Impact resistant glass, also known as shatter-resistant glass, is a vital component in many fields, ranging from vehicle manufacturing to construction. Its unique feature of resisting shattering upon impact has made it an essential material in safety-conscious industries. But how exactly does impact resistant glass work? This article aims to explain the composition, physics, manufacturing process, applications, and testing standards of impact resistant glass.
Firstly, we will delve into the composition and structure of impact resistant glass, gaining an understanding of the components that give it its toughness and durability. Next, we will explore the physics behind impact resistance, shedding light on the scientific principles that allow this type of glass to withstand strong forces.
In the third section, we will walk you through the manufacturing process of impact resistant glass. Here, we will uncover how the raw materials are transformed into the robust and resilient glass we use in our everyday lives.
Following this, we will discuss the various applications and uses of impact resistant glass, illustrating its prevalence in many aspects of modern living. Lastly, we will examine the rigorous testing and standards that impact resistant glass must meet to ensure it is safe for use in different settings.
Whether you are a student, a professional, or simply a curious mind, this comprehensive exploration of impact resistant glass will satisfy your curiosity and equip you with a thorough understanding of this fascinating material.
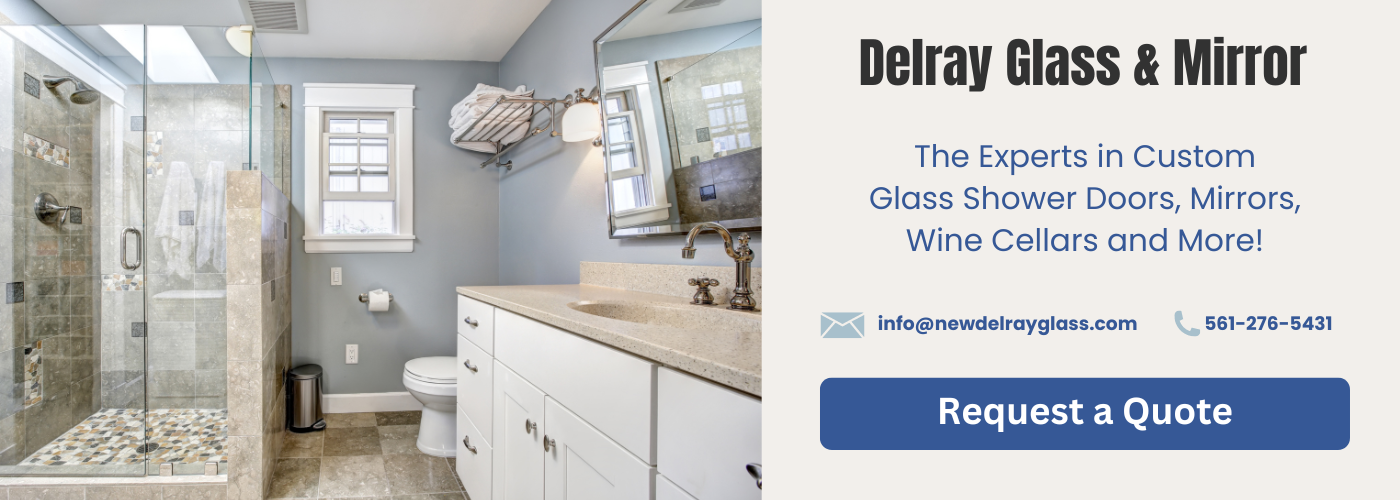
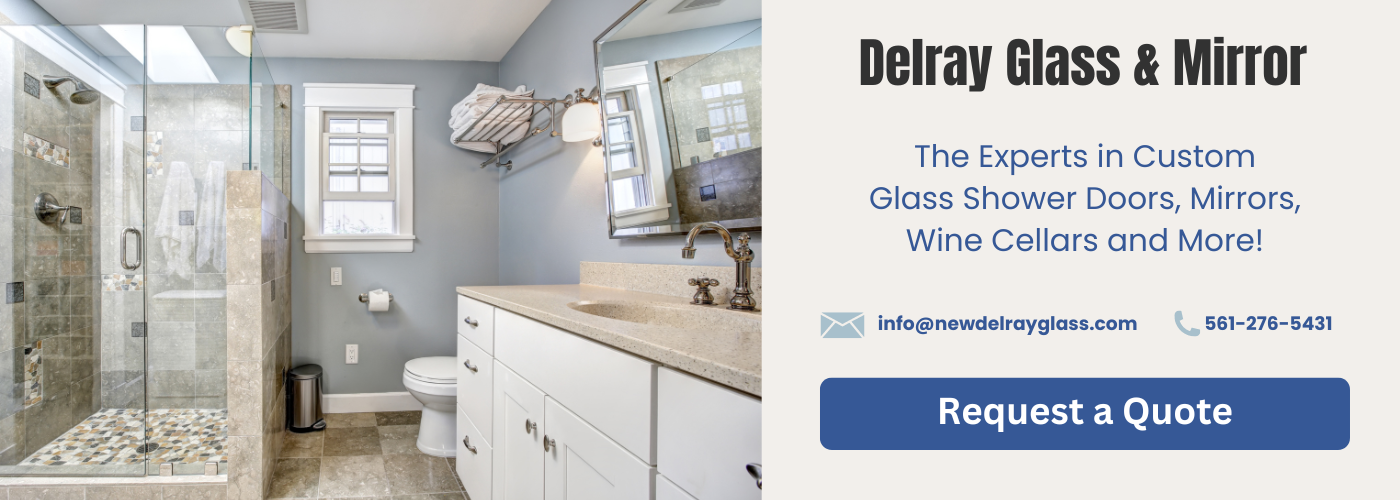
The Composition and Structure of Impact Resistant Glass
Impact resistant glass, also known as safety glass, is an essential material used in various applications where potential threats such as high winds, physical impacts, and security breaches are a concern. It plays a crucial role in ensuring safety and protection, and its robustness is primarily due to its unique composition and structure.
