In the intricate world of glass manufacturing, one question stands paramount: Are your glass cutting methods compliant with industry standards? Adherence to these standards isn’t just a matter of legality, but also of ensuring safety, productivity, and the overall quality of the finished product. This article will delve into the crucial aspects of compliance as it pertains to glass cutting, providing a comprehensive understanding of what it means to meet industry standards.
Our first topic of discussion will be gaining a fundamental understanding of industrial standards for glass cutting. We’ll explore the governing bodies that define these standards and the critical elements that constitute compliant practices. Following this, we will turn our attention to the safety protocols in glass cutting. Safety is a cornerstone of the industry, and we’ll outline the measures that must be in place to protect workers and maintain operational integrity.
We’ll then delve into the various equipment used in compliant glass cutting methods, focusing on the technology and tools that align with industry standards. This section will give you an insight into the importance of using the right resources in achieving compliance. Subsequently, we will examine the role of quality control in glass cutting compliance, highlighting how regular inspections and checks can ensure continual adherence to standards.
Finally, we will take a look at the training and skills required for compliant glass cutting. This section will underline why a well-trained workforce is the bedrock of any compliant operation. Join us as we navigate these complex topics to provide a clear understanding of compliance in the glass cutting industry.
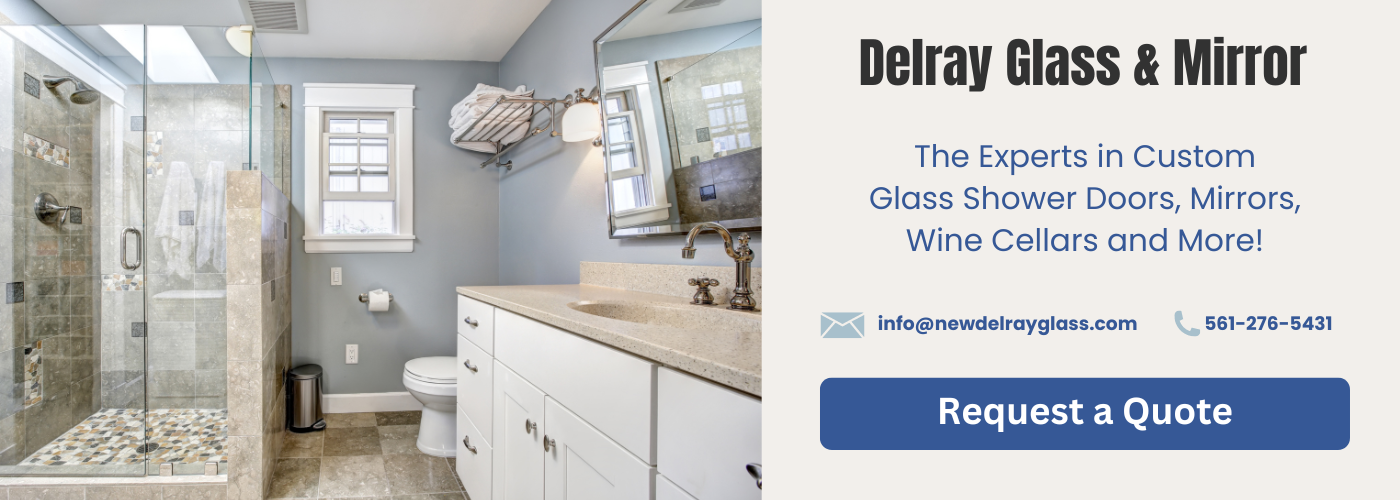
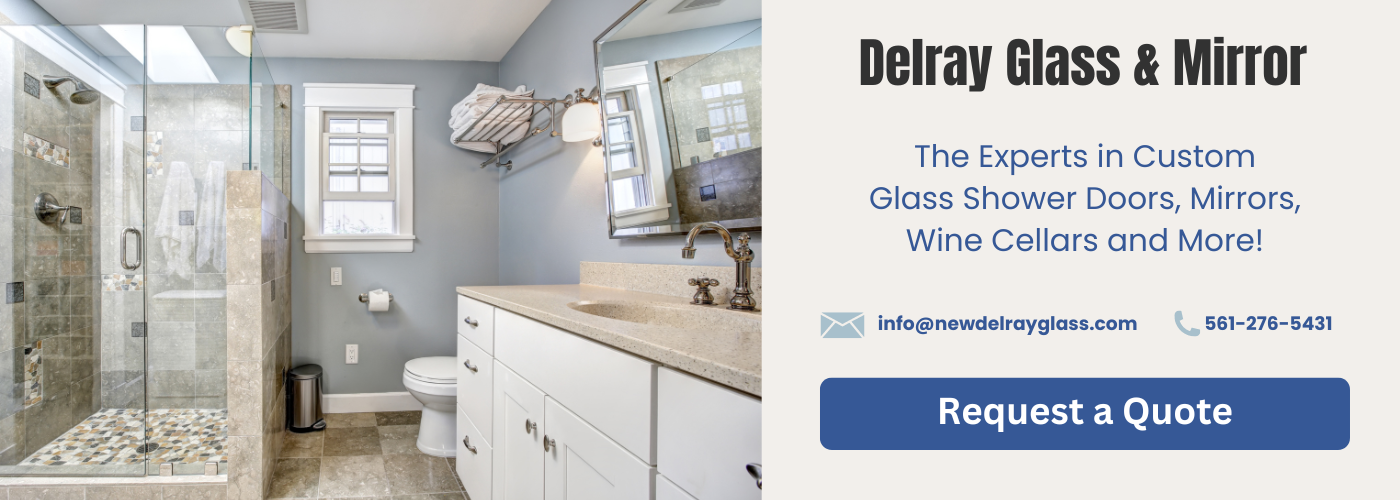
Understanding Industrial Standards for Glass Cutting
Understanding industrial standards for glass cutting is an integral part of ensuring compliance and maintaining a high level of quality in the glass industry. These standards are established by various industry bodies and provide guidelines on the best practices, safety measures, and efficient methods to be used during the glass cutting process.
