In the world of building materials, laminated glass holds a pivotal position due to its increased safety features. Yet, a common question often arises: “How is laminated glass tested for durability?” This article seeks to provide a comprehensive understanding of the rigorous and multifaceted testing process that laminated glass undergoes to ensure its durability and reliability.
The first section, “Understanding the Composition of Laminated Glass,” delves into the structure and materials that constitute laminated glass. By understanding its composition, we can better appreciate why and how certain tests are performed.
Next, the article explores the “Different Testing Methods for Laminated Glass Durability,” offering a broad overview of the various types of tests that laminated glass is subjected to. This section will enable readers to grasp the wide-ranging nature of these tests.
Subsequent sections focus on specific types of tests. In “Impact Resistance Test for Laminated Glass,” we explore how the glass’s capacity to withstand external forces is measured. Following this, the “Weathering and Ageing Test for Laminated Glass” section sheds light on the procedures used to assess the glass’s performance under various weather conditions and over time.
Finally, the “Thermal Stress Testing for Laminated Glass” segment examines the glass’s ability to endure temperature variations. Each of these tests plays a crucial role in ensuring that laminated glass is durable and ready to stand the test of time. Dive into this article to discover the rigorous processes that ensure the resilience of laminated glass.
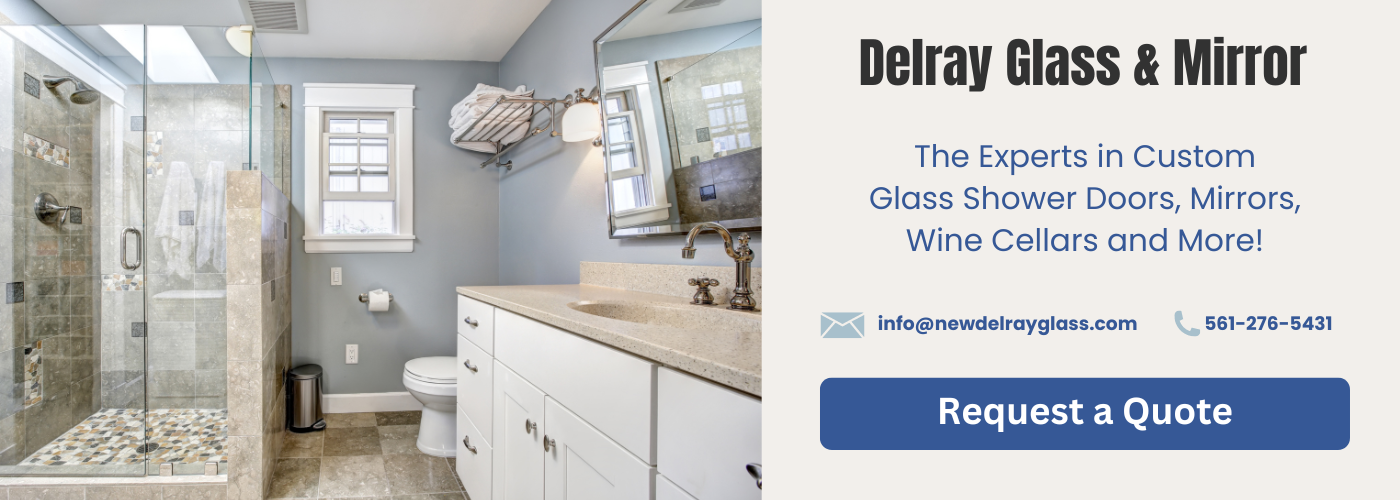
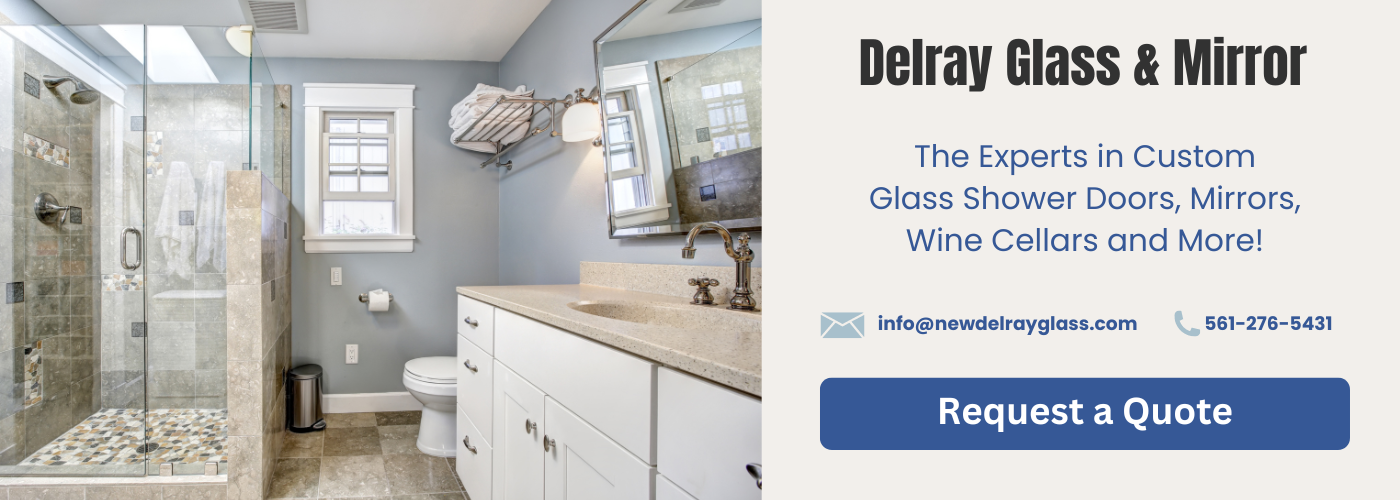
Understanding the Composition of Laminated Glass
The composition of laminated glass is a crucial aspect to comprehend when discussing its durability and the methods used for its testing. Laminated glass is a type of safety glass that stays intact even when shattered, and this unique characteristic is due to its specific composition.
