When it comes to choosing mirrors for interior design, functionality, or precision applications, the debate often arises between opting for custom mirrors or settling for regular, off-the-shelf mirrors. The key to making an informed decision lies in understanding how the reflection quality of these two mirror types compares. This comparison is influenced by several critical factors, including the types of materials used, the coatings and reflective materials applied, the manufacturing processes and quality control standards adhered to, their durability and longevity, and the customization options available along with their applications. This article delves into each of these aspects to shed light on how custom mirrors stack up against their regular counterparts in terms of reflection quality, thereby helping consumers, designers, and technicians make choices that best fit their specific needs and expectations. Each subtopic will explore the nuances that contribute to the overall performance and aesthetic appeal of mirrors, ultimately guiding the reader through a detailed comparison.
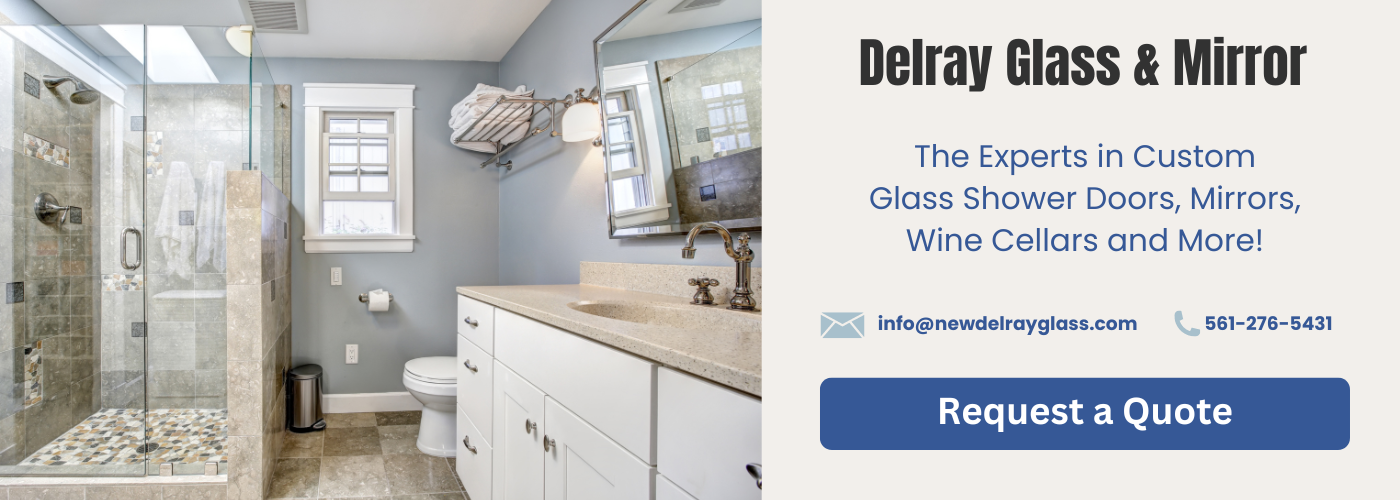
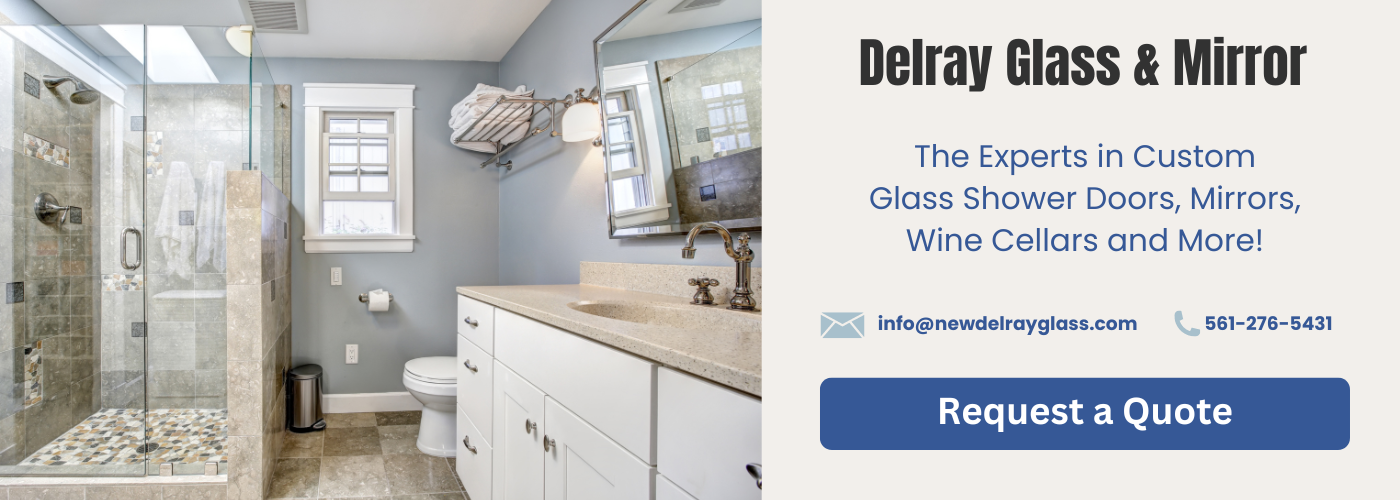
Types of Materials Used
The quality of reflection in mirrors, whether custom or regular, largely depends on the types of materials used in their construction. For mirrors, the most critically influential material is the substrate—the base layer upon which the reflective coating is applied. Common substrates include glass and acrylic, each offering distinct characteristics that impact the mirror’s overall performance and application.
Glass, used in both custom and regular mirrors, is favored for its excellent clarity and durability. It provides a high-quality reflection with minimal distortion, which is crucial for applications requiring precise, true-to-life images such as in bathrooms, vehicles, and optical instruments. However, glass is heavier and more fragile, which can limit its use in certain scenarios.
Acrylic mirrors, on the other hand, are lighter and shatter-resistant, making them ideal for use in environments where safety and weight are concerns, such as in children’s play areas, portable mirrors, or in certain automotive applications. While acrylic mirrors are less prone to breaking, they can scratch more easily and may offer slightly less clarity compared to glass mirrors, which can affect the reflection quality.
