Insulated glass, sometimes referred to as double glazing, is a vital component in a variety of architectural and design contexts due to its superior thermal efficiency, noise reduction capabilities, and security benefits. Yet, how many people actually understand the complexity of the manufacturing process behind this innovative product? This article aims to shed light on the intricacies of how insulated glass is produced, from the materials used to the end product’s applications.
The first section will delve into the materials used in manufacturing insulated glass. This will provide a comprehensive look at the key components that go into creating these unique glass systems, from the type of glass used to the gases that fill the spaces between the panes. Following this, we will explore the process of manufacturing insulated glass, detailing each step from start to finish, and giving readers a clear picture of how a seemingly simple product requires a highly sophisticated production process.
Quality control and testing procedures in insulated glass production is another crucial aspect that ensures the end product meets the highest standards. We will discuss various testing methods used to confirm the durability, safety, and performance of the glass. In the fourth section, we will explore the different applications and uses of insulated glass, showcasing its versatility and importance in today’s construction and design industries.
Finally, no discussion of insulated glass would be complete without examining the latest innovations and technological advancements in its manufacturing. From new machinery to improved production techniques, this section will highlight how technology continues to shape and enhance the world of insulated glass manufacturing. By the end of this article, you will have a deep understanding of what goes into creating this essential material that plays such a significant role in our everyday lives.
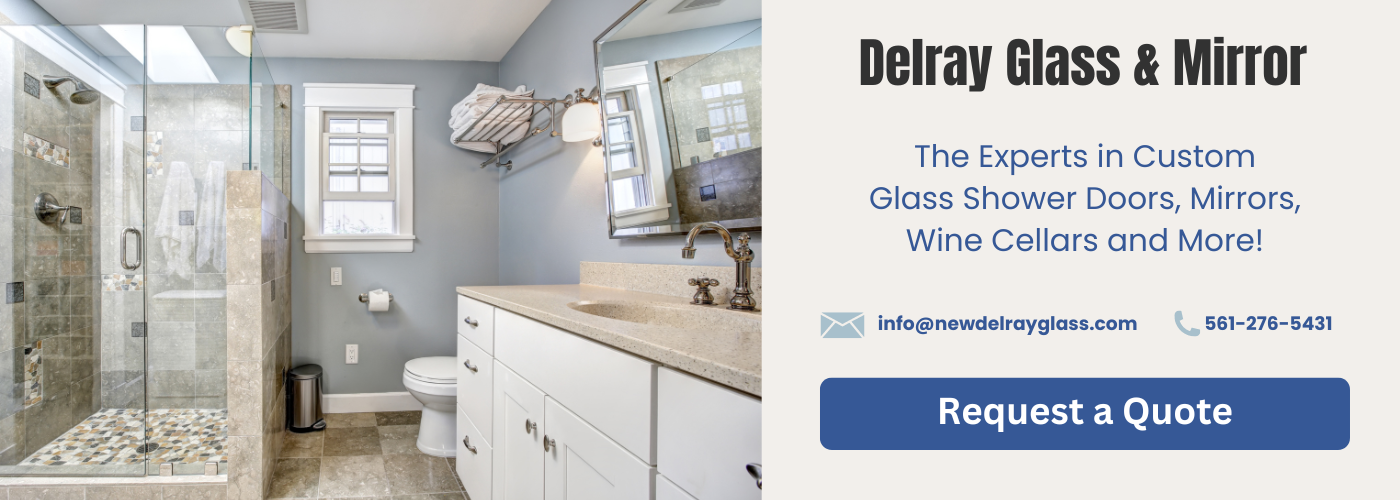
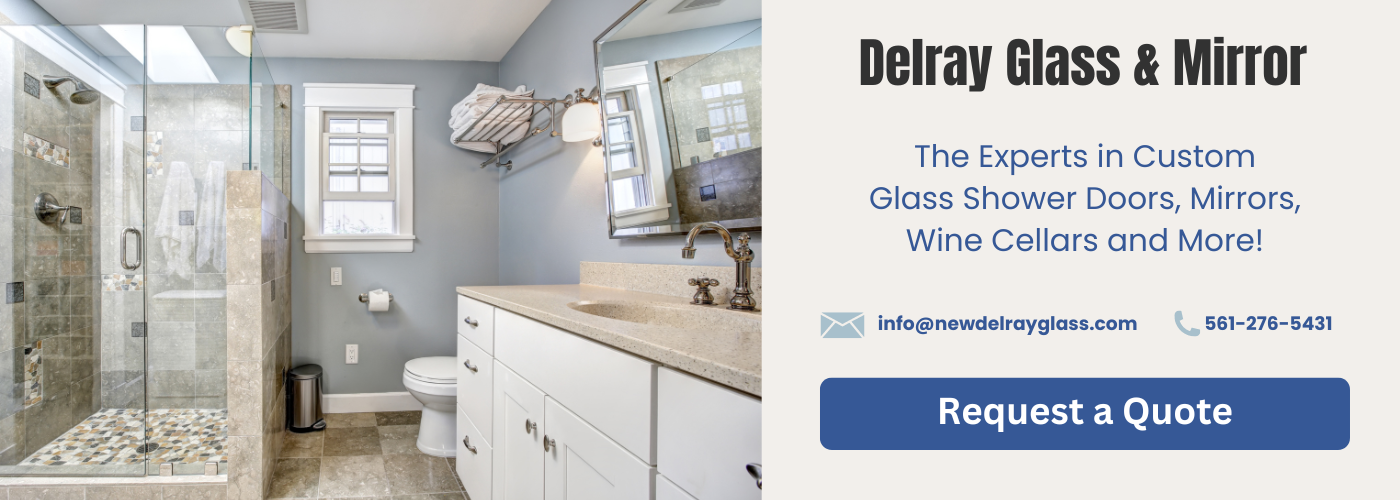
Materials Used in Manufacturing Insulated Glass
In the manufacturing of insulated glass, several materials are integral to the process, each serving a unique purpose. These materials typically include two or more panes of glass, spacers, and the desiccant.
The glass panes are the most visible component of insulated glass. They can be of different thicknesses and types depending on the requirements of the building project. They can be clear, tinted, or coated to achieve the desired aesthetics and thermal performance.
