Safety glass, a vital element in many different industries and applications, is specifically designed to be stronger and safer than regular glass. The importance of this material in structures such as vehicles, buildings, and various types of equipment cannot be overstated, making its durability and strength paramount. But how exactly is safety glass tested to ensure it can withstand the rigors of its intended use? This article aims to delve into the intricacies of safety glass testing, providing a comprehensive understanding of the processes involved.
Firstly, it is important to understand the composition of safety glass, and how its unique structure contributes to its strength and resilience. The manufacturing process involves various elements that enhance its safety features, all of which will be explored in detail. The next section will focus on the different types of durability tests for safety glass, including the techniques, equipment, and measurements used to evaluate its resistance to environmental stressors.
The article then moves onto the process of impact strength testing for safety glass. This test is crucial to assess the glass’s resistance to sudden forces or impacts, a common occurrence in accidents or extreme weather conditions. The methods used for these tests, and how they simulate real-world scenarios, will be discussed in depth.
Interpreting the results of these tests is a critical part of the process, and this will be the focus of the fourth section. We will explore how testers evaluate the data and determine whether the safety glass meets the required standards for durability and strength. Finally, the article concludes by examining the role of regulatory standards in safety glass testing. These standards are vital in ensuring the safety and effectiveness of the glass, providing guidelines and benchmarks that manufacturers must meet.
Through exploring these five subtopics, this article aims to provide a comprehensive understanding of how safety glass is tested for durability and strength, shedding light on the rigorous processes that ensure the safety and reliability of this important material.
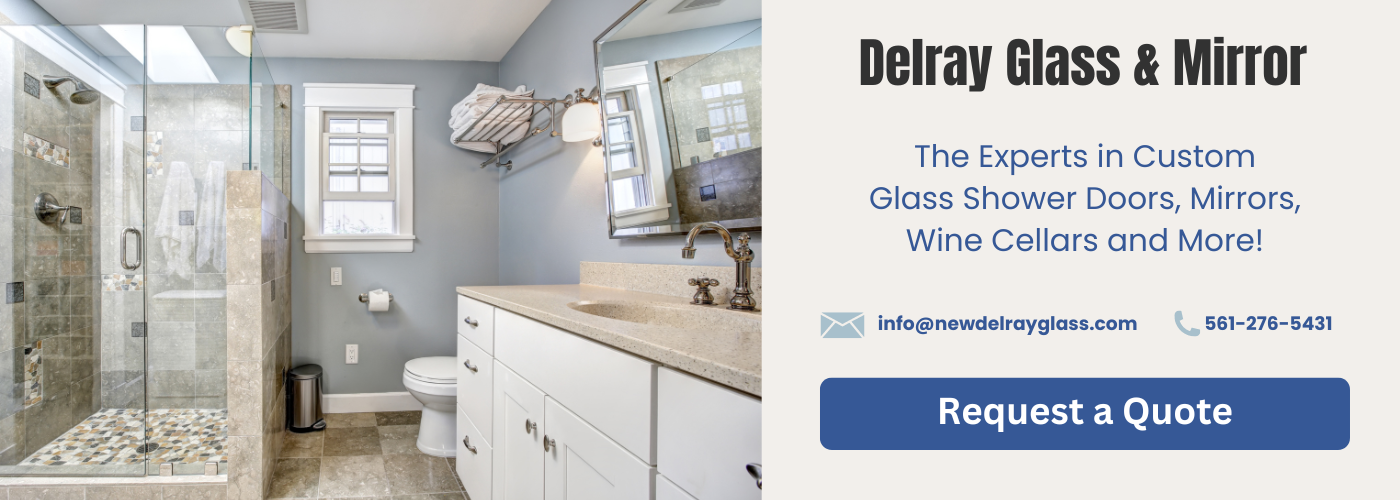
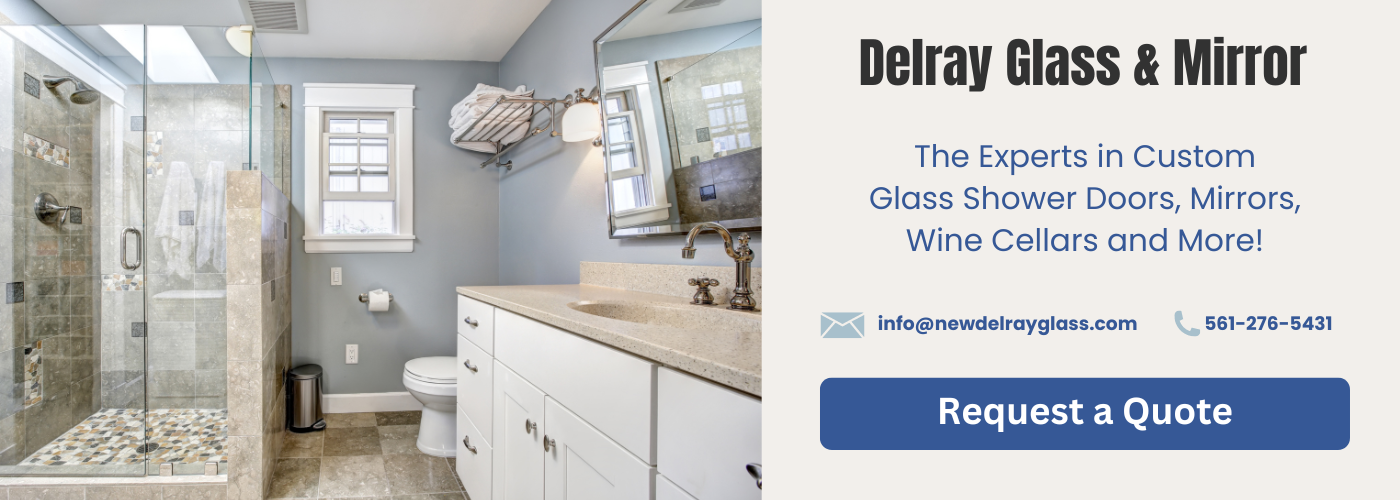
Understanding the Composition of Safety Glass
