Impact-resistant glass, a crucial component in various industries such as automotive, construction, and safety equipment, is meticulously engineered to withstand extreme forces without shattering. This article will delve into the question: How do manufacturers ensure the quality of impact-resistant glass? Understanding the processes and procedures behind the manufacturing of this specialized glass type not only sheds light on its robustness, but it also highlights the level of precision and consistency required to produce such a reliable product.
The first segment of the article will explore the raw materials and production processes involved in the creation of impact-resistant glass. This section will provide an insight into the unique mix of substances and the stages of manufacturing that contribute to the glass’s resilience. This will be followed by an examination of the quality control measures in manufacturing, a critical component in ensuring the durability and reliability of the finished product.
In the third section, we will discuss the role of regulatory standards in guaranteeing manufacturing quality. This will involve a look at various international and local regulations that govern the production of impact-resistant glass, providing a layer of accountability for manufacturers. The fourth part of the article will detail the rigorous testing procedures for impact-resistant glass, which are designed to confirm its strength and durability under different circumstances.
Finally, we will consider the maintenance and evaluation of quality over time. This part will discuss how manufacturers monitor and maintain the quality of their products post-manufacture, ensuring they continue to meet the high standards set by both the company and regulatory bodies. Overall, this article will offer a comprehensive understanding of the meticulous process behind the manufacturing of quality impact-resistant glass.
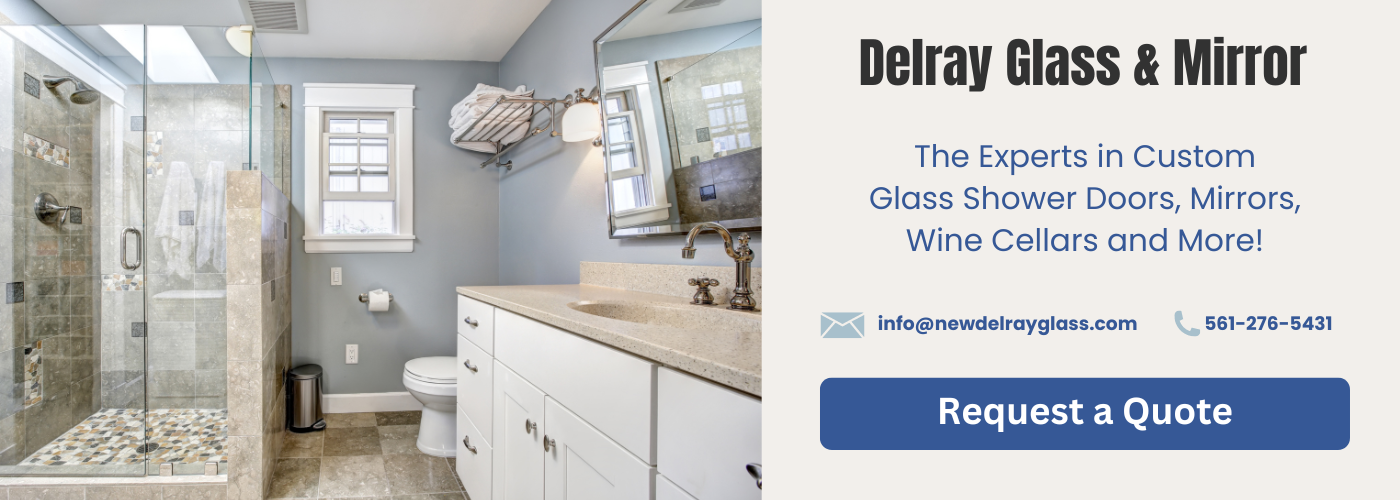
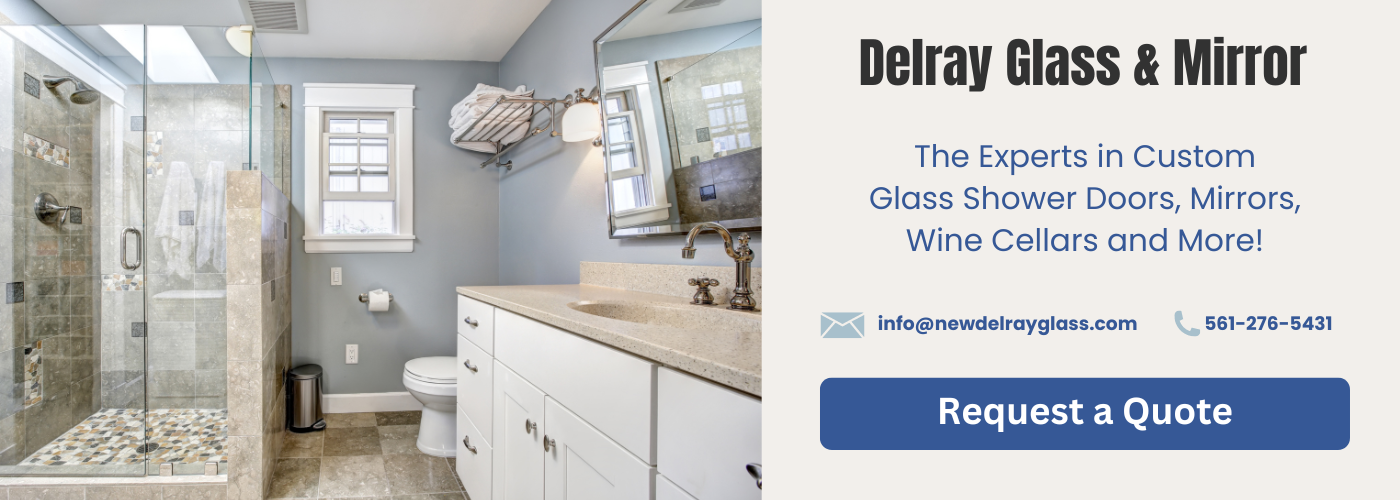
Raw Materials and Production Process of Impact Resistant Glass
The production of impact resistant glass starts with the selection of high-quality raw materials. This includes silica sand, soda ash, dolomite, limestone, and cullet. These components are carefully chosen and measured to ensure the final product possesses the desired characteristics, such as strength, clarity, and impact resistance.
