In the world of glassworks, a common query that surfaces recurrently is: Can clients provide their own glass for cutting? This question, while it may seem straightforward, is entwined with various factors that both glass cutting businesses and their clients need to consider. This article aims to delve deep into this topic, covering five critical subtopics that will provide a comprehensive understanding of the question at hand.
Firstly, we will discuss ‘Client-Supplied Glass: Quality and Suitability for Cutting’. This section will explore the importance of the quality of the glass in question and its impact on the final product. We will also assess how suitable a client-provided piece of glass might be for cutting, considering factors such as shape, size, and overall condition.
Next, we will delve into ‘Procedures for Handling and Evaluating Client-Provided Glass’. This segment will provide insight into the necessary steps a glass cutting business needs to undertake when a client brings their own glass. How should the glass be handled? What evaluation process needs to be followed to ensure the glass is suitable for cutting?
The third section, ‘Risks and Liabilities Associated with Using Client-Supplied Glass’, will shed light on the potential dangers and responsibilities that come with using glass supplied by the client. Are there additional risks involved? Who is liable should something go wrong?
Following this, we will discuss ‘Communication and Agreement with Clients on Glass Cutting’. Fostering clear communication and reaching an agreement with clients regarding the glass cutting process is crucial. This portion will highlight best practices for ensuring both parties are on the same page.
Lastly, we will address ‘Cost Implications for Clients Providing Their Own Glass’. Will bringing your own glass to be cut save money, or might it end up costing you more? This final section will delve into the financial aspects of providing your own glass for cutting.
By exploring these subtopics, this article aims to provide a comprehensive answer to the question: Can clients provide their own glass for cutting? Join us as we delve into these facets, providing clarity for both businesses and clients alike.
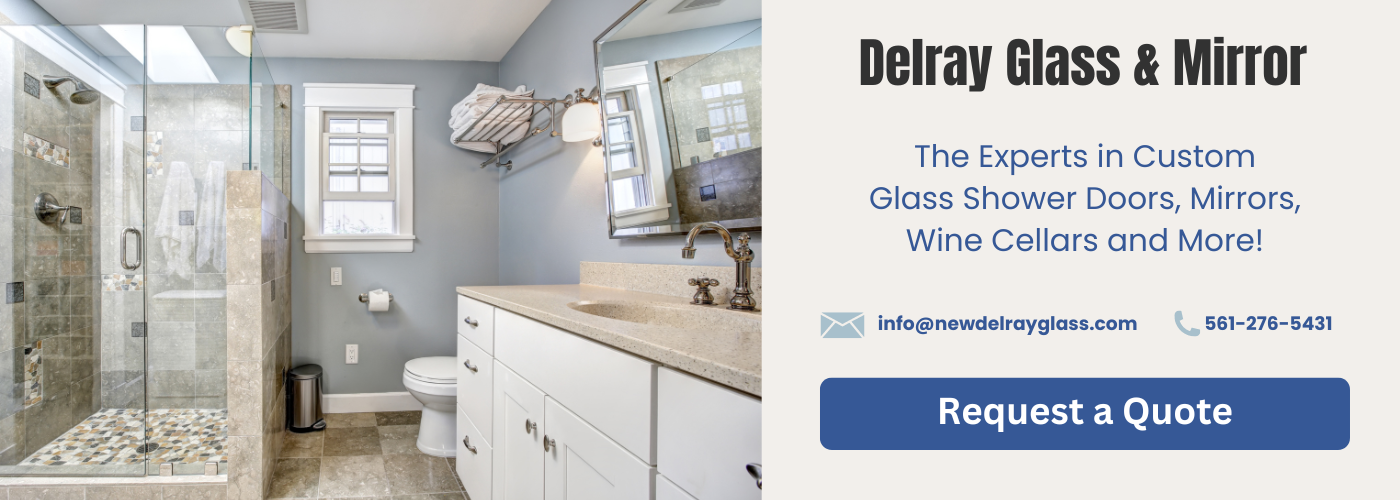
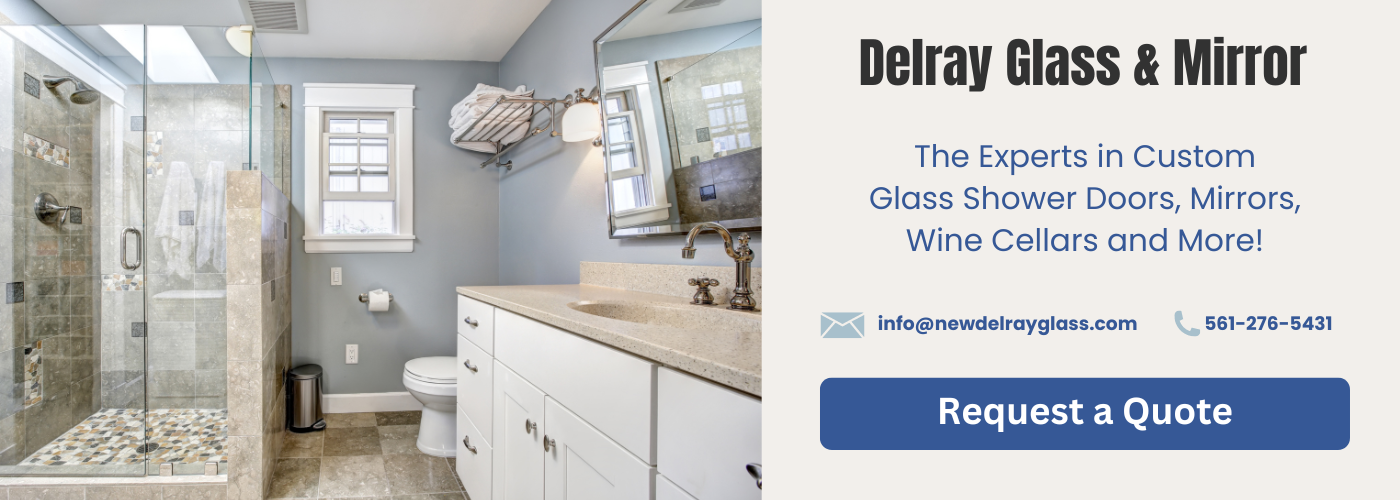
Client-Supplied Glass: Quality and Suitability for Cutting
When it comes to glass cutting, the quality and suitability of the glass play a significant role in the outcome. This is especially true when clients provide their own glass for the process. Client-supplied glass may come in various forms, types, and conditions, which may directly affect the quality and success of the cutting process.
