely resistant to thermal shock and chemical attack, making it ideal for use in a variety of harsh environments. It’s also very hard and has a low thermal expansion coefficient, making it suitable for precision applications.
Each of these glass types has different properties that affect how they respond to sandblasting. The optimal sandblasting pressure for each type of glass will depend on these properties, as well as the desired effect.
Fundamentals of Sandblasting Pressure
Sandblasting, also known as abrasive blasting, is a process that involves the use of high pressure to propel a stream of abrasive material (usually sand) against a surface. The main purpose of sandblasting is to smooth, shape, or clean a hard surface. The pressure used in sandblasting plays a crucial role in determining the efficiency and effectiveness of the process.
The fundamentals of sandblasting pressure are rooted in the principles of physics. The pressure used in sandblasting is the force exerted by the abrasive material per unit of surface area. It is usually measured in pounds per square inch (PSI). The higher the PSI, the more force the sand particles exert on the surface, which can lead to a more aggressive and quicker removal process.
However, the optimal sandblasting pressure varies depending on the type of material being blasted. In the case of glass, a delicate and brittle material, the selection of the right sandblasting pressure is critical. Too high a pressure can shatter the glass, while too low a pressure may not effectively remove the desired material or give the desired finish.
In conclusion, understanding the fundamentals of sandblasting pressure is essential in achieving the optimal result in glass sandblasting. It will help to ensure that the glass is neither under-processed nor over-processed, thus maintaining its integrity and achieving the desired finish.
Relationship between Glass Type and Optimal Sandblasting Pressure
Understanding the relationship between glass type and optimal sandblasting pressure is essential in ensuring the best result when sandblasting. This relationship is complex and influenced by several factors such as the physical properties of the glass, the type of sandblasting machine used, and the desired end result.
Different types of glass have different hardness levels, and this greatly affects the amount of pressure needed for sandblasting. For instance, harder glass types such as quartz and borosilicate glass require a higher sandblasting pressure compared to softer glass types like soda-lime glass. These harder glasses have a higher resistance to abrasion and therefore need a greater force to achieve the desired surface finish.
The optimal sandblasting pressure also depends on the specific sandblasting machine used. Different machines have different capacities, and the pressure must be adjusted accordingly to avoid damage. Too much pressure can cause the glass to crack or shatter, while too little pressure may result in an uneven surface finish.
Lastly, the desired end result also plays a role in determining the optimal sandblasting pressure. If a rough surface finish is desired, a higher pressure may be needed. On the other hand, if a smooth finish is desired, a lower pressure may be sufficient.
Therefore, understanding the relationship between glass type and optimal sandblasting pressure is crucial in achieving the desired results safely and efficiently. It requires a good understanding of the glass properties, the capabilities of the sandblasting machine, and the desired surface finish.
Specific Optimal Sandblasting Pressures for Different Glass Types
The subject of specific optimal sandblasting pressures for different glass types is both broad and complex. In general, the optimal sandblasting pressure for glass varies depending on the type of glass and the desired finish. The type of glass, its hardness and thickness, along with the desired outcome, all play a significant role in determining the optimal sandblasting pressure.
For instance, softer glass types such as soda-lime glass, which is often used in windows and bottles, require a lower sandblasting pressure. Using high pressure could easily damage the glass surface or even shatter it. On the other hand, harder glass types such as borosilicate glass, known for its resistance to thermal shock and chemical corrosion, can withstand higher sandblasting pressures. This allows for a faster and more aggressive sandblasting process, which can be helpful when aiming for deeper etching on the surface.
However, it’s important to note that these are general guidelines, and the optimal sandblasting pressure can also significantly depend on the specific characteristics of each individual glass piece, such as its size and shape, as well as the specific requirements of the job at hand. It’s always recommended to start with a lower pressure and gradually increase it until the desired result is achieved, while constantly monitoring the process to avoid any potential damage.
Furthermore, the choice of sandblasting media can also affect the optimal pressure. Some media are more abrasive than others, which means they can etch the glass more deeply at a lower pressure. Therefore, the combination of the glass type and the chosen sandblasting media should be considered when determining the optimal sandblasting pressure.
In conclusion, understanding the specific optimal sandblasting pressures for different glass types requires a solid understanding of the properties of different glass types, as well as practical experience with the sandblasting process. It’s a delicate balance that requires careful consideration and calibration to ensure the best results.
Risks and Precautions When Varying Sandblasting Pressure on Different Glass Types
The risks and precautions when varying sandblasting pressure on different types of glass are crucial to consider in the sandblasting process. Sandblasting, by nature, is a rough process and can be hazardous if not appropriately managed. The pressure used in sandblasting can greatly affect the outcome and safety of the operation.
Different types of glass have varying levels of resistance to sandblasting pressure. For example, tempered glass is more durable than annealed glass. Therefore, a higher pressure can be applied when sandblasting tempered glass. However, if the pressure is too high, it could still cause the glass to break or damage. Therefore, it is important to know the optimal sandblasting pressure for each type of glass to prevent any accidents or damages.
Moreover, the safety of the operator is also a significant concern. High pressure can cause sand particles to rebound and potentially harm the operator. Therefore, it is important to use protective gear, including goggles, gloves, and a dust mask, during the sandblasting process.
Furthermore, varying the sandblasting pressure can also affect the quality of the finished product. Too high pressure can cause the glass to warp or create an uneven surface, while too low pressure may not effectively remove the desired material from the glass surface. Therefore, it is important to adjust the sandblasting pressure according to the type of glass and the desired end result.
In conclusion, understanding the risks and precautions when varying sandblasting pressure on different types of glass is critical for both the safety of the operator and the quality of the finished product. Proper knowledge and application of these precautions can ensure a successful and safe sandblasting operation.