Safety glass is an essential material that offers both protection and aesthetic appeal in a range of different applications. But can safety glass be customized in terms of size and shape? The answer is yes; safety glass can indeed be tailored to meet specific demands, but the process, as well as the potential limitations, can vary greatly depending on several factors. This article aims to delve deeper into this topic, providing a comprehensive guide to customizing safety glass.
Our first focus will be on the different types of safety glass available in the market. Each type offers unique qualities and benefits, which may influence their suitability for customization. Following this, we will take you through the process of customizing safety glass, shedding light on the techniques and technologies that make this possible.
Despite the versatility of safety glass, there are still certain limitations when it comes to customization. We will explore these constraints, helping you understand what is achievable and what may not be possible in the realm of safety glass customization. Furthermore, we will look into the factors that affect the size and shape of safety glass, including technical considerations and practical aspects that play a role in the customization process.
Finally, we will delve into the various applications and uses of custom safety glass, illustrating how this material can be utilized across different industries and sectors. Whether you’re a homeowner, a business owner, or a professional in the construction or interior design industry, this article will offer valuable insights into the world of custom safety glass.
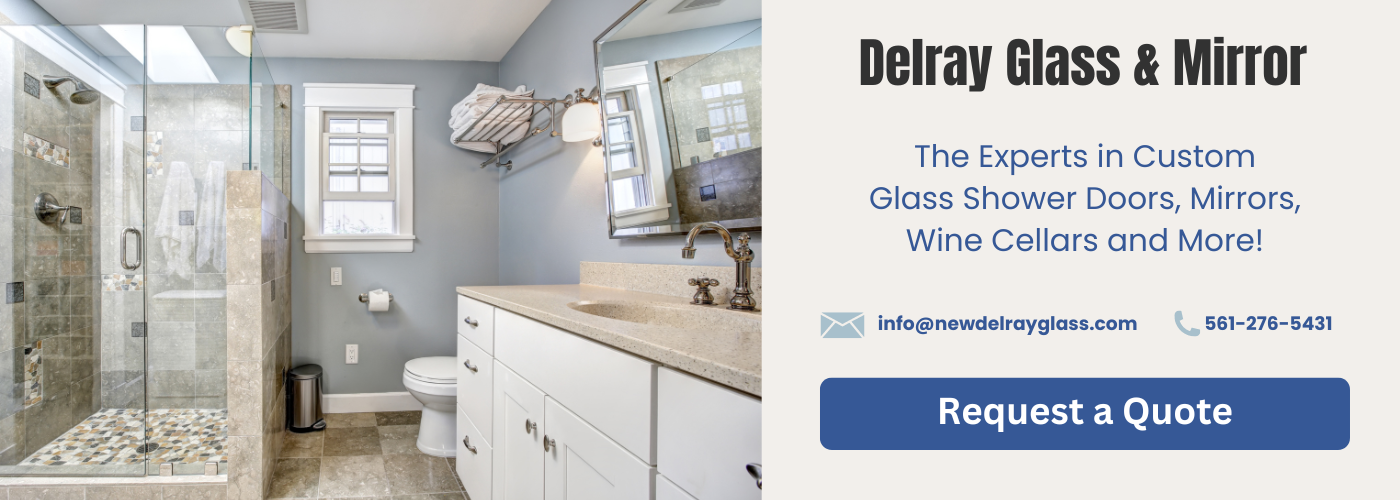
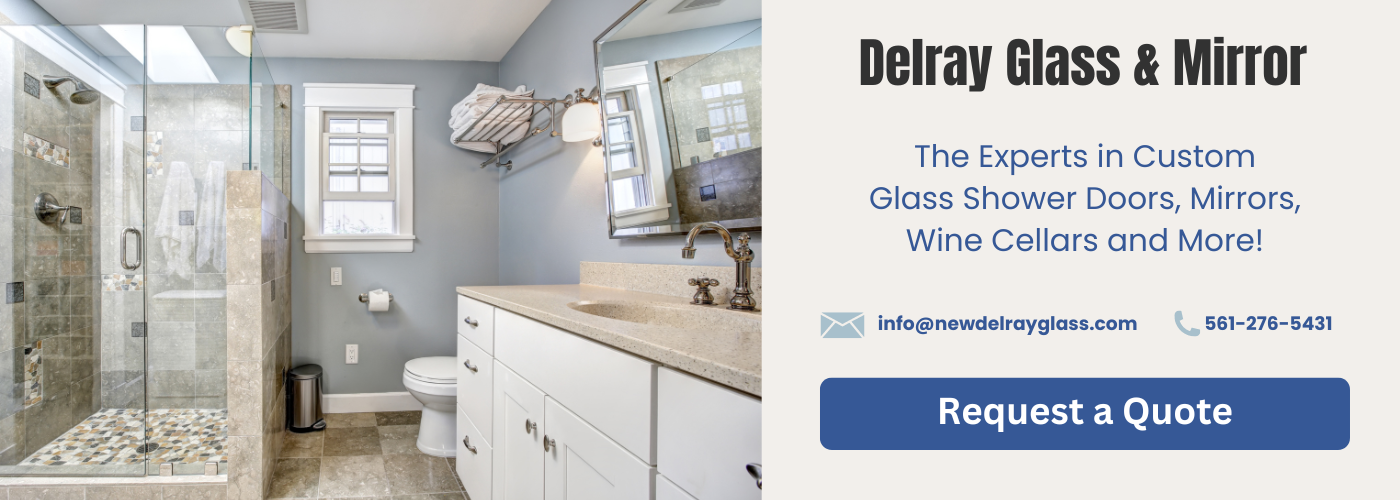
Different Types of Safety Glass
Safety glass is a type of glass specifically designed to be less likely to break, and less likely to pose a threat when it does break. The term “safety glass” is usually applied to types of glass that are manufactured through controlled thermal or chemical treatments to increase its strength compared with normal glass. The key feature of safety glass is its potential to prevent injury, as it tends to break into small granular pieces rather than sharp shards.
There are two main types of safety glass: tempered glass and laminated glass. Tempered glass is created by heating regular glass to high temperatures and then rapidly cooling it down, a process which makes it four to five times stronger than regular glass. If broken, tempered glass shatters into small, relatively harmless pieces.
