The world of insulated glass is far more versatile and adaptable than one might initially expect. One of the burning questions often asked is: Can insulated glass be customized for specific dimensions? The answer is a resounding yes. This article aims to shed light on the intriguing process of customizing insulated glass dimensions, providing a comprehensive view of this subject.
We start by delving into the intricate process of customizing insulated glass dimensions, outlining the steps taken to tailor these materials to specific measurements. Understanding this technique can provide valuable insight into the level of customization achievable with insulated glass. Following this, we will discuss the various factors that affect the customization of insulated glass. From the type of glass used to the desired level of insulation, these influential elements play a crucial role in determining the feasibility and process of customization.
However, like all good things, there are limitations in customizing insulated glass dimensions. We will examine these constraints, exploring the technical and practical boundaries that can potentially impede the customization process. Additionally, we’ll take a look at the impact of custom dimensions on the overall performance of insulated glass. Customization can affect several performance aspects, including insulation capacity, strength, and durability.
Lastly, we’ll delve into the cost implications of customizing insulated glass dimensions. While customization provides the advantage of specific dimensions, it can also come at a higher price than standard-sized insulated glass units. By the end of this article, you will have a well-rounded understanding of the ins and outs of customizing insulated glass dimensions, helping you make informed decisions for your next project.
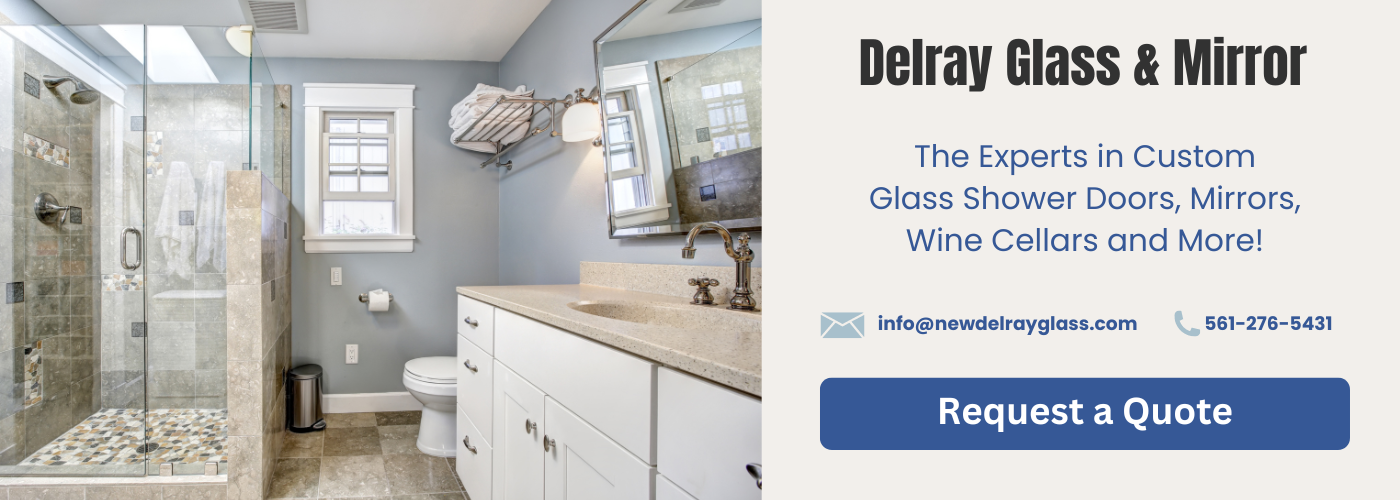
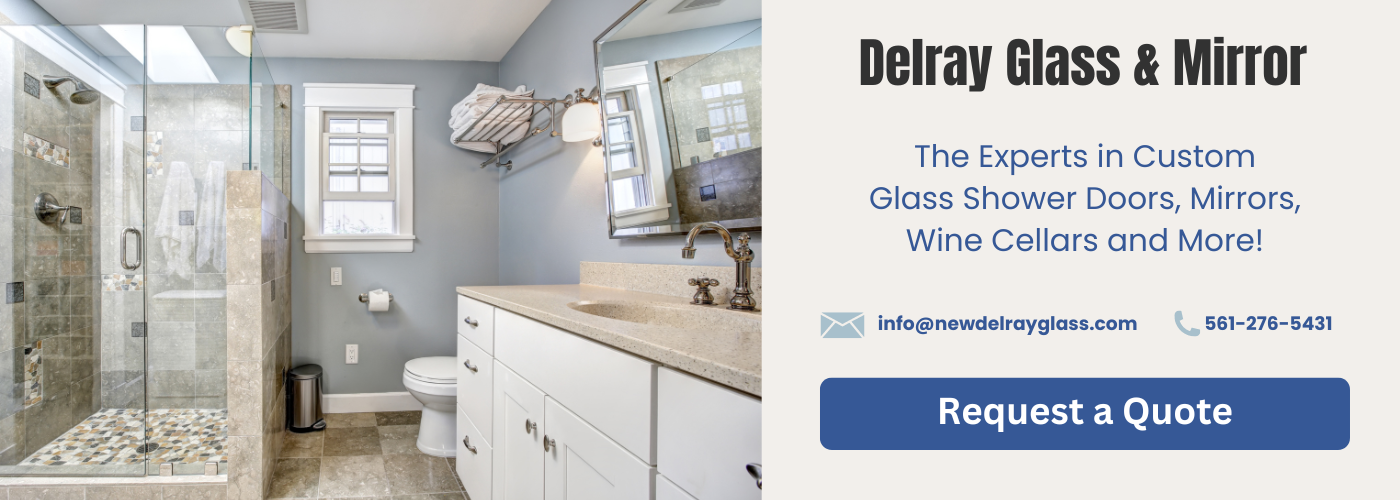
The Process of Customizing Insulated Glass Dimensions
The process of customizing insulated glass dimensions is a sophisticated and meticulous one. It starts with understanding the specific needs of the client. Each project is unique, and the dimensions required for insulated glass will vary depending on a range of factors such as the size of the windows, the design of the building, and the desired energy efficiency.
