Custom mirrors, with their delicate surfaces and often unique shapes, require meticulous attention during packaging to ensure they arrive at their destination in pristine condition. The process of preparing these mirrors for transportation is a fine art that combines robust materials and innovative techniques to protect them from mechanical stresses, environmental factors, and handling errors. This article delves into the comprehensive approach taken to package custom mirrors, focusing on several key aspects that contribute to their safe transit.
First, we will explore the material selection for packaging, which plays a pivotal role in the initial layer of protection. Special attention is given to materials that are not only strong and resilient but also lightweight to keep shipping costs manageable. Next, the discussion will move to protective layering techniques, which involve multiple layers of cushioning and shock-absorbent materials to safeguard the mirror surface from scratches and impacts.
The third focus is on structural support features. These are crucial for maintaining the integrity of the package during transport, especially for larger mirrors that may be prone to bending or breaking. We will examine how customized reinforcements are designed to suit different sizes and shapes of mirrors. Following that, we investigate sealing and waterproofing methods that protect against moisture and dust, elements that can degrade the mirror’s reflective quality over time.
Finally, the article will cover labeling and handling instructions, which are essential for informing logistics personnel about the specific care needed when handling these fragile items. Proper labels and instructions can significantly reduce the risk of damage during handling and transit. By the end of this article, readers will have a thorough understanding of the meticulous care and detailed processes involved in packaging custom mirrors for transportation.
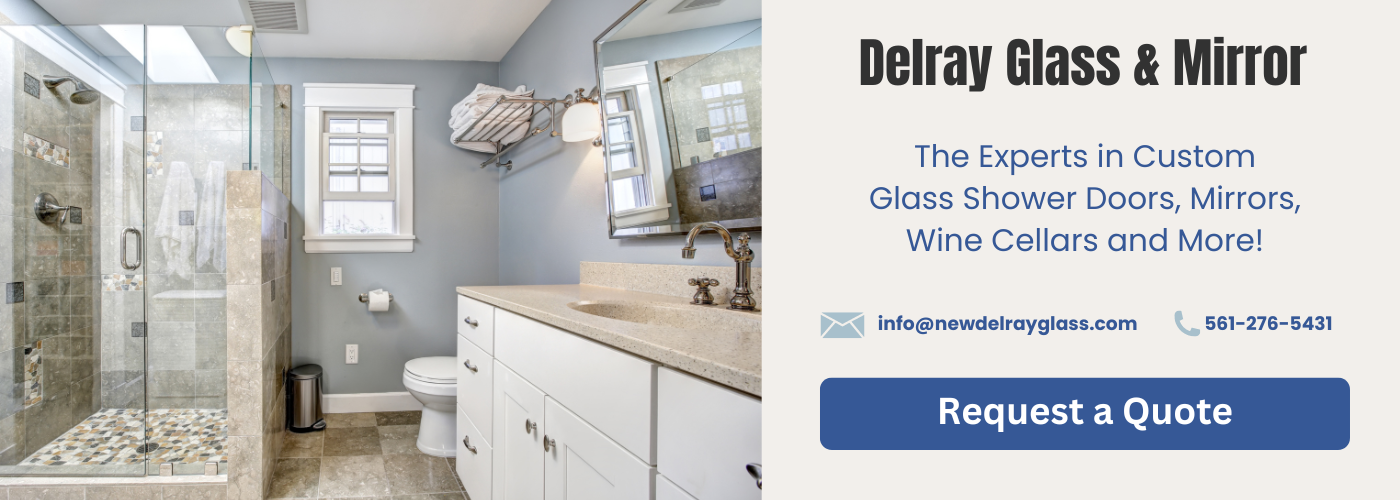
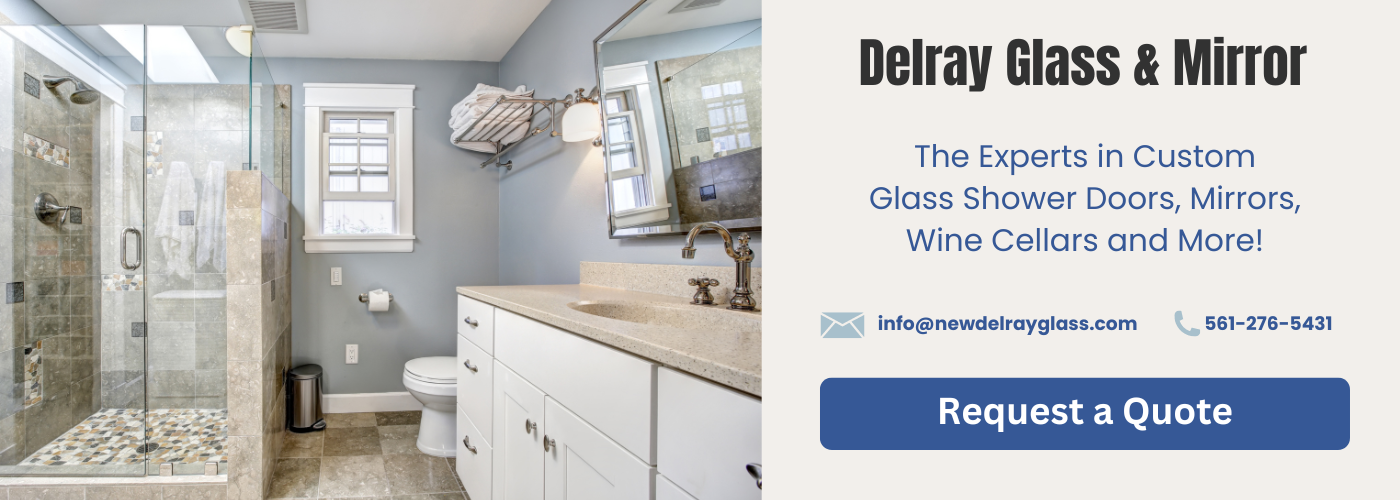
Material Selection for Packaging
When it comes to packaging custom mirrors for transportation, choosing the right materials is crucial to ensure the mirror reaches its destination without any damage. Material selection plays a pivotal role in protecting the mirror against potential threats such as impacts, pressure, or environmental factors during transit.
The primary goal in selecting packaging materials is to cushion and shield the delicate glass surface of the mirror. Typically, materials like polyethylene foam, bubble wrap, or padded corrugated cardboard are used due to their shock-absorbing properties. These materials can effectively dissipate the forces that might otherwise cause cracking or breaking of the glass.
