Laminated glass, widely used in various industries for its safety features and durability, is a unique product with a complex manufacturing process. It requires specialized knowledge, tools, and skills to cut and process this type of glass effectively. This article aims to provide a comprehensive understanding of how laminated glass is cut and processed.
In the first section, we delve into the composition and structure of laminated glass. We’ll unravel the distinct layers that make up this glass and how its construction contributes to its unique properties. Next, we’ll explore the tools and techniques employed in cutting laminated glass. This section will guide you through the step-by-step process and the specific equipment used in this delicate operation.
Safety, always a paramount concern, is our third focus. We’ll discuss the precautions and safety measures that should be taken during the cutting process to prevent accidents and ensure the wellbeing of those involved. After the cutting process, there are several steps taken to process and finish the laminated glass. We’ll discuss these methods in detail in the fourth section.
Finally, the last section will address quality control and inspection of cut laminated glass. Ensuring that the finished product meets the necessary standards and specifications is a critical part of the process, and we’ll delve into the techniques and protocols used to guarantee quality and consistency. Join us as we navigate the intriguing world of laminated glass cutting and processing.
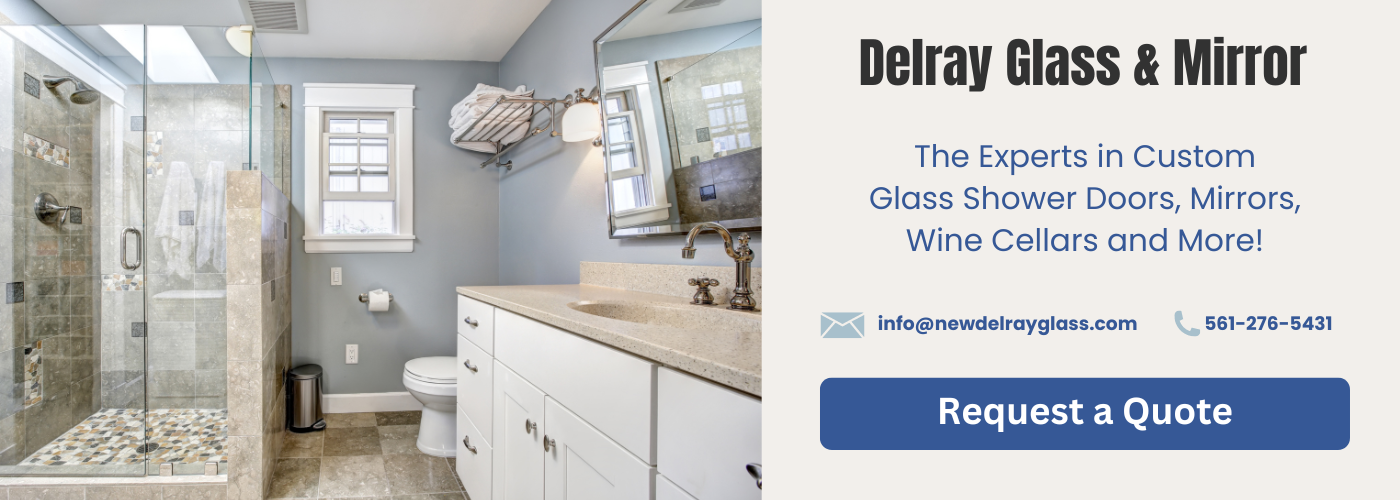
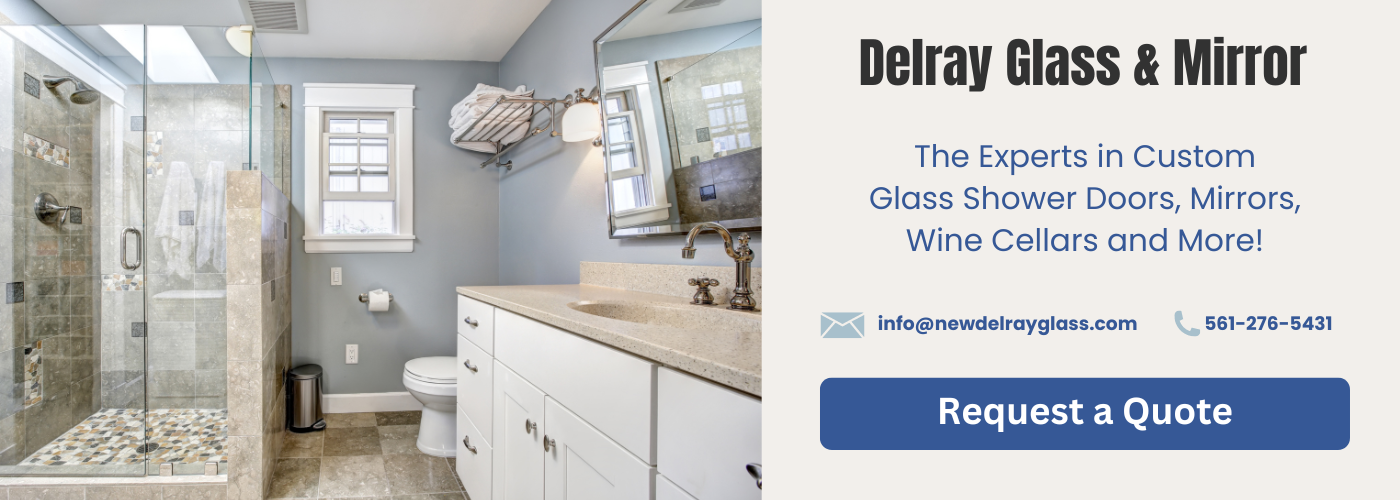
Understanding the Composition and Structure of Laminated Glass
Understanding the composition and structure of laminated glass is an essential step in understanding how it is cut and processed. Laminated glass is a type of safety glass that holds together when shattered. Its structure typically involves two or more layers of glass with an inner layer of a plastic material, usually polyvinyl butyral (PVB), sandwiched between them.
When the laminated glass is exposed to impact, this inner layer keeps the layers of glass bonded, preventing it from shattering into large shards. Instead, it causes the glass to “spider web,” creating a pattern of smaller, less dangerous pieces. The strength and durability of laminated glass come from this unique composition and structure.