Impact resistant glass is typically comprised of two or more sheets of glass bonded together with one or several layers of a plastic material known as Polyvinyl Butyral (PVB). The glass layers are either heat-strengthened or tempered, making them harder and more resistant to breakage than standard glass. On the other hand, the PVB layer is flexible and can absorb impact energy, preventing the glass from shattering into large, sharp pieces upon impact. Instead, when the glass is damaged, it tends to remain adhered to the plastic layer, resulting in a “spider web” cracking pattern, which is far less dangerous.
The structure of impact resistant glass can vary depending on the specific needs of its application. For instance, for applications requiring a higher level of security or protection against severe weather, the glass may be thicker, or more layers of PVB may be used. The number, thickness, and type of layers used in the glass all contribute to its overall strength and impact resistance.
In conclusion, the composition and structure of impact resistant glass are key elements that contribute to its ability to withstand significant forces. Through a combination of strengthened glass and flexible, energy-absorbing plastic, this type of safety glass provides a reliable solution for various applications where impact resistance is of the utmost importance.
The Physics Behind Impact Resistance
The Physics Behind Impact Resistance primarily revolves around the concept of energy absorption and distribution. When an object strikes the impact resistant glass, the energy from the impact is not concentrated at the point of contact, unlike traditional glass. Instead, the energy is spread out over a larger area which helps prevent shattering.
The secret behind this lies in the unique structure of the impact resistant glass. It typically consists of two layers of glass sandwiching a layer of plastic, usually polyvinyl butyral (PVB). This plastic interlayer acts as a shock absorber. When the glass is struck, the force of the impact is transferred to the plastic layer, which flexes and absorbs the energy, reducing the likelihood of the glass shattering.
Furthermore, even if the glass does crack under extreme force, the plastic interlayer holds the shards in place, preventing them from scattering and causing injury. This is why impact resistant glass is often referred to as safety glass.