Furthermore, considering the edges and corners of the mirror is essential, as these are the parts most susceptible to chipping. Specialized corner protectors made of dense foam or plastic can be used to safeguard these vulnerable points. Alongside the cushioning and padding, a rigid outer box, usually made from double-walled corrugated cardboard, provides an additional layer of protection. This outer shell not only maintains the integrity of the inner cushioning materials but also resists punctures and crushing forces that are common during shipping.
In addition to physical protection, the material selection for packaging must also consider factors like the weight and cost. Using excessively heavy materials can increase shipping costs, while overly light materials might not offer sufficient protection. Therefore, finding a balance between protection, weight, and cost is essential to optimize the packaging of custom mirrors.
By carefully selecting appropriate packaging materials and combining them effectively, businesses can minimize the risk of damage during transportation, ensuring that mirrors arrive in perfect condition, ready to be installed at their new location.
Protective Layering Techniques
When transporting custom mirrors, one of the most critical aspects to consider is the implementation of protective layering techniques. These techniques are designed to shield the delicate glass surfaces and edges from scratches, chips, and breakage that can occur during handling, shifting, and transit. The primary goal is to ensure that the mirror arrives at its destination in the same pristine condition as when it was dispatched.
The first layer of protection typically involves a soft, non-abrasive material such as foam or bubble wrap. This material acts as a cushion, absorbing shocks and vibrations that are common during transportation. Bubble wrap is particularly favored for its ability to provide both cushioning and flexibility; it can be wrapped tightly around the mirror, conforming to its shape while providing an air-filled barrier against impacts.
In addition to bubble wrap, corrugated cardboard is often used to add an extra layer of protection. Sheets of cardboard can be cut and shaped to match the contours of the mirror, providing a firm shield that helps prevent puncture or pressure damage. For mirrors with exceptionally delicate frames or ornate details, additional soft padding materials, such as felt or special foam inserts, might be used to cover these vulnerable areas specifically.
Moreover, edge protectors made of foam or hardened cardboard can be applied to the edges of the mirror. These protectors serve as a buffer, reducing the risk of chipping or breaking the edges, which are particularly susceptible to damage during movement.