The initial step typically involves taking accurate measurements of the space where the insulated glass will be installed. It is crucial to ensure that the measurements are correct, as any inaccuracies can lead to complications during the installation process.
The next stage involves the actual production of the insulated glass. The two glass panes are cut according to the precise dimensions obtained from the measurements. The space between these panes is then filled with an insulating material, typically a gas like argon or krypton. This space is what gives insulated glass its thermal efficiency, helping to maintain a comfortable temperature inside the building, regardless of the weather conditions outside.
Once the insulated glass units are made, they are thoroughly inspected to ensure they meet the required standards and dimensions. The final step is the installation process, where the customized insulated glass units are fitted into the existing window frames.
Overall, the process of customizing insulated glass dimensions involves a combination of technical expertise, precision, and a deep understanding of the client’s needs. It’s a task that requires a high degree of professionalism and attention to detail.
Factors Affecting the Customization of Insulated Glass
When it comes to the customization of insulated glass for specific dimensions, several factors come into play. These factors largely affect the feasibility, process, and results of the customization process. It’s crucial to understand these factors to make informed decisions and achieve the desired outcomes.
Firstly, the type of insulated glass is an essential factor. Different types of insulated glass, such as double glazing and triple glazing, have different customization possibilities due to their structural differences. For instance, triple glazing may offer less flexibility in customization because of its additional glass layer.
Secondly, the size and shape of the window or door where the insulated glass will be installed also play a critical role. The dimensions must be accurately measured to ensure the customized insulated glass fits perfectly. Additionally, more complex shapes may require more extensive customization processes.
Material availability is another key factor. The materials used for the glass and the insulating layer, such as argon gas or low-emissivity coatings, can affect the customization options. Certain materials may not be available in all sizes or may not be suitable for specific dimensions.
