Insulated glass units (IGUs), commonly known as double glazing or double-pane, have become a standard in modern construction due to their superior insulation properties. They are designed to offer high thermal and acoustic insulation by reducing heat transfer and external noise. The effectiveness of these units, however, largely depends on how well they are sealed. In this article, we delve into the intriguing subject of how insulated glass units are sealed.
Firstly, we will explore the components of insulated glass units. This will provide a comprehensive understanding of what these units are made of and how each part contributes to the overall functionality of the unit. The second part of our discussion will focus on the process of sealing insulated glass units. This section will take a detailed look at the steps involved in sealing these units and ensuring their optimal performance.
Next, we will delve into the types of sealing materials used in this process. This section will shed light on the various materials utilized to achieve a tight and durable seal, and their respective benefits and drawbacks. The fourth subtopic will examine the factors affecting the sealing process. This will cover various conditions and elements that can influence the efficiency of the sealing process.
Lastly, we will emphasize the importance of proper sealing in insulated glass units. This concluding part will underscore the crucial role that sealing plays in the overall performance and durability of these units, including their energy efficiency and longevity. Join us as we unravel the intricate process of sealing insulated glass units, a key aspect that plays a pivotal role in modern architecture and construction.
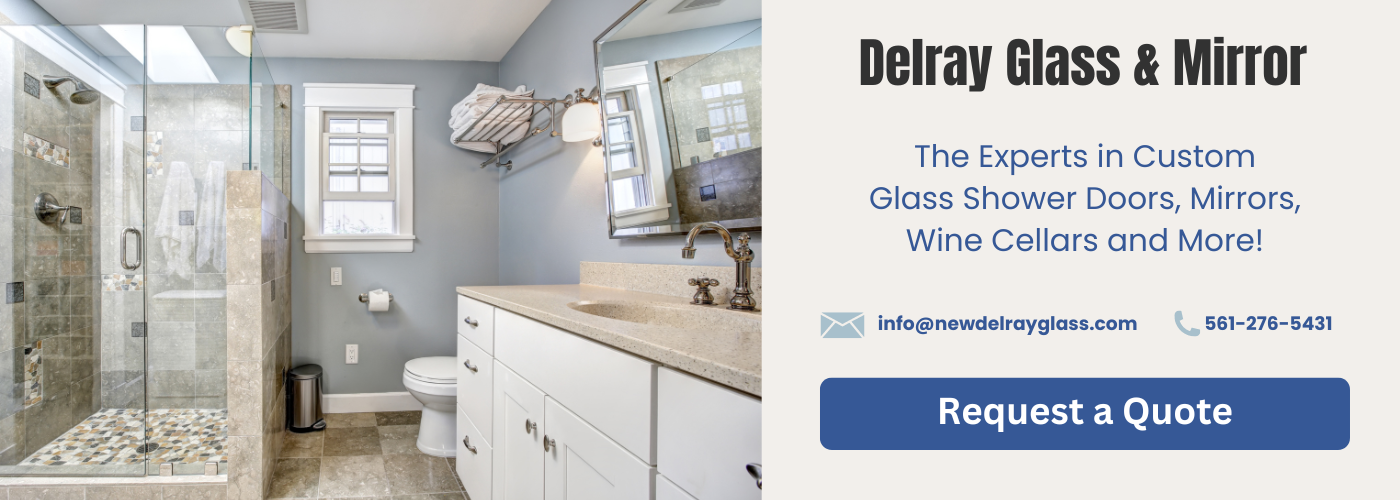
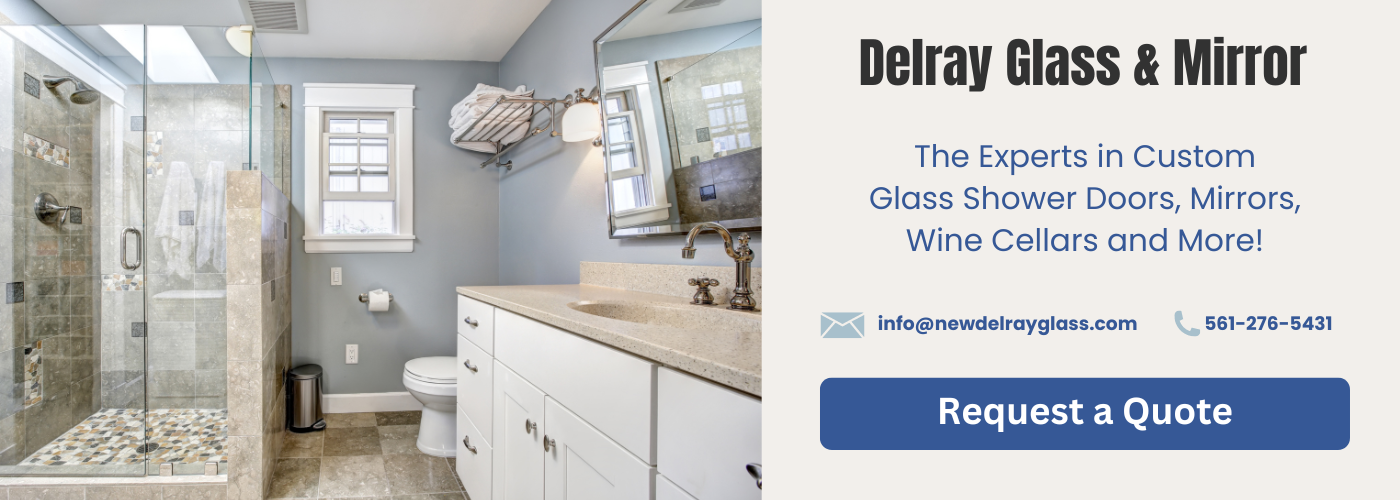
Components of Insulated Glass Units
The components of Insulated Glass Units (IGUs) are a fundamental aspect when it comes to understanding how they are sealed. An IGU is a combination of multiple glass panes into a single unit, with the aim of improving insulation and energy efficiency. The IGU essentially consists of two or more panes of glass, separated by a space which is filled with air or a specific type of gas. These panes are typically held apart by a spacer, which is a piece of material that goes around the edge of the glass panes, creating and maintaining the necessary space between them.
