Mirrors are a ubiquitous part of our everyday lives, reflecting our world in ways both mundane and profound. However, not all mirrors are created equal, and differences in their construction can have significant implications for their weight and use. One particular type of mirror that has gained interest in recent years is the floating mirror, which boasts a unique manufacturing process and composition that sets it apart from traditional, or conventional, mirrors. This article aims to delve into the comparison of floating mirrors and conventional mirrors, particularly focusing on their weight differences.
Among the topics to be explored include the composition and structure of both floating and conventional mirrors. This will provide an understanding of the material composition of each mirror type, as well as its structural design, which plays a pivotal role in determining weight.
Next, the article will examine the manufacturing processes of both floating and conventional mirrors. The manufacturing process not only impacts the mirror’s final form but can also significantly affect its weight, making this a critical factor in our comparison.
The core of the article will deal with the weight comparison between floating and conventional mirrors. Here we will delve into the specifics of how each mirror type measures up against the other in terms of weight, shedding light on the practical implications of their differences.
Finally, we will discuss the factors influencing the weight of mirrors. This will help readers understand why mirrors have the weight they do, and what can be done during the manufacturing process to manipulate this. By addressing these topics, this article will provide a comprehensive overview of how floating mirrors compare in weight to conventional mirrors.
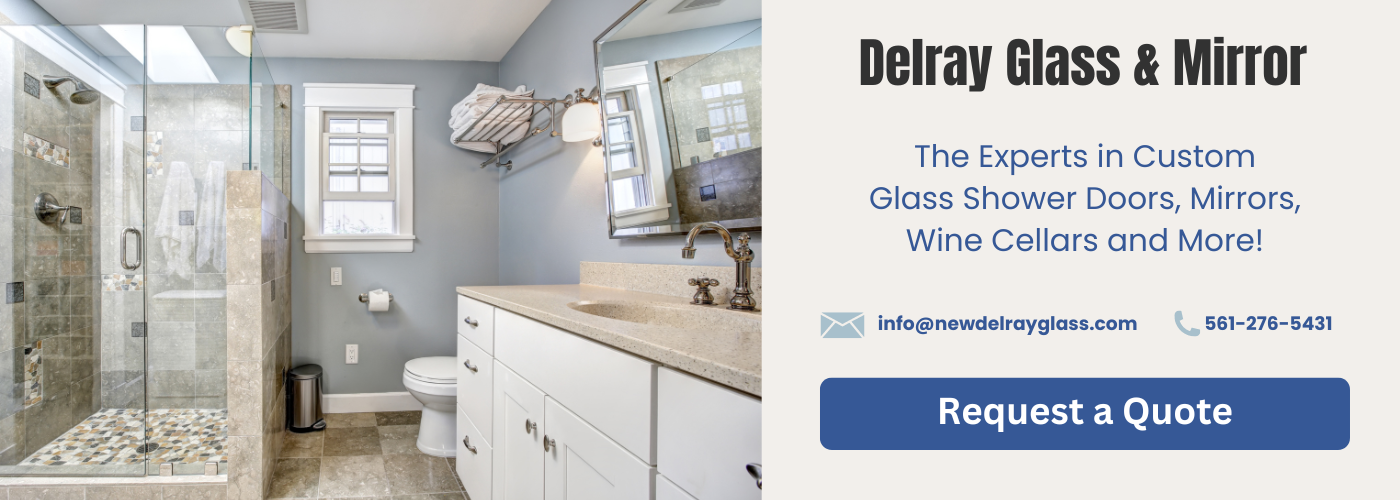
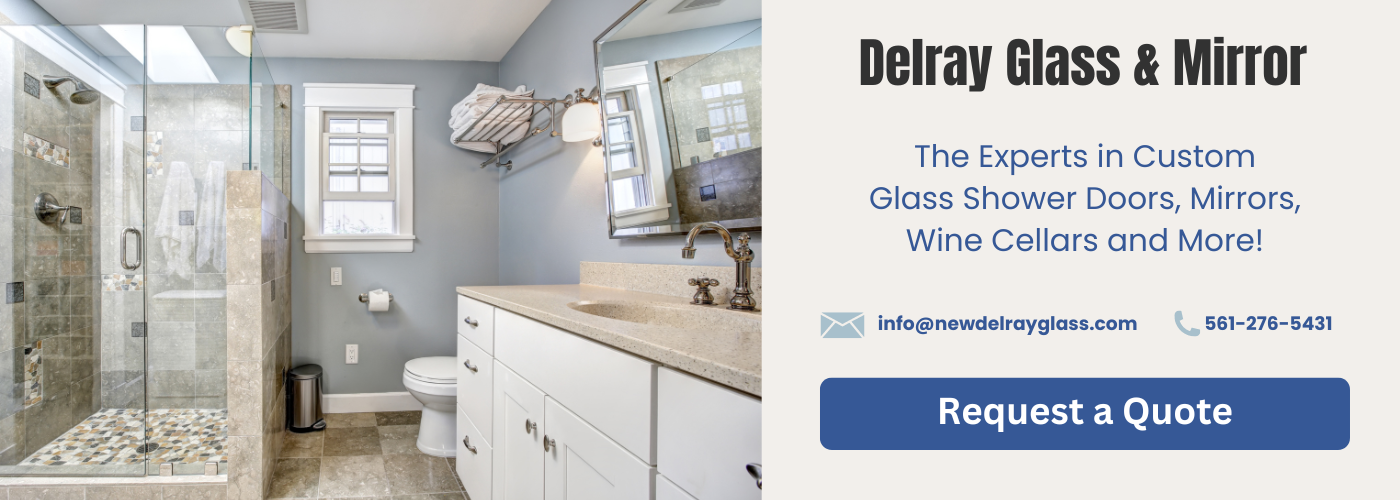
Composition and Structure of Floating Mirrors
The composition and structure of floating mirrors play a crucial role in distinguishing them from conventional mirrors. Floating mirrors are an innovative product of technology, designed to deliver high precision and efficiency. They are named so because of the method employed in their production process which allows a thin layer of molten metal to ‘float’ on top of a molten tin bath. This method ensures a highly reflective and flat mirror surface.
