The production of laminated glass, a type of safety glass that holds together when shattered, is a fascinating process that combines technology, quality control, and precise manufacturing. This sophisticated type of glass is used in various applications, from car windshields to high-rise windows, due to its durability and safety features. This article will delve into the intricacies of how laminated glass is made, beginning with the raw materials used in its production, through the actual manufacturing process, and finally to its various applications and impact on the environment.
In the first section, we will explore the raw materials used in the production of laminated glass, providing insight into the components that give this glass its distinct properties. Following that, we will walk you through the step-by-step process of making laminated glass which involves bonding layers of glass with a plastic interlayer.
The third part of the article will focus on the rigorous quality control and testing processes that ensure the durability and safety of the laminated glass. These procedures are crucial to guarantee that the final product meets the high standards required for its various uses.
In the fourth section, we will discuss the diverse uses and applications of laminated glass, showcasing its versatility and the vital role it plays in various industries. Lastly, we will examine the safety and environmental impact of laminated glass production, a topic of increasing importance in our environmentally-conscious society.
Join us as we take a closer look at the fascinating world of laminated glass production, shedding light on the intricate process that transforms simple raw materials into a product of immense practicality and resilience.
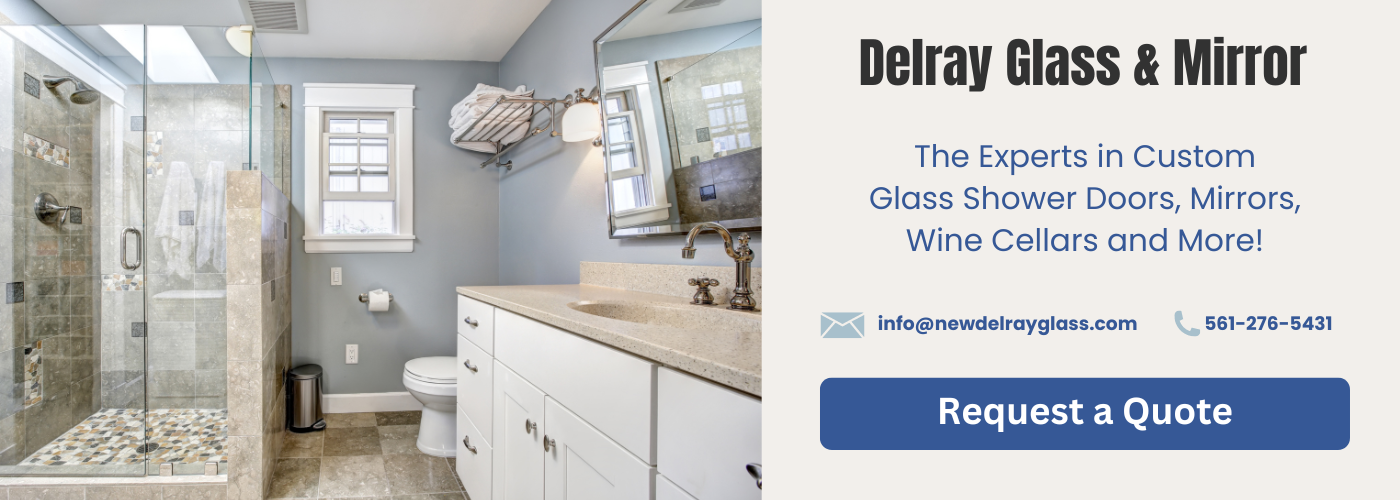
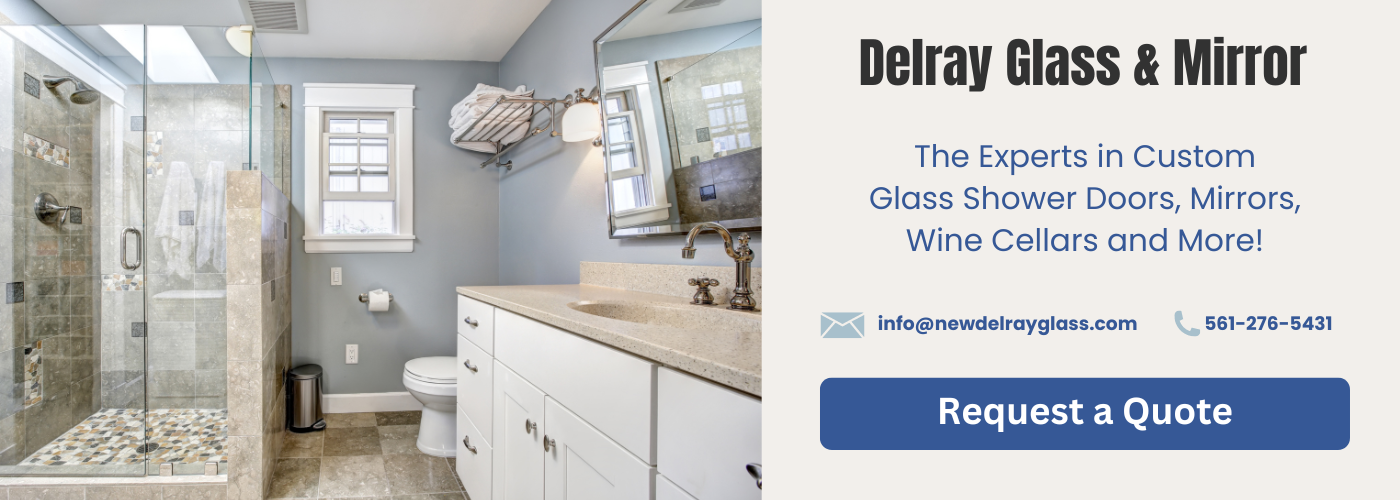
Raw Materials Used in the Production of Laminated Glass
Laminated glass is a type of safety glass, designed to stay intact even when shattered. It’s often used in car windshields, building windows, and other applications where safety and durability are paramount. The production of laminated glass begins with the right raw materials.
The main raw materials used in the production of laminated glass are float glass, polyvinyl butyral (PVB) interlayer, and other materials such as adhesives. Float glass is a type of flat, clear glass that forms the primary component of laminated glass. It’s created through a process where molten glass is floated on a bed of molten metal to create a uniform thickness and surface.