The industrial standards for glass cutting cover a broad range of aspects. They define the acceptable dimensions and tolerances, the types of glass that can be used, the cutting techniques, and the machinery and equipment required. In addition, they may also outline the necessary protective measures to safeguard the workers and the environment.
By following the industrial standards for glass cutting, companies can ensure that their products meet the required quality, safety, and performance criteria. It also helps them to avoid potential legal issues and penalties, improve their operations, and provide a better service to their customers. Therefore, a deep understanding of these standards is crucial for any organization involved in the glass cutting industry.
Safety Protocols in Glass Cutting
Safety Protocols in Glass Cutting are an essential aspect of the glass cutting industry, and its importance cannot be overstated. These protocols are carefully designed to ensure that the process of cutting glass is conducted safely and effectively, minimizing the risk of injury to personnel and damage to equipment.
The nature of glass cutting involves handling sharp and potentially dangerous materials, making safety protocols a critical part of the process. These protocols often include measures such as using appropriate personal protective equipment (PPE), following correct procedures for handling and cutting glass, and implementing proper training programs.
Firstly, the use of PPE is paramount in preventing accidents. This could include items such as safety glasses, gloves, and protective clothing to shield the body from potential harm caused by broken or sharp glass.
Secondly, the correct procedures for handling and cutting glass are also a crucial part of these safety protocols. This could include instructions on how to correctly handle glass to prevent breakage or injury, as well as specific steps for using glass cutting equipment safely and effectively.
Finally, proper training programs are a vital part of safety protocols. These are designed to ensure that all personnel involved in the glass cutting process are fully aware of the risks involved and know how to mitigate them effectively. This training can include both theoretical knowledge and practical skills, providing a comprehensive approach to safety in the glass cutting industry.
