In the world of manufacturing, the question often arises: are there special coatings that can be applied after cutting? The answer is a resounding yes. There exists a myriad of unique coatings designed specifically to be applied post-cutting, offering a range of advantages from durability enhancement to aesthetic improvement. This article will delve into five key aspects of these special coatings: the variety available, their application process, their benefits and limitations, their durability, and their maintenance needs, as well as their use in specific industries.
Our exploration begins with a look at the types of special coatings for cut surfaces. This section will classify and describe these coatings, shedding light on their unique characteristics and how they differ from one another. Following that, we’ll discuss the application process of these coatings after cutting, providing a step-by-step guide that demystifies this often complex procedure.
We will then weigh the pros and cons in our section on the benefits and limitations of applying coatings after cutting. While these coatings can offer substantial advantages, it’s crucial to understand their potential drawbacks to ensure they’re the right fit for your needs.
Our fourth section will detail the durability and maintenance of post-cutting coatings. How long can you expect these coatings to last? What kind of upkeep do they require? We’ll answer these questions and more.
Finally, we will examine the sector-specific uses and requirements for post-cutting coatings. Whether you’re in the automotive, construction, or aerospace industry, you’ll find valuable information tailored to your field. With this comprehensive guide, you’ll be well-equipped to make informed decisions about applying special coatings after cutting.
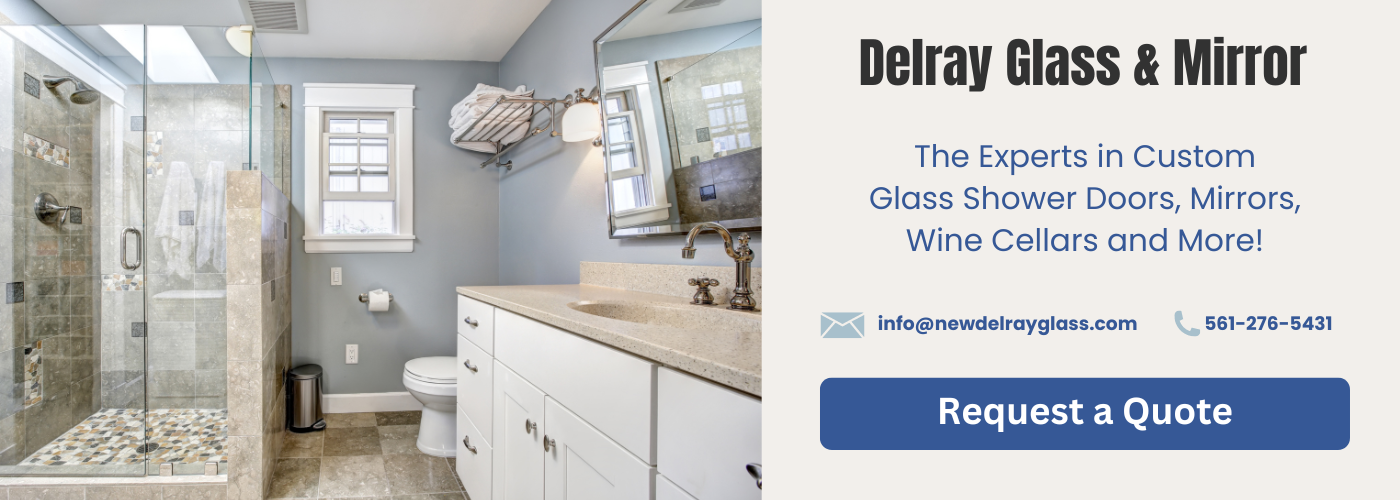
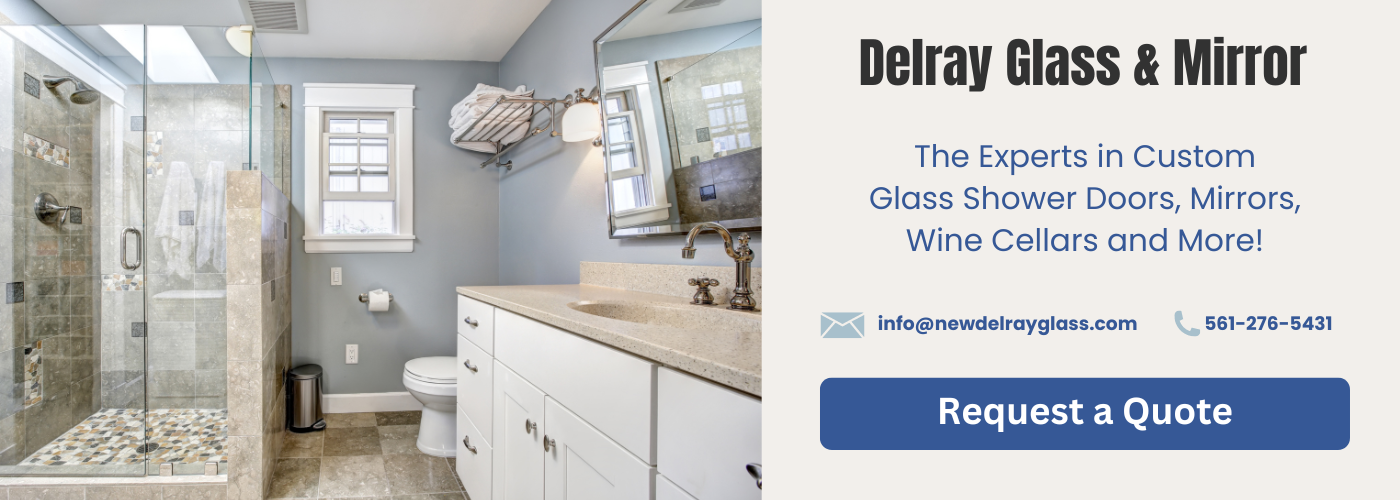
Types of Special Coatings for Cut Surfaces
The types of special coatings for cut surfaces are manifold and each serves a unique purpose. These coatings not only help in enhancing the appearance of the cut surfaces but also extend their lifespan by providing a protective layer against various damaging factors such as rust, corrosion, and abrasion.