The process of creating laminated glass involves bonding the layers of glass and plastic together under heat and pressure, resulting in a single piece of glass. This process can be adjusted to create laminated glass of varying thicknesses and strengths, making it a versatile material that can be used in a wide range of applications, from car windshields to skyscraper windows.
Cutting laminated glass involves a more complex process than cutting regular glass due to its layered structure. It requires specialized tools and techniques to ensure that the glass is cut precisely without damaging its inner plastic layer or causing the glass to shatter. Understanding the composition and structure of laminated glass is crucial to carry out this process safely and efficiently.
Tools and Techniques for Cutting Laminated Glass
Laminated glass cutting involves a unique set of tools and techniques to ensure precision and prevent damage. The process starts with a glass cutter, a specialized tool designed to score the surface of the glass. This score line guides the subsequent break, allowing for a clean, precise cut. Some glass cutters are equipped with a small reservoir that dispenses oil onto the wheel, reducing friction and making the cutting process smoother.
Once the surface of the glass is scored, pliers are used to apply pressure on the scored line and break the glass. This process is repeated for the other layer of the laminated glass. To separate the intermediate layer, a knife or similar sharp tool is used. It is important to note that the cutting process must be carried out with extreme care to avoid cracking or chipping the glass.
In terms of techniques, laminated glass cutting requires a firm, steady hand and a good understanding of the material’s properties. The glass needs to be properly supported during the cutting process to prevent it from vibrating or moving, which could result in an inaccurate cut. The score line must be made in one continuous motion, as stopping and starting can lead to a jagged break. The pressure applied during scoring and breaking should also be carefully controlled; too much pressure can cause the glass to crack, while too little may not create a deep enough score line.