The quality of client-supplied glass may range from excellent to poor, based on how it has been stored, handled, and transported. High-quality glass often results in cleaner cuts and fewer breakages, improving the overall results. On the other hand, poor quality glass may lead to wastage, frequent breakages, and overall poor workmanship, regardless of the cutting techniques applied.
The suitability of the glass for cutting also varies. Not all glass types are suitable for every cutting process. Some may be too thick or too thin, while others may have physical characteristics that make them unsuitable for certain cutting methods. For instance, tempered glass cannot be cut without shattering, while laminated glass requires special tools and techniques.
Therefore, it is essential for clients to understand the implications of providing their own glass for cutting. It requires careful evaluation and understanding of the quality and suitability of the glass to ensure a successful cutting process. It is also important for the clients to communicate with the professionals to understand the potential risks and challenges associated with using their own glass. With this, they can make informed decisions and be prepared for any possible outcomes.
Procedures for Handling and Evaluating Client-Provided Glass
The second item, “Procedures for Handling and Evaluating Client-Provided Glass”, is a crucial aspect in the discussion of whether clients can provide their own glass for cutting. This refers to the set of guidelines and protocols that companies must follow when a client supplies their own glass for cutting.
First and foremost, it is important to handle the client-provided glass with utmost care to avoid any damage that may compromise the cutting process. Proper handling techniques must be observed at all times. This includes wearing the appropriate safety gear, using suitable equipment for transport, and storing the glass in a safe and secure location until it is ready to be cut.
Evaluating the client-provided glass is equally important. A thorough examination of the glass should be conducted to assess its quality and suitability for the cutting process. This involves checking the glass for any visible defects such as scratches, chips, or cracks that could potentially affect the outcome of the cutting process. The type and thickness of the glass should also be taken into consideration as these factors can greatly influence the cutting techniques and tools to be used.
