In the world of construction and interior design, safety and durability are as important as aesthetics. One essential component that strikes a balance between these needs is impact resistant glass. This unique type of glass is specially designed to withstand extreme conditions, making it a valuable asset for various custom projects. However, not all impact resistant glass is created equal. There are various types that are available, each boasting its features, manufacturing process, and customization options.
This article will delve into the different types of impact resistant glass, discussing their characteristics and ideal applications. We will then explore the manufacturing process of these glasses, shedding light on the intricate procedures that ensure their durability and resilience. Customization options will also be covered to help you understand how these glasses can be tailored to fit specific project requirements. Further, we will examine the use of impact resistant glass in different projects, offering real-world examples of their application. Lastly, we will provide a comparative analysis of the performance and cost of various impact resistant glass types, guiding you in making an informed decision for your custom projects.
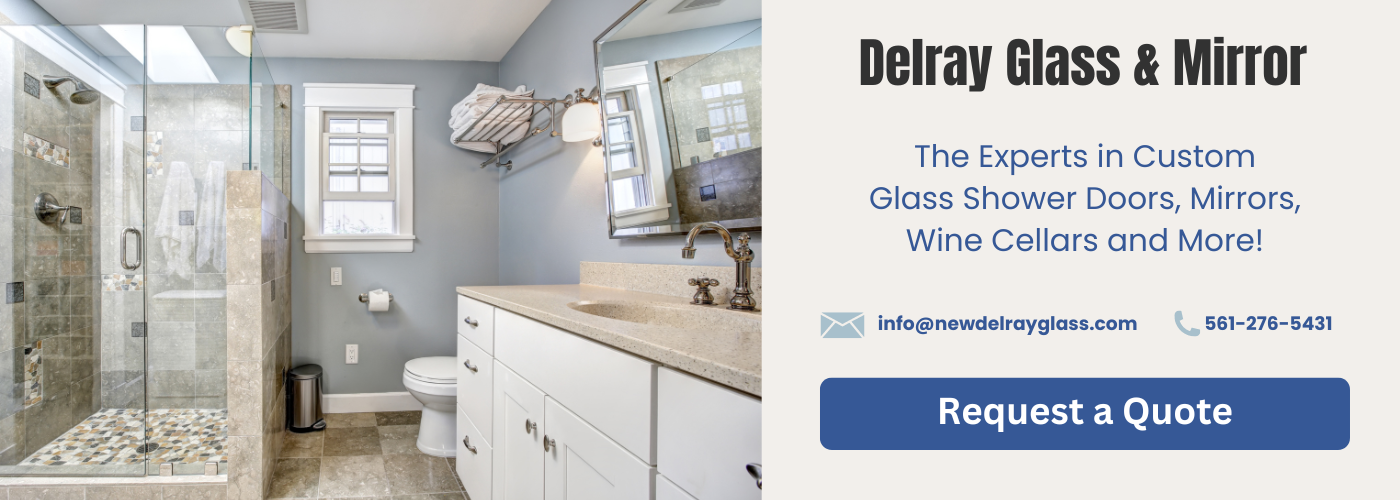
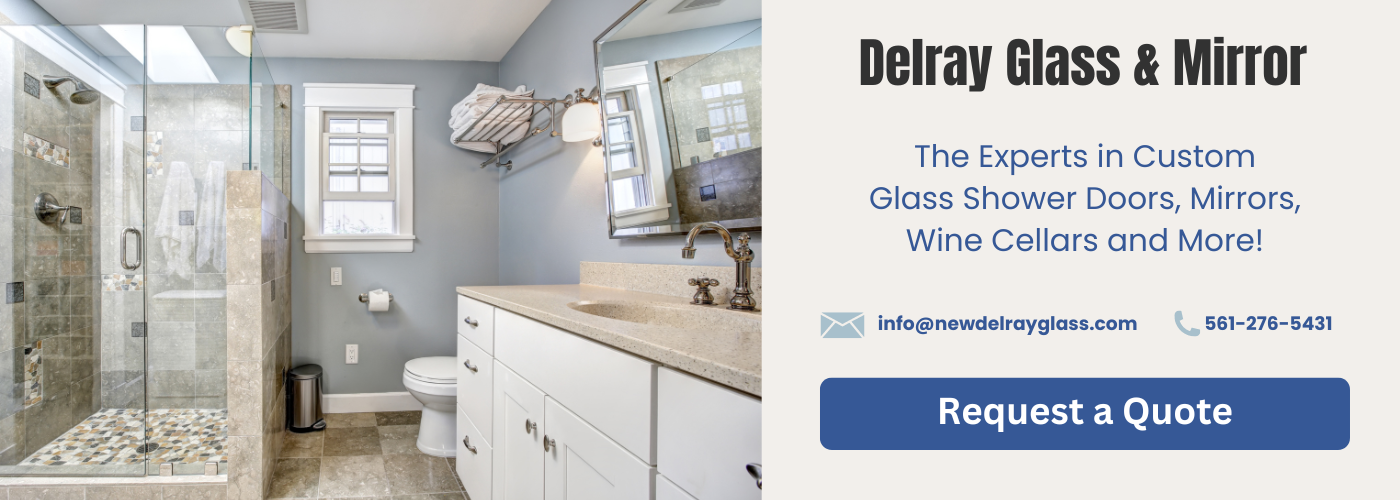
Different Types of Impact Resistant Glass
The world of impact resistant glass is diverse and expansive, offering a myriad of options for custom projects. This particular type of glass is designed to withstand heavy impacts without shattering or breaking into dangerous shards. It is a commendable safety feature that’s used extensively in a variety of sectors, from residential to commercial and even industrial applications.
There are several types of impact resistant glass available for custom projects. One of the most common types is laminated glass. This is made by bonding two or more layers of glass together with an interlayer of plastic. The interlayer holds the glass together if it’s shattered, preventing it from breaking into large, dangerous pieces.
Tempered glass is another type of impact resistant glass. It is treated with heat or chemicals to increase its strength. When it breaks, it shatters into small, granular pieces that are less likely to cause injury.
