Safety glass is an essential component in a variety of industries, from automotive to construction, due to its unique property of enhanced impact resistance. The question of exactly how impact-resistant safety glass is, however, remains intriguing to many individuals. This article aims to delve into this question by exploring various aspects of safety glass and its impact resistance.
Our first subtopic will provide a comprehensive understanding of what safety glass is and the different types available in the market. This knowledge lays the foundation for the next discussion about the manufacturing process of safety glass. By understanding how safety glass is made, readers will gain a deeper insight into why this type of glass exhibits superior impact resistance compared to regular glass.
The third subtopic will focus on the impact resistance testing of safety glass. This is a crucial process in the industry as it provides empirical evidence of the glass’s ability to withstand impacts of varying magnitudes. Following this, we will explore the different factors that can affect the impact resistance of safety glass. Various conditions and elements can potentially alter the performance of safety glass, and these will be discussed extensively.
Lastly, we present a comparative analysis of the impact resistance between safety glass and regular glass. This final subtopic will provide a clear and concise understanding of why safety glass is often the preferred choice in applications where impact resistance is a key consideration. Through this article, we aim to provide readers with a comprehensive understanding of the impact resistance of safety glass.
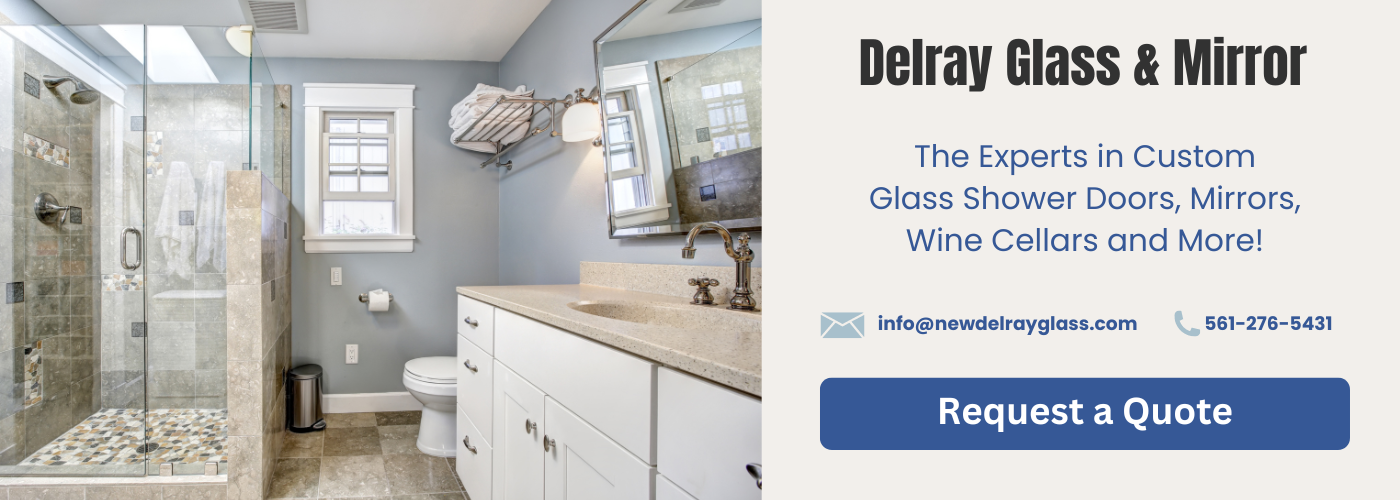
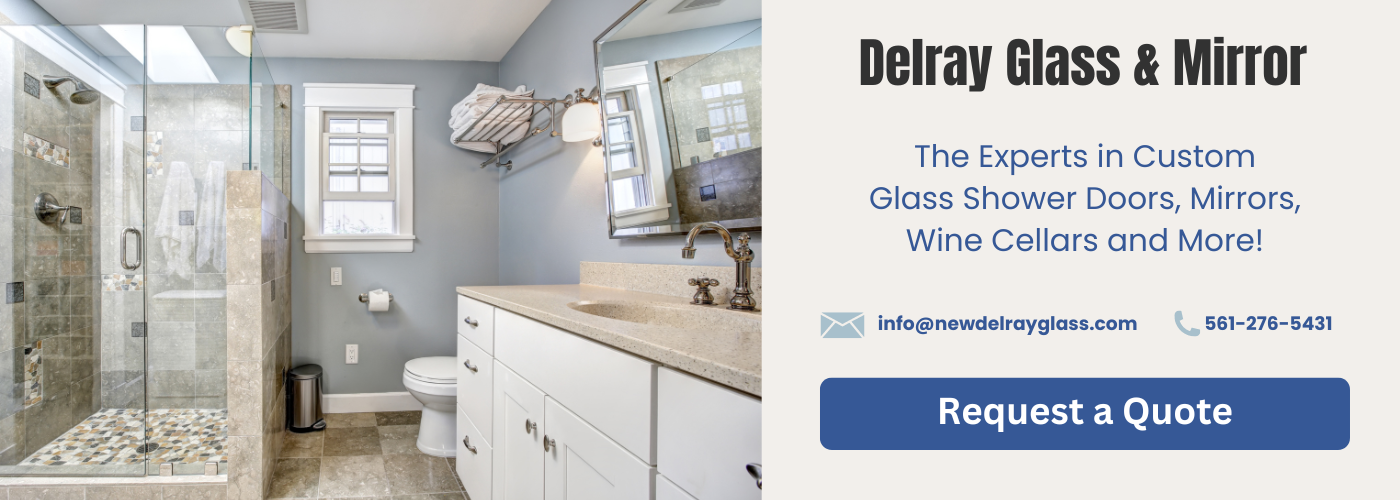
Definition and Types of Safety Glass
Safety glass, as indicated by its name, is a type of glass specifically designed to be safer and less likely to break, or if it does break, it would crumble into small granular chunks instead of splintering into jagged shards as plate glass would. This characteristic is achieved through various manufacturing processes and materials used. The purpose is to minimize the potential for injury if the glass is broken, making safety glass an optimal choice for use in environments where human safety is a concern.
