Safety glass, renowned for its strength and security capabilities, plays a fundamental role in various applications, from automobile windshields to protective eyewear. However, the durability of safety glass is tested by numerous factors, one being exposure to ultraviolet (UV) radiation. This article explores the multifaceted question: How does UV exposure affect the longevity of safety glass?
To comprehensively answer this question, the article delves into five key subtopics. The first section, ‘Types of Safety Glass and their UV Resistance’, presents an overview of different safety glass categories, including tempered, laminated, and wire mesh, along with an analysis of their distinct UV resistance properties.
In the subsequent section, ‘Chemical Composition of Safety Glass and UV Degradation’, we dissect the specific elements that constitute safety glass and how these components react when subjected to UV radiation, thereby leading to its degradation.
Moving on to ‘Mechanisms of UV Damage to Safety Glass’, we delve deeper into the scientific processes occurring at a micro level when UV rays interact with safety glass, resulting in its potential damage and reduced lifespan.
The fourth section, ‘Impact of UV Exposure on Safety Features of the Glass’, investigates how prolonged UV exposure can compromise the inherent safety features of the glass, including its impact resistance and shatter-proof qualities.
Finally, the article concludes with ‘Prevention and Mitigation Strategies for UV-induced Damage to Safety Glass’, providing practical, science-backed solutions to extend the longevity of safety glass, despite UV exposure. Through this comprehensive exploration, we aim to provide an in-depth understanding of the relationship between UV exposure and the durability of safety glass.
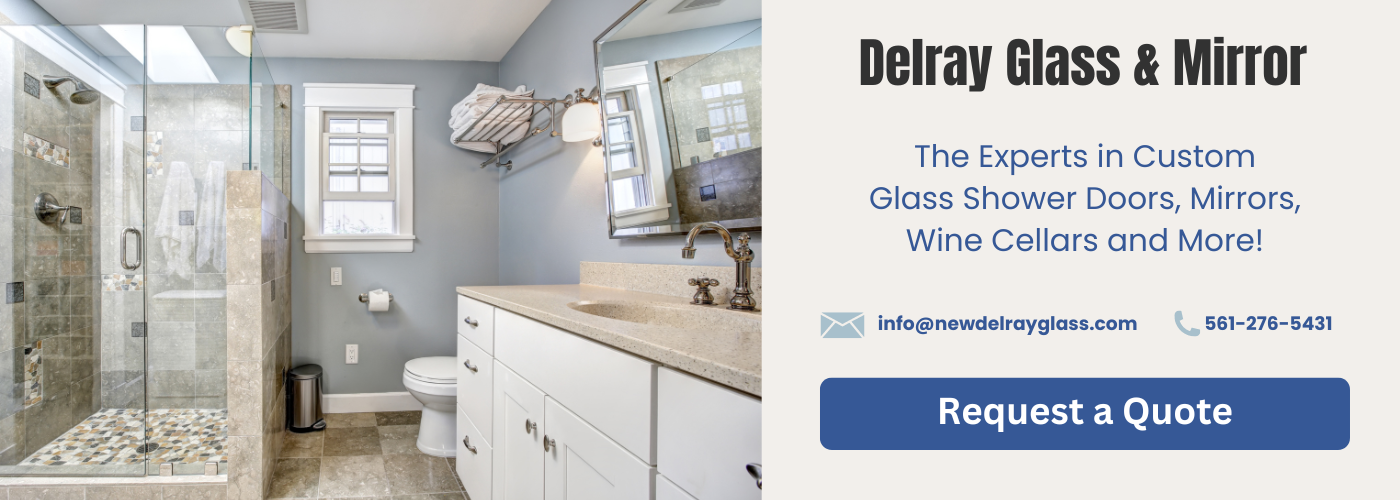
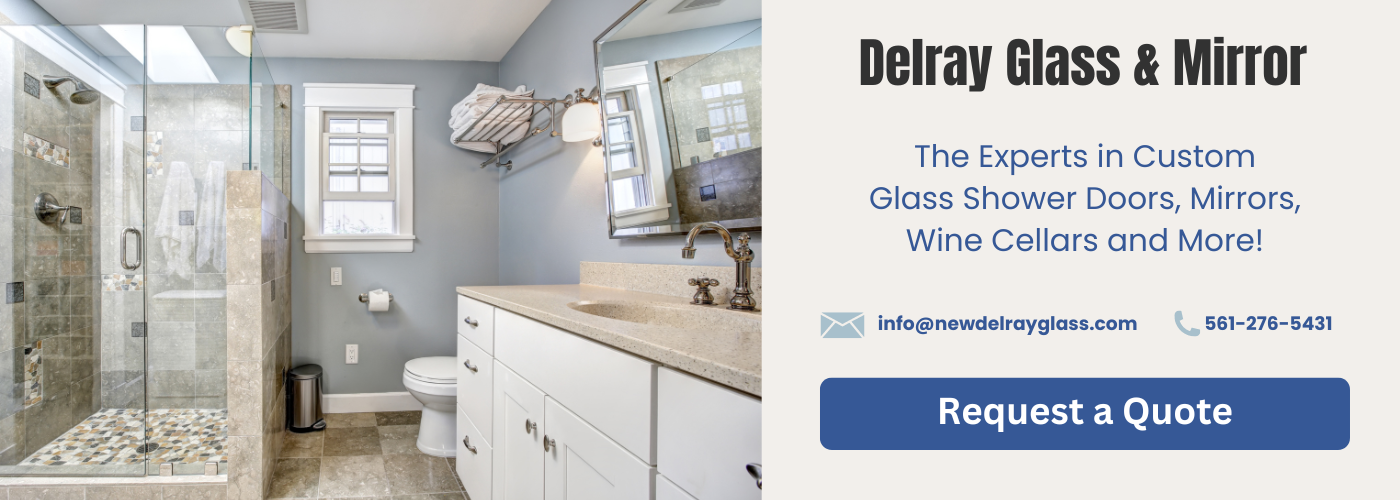
Types of Safety Glass and their UV Resistance
Safety glass is a broad term used to describe various types of glass that are designed to be less likely to break, or less likely to pose a threat when broken. These types of glass include laminated glass, tempered glass, and wire mesh glass. Each of these types of safety glass has a unique structure and composition that contributes to their UV resistance.
