The ever-growing demand for safer, stronger, and more durable construction materials has led to the rise of impact resistant glass. This type of glass is known for its ability to withstand high levels of stress, making it an ideal choice for buildings in disaster-prone areas. However, despite its clear advantages, questions have been raised about the environmental footprint of its production process. This article explores the environmental impacts associated with the production of impact resistant glass.
Our first section delves into the manufacturing process of impact resistant glass. What steps are involved? How do these processes differ from the production of ordinary glass? By exploring these questions, we can identify potential environmental issues at the production stage.
Next, we examine the energy consumption and emissions during the production process. Factories that produce impact resistant glass require a significant amount of energy. This energy usage, and the emissions that result from it, can have a profound impact on the environment.
The third section discusses the extraction of raw materials required for the production of impact resistant glass. We will look into the environmental implications of extracting these resources, including potential habitat destruction and pollution.
In the fourth section, we focus on waste management during the production of impact resistant glass. The process of making this kind of glass inevitably generates waste, so it’s crucial to examine how this waste is managed and what environmental impacts it might have.
Finally, we look at the lifespan and recyclability of impact resistant glass. These factors can significantly affect the overall environmental footprint of the product. Can impact resistant glass be recycled? If so, how efficient is the process? These are some of the questions we will address in this part of the article.
By understanding the environmental impact at different stages of production, we can determine the overall footprint of impact resistant glass and explore potential solutions for mitigating these impacts.
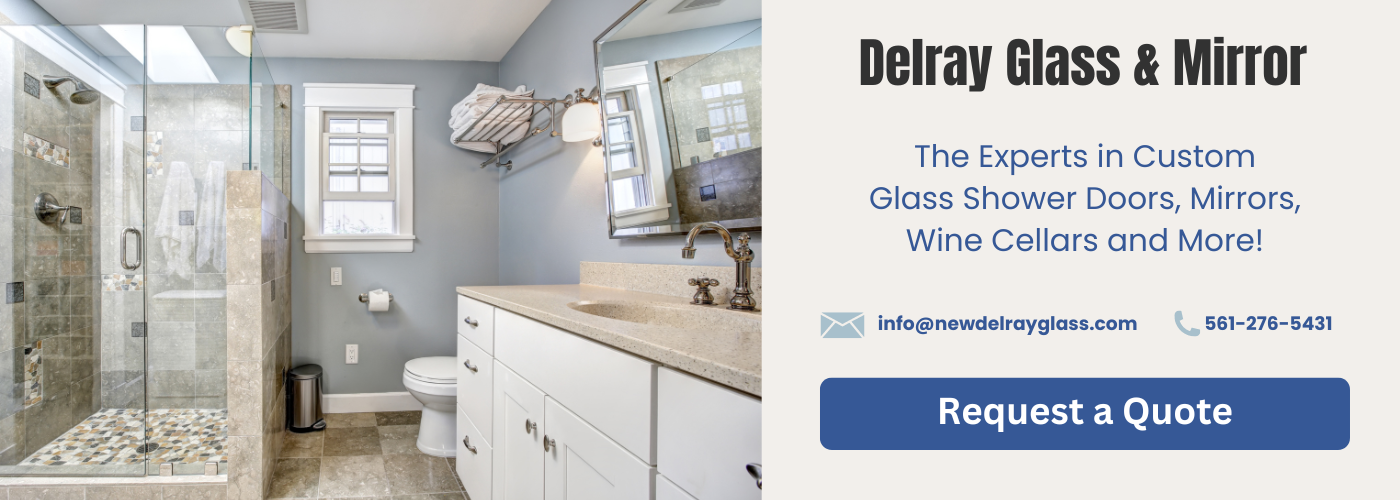
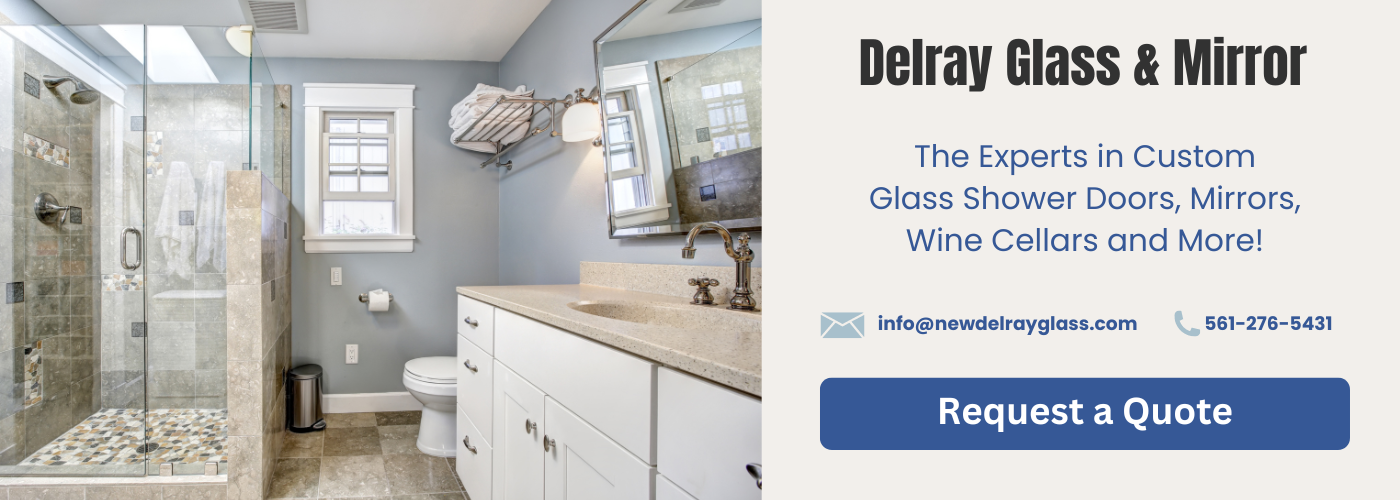
Manufacturing Process of Impact Resistant Glass
The manufacturing process of impact resistant glass is an intricate one that involves several steps. It begins with the procurement of raw materials, such as silica sand, soda ash, and limestone. These materials are then melted together in a furnace at extremely high temperatures to create a molten glass mixture. The molten glass is then shaped, cooled, and cut into the desired sizes.