The PVB interlayer is a type of plastic that is sandwiched between two layers of glass in the lamination process. This interlayer gives the glass its safety properties by holding the glass together if it’s shattered, preventing it from breaking into large, dangerous shards.
Adhesives are also used in the lamination process to bond the glass and PVB interlayer together. These adhesives need to be strong enough to withstand the extreme heat and pressure used in the lamination process, and flexible enough to allow the glass and interlayer to bond effectively.
The choice of raw materials is crucial in the production of laminated glass, as they directly affect the glass’s safety properties, clarity, and durability. Different manufacturers may use different types of glass, interlayers, and adhesives depending on the desired properties of the final product. But regardless of the specific materials used, the quality of the raw materials and the precision of the manufacturing process are essential for producing high-quality laminated glass.
The Process of Making Laminated Glass
Laminated glass is made through a meticulous process that involves bonding together two or more layers of glass with an inner layer of polyvinyl butyral (PVB), ethylene-vinyl acetate (EVA), or another type of interlayer. This process is intended to make the glass safer and more durable.
The first step in the process of making laminated glass is to cut the glass into the desired shape and size. This is typically done with a computer-controlled machine to ensure precision. Once the glass is cut, it’s then cleaned and dried to ensure no contaminants interfere with the lamination process.
After the glass is clean and dry, the interlayer material is applied. The selection of this material is crucial as it gives the laminated glass its unique properties. For instance, PVB is often used because it’s strong and can hold the glass together even when it’s broken. On the other hand, EVA provides excellent adhesion and high transparency, making it a popular choice for architectural applications.
Once the interlayer is applied, the glass layers are bonded together under heat and pressure in an autoclave, a type of industrial oven. This process, known as lamination, causes the interlayer to melt and adhere to the glass, creating a single, solid piece.
The final product is a piece of glass that is more resistant to breaking and, if it does break, tends to stay together, reducing the risk of injury. Additionally, laminated glass can offer improved sound insulation, UV protection, and can even be designed to be bullet-resistant or blast-resistant, depending on the specific requirements of its intended application.