There’s also a type known as wire mesh glass. This has a network of wire mesh embedded within the glass that holds it together if it’s shattered. It’s commonly used in fire doors and windows because the wire mesh helps prevent the spread of fire.
Polycarbonate and trivex are types of plastic that are often used as impact resistant glass. They are lighter and more impact resistant than regular glass, but they scratch more easily.
In conclusion, the type of impact resistant glass chosen for a custom project depends on the specific needs and requirements of the project. Factors such as safety, durability, and cost all play a vital role in the decision-making process.
The Manufacturing Process of Impact Resistant Glass
The manufacturing process of impact resistant glass is an intricate procedure that requires a high level of precision and quality control. This type of glass is specifically designed to withstand high-impact forces, making it an ideal choice for custom projects that require added safety and durability.
The process begins with the production of the glass layers. These layers are typically made of float glass, a type of glass that is renowned for its superior clarity and uniform thickness. The glass layers are then treated using a process known as tempering, which involves heating the glass to extremely high temperatures and then rapidly cooling it. This process significantly strengthens the glass and makes it more resistant to breakage.
Next, an interlayer made of a plastic material, usually polyvinyl butyral (PVB), is sandwiched between the tempered glass layers. The glass and the interlayer are then subjected to heat and pressure in an autoclave, a type of machine that is designed to provide the right conditions for the materials to bond together. This results in a single piece of glass that is highly impact-resistant.
The manufacturing process of impact resistant glass is not only rigorous but also requires state-of-the-art equipment and skilled professionals. This ensures that the final product not only meets the necessary safety standards but also the specific requirements of each custom project.
In conclusion, the manufacturing process of impact resistant glass is a complex but crucial aspect of its production. By understanding this process, one can appreciate the high level of durability and safety that this type of glass provides. This makes it a highly sought-after material for custom projects that require robust and impact-resistant solutions.