This understanding of physics not only makes impact resistant glass safer in the event of an accident, but it also contributes to its effectiveness against burglary attempts. The time and noise involved in trying to break through impact resistant glass often deters potential intruders. It can also withstand extreme weather conditions such as hurricanes, making it a popular choice in regions prone to these natural disasters.
The Manufacturing Process of Impact Resistant Glass
The manufacturing process of impact resistant glass is a complex and intricate procedure that has been refined over many years. The first step involves the creation of two separate glass panels, which are precisely cut to the desired size. These panels are then thoroughly cleaned and prepared for the next stage.
The second stage is the placement of a special layer of polyvinyl butyral (PVB) or ethylene-vinyl acetate (EVA) between the two glass panels. This layer acts as a strong adhesive which bonds the panels together and also provides the impact resistance property to the glass. The glass and the PVB or EVA layer are then heated and pressed together under high pressure. This process ensures a complete and strong bond between the layers and removes any air bubbles that may have been trapped during the placement of the PVB or EVA layer.
The third and final stage involves cooling the glass under controlled conditions. This step is crucial as it helps to strengthen the bond between the layers and also ensures that the glass achieves the desired level of hardness and durability. Once the glass has cooled, it is then inspected for any defects and prepared for shipping.
The manufacturing process of impact resistant glass requires a high level of precision and quality control. Any minor defects or imperfections can have a significant impact on the performance of the glass. Therefore, manufacturers invest a significant amount of time and resources to ensure that each piece of impact resistant glass is manufactured to the highest standards.
The Applications and Uses of Impact Resistant Glass
Impact resistant glass, also known as safety glass, is a product of innovation in the glass industry. It was created with the objective of providing security and safety, and it has found numerous applications in various sectors due to its unique features.
The primary use of impact resistant glass is in the construction industry, particularly in areas prone to hurricanes and storms. It’s commonly installed in windows, doors, and skylights of buildings to protect them from the destructive effects of high winds and flying debris. Specifically, it’s designed to resist penetration, helping to prevent injuries and damage during severe weather conditions.
Moreover, it is also extensively used in the automobile industry. Windshields made of impact resistant glass can withstand high-speed impacts, and even when shattered, the glass pieces tend to stick together, reducing the risk of injuries from glass fragments.
In addition to these, impact resistant glass is utilized in many other sectors such as the aviation industry, nautical sector, and even in mobile devices. It’s used in the crafting of bullet-resistant glass for security purposes and is also found in the screens of smartphones and tablets due to its high durability.
In conclusion, the applications and uses of impact resistant glass are broad and varied, making it an integral part of our everyday lives. Its ability to provide safety and security in different scenarios is what sets it apart from other types of glass.
Testing and Standards for Impact Resistant Glass
Testing and Standards for Impact Resistant Glass form an essential part of the whole production process and usage. These standards ensure the quality and durability of the glass, and the testing procedures verify if the glass can withstand impacts as it should.
Various organizations set the standards for impact resistant glass. These standards determine the specific requirements for the materials, design, and performance of the glass. The goal is to ensure that the glass maintains its integrity and safety during normal use and under extreme conditions.
The testing process for impact resistant glass consists of several stages. The glass is subjected to different types of impacts, including small and large impacts, at varying speeds. In addition, the glass is also exposed to extreme weather conditions to determine its resistance to such conditions. The results of these tests provide a comprehensive understanding of the glass’s resistance capabilities.
Furthermore, these tests and standards are not static and are continuously updated and refined based on new research findings, technological advancements, and real-world experiences. This continuous improvement ensures that impact resistant glass remains effective and reliable in protecting people and properties from different types of impacts.
In conclusion, the testing and standards for impact resistant glass play a crucial role in ensuring its quality, performance, and safety. They instill confidence in users that the glass will perform as expected in different circumstances, whether it’s a minor accident or a major natural disaster.