The question of whether safety glass can be drilled or cut after manufacturing is a complex one, fraught with numerous technical considerations and safety implications. Cutting or drilling into safety glass doesn’t only require a careful approach, but also a deep understanding of the properties of the material, an examination of the manufacturing process, and knowledge of the impacts such modifications could have on its safety features. In this article, we will delve into these aspects to provide a comprehensive answer.
We will first explore the properties of safety glass, understanding its composition and the characteristics that differentiate it from other types of glass. The focus will then shift to the manufacturing process of safety glass, which plays a critical role in determining whether and how it can be modified after production.
Next, we will discuss the various techniques used for drilling and cutting glass, drawing attention to any specific considerations when dealing with safety glass. This section will offer practical insights for professionals and DIY enthusiasts alike, detailing the tools, techniques, and best practices for manipulating safety glass.
Fourthly, we will look into the risks and precautions associated with drilling or cutting safety glass, highlighting the potential dangers and providing precautionary measures to ensure safety during the process.
Finally, we will examine the impact of drilling or cutting on the safety features of the glass. This section will address how these modifications could potentially compromise the structural integrity and safety features of the glass, providing important information for anyone considering drilling or cutting into their safety glass.
This comprehensive exploration aims to provide clear, factual information to aid in understanding the possibilities and limitations when considering modifying safety glass after manufacturing.
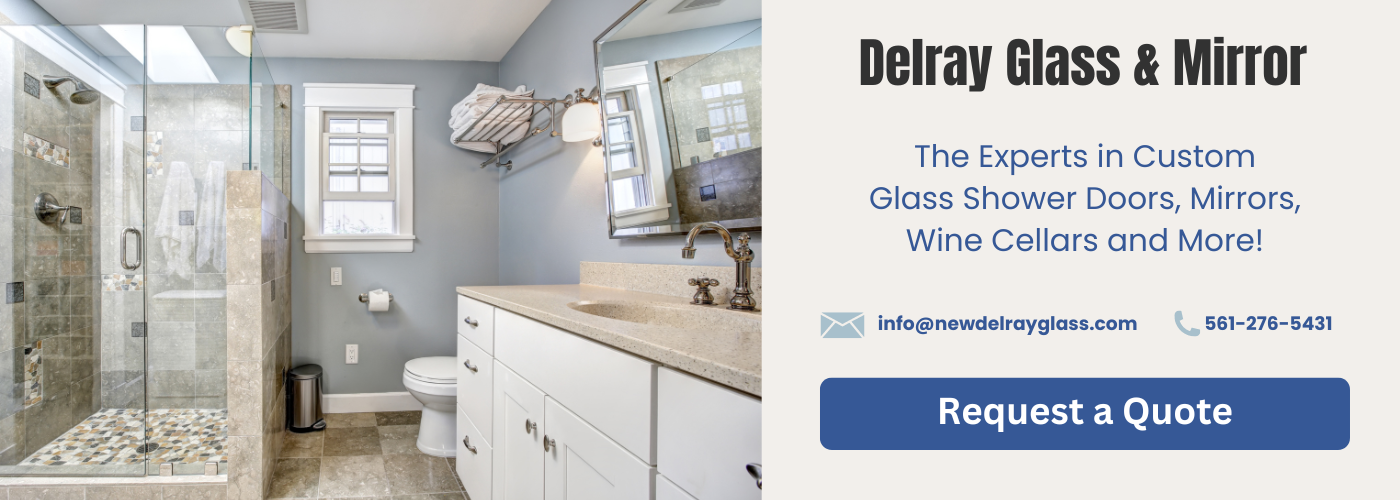
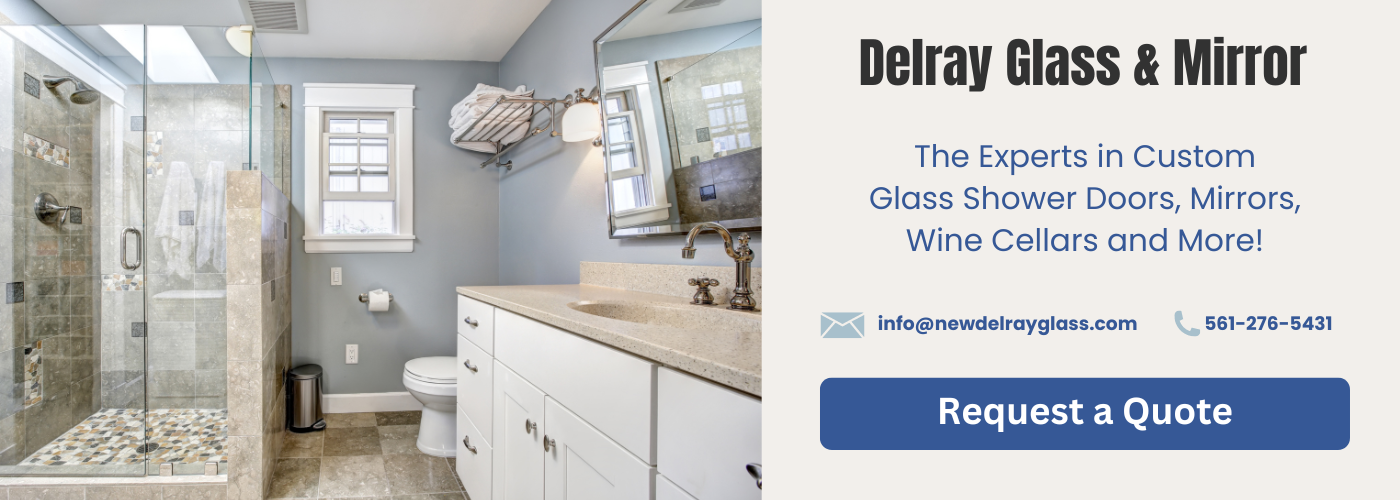
Properties of Safety Glass
Safety glass, also known as tempered glass, is a type of glass that is designed to be stronger than ordinary glass. It undergoes a process of heat or chemical treatments that increase its strength and make it less likely to break, or if it does break, it will crumble into small, less harmful pieces rather than shattering into sharp shards. This is what makes it a popular choice for applications where safety is of paramount importance.