Laminated safety glass, on the other hand, consists of two or more layers of glass held together by a plastic interlayer. The plastic layer provides strength to the glass and keeps it from shattering upon impact. Instead, the glass fragments stick to the plastic layer, preventing injury.
These different types of safety glass can be customized in terms of size and shape, making them highly versatile for a wide range of applications. Whether it is for vehicle windows, eyewear, or architectural applications, safety glass can be designed and fabricated to meet specific needs.
Process of Customizing Safety Glass
The process of customizing safety glass is a complex and precise operation that requires the integration of advanced technology and skilled craftsmanship. The primary objective of customization is to meet the unique needs of the client by altering the size and shape of the safety glass.
The process begins with the client specifying their desired dimensions and shape. This can range from standard rectangles and squares to more complex shapes like circles, ovals, or even custom designs. Once the specifications are defined, they are input into a computerized system that guides the cutting process. This ensures maximum accuracy and minimal waste.
The glass is then subjected to a series of treatments to enhance its safety properties. This typically involves heating the glass to extreme temperatures, then rapidly cooling it in a process known as tempering. This alters the internal structure of the glass, making it much stronger and more resistant to breakage. If the glass does break, it shatters into small, blunt pieces that are less likely to cause injury.
Another key part of the customization process is the addition of a safety interlayer. This is a thin sheet of plastic or resin that is sandwiched between two layers of glass. In the event of breakage, this interlayer holds the shattered pieces together, preventing them from scattering and causing potential harm.
Customizing safety glass is a highly specialized process that requires a deep understanding of the material and its properties. Each piece is carefully crafted to meet the specific needs of the client, ensuring that the final product is not only safe, but also aesthetically pleasing and functional.
