Safety glass, a vital element in countless everyday applications from automobile windshields to architectural glazing, plays an essential role in providing protection and security. But what exactly is it and how is it made? This article delves into the fascinating world of safety glass production, shedding light on its origins, the materials used, manufacturing processes, types, properties, and the rigorous quality control and testing methods implemented.
We commence with the intriguing history and development of safety glass, tracing its roots from its earliest conception to its modern-day incarnations. The evolution of safety glass is a testament to human ingenuity and technological advancement, and it has unquestionably revolutionized the way we build and protect our environments.
Next, we enter the raw, gritty world of the raw materials used in safety glass production. By understanding the components that constitute safety glass, we can better appreciate its robustness and resilience. From sand to soda ash, we will explore the essential elements that go into making this indispensable material.
Moving forward, we will delve into the intriguing manufacturing process of safety glass. From the initial batch mixing to the final thermal treatment, each step plays a pivotal role in ensuring the glass’s safety properties. This section will demystify the complex processes that transform simple raw materials into a highly engineered safety product.
We will also discuss the different types of safety glass and their properties. By recognizing the unique characteristics and benefits of each type, we can make informed decisions about which kind of safety glass is best suited for a particular application. From laminated to tempered, each type of safety glass offers a unique set of properties designed to meet specific safety requirements.
Lastly, we will examine the stringent quality control and testing methods for safety glass. Guaranteeing the safety and integrity of this type of glass is of paramount importance, and it is achieved through rigorous testing and quality assurance practices. This section will provide insight into the measures taken to ensure that each piece of safety glass meets the highest safety standards.
Join us as we journey through the multifaceted world of safety glass production, from its historical roots to the cutting-edge manufacturing processes of today. Whether you are a professional in the field, a student, or simply a curious reader, this comprehensive overview of safety glass production offers valuable insights and knowledge.