In conclusion, the cutting of laminated glass is a delicate process that requires specific tools and techniques. It is not just about making a cut, but doing so in a way that ensures the integrity and quality of the glass is preserved.
Safety Measures During Laminated Glass Cutting
Laminated glass cutting, like any other industrial process, requires a high level of safety consideration. The nature of the material and the operation of cutting tools present potential hazards that must be effectively managed to prevent accidents or injuries in the workplace.
The first key safety measure involves the use of personal protective equipment (PPE). Cutting laminated glass can lead to the formation of glass shards, which can cause serious harm if not handled properly. Therefore, workers are required to wear safety goggles to protect their eyes, gloves to guard their hands, and in some cases, body covers to shield their skin.
Additionally, the cutting tools used in this process are typically sharp and powerful. Therefore, they should be handled with care, and only trained personnel should operate such machinery. These tools should also be properly maintained, as faulty equipment can lead to accidents.
Another safety measure pertains to the work environment. The area should be well-lit and properly ventilated, and the floor should be kept free of glass shards or any other debris that might cause slips or falls. Regular clean-ups and inspections are crucial in maintaining this safety standard.
Furthermore, proper training and awareness among workers are paramount. Workers should be aware of the safety procedures, know how to use the equipment correctly, and understand what to do in case of an accident. Regular safety drills and training sessions can ensure that all individuals are well-prepared and can respond effectively to any safety risks.
In conclusion, safety measures during laminated glass cutting are multi-faceted, involving personal protection, careful handling and maintenance of tools, a clean and safe work environment, and adequate training and awareness. All these aspects need to work in tandem to ensure a safe and efficient laminated glass cutting process.
Processing Methods After Cutting Laminated Glass
Processing Methods After Cutting Laminated Glass is a crucial stage in the manufacture and utilization of laminated glass. It’s the step that follows the cutting of the laminated glass and involves a series of processes to ensure that the cut glass is ready for use in its intended application.
After the laminated glass has been cut, it goes through a process called edge finishing. This process involves grinding the edges of the glass to make them smooth. This is a critical process as it removes any sharp edges that may be dangerous to handle. It also gives the glass a finished look.
After edge finishing, the laminated glass goes through a process called tempering. This is where the glass is heated to a high temperature and then cooled rapidly. This process makes the glass much stronger and more resistant to breakage. It is an essential process as it adds to the durability and safety of the laminated glass.
Finally, the laminated glass is cleaned and inspected. This ensures that the glass is free from any defects and is ready for use. Any pieces of glass that do not pass the inspection are rejected and recycled.
In summary, Processing Methods After Cutting Laminated Glass is an important stage in the production of laminated glass. It involves a series of processes that are designed to ensure the safety, quality, and durability of the laminated glass. Without these processes, the cut laminated glass would not be suitable for use.
Quality Control and Inspection of Cut Laminated Glass
Quality control and inspection of cut laminated glass is a crucial step in the process of laminated glass production. It ensures that the final product meets the required quality standards and is safe for use. This process involves a comprehensive check of the glass for any defects that might have occurred during the cutting or processing stages.
Inspectors look for any cracks or chips in the glass that might compromise its structural integrity. They also check the edges of the glass to ensure they have been cut and finished correctly. The lamination on the glass is inspected for any bubbles or delamination that could impact the visibility or strength of the glass. Furthermore, the overall dimensions of the glass are measured to ensure they meet the specifications provided.
In addition to visual inspection, various tools and techniques are used to assess the quality of the cut laminated glass. For instance, a light box may be used to illuminate the glass from behind, making any defects more visible. Certain types of defects might only be visible under specific lighting conditions, so different light sources may be used during the inspection process.
Quality control and inspection are not just about identifying defects. They also play a crucial role in continuous improvement. By identifying common issues and their causes, the process of cutting and processing laminated glass can be fine-tuned to minimize defects, improving the overall quality of the final product. As a result, quality control and inspection are integral to the production of laminated glass and help ensure that the end user receives a product that is safe and meets their expectations.