When it comes to adding a unique touch to any living space or commercial area, custom mirrors are a popular choice. However, the journey from conception to installation involves a series of intricate steps, each crucial to the final product’s quality and aesthetics. Understanding the timeline and processes involved can help set realistic expectations for those considering this bespoke addition. This article will guide you through the entire lifecycle of a custom mirror, from initial design to the final installation, covering five essential stages: the design process, material selection, fabrication time, shipping and handling, and installation procedures.
The design process begins with a consultation to capture the client’s vision, which is then translated into a practical design by skilled artisans. Following this, the selection of materials plays a pivotal role, impacting not only the look but also the durability of the mirror. The fabrication phase is where the design comes to life, a period that varies greatly depending on the complexity and details involved. Shipping and handling are subsequent critical steps, requiring meticulous planning to ensure the mirror arrives safely at its destination. Finally, the installation procedures, which may vary based on the mirror’s size, weight, and design, are the last hurdle to achieving the envisioned aesthetic. Each of these stages intertwines to affect the overall timeline for creating and installing a custom mirror, which this article will explore in detail.
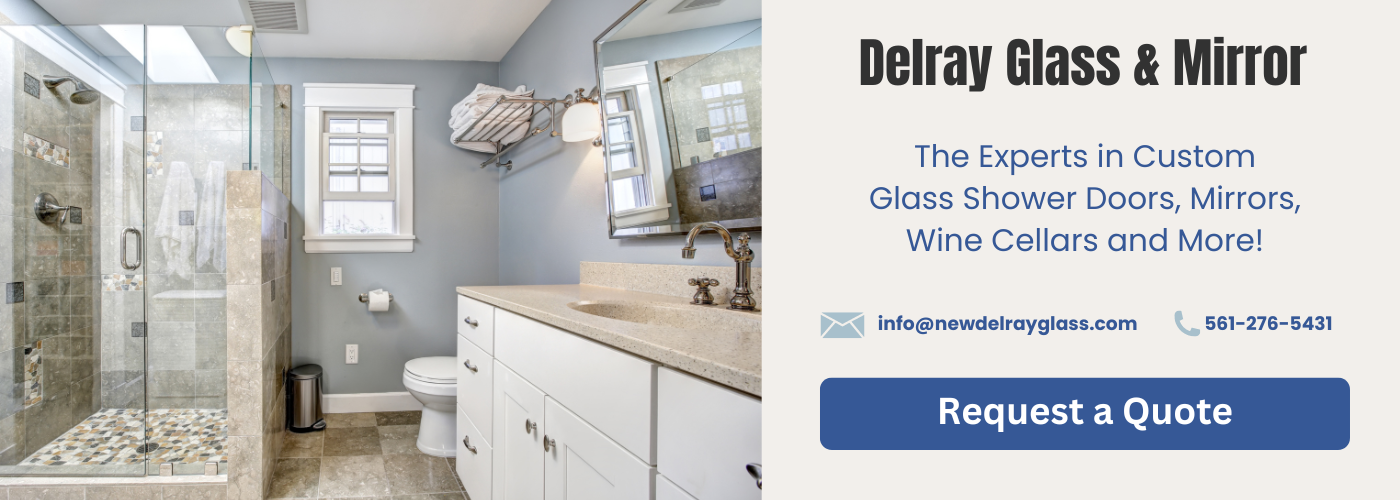
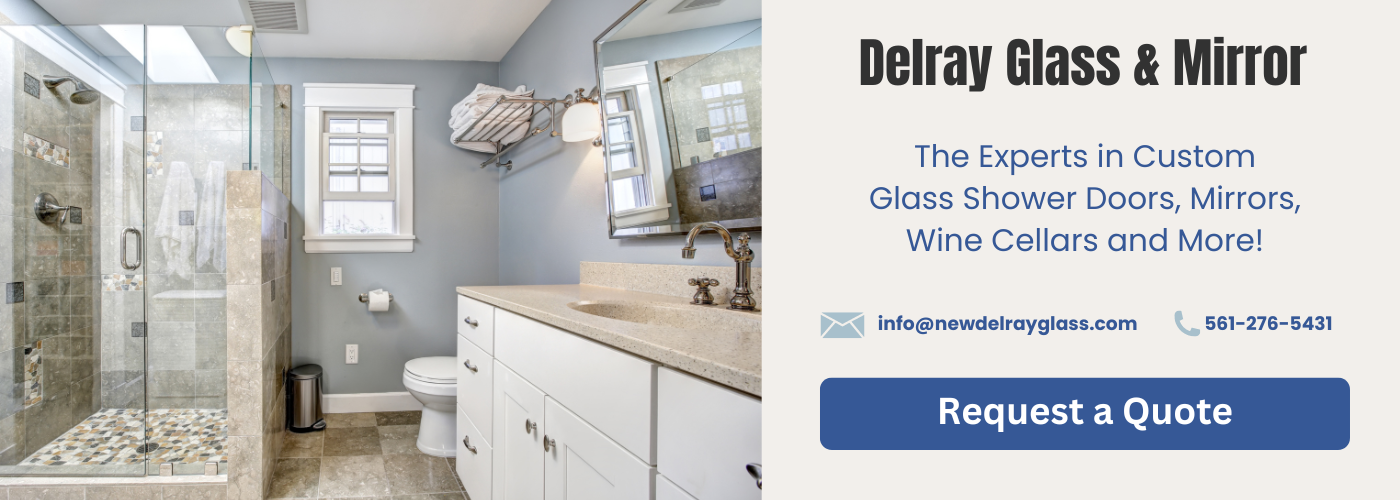
Design Process
The design process is a critical first step in the creation and installation of a custom mirror. This stage involves several key activities, each of which is essential for ensuring that the final product meets the specific requirements and preferences of the customer. Initially, the process begins with client consultations, during which the purpose of the mirror, the desired aesthetic, size, shape, and any additional features are discussed. This is a collaborative effort to align the designer’s capabilities with the client’s vision.
Following the initial discussions, detailed sketches or digital renderings of the mirror are created. These designs serve as a visual aid to help both the client and the designer agree on the final look before any material is cut or assembled. It’s important during this phase for the designer to consider not only the appearance but also the practical aspects of the mirror, such as its weight, the method of installation, and its longevity and durability in the intended environment.