Finally, the entire mirror, once layered with protective materials, is typically placed inside a sturdy wooden crate or a corrugated box that is often custom-fitted to the mirror’s dimensions. This outer casing provides structural integrity, safeguarding the mirror against external pressures and ensuring that it remains stationary within its packaging during the transportation process.
By employing these protective layering techniques, shippers can significantly minimize the risk of damage to custom mirrors during transit, ensuring that these valuable items are delivered safely and securely.
Structural Support Features
Structural support features play a crucial role in the packaging of custom mirrors for transportation. These features are essential to ensure that the mirrors reach their destination without any damage. Custom mirrors, particularly those that are large or uniquely shaped, are vulnerable to stress, pressure, and impact during transit. Therefore, implementing effective structural support within the packaging design is paramount.
The primary aim of structural support is to maintain the integrity of the mirror throughout the shipping process. This can be achieved through various means. For instance, rigid foam inserts are often used to create a protective buffer around the edges and surfaces of the mirror. These inserts are designed to absorb shocks and prevent the mirror from shifting inside the box, which could cause scratches or cracks.
Another common structural support feature is the use of wooden crates. These crates are custom-built to fit the specific dimensions of the mirror. The robustness of wood helps protect against impacts and heavy loads that could otherwise damage the mirror during handling and transportation. Inside the crate, adjustable braces can be used to secure the mirror firmly in place, allowing for little to no movement.
Additionally, some packaging designs incorporate internal frames or cross-bracing elements that reinforce the entire structure. These can be particularly useful when transporting multiple mirrors or very large pieces where the risk of flexing or bending during handling is higher.
In conclusion, the structural support features within the packaging of custom mirrors are tailored to counteract the challenges posed by transportation. By carefully designing these elements, manufacturers and shippers can drastically reduce the risk of damage, ensuring that the mirrors arrive in perfect condition. This careful consideration not only protects the physical product but also preserves the reputation of the manufacturers and satisfies customer expectations.
Sealing and Waterproofing Methods
Sealing and waterproofing are critical steps in the packaging process for custom mirrors, especially when preparing them for transportation. The primary goal of these methods is to protect the mirror from moisture, dirt, and other environmental factors that could potentially damage the surface or degrade the quality of the mirror.
To begin with, sealing typically involves covering all the edges and joints of the packaging material with a strong adhesive tape or sealant. This prevents any external substances from entering the package. It is crucial that the sealing materials used are durable and provide a tight seal to ensure no moisture can penetrate, as moisture can cause the mirror to tarnish or the backing to peel away.
Waterproofing is the next essential step. This might involve wrapping the mirror in a waterproof material such as plastic wrap or a specially designed waterproof cover. These materials act as a barrier against humidity and liquid water, which are prevalent during transit, especially in changing climates or via sea transport.
Together, these sealing and waterproofing methods ensure that the mirror remains in pristine condition from the point of dispatch to the end customer, safeguarding the manufacturer’s reputation and reducing the risk of returns due to damage. Additionally, these methods contribute to the overall structural integrity of the packaging, which is crucial for preventing physical damage during handling and transportation.
Labeling and Handling Instructions
Labeling and handling instructions are crucial aspects of packaging, especially when it comes to delicate items like custom mirrors. These instructions ensure that the mirrors are handled properly throughout their journey, reducing the risk of damage. The labels on the packaging provide essential information such as the nature of the item inside, the side that should face upwards, and whether the item is fragile. This helps in making sure that the handlers are aware of the delicacy of the item and take extra caution during transportation.
Handling instructions are often specific and detailed. They might instruct on how to lift the package correctly or warn against using sharp objects to open the package, which could potentially damage the mirror. Furthermore, the instructions can include tips on the ideal temperature and humidity conditions for the storage of the package during transit. This is particularly important for mirrors, as extreme conditions could lead to deterioration or warping of the materials used in the mirror or its frame.
In addition to providing handling details, labeling also plays a role in the tracking and tracing of the shipment. Barcodes or QR codes can be used to keep track of the location of the package as it moves through various checkpoints. This not only helps in managing the logistics but also provides reassurance to the customer about the safety and progress of their shipment.
Overall, proper labeling and handling instructions are integral to ensuring the safe transportation of custom mirrors. They mitigate the risks associated with transit and handling, thus preserving the quality and integrity of the mirror from the point of dispatch to the point of delivery.