In the world of interior design and bathroom upgrades, frameless shower doors have become a prominent choice given their sleek and modern aesthetic. However, due to their delicate nature, a common query that arises is: How are frameless shower doors packaged and delivered to ensure their safety? This article will delve into this question in detail, shedding light on the process that ensures these delicate items arrive at their destination unharmed.
To start, we’ll examine the various packaging materials used for frameless shower doors, which play a pivotal role in protecting them from any potential harm. Next, we’ll explore the meticulous safety measures implemented during the packaging process, designed to provide an extra layer of security.
Our journey through this topic will then take us to the delivery process of these doors, a stage that requires significant care and professionalism. We will discuss the handling and transportation guidelines that are strictly adhered to, ensuring that the frameless shower doors are not compromised during transit.
Finally, we’ll address the last and equally important aspect of this process: damage control and replacement policies. Despite the rigorous measures taken, there’s always a chance of unforeseen accidents. Hence, understanding the procedures in place for such scenarios is imperative. Through this comprehensive guide, you’ll gain a thorough understanding of how frameless shower doors are packaged and delivered safely to your doorstep.
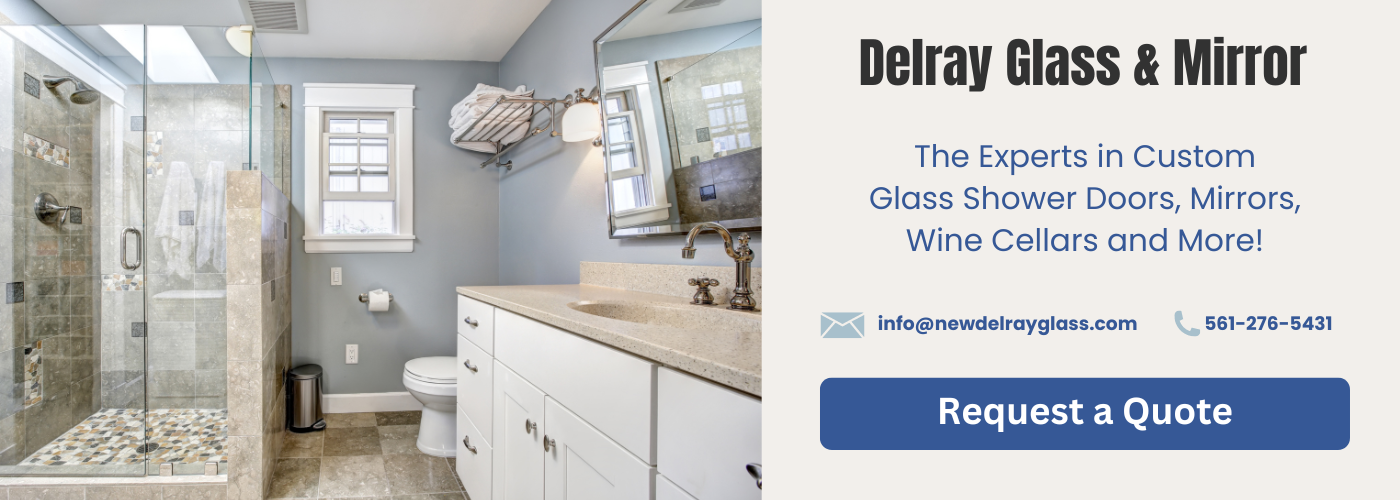
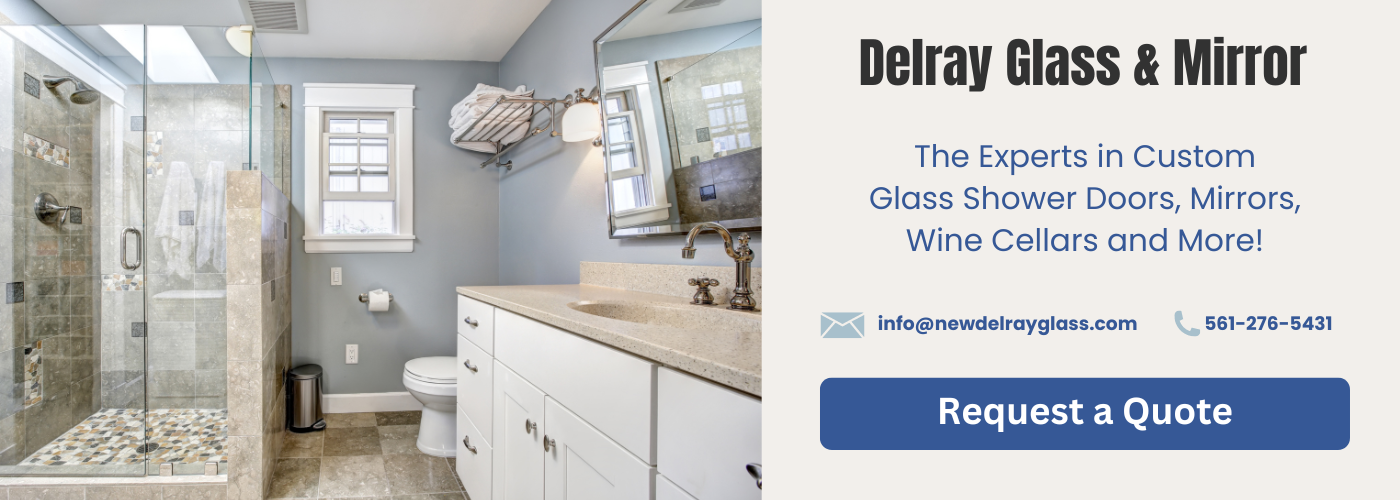
Packaging Materials Used for Frameless Shower Doors
When it comes to the packaging of frameless shower doors, suppliers take extra care to ensure that the product reaches its destination without any damage. The materials used for packaging play a crucial role in providing the necessary protection during the transit.
One of the most common materials used in the packaging of frameless shower doors is foam padding. This soft, yet sturdy material is used to cushion the glass panels and prevent any scratches or cracks. The foam padding is typically wrapped around each individual glass panel before it is placed into the box.
In addition to foam padding, corrugated cardboard is also used. This type of cardboard is known for its strength and durability, making it an excellent choice for protecting heavy items such as frameless shower doors. The cardboard box not only provides an additional layer of protection, but it also makes it easier to handle and transport the shower doors.