The spacer not only physically separates the panes of glass but also helps to seal the space between them, preventing the entry or exit of air or gas. The spacer usually contains a desiccant material which helps to absorb any moisture that may exist in the air or gas-filled space, thus preventing condensation from occurring within the IGU.
The outer edges of the IGU are then sealed with a special type of sealant, which helps to maintain the integrity of the unit, preventing any leakage of air or gas, and also providing a barrier against the entry of water, dust, and other potentially harmful elements. The type of sealant used can vary, depending on the specific requirements of the IGU, including factors such as the type of glass used, the type of gas filled into the space, and the overall design and construction of the IGU.
In conclusion, the components of an Insulated Glass Unit play a crucial role in its sealing process. From the glass panes, spacer, desiccant, to the sealant, each component has its unique function which collectively ensures the IGU is perfectly sealed for optimal insulation and energy efficiency.
Process of Sealing Insulated Glass Units
The process of sealing insulated glass units is an integral part of the manufacturing process and plays a crucial role in the performance and longevity of the units. It involves several stages to ensure a firm, air-tight seal that prevents heat transfer and condensation.
In the initial stages, the glass panes are thoroughly cleaned and dried to remove any dust or debris that could compromise the seal. Afterward, a spacer is applied around the edges of one of the panes. This spacer typically contains a desiccant material that will absorb any moisture within the unit, preventing fogging between the panes.
Next, the second pane of glass is placed over the first, aligning with the spacer to create an insulating chamber between them. This chamber can be filled with inert gas, such as argon or krypton, to further enhance the unit’s insulation properties.
The final step in the process is the application of the sealant. This is typically a specially formulated adhesive that is applied around the edges of the unit, bonding the two panes of glass and the spacer together. This creates a hermetic, or air-tight, seal that prevents the ingress of outdoor air and the egress of the insulating gas.
