In the world of construction and manufacturing, the lead time for custom safety glass orders is an important consideration. It is the duration between the initiation and completion of a production process, from the time an order is placed until the product is ready for delivery. This article will delve into the details of what influences the lead time for custom safety glass orders, providing comprehensive insights on key factors to consider.
Firstly, we will explore the manufacturing process of custom safety glass to give you a better understanding of what this entails. Then, we will examine the various factors that influence the lead time, such as the complexity of the order, capacity of the manufacturer, and the availability of raw materials.
Next, we will discuss the average lead times within the industry, giving you a benchmark to compare with your own experiences or expectations. The role of suppliers in determining lead time is also a significant aspect to be considered. Suppliers can influence the lead time both positively and negatively based on their efficiency and reliability.
Lastly, we will provide insights on how to expedite lead time for urgent custom safety glass orders. Sometimes, despite the best planning, urgent orders are inevitable. Knowing how to navigate these situations can significantly impact the success of your project. So, whether you are a project manager, a procurement officer, or simply an interested party, this article will equip you with the necessary knowledge to understand and manage the lead time for custom safety glass orders.
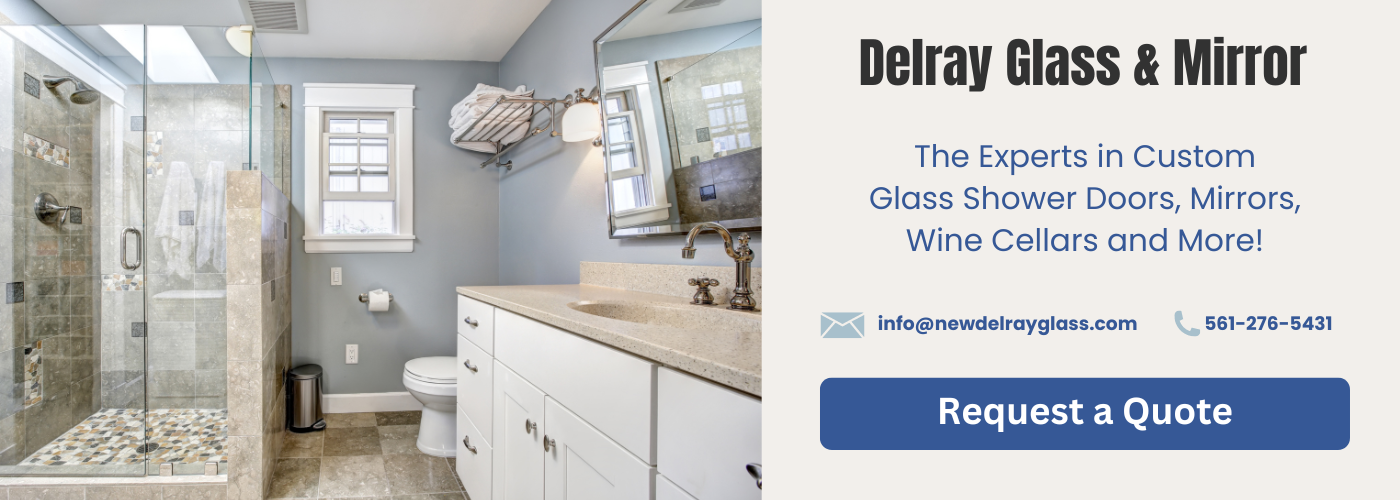
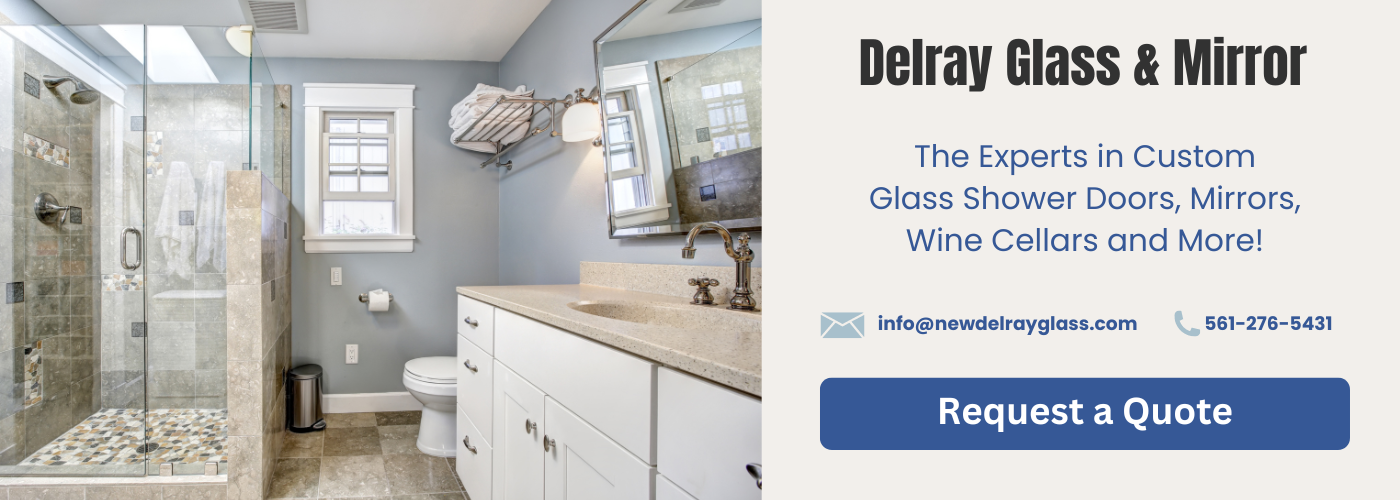
Understanding the Manufacturing Process of Custom Safety Glass
The manufacturing process of custom safety glass is a key factor in understanding the lead time for its orders. This process involves multiple stages, which could variably influence the lead time. The production of custom safety glass starts with acquiring the raw materials required, which include silica sand, soda ash, and limestone. These materials are heated to extreme temperatures, resulting in a molten state. This molten form is then carefully cooled to form the glass.