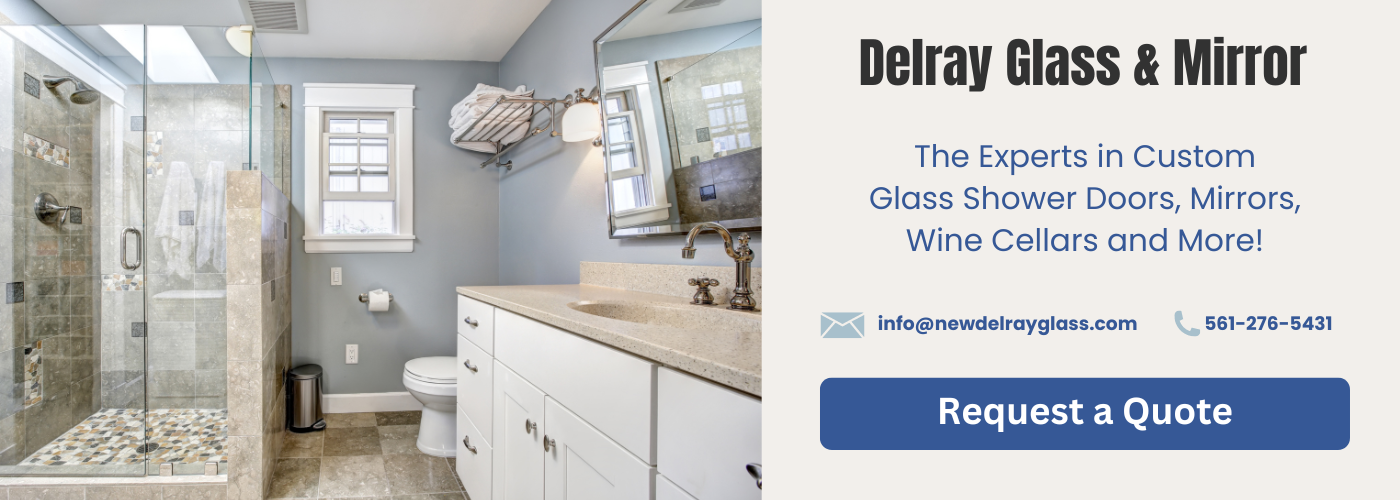
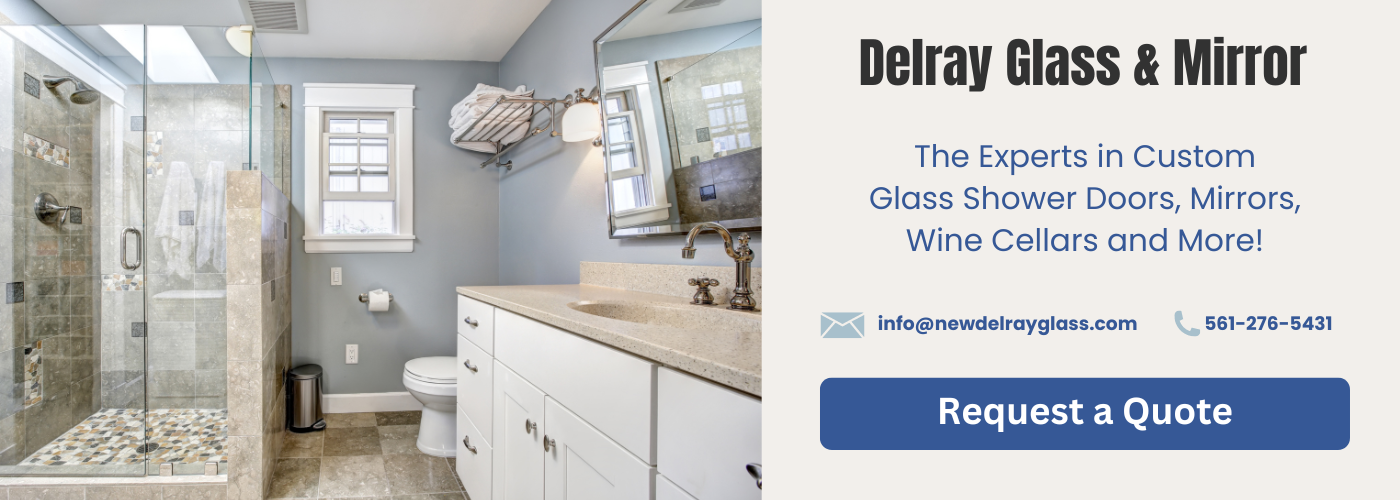
History and Development of Safety Glass
Safety glass, known also as “laminated glass” or “tempered glass”, is a type of glass that is designed to be less likely to break, and less likely to pose a threat when it does break. The origins of safety glass are fascinating, with its development having a significant impact on various industries and our everyday lives.
The history of safety glass dates back to the early 20th century. The French chemist Edouard Benedictus is credited with the accidental invention of safety glass in 1903. When a glass flask in his laboratory fell and shattered but did not break into pieces, he realized that the flask had been lined with a plastic cellulose layer which held the glass together. This observation led to the development of the first laminated safety glass, initially used in eyewear and later adopted in automobile windshields.
This breakthrough led to the development of different types of safety glass, each designed for specific applications. For instance, tempered safety glass, which is produced by heating regular glass to a high temperature and then rapidly cooling it, was developed to break into small, harmless pieces rather than large, sharp shards.
Over the years, the safety glass production process has been refined and improved. Today’s safety glass is far more resilient and safer than its early counterparts. It is used in a wide variety of applications, from car windshields to architectural installations, and continues to be an essential material in modern construction and manufacturing. The development of safety glass represents a significant advancement in safety and technology, protecting lives and enhancing the durability of numerous products.
Raw Materials Used in the Production of Safety Glass
The production of safety glass entails the use of a variety of raw materials. These include sand (silica), soda ash (sodium carbonate), dolomite, limestone, and alumina. Silica makes up the largest portion of these materials. It is combined with soda ash, which lowers the melting point of the sand, and dolomite and limestone, which help control the viscosity of the glass and make it chemically stable.
