When it comes to enhancing the safety and durability of bathroom fixtures, the glass used in shower doors is a prime example of how material science and engineering come into play. The process of tempering glass, a method developed to increase its strength and safety, is particularly critical for applications like shower doors where human safety and everyday use are closely intertwined. This article delves into the meticulous process of tempering glass specifically for shower doors, ensuring it can withstand impacts and thermal stresses without compromising on safety.
We begin by exploring the **Glass Composition and Preparation**, where the type of glass and its initial treatment set the foundational properties for what will become a resilient and safe shower door. Next, the **Heating Process** is crucial as the glass must be heated to a precise temperature that is high enough to alter its internal structure but controlled to avoid any deformities or weaknesses.
Following the heating, the **Cooling Process (Quenching)** is what truly defines the tempering, rapidly cooling the glass to lock in a new, tougher structure. This stage is critical in enhancing the glass’s toughness and making it far less likely to cause injury if broken. We then look at the **Safety Features and Standards** that govern the production of tempered glass for shower doors, ensuring that every piece meets rigorous safety criteria to be fit for consumer use.
Finally, **Testing and Quality Control** measures are discussed, highlighting how each batch of tempered glass is scrutinized for defects and inconsistencies, ensuring that only the highest quality glass makes it to your bathroom. This comprehensive approach to the tempering process not only enhances the safety of shower doors but also extends their lifespan, making them a wise investment for any modern home.
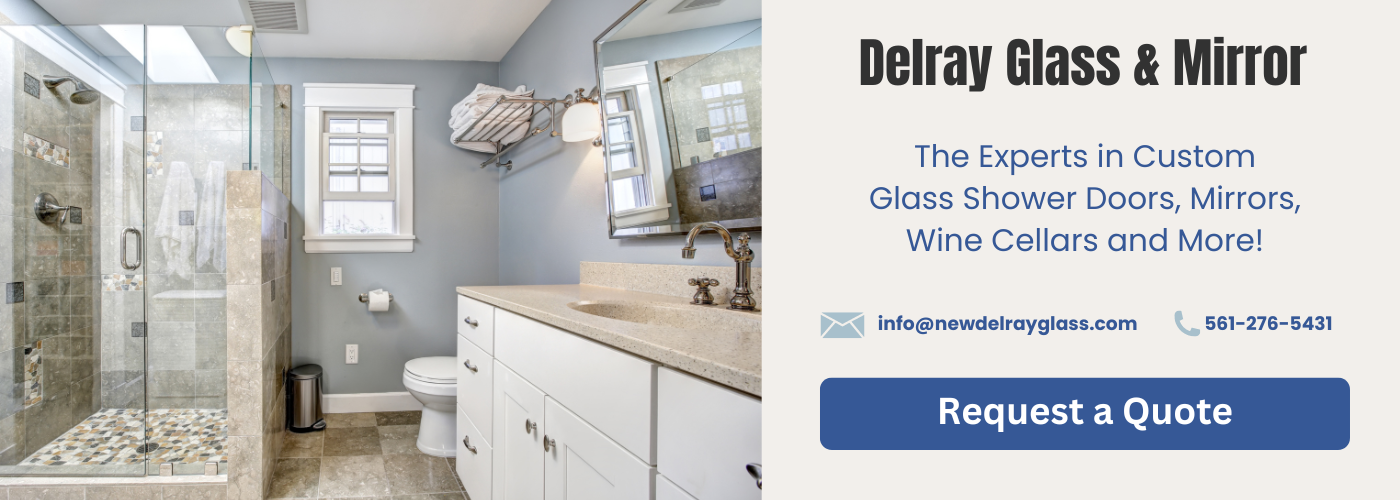
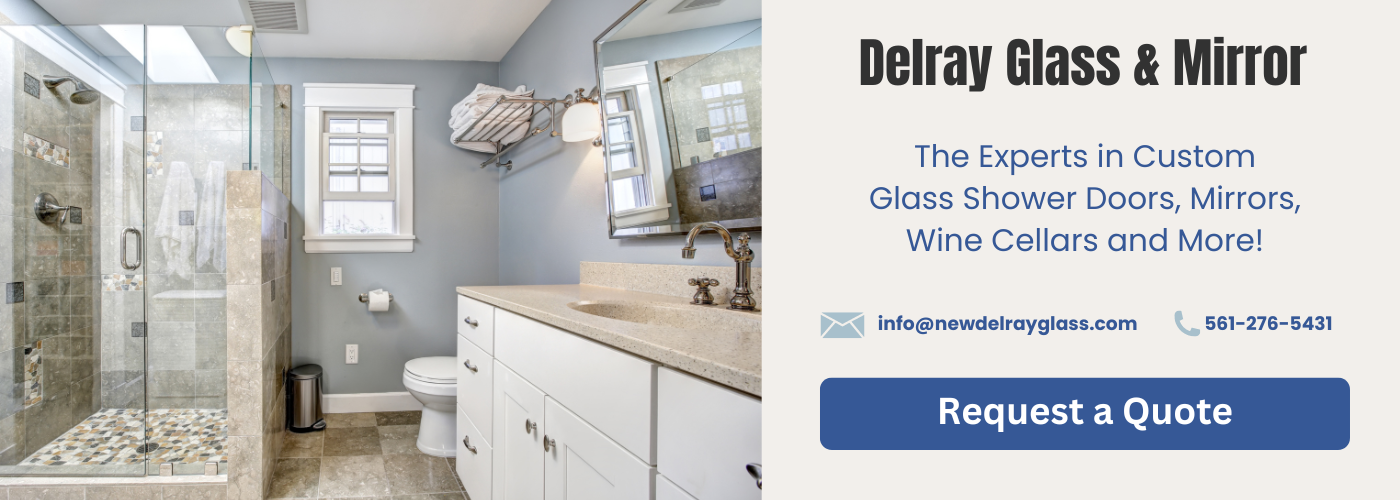
Glass Composition and Preparation
The process of tempering glass for shower doors begins at a very foundational level, focusing on glass composition and preparation. This initial step is crucial as it sets the stage for the strength and safety characteristics of the final product. The typical glass used in these applications is a type of safety glass, which is formulated to be more durable and less prone to breaking than regular glass.
The composition of glass generally involves mixing silica sand with soda ash and lime. These materials are carefully measured and combined in specific proportions to ensure the glass will exhibit the desired properties. In some cases, other additives like alumina or magnesium oxide are included to enhance the glass’s physical properties.