There are primarily two types of safety glass – tempered and laminated. Tempered safety glass, also known as toughened glass, is processed by controlled thermal or chemical treatments to increase its strength. It is several times stronger than normal glass and when broken, it shatters into small pebble-like pieces.
On the other hand, laminated safety glass is made by sandwiching a layer of plastic, usually polyvinyl butyral (PVB), between two or more layers of glass. The interlayer keeps the layers of glass bonded even when broken, and its high strength prevents the glass from breaking up into large sharp pieces. This results in a characteristic “spider web” cracking pattern upon impact.
The impact resistance of safety glass is determined by factors such as the type of safety glass, the manufacturing process, and the thickness of the glass. Both tempered and laminated safety glass are designed to withstand high levels of impact, providing safety in various applications including automobile windows, shower doors, architectural glass doors and panels, and even in bulletproof glass.
Manufacturing Process of Safety Glass
The manufacturing process of safety glass is a crucial aspect that contributes to its impact resistance. This process involves two primary techniques: tempering and lamination.
Tempering is a heat treatment technique where the glass is heated to its softening point and then rapidly cooled. This process sets up compressive stresses on the surface of the glass, which makes it stronger and more resistant to impact compared to regular glass.
In the lamination process, two or more layers of glass are bonded together with a plastic interlayer, usually polyvinyl butyral (PVB). This plastic layer holds the glass together in case of breakage, preventing it from shattering into large, sharp pieces.
These manufacturing processes greatly enhance the safety glass’s ability to withstand impacts. They also play an essential role in determining the level of impact resistance in different types of safety glass. For instance, tempered safety glass is usually more impact-resistant than laminated safety glass. However, laminated safety glass offers greater safety because, in the event of breakage, the glass shards remain attached to the plastic layer, reducing the risk of injury.