The properties of safety glass also include its resistance to high temperatures, making it ideal for use in environments where there is a risk of exposure to extreme heat. It is also more scratch resistant and impact resistant than standard glass.
However, these properties also make safety glass more difficult to work with post-manufacture. Its enhanced strength and the way it breaks means that it cannot be cut or drilled into after it has been tempered, without the risk of shattering the entire piece. This is why any cutting or drilling into safety glass must be done before the tempering process.
In conclusion, while the properties of safety glass make it a safer and more durable choice for many applications, they also mean that modifications such as drilling or cutting can be challenging and must be done with care and prior to certain manufacturing processes.
Manufacturing Process of Safety Glass
The manufacturing process of safety glass is quite an interesting one. Safety glass, which is commonly used in applications where standard glass could pose a potential danger, is created through a unique process to strengthen it and reduce its risk of breaking. There are two primary types of safety glass: tempered glass and laminated glass. Both undergo specific manufacturing processes to enhance their safety features.
Tempered glass is made by heating it to over 600 degrees Celsius and then cooling it rapidly. This process, known as tempering, puts the surface of the glass into compression and the interior into tension, which strengthens the glass and changes how it breaks. Instead of shattering into large, sharp pieces, tempered glass will crumble into small, granular chunks that are less likely to cause injury.
On the other hand, laminated safety glass is created by sandwiching a layer of plastic, typically polyvinyl butyral (PVB), between two layers of glass. The glass and plastic are bonded together using heat and pressure. In case the glass gets broken, the plastic layer holds the glass fragments together, preventing them from scattering and causing injuries.