Laminated safety glass is made up of two or more layers of glass with a protective interlayer made of polyvinyl butyral (PVB) or ethylene-vinyl acetate (EVA). This interlayer absorbs the majority of the UV radiation, preventing it from penetrating through the glass. This makes laminated safety glass highly UV resistant and an excellent choice for applications that require high levels of UV protection.
Tempered safety glass, on the other hand, is a single piece of glass that has been heat-treated to increase its strength. While it does not have an interlayer like laminated glass, its increased density can partially block UV radiation. However, it is not as effective as laminated glass at preventing UV penetration.
Wire mesh glass is a type of safety glass that contains a wire mesh embedded within the glass. It is primarily used for its fire-resistant properties, and its UV resistance is similar to regular glass. The wire mesh does not provide any additional UV protection.
In conclusion, while all types of safety glass offer some level of UV resistance, laminated safety glass provides the greatest protection due to its special interlayer. This makes it a suitable option for applications where UV exposure is a concern.
Chemical Composition of Safety Glass and UV Degradation
The longevity of safety glass is significantly influenced by its chemical composition, particularly in terms of its susceptibility to UV degradation. Safety glass, such as tempered or laminated glass, is designed to be stronger and more resistant to breakage than standard glass. However, exposure to UV radiation can have detrimental effects on the durability of these materials.
Safety glass is typically composed of two or more layers of glass bonded together with an interlayer of polyvinic butyral (PVB) or ethylene-vinyl acetate (EVA). These materials are chosen for their ability to absorb impact and reduce the likelihood of shattering, which is critical for the safety function of this type of glass.
However, upon exposure to UV radiation, chemical reactions can occur within the glass and the interlayer materials, leading to their degradation. UV radiation can trigger the formation of free radicals within the glass, leading to a process known as photooxidation. This can cause discoloration and weakening of the glass over time.
In addition, UV radiation can cause the PVB or EVA interlayer to become brittle and less effective at holding the glass layers together. This can compromise the safety function of the glass, making it less resistant to impact and more prone to shattering.