Therefore, understanding the manufacturing process of safety glass is important not only for manufacturers but also for users to make informed decisions about the type of safety glass that best suits their needs.
Impact Resistance Testing of Safety Glass
The impact resistance testing of safety glass is an integral aspect of evaluating its overall durability and safety. This process is designed to measure the ability of the glass to withstand impacts and resist shattering. The testing is conducted in a controlled environment using specific tools and techniques to ensure accuracy and consistency.
The tests typically involve dropping a heavy object from a certain height onto the glass, subjecting it to a specific amount of force. The results of the test are then used to determine the impact resistance level of the glass. The higher the impact resistance, the less likely the glass is to break upon impact.
Impact resistance testing is crucial in the production of safety glass as it ensures that the glass meets the necessary safety standards. This is especially important in various industries where safety glass is used, such as automotive, construction, and aerospace. The testing provides valuable information about the performance of safety glass under different impact conditions and can help manufacturers improve their products and ensure their safety.
The process of impact resistance testing also includes repeated testing to verify the consistency and reliability of the results. This helps to ensure that the safety glass produced is of high quality and can withstand the rigors of its intended use.
In conclusion, impact resistance testing of safety glass is a critical process that contributes significantly to its safety and durability. Through this testing, manufacturers can ensure that their safety glass products are reliable, durable, and most importantly, safe for use.
Factors Affecting Impact Resistance of Safety Glass
When discussing the impact resistance of safety glass, it’s necessary to take into account the varying factors that can affect this property. These factors can include the manufacturing process, the materials used, and the specific design of the safety glass itself.
The manufacturing process is a crucial factor that affects the impact resistance of safety glass. Different techniques, such as tempering or laminating, can enhance the strength of the glass and its ability to withstand force. For instance, tempered glass is created by heating it to a high temperature and then rapidly cooling it. This process increases the strength of the glass by creating tension in its inner layers and compression in its outer layers. Laminated glass, on the other hand, consists of two or more layers of glass bonded together with an interlayer. This design helps the glass to absorb impact energy and prevent shattering.
The materials used in the production of safety glass also play a significant role. For instance, the type of interlayer used in laminated glass can affect its impact resistance. Some materials can absorb more impact energy than others, and thus can provide better protection.
The design of the safety glass is another factor. The thickness of the glass, the number of layers, and the type of edge finish can all influence the glass’s impact resistance. Thicker glass and more layers generally provide better impact resistance, but they also make the glass heavier and potentially less transparent.
Moreover, the way the glass is installed can also affect its impact resistance. If the glass is not properly installed, it may not perform as effectively in absorbing impact energy.
In conclusion, several factors can affect the impact resistance of safety glass, and they all need to be considered when selecting and installing safety glass for a specific application.
Comparison of Impact Resistance Between Safety Glass and Regular Glass
The Comparison of Impact Resistance Between Safety Glass and Regular Glass is a crucial subtopic when discussing the impact resistance of safety glass. Safety glass, as its name implies, is designed with safety in mind. It is manufactured to withstand more impact than regular glass, and, even when it does break, it’s designed to do so in a way that reduces the likelihood of injury.
Regular glass, or annealed glass, breaks into large, jagged shards that can cause significant harm. On the other hand, safety glass, which includes types like tempered and laminated glass, is designed to either resist breakage or to break into small, less harmful pieces. Tempered glass, for instance, is heated and then cooled rapidly in the manufacturing process, a treatment that makes it four to five times stronger than regular glass.
Laminated safety glass, another type, is essentially a glass sandwich: it features a plastic layer between two layers of glass. When it breaks, the broken pieces adhere to the plastic, reducing the risk of injury from scattered glass shards.
The difference in impact resistance between safety glass and regular glass is therefore significant. Safety glass is clearly superior when it comes to withstanding force and minimizing potential harm upon breakage. This makes it the preferred choice for applications where human safety is a concern, such as in vehicles, buildings, and certain types of furniture.