The production process itself involves numerous stages. First, the raw materials are melted together in a furnace at extremely high temperatures. The molten glass is then poured onto a molten tin bath where it spreads out and forms a flat surface due to gravity and surface tension. This process, known as the float process, results in a sheet of glass that has uniform thickness and a highly polished surface without the need for grinding and polishing.
Once the basic glass sheet is formed, it undergoes further treatments to increase its impact resistance. One common method is thermal tempering, where the glass is heated to a high temperature and then rapidly cooled. This process puts the outer surfaces into compression and the interior into tension, which strengthens the glass and makes it more resistant to breaking. Another method is laminating, where two or more layers of glass are bonded together with a tough plastic interlayer. The interlayer holds the glass together if it’s shattered, offering additional safety and impact resistance.
The raw materials and production process of impact resistant glass are critical factors that manufacturers focus on to ensure the quality of the final product. By using high-quality inputs and following stringent production procedures, they can produce glass that not only meets but often exceeds the required safety and performance standards. These steps form the basis of the quality assurance process for impact resistant glass.
Quality Control Measures in Manufacturing Impact Resistant Glass
Quality control measures in the manufacturing of impact resistant glass play a significant role in ensuring the final product meets the required standards of safety and durability. These measures vary from one manufacturer to another, but they generally follow a similar pattern, all aimed at ensuring the premium quality of the end product.
One of the most common quality control measures is the thorough inspection of raw materials. Manufacturers ensure that all the materials used in the production process, such as glass, plastic interlayers, and coatings, meet the specified standards. This step is crucial in preventing defects and ensuring the production of highly resistant glass.
The production process itself is also under strict quality control measures. Manufacturers use advanced technology and machinery to ensure precision and consistency in each step of the manufacturing process. This includes the careful layering of glass and plastic interlayers, as well as the use of heat and pressure to bond these layers together.