UV degradation is a gradual process, and the rate at which it occurs depends on several factors, including the intensity of the UV radiation, the duration of exposure, and the specific chemical composition of the safety glass. Therefore, understanding the chemical composition of safety glass and how it interacts with UV radiation is critical for improving the longevity of these materials.
Mechanisms of UV Damage to Safety Glass
Ultraviolet (UV) radiation, particularly its most damaging form – UV-B, can cause significant harm to safety glass. The mechanisms of UV damage to safety glass mainly involve the breakdown of the protective layers and the degradation of the material’s chemical structure over time.
Safety glass is typically treated with a protective layer that resists UV radiation. However, continuous exposure to UV rays can cause this layer to break down, reducing its effectiveness. This can lead to the glass losing its color, transparency, and in severe cases, its structural integrity.
UV radiation can also interact with the chemical structure of the safety glass. The energy from the UV rays can break the chemical bonds in the glass, causing micro-cracks and leading to the glass becoming brittle over time. This can significantly reduce the longevity of the safety glass, making it more prone to shattering on impact.
One of the key aspects of UV damage is that it is cumulative. The more the safety glass is exposed to UV radiation, the more damage is done. This is why it is important to regularly check and replace safety glass in areas with high UV exposure.
Overall, while safety glass is designed to be durable and resistant to many forms of damage, UV radiation is one factor that can significantly affect its longevity. Understanding the mechanisms of UV damage to safety glass can help in developing strategies to prevent or mitigate this damage, thereby extending the life of the safety glass.
Impact of UV Exposure on Safety Features of the Glass
The impact of UV exposure on the safety features of the glass is a crucial aspect to consider when discussing the longevity and durability of safety glass. Safety glass is primarily designed to withstand impacts and resist shattering, but its exposure to ultraviolet (UV) light can potentially alter these features.
UV light, especially the more harmful UVB and UVC types, can cause a phenomenon known as photo-degradation. This is a chemical reaction triggered by the absorption of UV light, leading to a breakdown of the bonds within the material. In the case of safety glass, this can result in reduced impact resistance over time.
Furthermore, if the safety glass has been treated or coated for specific features – such as anti-glare, anti-scratch, or tinting – UV exposure can potentially degrade these treatments. For example, prolonged UV exposure might cause the tint on safety glass to fade, reducing its effectiveness.
In cases where the safety glass is laminated, UV exposure might also affect the integrity of the interlayer material. This material, commonly made of polyvinyl butyral (PVB), is used to hold the glass fragments together in case of breakage. However, PVB is susceptible to UV damage, which can cause it to yellow and lose its adhesion properties. In turn, this can compromise the overall safety function of the laminated glass.
In conclusion, while safety glass is designed to provide high levels of protection and durability, its exposure to UV light can significantly affect its safety features and lifespan. Therefore, understanding the impact of UV exposure and implementing strategies to minimize it is crucial in maintaining the longevity of safety glass.
Prevention and Mitigation Strategies for UV-induced Damage to Safety Glass
Prevention and mitigation strategies for UV-induced damage to safety glass are critical to maintain the longevity and integrity of the glass. Continuous exposure to ultraviolet (UV) radiation can lead to the degradation of the silica-based material, resulting in a reduction of its safety features. Therefore, understanding and implementing effective strategies for prevention and mitigation is essential.
One common prevention strategy is the application of a UV-resistant coating on the surface of the safety glass. This coating acts as a barrier that absorbs or reflects the UV radiation, reducing the amount of radiation that penetrates the glass. Various types of UV-resistant coatings are available in the market, and they differ in their effectiveness based on the composition and method of application. Some coatings are integrated into the glass during the manufacturing process, while others can be applied post-manufacture.
Another effective strategy is the use of laminated safety glass, which consists of two or more layers of glass bonded together with a plastic interlayer. The plastic interlayer is usually made of materials like polyvinyl butyral (PVB) or ethylene-vinyl acetate (EVA), which have excellent UV-blocking properties. Therefore, even if the outer layer of the glass is damaged by UV radiation, the interlayer continues to provide protection.
These prevention and mitigation strategies are not only important for the longevity of the safety glass but also for the safety and welfare of the individuals who rely on it. By reducing UV-induced damage, the risk of glass failure and the potential for injury is significantly reduced.