Safety glass, as the name implies, is designed to be safer than regular glass. It is a broad term that encompasses several types of glass, all of which have been reinforced in some way to increase their strength and reduce the likelihood of injury when they break. Safety glass can be made in several ways, but all types are designed to either resist breaking or to break in a safe manner.
The most common types of safety glass are tempered glass and laminated glass. Tempered glass, also known as toughened glass, is made by heating normal glass to high temperatures and then cooling it rapidly. This process increases the strength of the glass and changes the way it breaks, causing it to shatter into small, blunt pieces instead of large, sharp shards.
Laminated glass, on the other hand, is made by sandwiching a layer of plastic between two layers of glass. This not only makes the glass stronger, but also causes it to hold together when broken, preventing it from shattering and causing injury.
Understanding the composition of safety glass is crucial in testing its durability and strength. By knowing what the glass is made of and how it is made, testers can design experiments that accurately measure the glass’s resistance to forces like impact and pressure. In addition, this knowledge helps testers predict how the glass will break, which is important for assessing its safety.
Different Types of Durability Tests for Safety Glass
Safety glass undergoes a series of durability tests to ascertain its strength and resilience. These tests are different in nature and aim to simulate various real life scenarios that the safety glass may encounter.
One of the commonly used durability tests for safety glass is the Hard Body Impact Test. This type of test involves dropping a blunt object (often a weighted bag of glass beads) from a specific height onto the safety glass. The test measures the height from which the object can fall without breaking the glass.
Another popular test is the Soft Body Impact Test. This test simulates a human body impact by using a larger, softer body like a crash test dummy. The dummy is propelled towards the safety glass at a certain speed, and the test measures the speed at which the dummy can hit the glass without breaking it.
Additionally, there is the Shot Bag Impact Test. In this test, a leather bag filled with lead shot is swung from a pendulum onto the glass. This test simulates impact from various angles and measures the strength of the glass under such conditions.