In custom mirror manufacturing, the choice of materials extends even further, allowing for the use of specialized substrates and coatings tailored to specific needs. For example, a customer might opt for a reinforced glass mirror with a high-quality silver or aluminum coating for enhanced reflectivity and corrosion resistance in harsh environments. Alternatively, a custom mirror might use a unique combination of materials to achieve specific aesthetic goals, such as tinted glass or mirrors with integrated lighting.
Thus, the reflection quality of custom mirrors can be comparable or even superior to regular mirrors, depending on the materials used and the specific requirements of the application. Customization allows for the optimization of both functionality and aesthetics, ensuring that the mirror not only meets but exceeds the performance of standard off-the-shelf products in many cases.
Coating and Reflective Materials
In the context of comparing custom mirrors to regular mirrors, the choice of coating and reflective materials plays a critical role in determining the reflection quality of the mirrors. Regular mirrors typically use a standard silver or aluminum coating. Silver coatings are known for providing a very clear and precise reflection, which is why they are often used in mirrors that require high reflectivity, such as in bathrooms and vanity products. Aluminum, while slightly less reflective than silver, is often used due to its lower cost and higher durability.
Custom mirrors, on the other hand, may use these standard materials but often offer more options for customization. For instance, they can include layers of specialized coatings to enhance durability or to achieve specific reflective qualities. These coatings can also be tailored to reduce glare, improve scratch resistance, or alter the color of the reflection. Additionally, custom mirrors might use high-tech materials such as gold for infrared reflectivity or copper for different aesthetic effects.
The quality of reflection in custom mirrors can surpass that of regular mirrors if the coatings are applied with advanced technologies that minimize defects like pinholes and scratches. Techniques such as sputtering and thermal evaporation allow for a more uniform distribution of the coating material, which can result in a mirror with superior optical qualities. Moreover, the ability to add multiple layers of different materials can help in achieving desired outcomes such as enhanced brightness, contrast, or even energy-saving capabilities by reflecting heat.