The process of sealing insulated glass units is both a science and an art, requiring precision, quality materials, and meticulous workmanship. When done correctly, it results in a high-performance product that significantly enhances the energy efficiency and comfort of a building.
Types of Sealing Materials Used
The sealing of insulated glass units is a critical process that plays a key role in their performance and durability. One of the most important aspects of this process is the type of sealing material used. There are several different types of sealing materials that are commonly used in the sealing of insulated glass units, each with its own unique properties and benefits.
One of the most commonly used sealing materials is silicone. Silicone sealants are known for their excellent adhesion properties and their ability to withstand extreme temperatures and weather conditions. They are also highly flexible, which makes them ideal for use in insulated glass units that may experience significant thermal expansion and contraction.
Another popular type of sealing material is polyurethane. Polyurethane sealants offer excellent adhesion and flexibility, and they are also highly resistant to UV radiation, which makes them a good choice for use in insulated glass units that will be exposed to direct sunlight.
In addition to silicone and polyurethane, there are also a number of other sealing materials that are sometimes used, including butyl, polysulfide, and hot melt butyl. Each of these materials has its own unique set of properties and benefits, and the choice of which one to use will depend on a variety of factors, including the specific requirements of the insulated glass unit and the conditions it will be exposed to.
Therefore, understanding the different types of sealing materials and their properties is a key aspect of the insulated glass unit manufacturing process.
Factors Affecting the Sealing Process
The sealing process of insulated glass units is influenced by several factors. These factors play a crucial role in ensuring the effectiveness and durability of the seal, thereby enhancing the performance of the insulated glass units.
One of the primary factors is the quality of the sealing materials used. The selection of high-quality materials is critical to ensure the seal is robust and can withstand varying environmental conditions. Poor quality materials may lead to seal failure, resulting in compromised insulation and increased energy loss.
The environment in which the sealing process is conducted also has a significant impact. The presence of dust and moisture can affect the seal’s adhesion to the glass surface, leading to potential leakage and reduced insulating properties. Therefore, it is essential to maintain a clean and controlled environment during the sealing process.
Temperature and humidity control during the sealing process is another essential factor. Extreme temperatures and high humidity levels can affect the adhesive properties of the sealing material, leading to an ineffective seal. Therefore, maintaining an optimal temperature and humidity level during the process is crucial.
Lastly, the skill and expertise of the technician performing the sealing process also influence the quality of the seal. A well-trained technician will ensure the proper application of the sealing material, thus ensuring a high-quality and durable seal. Therefore, it is essential to have skilled and experienced technicians for the sealing process of insulated glass units.
Importance of Proper Sealing in Insulated Glass Units
The importance of proper sealing in insulated glass units cannot be overstated. The sealing process is a critical step in the manufacturing of insulated glass units as it ensures the overall effectiveness and longevity of the unit. Sealing is what keeps the insulating gas, usually either argon or krypton, trapped between the panes of glass. This gas is what provides the insulation in insulated glass units, reducing heat transfer and thus increasing the energy efficiency of the unit.
Without a proper seal, the gas would escape and the insulating properties of the unit would be greatly diminished. This could result in increased energy costs due to heat loss in the winter and heat gain in the summer. Furthermore, an improper seal could also allow moisture to enter the unit, which could then condense on the inside of the glass. This condensation could obstruct the view through the glass and could potentially damage the window frame.
Therefore, it is essential that the sealing process is carried out correctly. This involves using the right type of sealing material and ensuring that it is applied evenly and securely. The sealing material must also be able to withstand the various stresses placed on it, such as changes in temperature and pressure, without degrading or failing. This makes the selection of the sealing material, and the process of applying it, crucial aspects of the production of insulated glass units.
In conclusion, proper sealing plays a pivotal role in the performance and durability of insulated glass units. It guarantees the integrity of the unit, making sure that the insulating gas stays in place and that the unit remains free from moisture. Therefore, understanding the importance of proper sealing is fundamental to ensuring the quality and effectiveness of insulated glass units.