In conclusion, Safety Protocols in Glass Cutting are a fundamental aspect of industry standards, ensuring a safe and efficient working environment. By implementing these protocols, companies can ensure they are compliant with industry standards, providing a safer working environment for their staff and producing high-quality, safe products for their customers.
Equipment Used in Compliant Glass Cutting Methods
In the glass cutting industry, utilizing the right equipment is crucial to ensure compliance with industry standards. The equipment used in compliant glass cutting methods is designed to ensure precision, safety, and efficiency, making it an integral part of the process.
Most compliant glass cutting methods use specialized machines like CNC glass cutters, waterjet cutters, or laser cutters. These machines offer high precision cutting, minimizing waste and ensuring the quality of the final product. They are also designed to reduce the risk of injury, as they limit direct human contact with the cutting process.
Apart from these machines, other necessary equipment includes protective gear for workers, such as gloves, safety glasses, and protective suits. This gear is designed to minimize the risk of injury from shards of glass or equipment malfunctions.
The choice of equipment can also have a significant impact on the efficiency of the glass cutting process. Modern glass cutting machines often have features like automated loading and unloading systems, and programmable cutting patterns. These features reduce the time required for cutting and increase the overall efficiency of the process.
In conclusion, the equipment used in compliant glass cutting methods is a key factor in maintaining industry standards. It contributes to the quality, safety, and efficiency of the glass cutting process, making it a vital consideration for any business in the industry.
Quality Control in Glass Cutting Compliance
Quality Control in Glass Cutting Compliance is a crucial aspect of the overall glass cutting process. This subtopic dives into the important role that quality control measures play in ensuring that the glass cutting methods employed are compliant with industry standards.
Quality control measures are put in place to ensure that every piece of glass cut meets the predetermined standards of quality, ensuring that the final product is safe, durable and meets the needs of the customer. These measures can include routine inspections of the equipment used in the glass cutting process to ensure their optimal functioning and adherence to safety standards.
In the context of glass cutting, quality control also involves the checking and verification of the dimensions, thickness, and edge finish of the cut glass. This helps to ensure that the final product is not only aesthetically pleasing but also fit for its intended purpose. For example, a piece of glass cut for a window must be of specific dimensions to fit into the window frame, and it must also be of a certain thickness to withstand the pressures it may face.
Quality control measures also encompass the management of waste materials. In a process like glass cutting, there is bound to be a significant amount of waste generated. Proper management of this waste is essential to minimize its impact on the environment and comply with environmental protection standards.
In a nutshell, Quality Control in Glass Cutting Compliance is not a standalone process but an integral part of the entire glass cutting process. It ensures the quality and safety of the final product while contributing to the overall efficiency and sustainability of the process.
Training and Skills Required for Compliant Glass Cutting
Training and skills are a fundamental part of ensuring compliance with industry standards in glass cutting. It is crucial that individuals involved in this process have a comprehensive understanding and practical experience. This not only assures the quality of the end product but also ensures safety in the workplace.
Glass cutting is a highly specialized field, requiring a unique set of skills. The training for this role involves understanding the properties of different types of glass, the appropriate tools to use, and the techniques to cut glass accurately and safely. This training is essential to maintain the stringent standards set by the industry.
On-the-job training is common in this industry. It provides hands-on experience and a direct understanding of the processes involved. However, it is also supplemented by formal education and certification programs. These programs not only teach the technical skills necessary but also instill a deep understanding of the safety protocols and quality control measures required in compliant glass cutting.
Continuous education and skills development are also essential. As technology advances, the methods and tools used in glass cutting evolve. It is, therefore, necessary for those in the industry to stay abreast of these changes. Regular training updates and refresher courses ensure that the skills of the workforce remain relevant and compliant with the industry standards.
In conclusion, training and skills are a vital aspect of compliant glass cutting. They ensure the quality of the product, the safety of the workers, and the overall adherence to industry standards.