Spacers are used to maintain a uniform distance between the glass panes, creating an air space. These spacers can be made from aluminum, stainless steel, or other materials that offer excellent thermal performance. They are often filled with a desiccant, a hygroscopic material, to absorb moisture within the air space, thus preventing the formation of condensation and frost.
In addition to these, gas fillings like argon or krypton are used in the air space to improve the thermal performance of the insulated glass. These gases are denser than air, thereby reducing the heat transfer through the glass.
The selection and combination of these materials play a vital role in the performance and lifespan of insulated glass. The quality of these materials and their proper assembly ensure the overall efficiency of the insulated glass unit, thereby contributing to energy conservation and comfort in the building where they are installed.
The Process of Manufacturing Insulated Glass
The manufacturing process of insulated glass is a detailed and meticulous process that ensures the final product is efficient in energy consumption and provides optimal insulation. This process involves multiple steps, each contributing significantly to the final product’s performance.
The first step in the manufacturing process is cutting the glass to the required size. This is typically performed by automated machines for precision and consistency. After the glass is cut, it is cleaned thoroughly to remove any dust, dirt, or other contaminants that could affect the seal or the insulating gas.
The next step is the assembly of the insulated glass unit (IGU). This involves placing spacers between the glass panes. These spacers do not only keep the panes apart but also create a sealed space that will later be filled with insulating gas. The spacers are usually filled with desiccant material to absorb any moisture in the air space.
Once the glass panes and spacers are assembled, the edges are sealed to create airtight insulation. This is typically done using a primary seal of butyl and a secondary seal of silicone or polysulfide. After the unit is sealed, it is filled with insulating gas, typically argon or krypton, through a hole in the spacer. Following this, the hole is sealed to keep the gas inside.
The final step in the process is the quality control, where each IGU is checked for defects such as leaks or failure in the seal. This ensures that all manufactured insulated glass units are of the highest quality and will perform at their best.