Quality Control and Testing of Laminated Glass
Quality control and testing of laminated glass is a critical step in its production process. It is this stage that ensures the final product is of high quality and safe for use. The production of laminated glass involves bonding two or more layers of glass together with a plastic interlayer. The quality control process, therefore, focuses on ensuring this bonding process has been carried out correctly and that the final product has the desired properties.
The testing process involves several stages. Firstly, the glass is visually inspected to check for any imperfections. This is followed by a physical inspection, where the thickness and weight of the glass are measured to ensure they meet the required standards. In addition, the glass is also tested for its impact resistance, which is a crucial property of laminated glass.
Quality control also involves checking the adhesion of the plastic interlayer to the glass. This is done by conducting a peel test where an attempt is made to separate the layers. If the layers separate easily, this indicates poor adhesion and the glass is rejected.
Finally, the laminated glass is tested for its thermal and acoustic properties. This is to ensure that it provides the required levels of insulation and noise reduction.
In conclusion, quality control and testing of laminated glass is a meticulous process that plays a crucial role in ensuring that the final product meets the required safety and quality standards. It involves a series of tests and inspections that check various properties of the glass, from its visual appearance to its physical properties and performance.
Uses and Applications of Laminated Glass
Laminated glass is a type of safety glass that holds together when shattered. This unique feature makes it extremely useful in various applications where safety, security, and durability are paramount.
In the automotive industry, laminated glass is primarily used for windshields. Its ability to stay intact on impact prevents shards of glass from causing injuries to the vehicle occupants during accidents. The property also aids in maintaining visibility after a crash, potentially allowing the driver to control the vehicle and steer it to safety.
Laminated glass is also extensively used in the construction industry. In buildings, it’s used in windows, skylights, curtain walls, and partitions. The durability and safety aspects make it ideal for these applications. Moreover, it provides excellent sound insulation, contributing to a quieter indoor environment. It is also used in balustrades and flooring systems due to its high strength and resistance to breakage.
In the realm of security, laminated glass is used to create bulletproof or resistant glass. Multiple layers of laminated glass can effectively stop bullets and other high-speed projectiles, making it a preferred choice for banks, embassies, and other high-security buildings.
Moreover, laminated glass plays a crucial role in the solar energy industry. It’s used in the production of solar panels due to its durability and transparency, which allows sunlight to pass through while protecting the delicate photovoltaic cells inside.
In summary, the uses and applications of laminated glass are extensive and varied, driven by its unique properties of safety, durability, and sound insulation. Its role is indispensable in many sectors, from automotive and construction to security and renewable energy.
Safety and Environmental Impact of Laminated Glass Production
The safety and environmental impact of laminated glass production is a significant concern in the industry. This is because both the production process and the product itself have potential implications for worker safety, consumer safety, and the environment.
From a safety perspective, the production of laminated glass requires stringent protocols to ensure worker safety. Production involves the use of heat and pressure, presenting risks of burns or injuries from machinery. Additionally, the raw materials used in production, such as polyvinyl butyral (PVB), can pose health risks if not handled appropriately. Hence, regular safety training, protective clothing and equipment, and workplace safety measures are integral to the production process.
As for the product itself, laminated glass is designed to enhance safety. When broken, it holds together, reducing the risk of injury from glass shards. This makes it a preferred choice for applications where safety is paramount, such as in automobiles and high-rise buildings.
On the environmental front, laminated glass production can have several impacts. The energy-intensive production process contributes to greenhouse gas emissions. However, the industry is making strides to reduce its carbon footprint through energy-efficient manufacturing processes and recycling initiatives. One of the main environmental benefits of laminated glass is its recyclability. Old or broken laminated glass can be recycled into new products, reducing the need for raw materials and minimizing waste. Moreover, laminated glass plays a role in energy conservation. Its insulating properties can help reduce energy use in buildings, contributing to sustainability.
In conclusion, while the production of laminated glass does have safety and environmental considerations, the industry is making significant efforts to ensure worker and consumer safety and to mitigate environmental impacts.