Revisions are a normal part of the design process, as it’s rare to arrive at the perfect solution on the first try. Feedback is taken into account to refine the design, ensuring that the finished product will be exactly as envisioned. Once the design is finalized, specifications are meticulously documented, including dimensions, materials, and special requirements. This documentation is crucial as it guides the subsequent steps in the custom mirror making process.
Overall, the design process can vary in length depending on the complexity of the project and the efficiency of the communication between the client and the designer. Typically, this phase can take anywhere from a few days to several weeks. Ensuring a thorough and unhurried design process lays a solid foundation for the fabrication of a custom mirror that perfectly matches the client’s needs and the functional context of its placement.
Material Selection
The process of material selection is a crucial step in the creation of a custom mirror, influencing not only the aesthetics but also the functionality and durability of the finished product. When choosing materials for a custom mirror, several factors must be considered to ensure the final product meets the desired specifications and quality standards.
Firstly, the type of glass used for the mirror is of utmost importance. Most mirrors are made from clear, flat glass that is then coated on one side with a reflective material, typically silver or aluminum. The quality of the glass affects the clarity and reflection quality of the mirror. Higher-quality glass with fewer imperfections will result in a better reflection, making it a preferred choice for custom projects.
In addition to the glass itself, the reflective coating is another significant material choice. Silver coatings are known for providing a very clear and precise reflection, whereas aluminum coatings are often more durable and resistant to tarnishing. The choice between these materials often depends on where the mirror will be placed and what environmental factors it will be exposed to.
The thickness of the glass also plays a role in the selection process. Thicker glass is less prone to warping and provides a more stable reflection, but it is also heavier and more difficult to handle during installation. The environment where the mirror will be installed may dictate the thickness needed, especially in areas prone to high humidity or temperature changes.
Finally, the frame and backing materials are also essential components. The frame not only enhances the mirror’s appearance but also contributes to its structural integrity. Frames can be made from a variety of materials including wood, metal, or even plastic, depending on the design requirements and budget. The backing material helps protect the reflective coating on the glass and adds to the overall durability of the mirror.