The next stage in the manufacturing process is the lamination. This involves applying a layer of polyvinyl butyral (PVB) or ethylene-vinyl acetate (EVA) between two sheets of glass. The purpose of this layer is to hold the glass together in the event of a break. The laminated glass is then subjected to heat and pressure in an autoclave, which causes the interlayer to bond tightly to the glass.
Despite the fact that the manufacturing process of impact resistant glass is quite energy-intensive, it is important to note that it results in a product that can significantly enhance the safety and security of buildings and vehicles. Moreover, the use of impact resistant glass can also contribute to energy savings by reducing the need for heating and air conditioning.
However, there are also environmental impacts associated with the manufacturing process of impact resistant glass. These include the emissions produced during the melting and shaping of the glass, as well as the energy consumed during the lamination process. In addition, the extraction of raw materials can also have environmental impacts, such as habitat destruction and biodiversity loss. Therefore, it is crucial to find ways to minimize these impacts and make the production of impact resistant glass more sustainable.
Energy Consumption and Emissions in Production
The production of impact resistant glass, like any other industrial process, involves significant energy consumption and emissions. The energy consumption is primarily due to the high temperatures required in the melting process of glass production. This energy is typically derived from non-renewable sources such as coal and natural gas, leading to the release of greenhouse gases.
The emissions in the production of impact resistant glass are not just limited to carbon dioxide. Other harmful gases such as sulfur dioxide, nitrogen oxides, and particulates are also released. These pollutants contribute to air pollution, which can have detrimental effects on the environment and human health.
Furthermore, the production of impact resistant glass involves the use of certain chemicals to enhance its properties. These chemicals, if not properly managed, can be released into the environment, causing further damage.