Plastic wrap is another essential packaging material. It is used to tightly secure the foam padding and glass panels together, preventing them from moving around inside the box during transportation.
Lastly, for added protection, the packaged shower doors may be placed on wooden pallets. The pallets provide a sturdy base and make it easier for handling and transportation using a forklift or a pallet jack.
So, the packaging materials used for frameless shower doors are specifically chosen to protect the product from potential damage during the delivery process. It’s all about ensuring that the shower doors arrive at their destination in the same condition they left the factory.
Safety Measures in Packaging Frameless Shower Doors
The safety measures in packaging frameless shower doors are crucial to ensure the integrity of the product during shipping and handling. These measures are meticulously designed to protect the frameless shower doors from any potential damage that may occur during transit.
The first step in the safety measures is to make sure that the shower doors are thoroughly cleaned and dried. Any residual water or moisture on the doors could potentially damage the packaging materials, and subsequently, the shower doors themselves. After ensuring the doors are clean and dry, they are carefully inspected for any pre-existing damages or defects. This ensures that only top-quality products reach the consumers.
The doors are then wrapped in a thick layer of cushioning material, often bubble wrap or foam, to absorb any shocks or impacts the package might experience during transportation. This cushioning layer is of utmost importance as it serves as the first line of defense against potential damages. The corners and edges, being the most vulnerable parts, are given extra padding for additional protection.
After the cushioning, the doors are placed in sturdy, corrugated boxes that are custom designed to snugly fit the doors. These boxes not only protect the doors from external impacts but also keep them immobile, thereby reducing the risk of damages due to movement within the box. The boxes are then sealed securely to ensure that they don’t accidentally open during transit.