Moreover, manufacturers conduct routine checks and tests throughout the production process. These checks ensure that the product aligns with the predefined specifications and any deviations are corrected immediately. It also provides an opportunity to identify and rectify any potential issues before the final product is released.
Lastly, manufacturers also rely on external audits and certification from recognized bodies to validate their quality control measures. These certifications not only provide assurance to the customers but also helps in maintaining the standards of the industry.
In conclusion, quality control measures in the manufacturing of impact resistant glass are comprehensive and rigorous. They ensure that the product can withstand high impacts without shattering, thereby ensuring the safety and security of the users.
Role of Regulatory Standards in Ensuring Quality
The role of regulatory standards in ensuring the quality of impact resistant glass is pivotal. These standards, set by recognized industry bodies, provide guidelines and requirements that manufacturers must adhere to in the production of impact resistant glass. They serve as a benchmark for quality, ensuring consistency across various manufacturers and products.
Regulatory standards often specify the types of materials to be used, the production process, and the acceptable levels of performance for the finished product. Their aim is to ensure that the impact resistant glass produced is of high-quality and reliable. To comply with these standards, manufacturers often have to undergo regular audits and inspections.
These standards not only ensure the quality of the impact resistant glass but also its safety. They often include criteria for impact resistance, ensuring that the glass can withstand specified levels of force without shattering. This is crucial in applications where impact resistant glass is used, such as in automotive windshields or protective glass in buildings.
In essence, regulatory standards play a crucial role in maintaining the quality and safety of impact resistant glass. They provide an objective measure of quality that manufacturers must adhere to, ensuring that consumers can trust the products they purchase.
Testing Procedures for Impact Resistant Glass
The testing procedures for impact resistant glass are critical in ensuring its quality. Manufacturers conduct rigorous testing to ensure that the glass is capable of withstanding high impacts and extreme conditions. These tests are designed to simulate the kinds of stresses that the glass would face in real-world situations, such as natural disasters or accidents.
The first step in the testing process is usually the ‘impact test’. This involves hitting the glass with a heavy object or applying a sudden force to it, and observing how the glass responds. If the glass shatters or cracks easily, it is not considered impact-resistant. If it withstands the impact without significant damage, it passes the test.
Another important test is the ‘pressure cycling test’. This test involves applying and then releasing pressure on the glass repeatedly, in cycles. This simulates the effect of wind blowing against a window during a storm, for instance. The glass needs to withstand this cycling without cracking or breaking to pass the test.
In addition to these tests, manufacturers also often conduct ‘penetration tests’. This involves trying to penetrate the glass with various objects, to see how well it resists penetration. This can simulate situations such as attempted break-ins, or flying debris during a storm.
All these tests are carried out in controlled laboratory conditions, to ensure consistency and accuracy. They are crucial in ensuring that impact resistant glass lives up to its name, and delivers the safety and protection it promises.
Maintenance and Evaluation of Quality Over Time
Maintenance and Evaluation of Quality Over Time is a critical subtopic when discussing how manufacturers ensure the quality of impact resistant glass. This process involves periodic assessments and check-ups to ensure that the quality of the glass remains consistent and reliable over its lifespan.
Manufacturers often employ a combination of manual inspections and automated monitoring systems to track and evaluate the state of their impact resistant glass products over time. These evaluations may include visual inspections, physical tests, and performance assessments under varying conditions. The data gathered from these evaluations are then used to identify any potential issues and implement necessary corrective measures.
Maintenance is another crucial aspect of this process. Regular cleaning, appropriate handling, and other preventive measures can significantly enhance the durability and longevity of impact resistant glass. Manufacturers often provide detailed maintenance guidelines to consumers to ensure that the glass performs optimally throughout its lifespan.
In conclusion, the maintenance and evaluation of quality over time is a critical process in ensuring the quality of impact resistant glass. This process enables manufacturers to deliver a product that not only meets the initial quality standards but also maintains its performance and reliability over time.