The structure of floating mirrors incorporates a layer of glass to which a reflective coating is applied. The reflective coating is often made from aluminum or silver. The layer of glass provides structural support to the mirror and contributes to its overall weight. Meanwhile, the reflective coating is responsible for the mirror’s primary function, which is to reflect light.
The composition of the floating mirror directly influences its weight. Due to the use of innovative manufacturing techniques, floating mirrors are generally lighter than conventional mirrors. This is primarily because of the even and controlled distribution of the reflective coating on the glass layer, which eliminates the need for a heavy backing that is typically seen in conventional mirrors. This not only makes floating mirrors lighter but also offers an advantage in terms of installation and handling.
In conclusion, the composition and structure of floating mirrors are unique, innovative, and have a direct impact on their weight comparison with conventional mirrors. Their lightweight nature, coupled with their high reflectivity, makes them a preferred choice in many applications.
Composition and Structure of Conventional Mirrors
The composition and structure of conventional mirrors play a significant role in their properties and functionalities. Conventional mirrors are typically composed of three primary components: glass, a reflective coating, and a protective coating. The glass layer, often made from high-quality, transparent float glass, serves as the substrate. This glass is usually flat and smooth to ensure optimal reflection.
The reflective coating is the most critical layer of a conventional mirror. It is typically made from metals like silver, aluminum, or chrome. These metals are chosen for their excellent reflective properties. The metal layer is applied to the glass in a very thin, even coating, which reflects light and produces the mirror effect.
The third layer, the protective coating, is applied over the reflective layer. It protects the metal coating from damage and corrosion, ensuring the longevity of the mirror. The protective layer is often composed of a paint or resin.