Overall, whether the reflection quality of custom mirrors compares favorably to regular mirrors largely depends on the materials and technologies used in the coating process. With the right choice of materials and application techniques, custom mirrors can be engineered to meet specific needs that regular mirrors might not be able to satisfy, making them a better option in certain applications.
Manufacturing Process and Quality Control
The manufacturing process and quality control are crucial elements that determine the reflection quality of custom mirrors compared to regular mirrors. Custom mirrors often undergo a specialized manufacturing process tailored to meet specific requirements of clients. This can include the use of particular materials, shapes, and sizes, which are not typically found in mass-produced regular mirrors. The ability to customize these aspects allows for enhanced control over the reflective properties of the mirror.
Quality control is another vital factor that impacts the overall quality of custom mirrors. In custom mirror production, quality control can be more stringent and personalized. Each mirror is often inspected individually to ensure it meets the desired specifications and quality standards. This contrasts with regular mirrors, where quality control might focus more on batch testing due to the high volume of production.
Moreover, the manufacturing process of custom mirrors can incorporate advanced technologies to improve the reflective quality. For example, the application of high-precision coatings that enhance reflectivity and protect against corrosion can be more meticulously applied in custom mirror production. This ensures that the mirror not only reflects accurately but also maintains its quality over time.
In summary, the manufacturing process and quality control are pivotal in determining the superiority of custom mirrors over regular mirrors. The personalized attention to detail and the use of advanced technologies in custom mirror manufacturing allow for a product that not only meets specific client needs but also provides superior reflective properties.
Durability and Longevity
Durability and longevity are important aspects to consider when comparing the reflection quality of custom mirrors to regular mirrors. Custom mirrors are often designed to meet specific needs and can incorporate materials and construction methods tailored to enhance their longevity and durability. This customization can be particularly advantageous in environments where the mirror will be subjected to harsh conditions or needs to perform a specific function over an extended period.
Regular mirrors typically use standard materials and manufacturing processes aimed at mass production, which might not prioritize longevity as highly as custom solutions do. For example, a custom mirror might use a thicker glass or a more robust reflective coating to withstand frequent cleaning, exposure to moisture, or outdoor conditions. The adhesives and backing materials can also be chosen based on the intended environment, reducing the likelihood of degradation over time.
Furthermore, the quality of the reflective coating is crucial in both custom and regular mirrors. However, custom mirrors might offer options for coatings that are more resistant to scratching and tarnishing, thereby maintaining a high-quality reflection for a longer time. Advanced coatings might also include UV-resistant properties or anti-fogging technologies, which contribute directly to the longevity of the mirror’s surface.
In summary, while both custom and regular mirrors can serve their intended purpose well, custom mirrors provide an opportunity to enhance durability and longevity through tailored materials and construction techniques. This makes them a preferable choice in situations where mirrors need to maintain their performance and aesthetics over long periods despite challenging conditions.
Customization Options and Applications
Custom mirrors offer a wide array of customization options and applications that set them apart from regular mirrors. This flexibility is particularly valuable in both residential and commercial settings where specific aesthetics or functional features are needed. Custom mirrors can be tailored to fit specific dimensions, shapes, and styles that may not be available with standard mirrors. This allows interior designers, architects, and homeowners to create unique spaces that perfectly fit their design requirements.
In terms of applications, custom mirrors are not limited to traditional uses such as in bathrooms or as vanity mirrors. They can be incorporated into furniture, used as statement pieces in living rooms, or installed as part of artistic installations. For businesses, custom mirrors can be crafted to enhance branding, with logos or specific designs etched into the mirror’s surface. This level of customization can significantly enhance the interior décor and create a unique ambiance that cannot be achieved with off-the-shelf mirrors.
Furthermore, the technological advancements in the mirror manufacturing process allow for additional features such as improved safety, anti-fog properties, and enhanced lighting. These features make custom mirrors not only aesthetically pleasing but also more functional and suited to specific environmental conditions or client needs. The ability to integrate these advanced features further distinguishes custom mirrors from regular mirrors, offering enhanced performance and versatility.