In order to mitigate these environmental impacts, it is important to implement energy-efficient technologies and processes in the production of impact resistant glass. Additionally, proper waste management and emission control measures should be taken to minimize the release of pollutants into the environment.
Raw Material Extraction and Its Environmental Impact
Raw Material Extraction and Its Environmental Impact is a vital aspect to consider when discussing the environmental impacts associated with the production of impact resistant glass. This process entails the extraction of raw materials such as silica sand, soda ash, limestone, and cullet from the earth, which are the primary components used in the creation of this type of glass.
Extraction of these raw materials can have significant environmental implications. For instance, mining silica sand can lead to the destruction of habitats and cause soil erosion, which can negatively affect biodiversity. Additionally, the extraction process can lead to the release of dust and other pollutants into the air, contributing to air pollution. It is also worth noting that the extraction process can consume a significant amount of energy, which can result in increased greenhouse gas emissions if the energy sources are non-renewable.
Moreover, the transportation of these raw materials from the extraction sites to the manufacturing facilities can also have environmental impacts. This includes the consumption of fossil fuels and the emission of greenhouse gases. It is therefore essential to manage and regulate the extraction and transportation processes to minimize these environmental impacts.
There are strategies in place to mitigate the environmental impacts associated with raw material extraction. For example, some glass manufacturers are now using more recycled glass (cullet) in their production process, which reduces the need for new raw materials and thus minimizes the associated environmental impacts. Furthermore, efforts are made to rehabilitate extraction sites after mining, which helps restore the local ecosystem.
In conclusion, while the extraction of raw materials for the production of impact resistant glass can have significant environmental impacts, there are measures that can be taken to mitigate these impacts. This includes the use of more recycled materials, the implementation of efficient extraction and transportation methods, and the rehabilitation of extraction sites post-mining.
Waste Management during Production
Waste management during the production of impact resistant glass is an essential subtopic when discussing the environmental impacts associated with its production. This process involves the utilization of resources efficiently and effectively to minimize waste and to responsibly dispose of any waste that is produced.
The production of impact resistant glass can generate various types of waste such as off-cuts, defective products, and container glass cullet. These wastes, if not managed well, can lead to environmental contamination and resource depletion. However, many manufacturers are now implementing more efficient production techniques and waste management strategies to minimize waste generation.
For instance, the use of advanced cutting technology can reduce the amount of off-cuts produced during the production process. Additionally, any defective products can be recycled back into the production process, reducing the need for new raw materials. Container glass cullet, produced from the crushing of glass, can also be recycled and reused in the production of new impact-resistant glass.
Furthermore, companies are increasingly adopting a closed-loop production system. In this system, waste materials from the production process are collected, treated, and reintroduced into the production cycle, reducing the total amount of waste produced. This not only minimizes the environmental impact but also makes economic sense as it reduces the cost of raw materials.
In conclusion, while waste management during the production of impact resistant glass does have environmental implications, the adoption of efficient production techniques and waste management strategies can significantly lessen these impacts.
Lifespan and Recyclability of Impact Resistant Glass
The lifespan and recyclability of impact resistant glass play a significant role in its overall environmental impact. The longer a product can be used before it needs to be replaced, the less environmental impact it has, because it reduces the need for new raw materials and energy for production, and it reduces the amount of waste that ends up in landfills. Impact resistant glass, also known as safety glass, is designed to be stronger and more durable than ordinary glass, which can significantly extend its lifespan.
Recyclability is another important factor. Glass is 100% recyclable and can be reused indefinitely without losing its quality or purity. This is not always the case with impact resistant glass, however, as it is often composed of multiple layers of glass and plastic. While the glass components can often be recycled, the plastic layers can be more challenging. This means that end-of-life management of impact resistant glass can be more complex and less environmentally friendly than for regular glass.
Despite these challenges, many manufacturers are making efforts to improve the recyclability of their impact resistant glass products. Some are developing new types of safety glass that are easier to recycle, while others are implementing take-back programs to ensure that their products are properly recycled at the end of their life. These initiatives are helping to minimize the environmental impacts of impact resistant glass production and use, and contribute to a more sustainable glass industry.