Customization Options for Impact Resistant Glass
Impact resistant glass is a type of glass that is designed to withstand heavy impacts without shattering. This type of glass is often used in areas prone to hurricanes, tornadoes, and other severe weather conditions. It is also commonly used in commercial and industrial settings where there is a risk of heavy machinery or equipment causing damage to the glass.
One of the key features of impact resistant glass is its customization options. This type of glass can be customized in a number of ways to suit different needs and applications. For example, it can be cut to specific shapes and sizes, making it suitable for use in a wide range of projects. This allows for a great deal of flexibility in design and construction, as the glass can be tailored to fit the specific requirements of a project.
In addition to size and shape, impact resistant glass can also be customized in terms of its thickness. The thickness of the glass can be adjusted depending on the level of impact resistance required. Thicker glass can withstand higher levels of impact, making it more durable and secure. This can be particularly beneficial in high-risk environments where the potential for damage is high.
Another customization option for impact resistant glass is the type of tint or coating that is applied to the glass. This can help to enhance the performance of the glass in various ways. For instance, a UV-resistant coating can help to reduce the amount of harmful UV radiation that passes through the glass, while a reflective coating can help to minimize heat gain and improve energy efficiency.
Overall, the customization options available for impact resistant glass make it a versatile and adaptable material that can be used in a wide range of applications. Whether you are looking for a solution for a residential, commercial, or industrial project, impact resistant glass can be tailored to meet your specific needs and requirements.
The Use of Impact Resistant Glass in Different Projects
The Use of Impact Resistant Glass in Different Projects is an extremely significant aspect of the broader topic of impact resistant glass. This particular subtopic delves into the various ways this type of glass can be integrated into diverse projects, showcasing its versatility and utility.
Impact resistant glass has a wide range of uses, owing to its robust properties that provide increased safety and security. One of the primary uses of impact resistant glass is in the construction industry, particularly in regions that are prone to harsh weather conditions or where there is a high risk of seismic activities. Buildings in such areas often incorporate impact resistant glass in their design to shield against potential damage from strong winds, heavy rains, or earthquakes.
In addition, this type of glass is also used in various custom projects such as in the manufacturing of automobiles and aircraft. The windshields of cars and planes, for instance, are made from impact resistant glass to ensure passenger safety, even under extreme circumstances.
Moreover, impact resistant glass is increasingly being used in residential projects. From windows and doors to shower enclosures and glass furniture, the use of this glass significantly enhances the durability and longevity of these structures. Furthermore, owing to its soundproofing capabilities, impact resistant glass is an excellent choice for buildings located in noisy environments.
The use of impact resistant glass in different projects is not limited to these examples. With ongoing advancements in technology and manufacturing processes, the potential applications of this type of glass continue to expand, making it a popular choice for a variety of custom projects.
Comparing the Performance and Cost of Various Impact Resistant Glass Types
Comparing the performance and cost of various impact resistant glass types is a crucial step in selecting the ideal glass for your custom project. Impact resistant glass is a type of safety glass designed to withstand high impact forces. It is commonly used in areas susceptible to severe weather conditions, like hurricanes, or in buildings requiring enhanced security measures.
There are several types of impact resistant glass available in the market, each with its distinctive performance characteristics and cost. This diversity is due to the different manufacturing processes and materials used.
Laminated glass, for instance, is a type of impact resistant glass created by bonding two or more layers of glass together with a plastic interlayer. It is highly durable and provides excellent protection against wind and impact. However, its intricate manufacturing process makes it relatively expensive.
On the other hand, tempered glass is another form of impact resistant glass that is heat-treated to increase its strength. Although it may not offer the same level of protection as laminated glass, it is more affordable and still provides significant impact resistance.
Lastly, there’s also the option of chemically strengthened glass. This type is treated with a chemical solution to increase its surface tension, making it tougher and more resistant to breakage. It falls somewhere in-between laminated and tempered glass in terms of cost and performance.
In conclusion, when comparing the performance and cost of various impact resistant glass types, it’s essential to consider the specific requirements of your project, such as the level of impact resistance needed, budget constraints, and any aesthetic preferences. By doing so, you can ensure that you select the most suitable glass type for your custom project.