Limitations in Customizing Safety Glass
Safety glass is a general term used to describe a type of glass that is designed to resist breaking, or to break in a way that prevents injury. It is commonly used in environments where there is a risk of impact, such as in cars, buildings, and protective eyewear. The customization of safety glass in terms of its size and shape has certain limitations.
When customizing safety glass, manufacturers need to consider the nature of the material, the method of production, and the intended application. In terms of material, safety glass typically involves a layer of plastic sandwiched between two sheets of glass. This structure, while providing increased safety, can pose challenges in terms of customization. For instance, the thickness and pliability of the plastic layer may limit the extent to which the safety glass can be molded into certain shapes.
The process of producing safety glass, particularly tempered glass, is another factor that can limit customization. The tempering process involves heating the glass to high temperatures and then rapidly cooling it, which strengthens the glass but also makes it more difficult to cut or reshape afterwards. Therefore, any customization in terms of size or shape needs to be done prior to the tempering process, which requires careful planning and precision.
Additionally, the intended use or application of the safety glass can also influence its customization. For example, safety glass used in vehicles or building windows may need to conform to certain safety standards or regulations, which can limit the extent to which they can be customized.
In conclusion, while safety glass can be customized to a certain degree, there are inherent limitations in the materials, production process, and intended use that need to be taken into account.
Factors Affecting the Size and Shape of Safety Glass
The size and shape of safety glass can be customized; however, there are certain factors that can impact the extent to which this is possible. These factors often include the manufacturing process, the specific requirements of the project, and the properties of the glass material itself.
In the manufacturing process, the glass is cut before it is tempered. This means that the dimensions and shape of the glass must be precisely determined before the tempering process begins, as any alterations after tempering can cause the glass to shatter. Therefore, the size and shape of safety glass are largely determined during the initial stages of production.
The specific requirements of the project also play a significant role in determining the size and shape of safety glass. For instance, certain architectural designs may require curved or unusually shaped glass, while others require large, flat panels. In such cases, the glass must be manufactured to meet these specific requirements, which can sometimes pose challenges in terms of production and installation.
Lastly, the properties of the glass material itself can affect its size and shape. Different types of glass have different properties, including their strength, flexibility, and resistance to impact. These properties can limit the extent to which the glass can be customized in terms of size and shape. For example, some types of safety glass may be more difficult to cut into intricate shapes or large sizes due to their physical properties.
In conclusion, while the size and shape of safety glass can be customized, there are various factors that can influence this customization. Understanding these factors can help in making informed decisions when planning for the use of safety glass in different applications.
Custom Safety Glass Applications and Uses
Custom safety glass plays a vital role in various fields due to its versatility and durability. Its ability to be customized to various shapes and sizes has made it a preferred choice for many applications where safety and durability are of paramount importance.
One of the most common uses of custom safety glass is in the automotive industry. Cars, buses, and other vehicles utilize custom safety glass for windshields and windows. These glasses are specifically designed to withstand high impacts and, in case of breakage, to crumble into small, granular pieces that are less likely to cause injury, unlike regular glass that shatters into sharp shards.
In the construction industry, custom safety glass is used in windows, doors, and even in structural elements in modern architecture. It provides not only safety but also aesthetic appeal. Safety glass can be customized to fit unique architectural designs without compromising on safety, making it a favored choice for many architects and builders.
In addition, custom safety glass is also used in various protective equipment such as goggles and face shields. It’s commonly used in industries where workers are exposed to hazardous conditions, providing them with reliable and durable protection.
Furthermore, safety glass is making its way into tech gadgets and home appliances. From smartphone screens to microwave oven doors, custom safety glass is being used extensively due to its strength and safety features.
In conclusion, the applications and uses of custom safety glass are extensive and varied, thanks to its ability to be customized in terms of size and shape. Regardless of the industry, safety glass provides a combination of safety, strength, and aesthetic appeal that is hard to match.