Additionally, the glass should be tested to ensure that it can withstand the cutting process without breaking or causing safety hazards. Depending on the nature of the glass and the specific requirements of the client, certain tests may need to be performed such as stress tests or impact tests.
In conclusion, the procedures for handling and evaluating client-provided glass are key to determining whether clients can provide their own glass for cutting. Not only do these procedures ensure the safety and success of the cutting process, but they also help to build trust and confidence between the company and the client.
Risks and Liabilities Associated with Using Client-Supplied Glass
When clients provide their own glass for cutting, there are several risks and liabilities to consider. One of the main risks is the condition and quality of the glass. If the glass is damaged or of poor quality, it may not withstand the cutting process, leading to breakage and potential injury. Moreover, the client may not be aware of the exact specifications of the glass, such as its composition, thickness, or durability, which can also impact the success of the cutting process.
Another risk involves the accuracy of the cutting. When using client-supplied glass, there’s the possibility that the glass may not be cut to the exact specifications required. This could be due to miscommunication between the client and the service provider, or the client’s misunderstanding of the glass cutting process.
Additionally, there are potential legal liabilities. If the client’s glass is damaged during the cutting process, or if the finished product doesn’t meet the client’s expectations, the service provider may be held liable. This could lead to disputes, legal action, and damage to the service provider’s reputation.
To mitigate these risks, it’s crucial for service providers to have clear policies and procedures in place for handling and evaluating client-supplied glass. They should also communicate these policies clearly to their clients, and ensure they have the client’s agreement before proceeding with the cutting process.
Communication and Agreement with Clients on Glass Cutting
The aspect of communication and agreement with clients on glass cutting is an integral part of the process when clients provide their own glass for cutting. This primarily involves discussions regarding the feasibility of the glass provided, the design requirements, and the potential risks involved. It’s crucial to ensure that the clients understand all the details and nuances before the cutting process commences.
There are several elements that need to be discussed and agreed upon in the communication process. The first is the quality and suitability of the glass provided by the client. The glass cutting service provider needs to make sure that the glass is of appropriate quality and thickness and is suitable for the specific design the client wants to achieve.
Next, the service provider needs to communicate the technicalities involved in the cutting process. This includes explaining to the client the equipment and techniques to be used and the time it will take. It also involves discussing any potential challenges that might arise during the process.
Another important aspect of communication is the discussion of risks and liabilities. The client needs to be made aware of the potential risks involved in using client-supplied glass, including the possibility of breakage or damage during the cutting process. The service provider also needs to clearly state their policy regarding such risks and liabilities.
Lastly, the cost implications for clients providing their own glass need to be clearly communicated. The service provider needs to explain how the costs might vary depending on the quality and size of the glass provided, the complexity of the design, and any additional services required.
In conclusion, effective communication and agreement with clients on glass cutting are crucial to ensure a smooth and successful process. It helps avoid misunderstandings, ensures the client’s expectations are met, and reduces the likelihood of disputes or dissatisfaction.
Cost Implications for Clients Providing Their Own Glass
The cost implications for clients providing their own glass for cutting depends on several factors. One of the most significant factors is the quality and suitability of the client-supplied glass. If the quality is high and the glass is well-suited for the intended application, it may result in cost savings. This is because the client could potentially source the glass at a lower price than the glass cutting company. However, it is important for the client to understand that the glass must meet certain standards to be suitable for cutting.
There are also potential additional costs associated with using client-supplied glass. For example, the glass cutting company may charge a handling fee for evaluating and processing client-provided glass. This is to cover the time and resources required to ensure the glass is safe and suitable for cutting. If the glass is found to be unsuitable, the client may also be responsible for the cost of procuring replacement glass.
Furthermore, using client-supplied glass could potentially increase the risk and liabilities for both the client and the glass cutting company. If the glass breaks or causes an accident during cutting, the client may be held responsible. This could result in additional costs, such as repair or replacement costs, or even legal fees in extreme cases.
In conclusion, while providing their own glass for cutting could potentially save clients money, it also comes with potential risks and additional costs. It is therefore crucial for clients to consider all these factors and discuss them thoroughly with the glass cutting company before deciding to supply their own glass.