In addition to these basic materials, a variety of other ingredients are used depending upon the specific type of safety glass being produced. For example, in the case of tempered safety glass, a surface compression process is used that requires heat treatment of the raw glass. For laminated safety glass, a layer of polyvinyl butyral (PVB) is sandwiched between two layers of glass. The PVB makes the glass shatter-resistant and improves its safety characteristics.
The materials used in the production of safety glass are critical to its characteristics and performance. They not only determine the glass’s basic properties but also its safety features. Thus, understanding these materials and their roles in the production process is crucial for anyone interested in the manufacture of safety glass.
The Manufacturing Process of Safety Glass
The manufacturing process of safety glass is fascinating and involves a blend of technology and scientific understanding. This process is integral in ensuring the protective characteristics that distinguish safety glass from regular glass.
Safety glass is typically made through one of two methods: tempering or laminating. Tempered safety glass is made by heating it to just below its melting point and then quickly cooling it down. This rapid change in temperature puts the glass under stress which increases its strength, making it up to five times stronger than regular glass. When it breaks, tempered safety glass shatters into small, dull pieces instead of sharp shards, reducing the risk of injury.
In contrast, laminated safety glass is made by sandwiching a layer of polyvinyl butyral (PVB) between two layers of glass. The PVB sticks to the glass, making it more difficult to break. If it does shatter, the PVB layer holds the broken pieces together, again reducing the risk of injury.
These manufacturing methods are carefully monitored and controlled to ensure the final product meets set safety standards. The process may also be adjusted depending on the specific application of the safety glass. For example, the glass used in car windshields may be made differently from the glass used in skyscraper windows. Regardless of the specific process, the primary goal is the same: to create a product that protects people and property from the potential dangers of shattered glass.
Different Types of Safety Glass and Their Properties
Safety glass is a type of glass that is designed to be less likely to break, and less likely to pose a threat when it does break. This makes it an important material in various applications such as automobile windows, shower doors, architectural glass doors and tables, refrigerator trays, mobile screen protectors, and as a component of bulletproof glass. There are mainly two different types of safety glass – tempered glass and laminated glass.
Tempered glass, also known as toughened glass, is four to five times stronger than standard glass and does not break into sharp shards when it fails. The process of tempering puts the outer surfaces into compression and the interior into tension. Such stresses cause the glass, when broken, to crumble into small granular chunks instead of splintering into jagged shards, which is much less likely to cause injury.
On the other hand, laminated glass is made by sandwiching a layer of polyvinyl butyral (PVB) between two pieces of glass. The benefit of laminated glass is that if it’s broken, the PVB layer keeps the glass from shattering. This is why laminated glass is used for car windshields – in the event of a crash, the glass shards stick to the plastic layer, reducing the risk of injury.
In addition to tempered and laminated glass, there are also other types of safety glass like wire mesh glass (used in fire-resistant doors and windows) and plexiglass (used where a transparent, strong material is required but safety glass is too heavy). Each type of safety glass has its unique properties and uses, making it a versatile and crucial material in many aspects of our daily life.
Quality Control and Testing Methods for Safety Glass
Quality control and testing methods for safety glass are key components in the overall safety glass manufacturing process. These methods ensure that the final product is not only safe for use, but also meets the highest standards of quality and durability.
The quality control process begins as soon as the raw materials are received. These materials are rigorously tested for purity and consistency before they are used in the manufacturing process. This helps to ensure that the safety glass made from these materials is of the highest possible quality.
During the manufacturing process, the safety glass undergoes numerous tests. These tests are designed to assess its strength, durability, and resistance to impact. In one common test, a weighted bag is dropped onto the glass from a certain height to see if it shatters. The glass is also subjected to heat and pressure tests to check its resistance to these forces.
After the safety glass has been manufactured, it undergoes further testing before it is shipped to customers. This includes visual inspections to check for any defects or imperfections, as well as additional strength and durability tests. Only when the safety glass has passed all of these tests is it deemed ready for use.
In conclusion, quality control and testing methods for safety glass are vital to ensure that the final product is safe, durable, and of the highest quality. These methods help to ensure that when you look through a piece of safety glass, you can do so with confidence, knowing that it has been thoroughly tested and inspected.