In summary, the material selection process for custom mirrors is a detailed and critical phase that directly impacts the aesthetics, functionality, and longevity of the mirror. It requires careful consideration and a good understanding of the materials available and their properties to achieve the best outcome for the specific application and environment where the mirror will be used.
Fabrication Time
Fabrication time is a critical phase in the process of making and installing a custom mirror. This stage involves cutting the mirror to the specified dimensions and shaping it according to the design requirements. The duration of the fabrication process can vary significantly depending on several factors including the complexity of the design, the type of materials used, and the capabilities of the manufacturing facility.
For simpler designs, the fabrication might be relatively quick, possibly completed within a few days. However, more intricate designs that require detailed craftsmanship or special treatments such as beveling, etching, or adding decorative features can extend the fabrication time significantly. During this phase, precision is crucial as even minor errors can spoil the aesthetics or functionality of the mirror.
Additionally, if the mirror incorporates advanced technologies, such as lighting or smart features, the fabrication could involve additional steps such as wiring and integration of electronic components. This integration requires careful handling and testing to ensure that all components function seamlessly together.
Once the mirror is fabricated, it must also undergo a thorough quality check to ensure that it meets all specified requirements and is free from defects. Only after passing these checks is the mirror deemed ready for the next phase, which is shipping and handling. The careful attention to detail at each step of fabrication ensures that the final product not only meets the client’s expectations but also stands the test of time in terms of durability and functionality.
Shipping and Handling
When considering the time it takes to make and install a custom mirror, the “Shipping and Handling” phase plays a crucial role. This stage involves the transportation of the finished mirror from the manufacturing site to its final installation location, which can significantly impact the overall timeline depending on several factors.
Firstly, the distance between the manufacturer and the installation site is a primary determinant of the shipping duration. Local deliveries might be completed within a day or two, whereas international shipping could take several weeks. The mode of transport—whether by road, air, or sea—also influences the time frame. Air freight is typically the fastest method, though it is more costly than shipping by road or sea.
Another critical aspect of shipping and handling is the care with which the mirror is packed and handled during transit. Custom mirrors, especially large or intricately designed pieces, require robust packing to protect them from any damage such as cracks, scratches, or breaks. The packing material and technique need to be meticulously chosen and applied to ensure the mirror’s safety.
Lastly, upon arrival at the destination, the handling process involves the careful unloading and storage of the mirror until the installation team is ready. This phase requires precision and attention to detail to prevent any last-minute damages.
Overall, the “Shipping and Handling” stage is vital in the timeline for creating and installing a custom mirror, as it involves multiple variables that can affect both the delivery time and the integrity of the final product. Proper planning and execution during this phase are essential for a successful installation.
Installation Procedures
Installation procedures are a critical part of the process when it comes to custom mirrors. Once the mirror has been designed, materials selected, fabricated, and shipped, the final step is to properly install it. This phase is crucial as it determines how well the mirror fits into the intended space and how securely it is mounted, which can affect both its functionality and aesthetics.
The installation process begins with the preparation of the area where the mirror will be placed. This may involve measuring the space accurately, ensuring the wall or surface is flat and strong enough to support the mirror, and possibly making adjustments to accommodate the hardware needed for mounting. It is important that the area is clean and free from debris to prevent any damage or irregularities once the mirror is installed.
Next, the hardware and supports for the mirror are installed. This could involve brackets, clips, or adhesive, depending on the design and weight of the mirror. The method of installation varies significantly based on the size and style of the mirror as well as the surface it will be attached to. For large or heavy mirrors, more robust mounting systems are necessary to ensure safety and stability.
Finally, the mirror itself is placed into position and secured. Care must be taken to align it correctly and ensure it is level. Once in place, additional adjustments may be needed to perfect its position. The installation should be checked thoroughly to confirm that the mirror is securely attached and there is no risk of movement or slippage.
Proper installation not only ensures that the mirror performs its functional role but also enhances the overall appearance of the space. Incorrect installation can lead to safety hazards, such as the mirror falling, or aesthetic issues, like uneven gaps or visible hardware. Therefore, it is often recommended to hire professionals who have experience with the specific challenges presented by custom mirrors.