These durability tests are crucial in the safety glass manufacturing process as they ensure the glass is strong enough to withstand various forms of impact without shattering. It is important to note that the specific tests applied can vary depending on the intended use of the safety glass, be it for automotive windshields, building windows, or other applications.
Process of Impact Strength Testing for Safety Glass
The process of impact strength testing for safety glass is an integral component in determining its durability and strength. This testing procedure aims to assess how well safety glass can withstand shock or impact forces that may arise in real-world scenarios. The results of these tests can provide valuable information about the toughness of the glass and its resistance to breakage upon impact.
The process begins by preparing the safety glass sample, which is usually a flat piece of glass cut to specific dimensions. This sample is then subjected to a controlled impact using a weighted bag or a pendulum-like device. The impact’s force is carefully measured and recorded for analysis. The glass is deemed to have passed the test if it can withstand the specified impact force without shattering into large, sharp pieces.
Another important aspect of impact strength testing is evaluating the fragmentation pattern of the glass upon impact. Safety glass, especially tempered safety glass, is designed to break into small, blunt pieces upon extreme impact to minimize injury risk. Therefore, observing the fragmentation pattern can provide valuable insights into the safety features of the glass.
In conclusion, the process of impact strength testing for safety glass is a rigorous and scientifically-driven process that provides critical data on the glass’s durability and strength. This information is vital in ensuring the safety and reliability of the glass in various applications, from vehicular windshields to architectural installations.
Evaluating the Results of Durability and Strength Tests
Evaluating the results of durability and strength tests is a critical phase in the overall process of assessing safety glass. This stage involves analyzing and interpreting the data collected from the various tests performed on the safety glass to determine its strength and durability.
In the context of safety glass testing, durability refers to the ability of the glass to withstand prolonged exposure to environmental factors such as varying temperatures, moisture, and UV radiation without significant degradation in its quality or performance. Strength, on the other hand, refers to the ability of the glass to resist mechanical forces such as impact or pressure without breaking or shattering.
The results of these tests provide valuable insight into the performance characteristics of the safety glass. They help to identify any potential weaknesses or vulnerabilities in the glass that could compromise its safety performance. For instance, if the glass demonstrates a high degree of brittleness during the impact strength test, it may be unsuitable for applications where it could be subjected to sudden or forceful impacts.
These test results are also crucial for validating whether the safety glass meets the required regulatory standards. Safety glass that fails to meet these standards would not be fit for use in safety-critical applications.
In conclusion, evaluating the results of durability and strength tests is not just about identifying the physical properties of safety glass. It is also about ensuring that the glass can perform its intended function effectively and safely under various conditions.
Role of Regulatory Standards in Safety Glass Testing
The role of regulatory standards in safety glass testing is absolutely crucial. These standards ensure uniformity and consistency across all safety glass products, regardless of the manufacturer. Regulatory standards are established by government or industry bodies, and they outline specific guidelines on how safety glass should be tested for durability and strength.
These standards often involve a series of rigorous tests that safety glass must pass before it can be deemed fit for use. For example, the glass may be subjected to impact tests, where a weighted bag or ball is dropped onto the glass from a certain height. The glass should be able to withstand the impact without shattering into dangerous shards. This is a vital characteristic of safety glass, as it protects individuals from potential harm in the event of an accident.
In addition to impact tests, safety glass is also usually subjected to durability tests. These tests might involve exposing the glass to extreme environmental conditions, such as high temperatures, high humidity, or UV radiation. The glass should be able to resist these conditions without losing its structural integrity or protective features.
Regulatory standards also typically require that safety glass be tested for strength. This involves measuring how much force the glass can withstand before it breaks. The testing process is often very precise, making use of specialized equipment to apply and measure the force.
In sum, the role of regulatory standards in safety glass testing is to ensure that all safety glass products meet a certain minimum standard of quality and safety. Without these standards, there would be no reliable way to ensure that safety glass can effectively protect individuals from harm.