In terms of structure, conventional mirrors are solid and rigid. They are often quite heavy and require secure mounting due to their weight. This is a stark contrast to floating mirrors, which, as their name suggests, appear to float and are lighter in weight. The weight difference between conventional and floating mirrors is a subject of much interest and study, with many factors influencing the final weight of each mirror type.
Manufacturing Process of Floating Mirrors vs Conventional Mirrors
The manufacturing process of floating mirrors and conventional mirrors significantly differs, leading to the unique characteristics of each. The manufacturing process is a crucial factor that impacts the final weight, performance, and quality of these mirrors, which is why it’s a vital subtopic when discussing how floating mirrors compare in weight to conventional mirrors.
The manufacturing process of floating mirrors involves using molten glass. The molten glass is poured onto a bath of molten tin, where it floats and spreads out, creating a smooth and uniform surface. The floating process allows the control of the thickness and flatness of the mirror, which can be manipulated to make it lighter or heavier as needed. The molten glass is then cooled gradually to prevent any stress or warping, giving the mirror its strength and durability.
On the other hand, conventional mirrors are typically manufactured by coating a glass substrate with a reflective material, usually silver or aluminum. The glass substrate is first polished to achieve the desired smoothness and clarity, then the reflective material is applied in a vacuum chamber. The thickness of the glass and the reflective coating determine the weight of the conventional mirror.
In summary, the manufacturing process of both mirrors significantly impacts their final weight. However, it is the floating mirror’s ability to control thickness during its manufacturing process that may give it an edge in the weight comparison against conventional mirrors. Understanding these processes can provide valuable insights into the weight properties and potential applications of both floating and conventional mirrors.
Weight Comparison between Floating and Conventional Mirrors
The weight of a mirror is a critical factor that influences its application and installation. It is concluded from various studies and practical applications that floating mirrors tend to be lighter than conventional mirrors. The key reason behind this is the difference in their manufacturing process and composition.
Floating mirrors are designed using a unique manufacturing process that involves floating molten glass on a bath of molten tin. This process results in a thin and uniform glass sheet that is lighter than the glass produced in conventional methods. Moreover, the thinness of the glass does not compromise its strength and durability, making floating mirrors a preferred choice for many applications.
On the other hand, conventional mirrors are typically made from thicker glass. This thickness adds to their weight, making them heavier than their floating counterparts. Additionally, the manufacturing process of conventional mirrors does not necessarily result in a uniform thickness, which can further increase their weight.
However, it is essential to note that the weight of a mirror also depends on other factors like size, shape, and additional features like frames or decorative elements. Therefore, while floating mirrors are generally lighter, the actual weight can vary significantly based on these factors.
Factors Influencing the Weight of Mirrors
The weight of mirrors, both floating and conventional, is determined by several key factors.
One of the most significant factors is the material composition of the mirror. Mirrors are made up of a reflective material, usually glass, and a reflective coating, typically silver or aluminum. The thickness and density of these materials directly impact the mirror’s weight. For instance, a mirror made from denser glass or with a thicker coating would be heavier than one made from less dense glass or with a thinner coating.
Another crucial factor is the size of the mirror. Naturally, the larger the mirror, the more material is required to create it, and thus the heavier it becomes. This is why large wall mirrors or full-length mirrors tend to be quite heavy, even if they are made from relatively lightweight materials.
The manufacturing process can also affect the weight of the mirror. For example, floating mirrors are made using a process known as float glass production. This process results in a very flat and uniform thickness of glass, which can help reduce the weight of the mirror compared to other manufacturing methods that may result in thicker, heavier glass.
Furthermore, any additional features or embellishments on the mirror can also add to its weight. For example, mirrors with decorative frames or those that incorporate other materials like metal or wood would be heavier than simple, frameless mirrors.
In summary, while there may be some differences in weight between floating mirrors and conventional mirrors due to the differences in their manufacturing processes and material composition, the weight of any given mirror is ultimately influenced by a wide range of factors, including its size, thickness, and any additional features or embellishments.