In its basic form, laminated glass consists of two or more layers of glass bonded together with an interlayer made from a material like polyvinyl butyral (PVB), ethylene-vinyl acetate (EVA), or thermoplastic polyurethane (TPU). This interlayer acts as a glue, keeping the glass layers together and preventing them from breaking apart easily. When the glass is shattered, the broken pieces adhere to this interlayer, reducing the risk of injury from flying or falling glass shards.
The interlayer not only contributes to the safety characteristics of laminated glass but also adds to its durability. It provides resistance against impacts and can withstand various environmental conditions. Moreover, depending on the material used, the interlayer can also offer additional properties, such as UV radiation protection, sound insulation, and improved thermal performance.
Understanding the composition of laminated glass is fundamental in the process of testing its durability. It helps determine the appropriate testing methods, the expected results, and the potential improvements or modifications that could enhance the glass’s performance. Therefore, before any durability testing can be conducted, a thorough understanding of the composition of laminated glass is necessary.
Different Testing Methods for Laminated Glass Durability
Laminated glass is a type of safety glass that is designed to remain intact even when shattered. To ensure its durability and reliability, a variety of testing methods are employed. The second item on the list, “Different Testing Methods for Laminated Glass Durability,” delves into the specifics of these tests.
The durability of laminated glass is tested in various ways depending on the desired characteristic to be tested. Some tests focus on the glass’s ability to resist impact, while others measure how the glass withstands weathering, ageing, and thermal stress. Each of these tests has its own set of standards and methodologies that are followed to ensure the reliability of the results.
For instance, impact resistance tests involve dropping a weighted bag onto the glass from varying heights to simulate the force of flying debris or a human body. On the other hand, weathering and ageing tests expose the glass to harsh environmental conditions, such as UV light, moisture, and changing temperatures, to assess how it would perform over time when installed in a building.
Furthermore, thermal stress tests are conducted to examine how laminated glass responds to extreme changes in temperature. This is crucial since sudden temperature shifts can cause glass to crack or shatter.
It is through these rigorous testing methods that the durability of laminated glass is determined, ensuring its suitability for use in various applications where safety and durability are paramount. These tests help manufacturers improve their products and assure customers of the quality and reliability of their purchase.
Impact Resistance Test for Laminated Glass
The impact resistance test is an essential part of assessing the durability of laminated glass. This test is aimed at determining how well the glass can withstand various impacts, which is crucial for its performance in various applications such as building facades, vehicle windshields, and safety glass.
The process involves dropping a weighted bag or other object from a specific height onto the glass surface. The weight and height are variable, depending on the standards the glass is meant to meet. The glass passes the test if it manages to resist the impact without shattering. Some standards may allow minor cracking, as long as the glass maintains its structural integrity.
This test is not only important for safety reasons but also for the longevity of the laminated glass. If the glass can withstand high impact forces, it implies that it will be able to withstand the usual wear and tear, thereby extending its lifespan. Therefore, the impact resistance test is a critical step in the testing process for laminated glass durability.
Weathering and Ageing Test for Laminated Glass
Weathering and aging tests for laminated glass are crucial procedures to ensure the durability and longevity of this type of glass. These tests aim to simulate the effects of natural environmental conditions such as sunlight, temperature changes, and humidity on the laminated glass over a certain period.
The primary purpose of weathering tests is to examine the resistance of the laminated glass to the damaging effects of UV radiation. In these tests, the glass is exposed to UV light for specific periods to mimic the sun’s effect. The test helps in determining the discoloration rate of the interlayer material and the potential for delamination due to prolonged exposure to sunlight.
The aging test, on the other hand, focuses on the long-term performance of the laminated glass. It involves subjecting the glass to cycles of extreme temperatures and humidity to simulate the changing seasons and different climatic conditions. The test results help in assessing the potential for fogging between the layers of glass and the overall structural integrity of the laminated glass over time.
Both weathering and aging tests are pivotal in ensuring the durability of laminated glass. Manufacturers and quality control agencies use these tests to guarantee that the glass can withstand the rigors of environmental exposure and maintain its functionality and aesthetic appeal over the years.
Thermal Stress Testing for Laminated Glass
Thermal stress testing is a crucial part of the durability assessment of laminated glass. This method of testing is designed to simulate the conditions the glass would be subjected to in real-world scenarios. The primary purpose of thermal stress testing is to determine how well the laminated glass can withstand fluctuations in temperature without compromising its structural integrity or performance.
In a typical thermal stress test, the laminated glass is subjected to a cycle of heating and cooling. The temperature ranges and rates of change are designed to replicate those experienced in the environments in which the glass is likely to be used. For example, the glass may be heated to simulate a hot summer day and then rapidly cooled to mimic the drop in temperature that occurs at night.
The thermal stress test is essential because it helps to identify any potential weak points in the glass. If the glass can withstand the rigors of the test without cracking, shattering, or showing any signs of stress, it is considered to have passed. This gives manufacturers and consumers confidence in the product’s durability.
In conclusion, thermal stress testing for laminated glass is a vital process in ensuring the glass’s durability and reliability. By subjecting the glass to real-world conditions, manufacturers can identify and rectify any potential issues before the product reaches the consumer, thereby ensuring the highest quality and performance.