Lastly, the manufacturing process and technology used by the glass company can also affect the customization of insulated glass. Some companies may have advanced machinery and techniques that allow for a wider range of customization options, while others may be more limited.
In conclusion, while it is indeed possible to customize insulated glass for specific dimensions, it’s vital to consider these factors to ensure the process runs smoothly and yields the desired results.
Limitations in Customizing Insulated Glass Dimensions
The customization of insulated glass dimensions allows homeowners and builders to have a perfect fit for their specific window frames. However, it’s essential to understand that there are certain limitations in this process. Despite the customization capabilities, not all sizes and shapes are possible to produce due to the inherent properties of the materials used and the manufacturing constraints.
These limitations primarily arise from the fact that insulated glass units are made by sealing two or more glass panes together with a gap in between. This gap is filled with a gas like argon or krypton to enhance the insulating properties of the unit. If the desired dimensions are too large, it can pose a challenge as the sealing process may not effectively encapsulate the insulating gas, leading to a loss in its insulating properties.
Similarly, if the desired dimensions are too small, it may be difficult to ensure a uniform gap between the panes, leading to an uneven distribution of the insulating gas and hence, compromised insulating performance. Additionally, the physical characteristics of the glass itself may also restrict the possible dimensions. For instance, extremely thin glass may be prone to breakage during the manufacturing process, and very thick glass may be difficult to cut and shape accurately.
Therefore, while it is possible to customize the dimensions of insulated glass, it’s important to work closely with the manufacturer to understand the potential limitations and adjust the design accordingly to ensure optimal performance and durability of the final product.
Impact of Custom Dimensions on Insulated Glass Performance
The impact of custom dimensions on insulated glass performance is a crucial factor to consider when opting for customized insulated glass. Insulated glass, also known as double glazing, is designed to help regulate indoor temperatures, reduce energy costs, and limit noise pollution. However, the effectiveness of these benefits can be influenced by the specific dimensions of the glass.
For instance, the thickness of the glass plays a significant role in its insulating properties. Thicker glass generally provides better insulation, but it also adds to the weight and cost of the installation. Similarly, the size of the glass panels can affect the structural integrity of the installation. Larger panels might require additional support structures, which could complicate the installation process and add to the overall costs.
The gap between the glass panes in an insulated glass unit also has an impact on its performance. This space is typically filled with a gas like argon, which acts as an insulator. The width of this gap can be adjusted according to specific requirements, but it’s important to note that a larger gap may not always result in better insulation. There’s an optimal range for this distance, beyond which the insulating properties of the unit may start to decrease.
In conclusion, while customizing the dimensions of insulated glass can provide greater flexibility in terms of design and installation, it’s crucial to consider the impact of these custom dimensions on the performance of the glass. By understanding these factors, one can make informed decisions and ensure that the customized insulated glass meets their specific needs while maintaining its efficacy.
Cost Implications of Customizing Insulated Glass Dimensions
Customizing the dimensions of insulated glass comes with several cost implications. The process of customization often involves modifying the standard manufacturing processes to achieve specific dimensions. This can require additional labor, time, and resources, all of which can increase the overall cost of the insulated glass.
A key factor that affects the cost of customizing insulated glass dimensions is the size and complexity of the desired dimensions. Larger or more complex dimensions may require more materials or specialized machinery to produce, thereby driving up costs. Conversely, smaller or simpler dimensions may be easier and cheaper to produce, but may still cost more than standard-sized glass due to the need for customization.
In addition, the cost of customizing insulated glass dimensions can also be affected by the type and quality of the materials used. High-quality materials often come at a higher cost, but can also provide better insulation and durability. Similarly, using specialized or innovative materials can also increase costs, but may offer unique advantages such as improved energy efficiency or superior aesthetic appeal.
It’s important for customers to weigh these cost implications against the benefits of having insulated glass with custom dimensions. While it may be more expensive upfront, the long-term benefits such as improved energy efficiency and increased property value can make it a worthwhile investment.