In both cases, the goal of the manufacturing process is to create a product that is significantly safer than ordinary glass. However, these safety features can also complicate attempts to drill or cut the glass after manufacturing, leading to potential risks and technical challenges.
Techniques for Drilling and Cutting Glass
Techniques for drilling and cutting glass, particularly safety glass, are specialized processes that require proper tools and methods. Safety glass is a type of glass that is designed to be less likely to break, and if it does, it will break in a way that minimizes the risk of injuries. It is widely used in various applications such as vehicle windows, shower doors, architectural glass doors and tables.
Drilling safety glass requires a specific type of drill bit designed for glass and tile. These drill bits have a spade-shaped point to create clean holes in the glass. The process is usually done slowly to prevent overheating, which could cause the glass to crack. It’s also common to use a lubricant or coolant like water during the process to help dissipate heat.
Cutting safety glass, on the other hand, is a bit more complex. Because safety glass is designed to break into small, rounded pieces, it can’t be cut using traditional methods. One technique is to score the glass using a glass cutter, which creates a weak point in the glass. Then, heat can be applied to the score line to cause the glass to break along the line. This process requires precision and patience to prevent the glass from breaking in unintended places.
It’s important to note that both drilling and cutting safety glass carry risks, such as the potential for the glass to shatter. Therefore, appropriate safety measures should always be taken, including the use of protective equipment like gloves and safety glasses. Furthermore, these procedures should ideally be performed by professionals or those with proper training to ensure safety and efficiency.
Risks and Precautions in Drilling or Cutting Safety Glass
Drilling or cutting safety glass after manufacturing indeed presents a set of risks and requires specific precautions. Safety glass is designed to be significantly more resistant to breakage than standard glass. However, any attempt to modify it after manufacturing, such as drilling or cutting, can compromise its structural integrity and safety features.
One of the primary risks is the possibility of the glass shattering under the pressure of the drilling or cutting process. Safety glass is manufactured through processes such as tempering and laminating to enhance its strength and shatter-resistance. These processes induce internal stresses within the glass, which, if disturbed by drilling or cutting, can result in the glass breaking into small, blunt fragments.
Precautions must be taken to manage these risks effectively. For instance, using specialized glass-cutting tools and drills can help reduce the pressure exerted on the glass. Cooling the glass and the tool during the operation can also prevent overheating, which can cause the glass to crack. Furthermore, it’s crucial to handle the glass delicately and ensure it’s adequately supported throughout the procedure to prevent any accidental pressure or impact that could lead to breakage.
Given the potential risks, it’s highly recommended that any modifications to safety glass be done by trained professionals. They have the necessary skills and equipment to perform these operations safely and effectively, minimizing the risk of damage to the glass and ensuring that its safety features remain intact.
Impact of Drilling or Cutting on the Safety Features of the Glass
The impact of drilling or cutting on the safety features of the glass is a critical subtopic when discussing whether safety glass can be drilled or cut after manufacturing. The fundamental concept to understand here is that any alteration to the glass post-manufacturing can potentially compromise its integrity, particularly its safety features.
Safety glass is designed to be robust and resistant to breakage. It is meant to shatter into small, less harmful pieces rather than large, sharp shards. However, drilling or cutting into it after it has been manufactured could disrupt the tension balance within the glass. This disruption could lead to an increased likelihood of breakage, and in the event of breakage, the glass may not shatter in the intended, safer way.
Moreover, the process of drilling or cutting itself presents risks. These operations can generate heat, which can introduce stress points into the glass, making it more susceptible to cracking or breaking. It’s also essential to consider that safety glass typically consists of multiple layers, including an interlayer of plastic or resin. This composition can make cutting or drilling challenging and could result in damage if not done correctly.
In conclusion, while it is technically possible to drill or cut safety glass after manufacturing, doing so can potentially impact the safety features of the glass. This impact can compromise the core purpose of safety glass, which is to provide a safer alternative to conventional glass in case of breakage. Therefore, any modifications to safety glass post-manufacturing should be approached with caution and ideally conducted by professionals.