The selection of the coating type primarily depends on the material that has been cut and the environment in which it will be used. For instance, cut metals often require anti-corrosion coatings such as galvanization or powder coating. On the other hand, cut wood surfaces might need varnish or paint to protect them from moisture and pests.
There are also special coatings designed for cut surfaces in high-temperature environments. These coatings resist heat and protect the underlying material from thermal damage. Then, we have anti-graffiti coatings which are applied to cut surfaces in public spaces to prevent damage from vandalism.
Each of these coating types has unique properties and is applied using specific techniques to ensure maximum effectiveness. Therefore, understanding the types of special coatings for cut surfaces is crucial to make informed decisions about surface protection post-cutting.
The Application Process of Coatings After Cutting
The application process of coatings after cutting forms an integral part of many manufacturing, production, and construction processes. It involves the application of a specialized coating onto a freshly cut surface to protect it from various elements, enhance its functionality, or improve its aesthetic appeal. This process plays a pivotal role in extending the lifespan of the cut material, whether it’s metal, wood, or other types of material.
The process begins immediately after the cutting phase to ensure the material’s surface doesn’t get exposed to harmful elements that could lead to deterioration. It usually involves cleaning the cut surface to remove any debris or residue from the cutting process. This is an essential step as it ensures the coating adheres properly to the surface.
Once the surface is clean, the coating is applied. The method of application varies depending on the type of coating and the material. It could be as simple as spraying the coating onto the surface or a more complex process involving heat or electricity. The coating is then left to dry or cure, again depending on the specific type of coating.
The application process of coatings after cutting is a precise operation that requires knowledge and expertise. It’s also customizable, with different types and methods of coating available to suit the needs of various industries and applications. Therefore, understanding this process can help optimize the performance and durability of cut materials, contributing to overall project success.
Benefits and Limitations of Applying Coatings After Cutting
The application of coatings to cut surfaces can yield numerous benefits. Firstly, these special coatings can add an extra layer of protection to the material, preventing it from corroding or rusting over time. This is especially important for metals that are susceptible to oxidation. Secondly, coatings can enhance the aesthetic appeal of the cut surface by providing a polished, glossy, or textured finish. In industries such as automotive or interior design, this can significantly increase the value of the end product.
However, despite the apparent benefits, there are also limitations to applying coatings after cutting. One of the main challenges is ensuring that the coating is applied evenly. If not done correctly, it can lead to inconsistencies in appearance and even accelerate the wear and tear of the material. Another limitation is that not all materials are suitable for post-cutting coatings. For example, certain types of plastics may not adhere well to these types of coats.
Furthermore, the application of coatings also demands extra time, resources, and expertise. It can add significantly to the overall production costs. Therefore, it’s crucial for businesses to conduct a cost-benefit analysis before deciding to apply a coating after cutting.
Overall, the benefits and limitations of applying coatings after cutting are context-specific and depend on various factors such as the type of material, the intended use of the product, and the available resources. Despite the potential challenges, with the right planning and execution, post-cutting coatings can be a valuable addition to the production process.
Durability and Maintenance of Post-Cutting Coatings
Durability and maintenance of post-cutting coatings are important considerations in the manufacturing industry. These coatings are applied after the cutting process to protect the surface of the material from environmental factors that may lead to corrosion, wear, and tear. The durability of these coatings depends on several factors such as the type of coating used, the application process, and the environmental conditions the coated material is exposed to.
The maintenance of post-cutting coatings is crucial in enhancing the lifespan of the coated material. Regular checks should be conducted to ascertain the condition of the coating. If any signs of wear are observed, immediate remedial measures should be taken. This could be reapplying the coating or using other protective measures to prevent further deterioration.
Moreover, the type of coating used plays a significant role in the durability and maintenance of post-cutting coatings. For instance, some coatings are more durable and require less maintenance compared to others. Therefore, it is essential to choose a coating that is not only suitable for the material being cut but also in line with the environmental conditions the material will be exposed to.
In conclusion, the durability and maintenance of post-cutting coatings are integral aspects that should be given due consideration in the manufacturing process. They not only protect the cut material but also enhance its lifespan, making it cost-effective in the long run.
Sector-Specific Uses and Requirements for Post-Cutting Coatings
The sector-specific uses and requirements for post-cutting coatings are varied and numerous. These coatings are not a one-size-fits-all solution, but rather, they need to be tailored to the specific needs of each sector. This is because different industries have different needs and requirements when it comes to the properties and characteristics of their cut surfaces.
In the automotive sector, for instance, post-cutting coatings are often used to prevent corrosion and enhance the overall durability of the parts. This is crucial in ensuring the longevity and safety of the vehicles. The coatings used in this sector must be able to withstand high temperatures and harsh conditions without compromising their protective properties.
In the aerospace industry, coatings are used to protect the cut surfaces from extreme environmental conditions, such as high temperatures, high pressure, and corrosive environments. The coatings used in this sector must be able to maintain their protective properties even under these extreme conditions.
In the electronics industry, on the other hand, coatings are primarily used to protect the cut surfaces from moisture, dust, and other contaminants that can affect the performance of the electronic components. These coatings must be able to provide a high level of protection without affecting the functionality of the electronic components.
In summary, the sector-specific uses and requirements for post-cutting coatings are diverse and complex. It’s important for manufacturers to understand these requirements in order to choose the right coatings for their specific needs.