In addition to these packaging safety measures, some companies also use tamper-evident seals or tapes. If the package is tampered with or mishandled, these seals or tapes provide visible evidence, thereby ensuring the accountability of the delivery personnel.
These stringent safety measures in packaging frameless shower doors ensure that the product reaches the customer in the best possible condition, maintaining the high standards of quality and customer satisfaction.
Delivery Process of Frameless Shower Doors
The delivery process of frameless shower doors is an intricate part of ensuring the safety of this delicate product. This process is designed to guarantee that the doors arrive at their destination in perfect condition, ready for installation.
The process begins with careful handling of the packaged shower door from the warehouse or factory to the delivery vehicle. Specialized equipment such as forklifts or hand trucks may be used for this purpose to minimize the risk of damage. The packaged doors are then loaded onto the delivery vehicle, often a truck that has been outfitted with protective padding and secure fastening systems to keep the doors stable during transportation.
Upon arrival at the delivery address, the shower doors are again carefully unloaded and brought into the building. If necessary, special equipment may be used to assist with this process, particularly if the doors need to be moved up stairs or through narrow hallways. In some cases, the delivery company may also offer installation services, which can ensure that the doors are properly installed without causing any damage.
Throughout the entire delivery process, the main focus is on maintaining the safety and integrity of the frameless shower doors. This involves not only physical handling practices, but also thorough documentation and communication between all parties involved. This way, any issues that may arise during delivery can be promptly addressed to prevent damage or delays.
In conclusion, the delivery process of frameless shower doors is a complex operation that requires careful planning and execution. However, with the right practices in place, it is possible to deliver these doors safely and efficiently, ensuring that they arrive in perfect condition for their eventual installation.
Handling and Transportation Guidelines for Frameless Shower Doors
The handling and transportation of frameless shower doors are crucial aspects of the delivery process. These doors are made from tempered glass, which, while stronger than regular glass, needs special care during transportation to prevent any damage.
The guidelines for handling and transportation usually start with the proper loading of the packaged shower door onto the delivery vehicle. The package should be positioned in a way that minimizes the risks of movement during transit. It is usually placed upright and secured with straps or braces to ensure stability. Moreover, the delivery vehicle should have a suspension system capable of absorbing shocks and bumps on the road, thus reducing the risk of damaging the product.
During the transportation, strict compliance with speed limits and road safety rules is expected from the delivery team. Sudden stops or accelerations can lead to the displacement or damage of the shower doors. Therefore, the transportation must be done cautiously to ensure the safe arrival of the product.
Once at the destination, the handling of the shower door package should be done with utmost care. It should be carefully unloaded and placed in a safe spot until installation. The unloading process often requires more than one person due to the weight and size of the product.
In conclusion, the handling and transportation guidelines for frameless shower doors are designed to ensure that the product reaches the customer in the best possible condition. These guidelines include safe loading and unloading processes, secure positioning during transit, cautious transportation, and careful unloading at the destination. Compliance with these guidelines ensures the safety and integrity of the product, providing customers with a high-quality, undamaged frameless shower door.
Damage Control and Replacement Policies for Delivered Frameless Shower Doors
The damage control and replacement policies for delivered frameless shower doors are an integral part of the overall packaging and delivery process. These policies ensure that the customer receives their product in the best condition and that any potential damages are effectively addressed.
Often, manufacturers and suppliers of frameless shower doors have stringent measures in place to minimize the chances of damage during transit. Despite these efforts, damages can still occur due to unforeseen circumstances. This is where damage control and replacement policies play a crucial role.
When a customer receives a damaged shower door, they are usually required to notify the supplier within a specified period. The supplier then verifies the damage and determines whether it occurred during transport. If it did, the supplier would typically replace the damaged item at no additional cost to the customer.
The replacement policy often includes conditions that the customer must meet, such as providing photographic evidence of the damage, retaining the original packaging, and not attempting to install or modify the damaged door.
In essence, these policies serve to protect the customer’s investment and maintain a high level of customer satisfaction. They also push manufacturers and suppliers to continually improve their packaging and delivery methods to minimize the chances of damage during transit.