In the context of safety glass, it’s not just about creating normal glass. An additional process is involved to make the glass ‘safe’. This often involves a process known as tempering, where the glass is heated and then rapidly cooled. This process makes the glass much stronger than regular glass and causes it to break into small, dull pieces rather than sharp shards if shattered.
However, when the glass is customized, the process becomes even more complex. Customization could involve anything from changing the thickness of the glass, altering its shape, or adding tints or coatings. Each of these elements prolongs the manufacturing time as they require additional steps or processes.
In conclusion, understanding the manufacturing process of custom safety glass provides insight into the lead time for such orders. The complexity of this process, combined with the customization requirements of the client, will directly influence how long it takes for the safety glass to be produced and delivered.
Factors Influencing the Lead Time for Custom Safety Glass
The lead time required for custom safety glass orders can be influenced by a variety of factors. These include the complexity of the design, the volume of the order, the availability of raw materials, the production capacity of the manufacturer, and the efficiency of the supply chain.
The design complexity is a significant factor. More complex designs require more time for manufacturing and quality testing. This is to ensure that the final product meets all safety standards and client specifications. Similarly, the volume of the order can also affect the lead time. Larger orders may take longer to fulfill due to the sheer amount of work involved.
The availability of raw materials is another important factor. If there is a shortage of any required material, it can delay the production process. Furthermore, the production capacity of the manufacturer plays a role. If the manufacturer is already operating at full capacity, it might be challenging to accommodate new orders without extending the lead time.
Lastly, the efficiency of the supply chain can influence the lead time as well. If there are delays in the supply chain, it can impact the time it takes to deliver the final product to the customer. For instance, logistical issues, customs delays, or problems with suppliers can all add to the lead time.
In conclusion, several factors can impact the lead time for custom safety glass orders. Understanding these factors can help customers plan their orders better and manage their expectations regarding delivery timelines.
Average Lead Times for Custom Safety Glass in the Industry
Average lead times for custom safety glass in the industry can vary depending on numerous factors. The entire process, from the initial order to delivery, can take several weeks or even months. This is because creating custom safety glass involves several complex steps, including design, production, and testing, before the final product is ready for shipment.
Lead times can also fluctuate depending on the size and complexity of the order. Larger or more complex orders will naturally take longer to produce. Additionally, the specific type of safety glass being ordered can also impact lead times. For instance, tempered glass may have a shorter lead time compared to laminated glass, as the latter involves more stages in its production process.
Another important factor affecting lead times in the safety glass industry is the current demand. During periods of high demand, manufacturers may struggle to keep up, causing lead times to increase. Conversely, during slower periods, lead times may decrease. Manufacturers usually communicate these changes to their clients, so they can plan accordingly.
Lastly, it’s crucial to note that lead times can also be influenced by factors outside of the manufacturer’s control, such as logistical issues or delays in raw material supply. Therefore, when placing an order for custom safety glass, it’s important for clients to factor in potential delays and plan their projects accordingly.
The Role of Suppliers in Determining Lead Time
The role of suppliers in determining the lead time for custom safety glass orders is pivotal. Suppliers are essentially the entities responsible for providing the raw materials required for the production of custom safety glass. Their efficiency and reliability have a direct impact on the lead time.
The lead time can vary greatly depending on the supplier’s ability to fulfill the order promptly. This hinges on various factors such as the supplier’s inventory levels, production capacity, and logistical capabilities. If a supplier has a well-managed inventory and efficient production processes, they can provide the materials more quickly, thereby reducing the lead time.
However, if the supplier is dealing with issues such as equipment breakdowns, labor shortages, or logistical problems, this can lead to delays in the delivery of materials, which in turn contributes to a longer lead time for the final product. Additionally, the geographical location of the supplier can also influence the lead time. A supplier located closer to the production facility can generally deliver the materials faster than a supplier located far away.
Therefore, it is crucial for manufacturers of custom safety glass to maintain good relationships with reliable suppliers. They must also have contingency plans in place to deal with any potential issues that may arise with their suppliers. By effectively managing their supply chains, manufacturers can minimize the lead time for custom safety glass orders.
How to Expedite Lead Time for Urgent Custom Safety Glass Orders
In the world of manufacturing and production, particularly in relation to custom safety glass orders, time is of the essence. This is especially true when there is an urgent need for these products. The question then arises: how can one expedite the lead time for urgent custom safety glass orders?
The answer to this question is multifaceted, largely dependent on a number of factors. First, understanding the manufacturing process is crucial. This includes being aware of the time required for each step, from design to production, and the potential bottlenecks that could delay the process.
Next, it’s important to engage with suppliers early and communicate your urgent needs clearly. The role of suppliers in determining lead time cannot be overstated. They control the availability of raw materials and components, and their efficiency can significantly impact the lead time.
Moreover, it’s also necessary to consider the external factors influencing the lead time. These can range from the current demand and supply dynamics in the industry, to unforeseen circumstances like natural disasters.
In conclusion, expediting lead time for urgent custom safety glass orders is a complex task. It requires a comprehensive understanding of the manufacturing process, effective communication with suppliers, and the ability to navigate and mitigate external factors. By mastering these aspects, it’s possible to significantly reduce lead time and meet urgent needs.