In conclusion, the process of manufacturing insulated glass is a complex one that involves precision and attention to detail. However, each step is crucial in ensuring the final product’s efficiency and performance.
Quality Control and Testing Procedures in Insulated Glass Production
Quality control and testing procedures in insulated glass production are essential for ensuring the performance and durability of the final product. These processes are integral to the manufacturing process, safeguarding the integrity of the insulated glass and its ability to perform its intended functions effectively.
Quality control begins right from the selection of raw materials. The materials used, such as the glass and the insulating materials, need to meet specific standards to ensure the performance of the end product. For instance, the glass should be free from impurities and defects that could affect its strength or clarity. Similarly, the insulating materials should have the right thermal resistance properties to provide adequate insulation.
During the manufacturing process, various testing procedures are carried out. These may include visual inspection to check for defects, dimensional checks to ensure the right size and shape, and performance tests to assess the insulating properties of the glass. Some manufacturers may also conduct accelerated aging tests to assess the longevity of the product.
Lastly, after the product has been manufactured, it undergoes a final quality check before being shipped to the customer. This may include a thorough visual inspection, as well as tests to verify its insulating properties and its resistance to environmental factors like temperature changes and humidity. Any product that does not meet the required standards is either discarded or sent back for rework.
In conclusion, quality control and testing procedures are crucial in the production of insulated glass. They ensure that the product meets the required standards and performs effectively in its intended application. Without these procedures, the reliability and effectiveness of insulated glass could be compromised, leading to inferior performance and potentially, product failure.
Applications and Uses of Insulated Glass
Insulated glass, also known as double glazing, is widely used in various commercial and residential settings due to its superior insulation properties. This type of glass is manufactured by sealing two or more glass panes together, creating an insulating gap filled with air or gas. This structure significantly reduces heat transfer, making it an excellent choice for energy-efficient buildings.
The primary application of insulated glass is in windows and doors for buildings. It helps maintain the indoor temperature, reducing the need for heating or cooling systems, and thus saving energy. In regions with harsh weather conditions, insulated glass is almost indispensable in homes and public buildings to provide comfort while minimizing energy consumption.
Another significant use of insulated glass is in the automotive industry. Many car manufacturers use insulated glass for car windows to provide better insulation, reduce noise, and protect passengers from harmful UV rays. This helps create a safer and more comfortable driving environment.
Apart from these, insulated glass is also used in refrigeration units, ovens, and other appliances where insulation is required. With its wide range of applications and benefits, insulated glass plays an essential role in creating energy-efficient and comfortable environments.
Innovations and Technological Advancements in Insulated Glass Manufacturing
The innovations and technological advancements in insulated glass manufacturing have significantly transformed the industry. These advancements are driven by the need for more efficient, sustainable, and high-performance products that meet the evolving demands of consumers and regulatory standards.
One of the significant innovations in insulated glass manufacturing is the introduction of high-tech machinery and automated systems. These technologies have improved production speed, accuracy, and efficiency, resulting in higher-quality glass with minimal defects. They have also reduced the risk of human error in the manufacturing process, leading to improved safety and reduced costs.
Another significant advancement is the development of new materials for insulated glass. These include high-performance glazing materials that offer better insulation properties, energy efficiency, and durability. For example, low-emissivity (Low-E) glass coatings are designed to minimize the amount of UV and infrared light that can pass through glass without compromising the amount of visible light that is transmitted.
There’s also the innovation of gas-filled insulated glass units. These are double or triple glazed window units filled with inert gases like argon or krypton in the space between the panes. These gases are more effective insulators than air, reducing heat transfer and improving energy efficiency.
Additionally, advancements in manufacturing processes have also allowed for the production of insulated glass with more complex shapes and sizes, providing more design flexibility in architecture and construction.
In conclusion, innovations and technological advancements in insulated glass manufacturing are playing a crucial role in shaping the future of the industry. They are pushing the boundaries of what’s possible, delivering more efficient, sustainable, and high-quality products that are transforming our built environment.