Once the raw materials are combined, the mixture is melted in a furnace at temperatures that can exceed 1700°C. This high heat ensures that all components are thoroughly fused together to form a uniform and clear molten glass. After melting, the glass is conditioned to remove any inconsistencies in its texture and to ensure it flows smoothly for the next steps.
The preparation phase also involves shaping the molten glass. This is typically done using a process called float glass technology, where the molten glass is poured onto a bed of molten tin. This method provides a smooth surface and uniform thickness, which are critical for the quality and safety of the final tempered glass. The glass must be perfectly flat and free of any distortions or impurities to ensure that it tempers correctly.
Understanding the meticulous attention to detail in the glass composition and preparation phase helps underscore the complexity and importance of creating glass that is not only functional for shower doors but also enhances safety for users. The integrity of these processes directly influences the effectiveness of subsequent tempering steps, ultimately contributing to the production of reliable and sturdy glass suitable for bathroom environments.
Heating Process
The heating process is a crucial step in the tempering of glass for shower doors, which significantly enhances its safety features. This part of the tempering process involves heating the glass to a temperature high enough to bring it to its softening point. This is typically around 600 to 650 degrees Celsius (1112 to 1202 degrees Fahrenheit), but the exact temperature can vary based on the composition and thickness of the glass.
During this stage, the glass is placed inside a tempering furnace where it is heated uniformly. The goal is to ensure that the entire body of the glass reaches the desired temperature without any cold spots, which could lead to uneven tempering. Uniform heating is critical because it allows for even expansion of the glass, which is necessary for achieving consistent strength across the entire pane once it is cooled.
The heating process must be precisely controlled. If the glass is heated too much, it can become too soft and lose its shape, potentially causing defects in the final product. On the other hand, insufficient heating can prevent the glass from reaching the necessary state for proper tempering. Thus, technicians closely monitor the temperature and the time the glass spends in the furnace to ensure optimal conditions for the next phase, which is cooling or quenching.
Understanding and controlling the heating process is vital for producing tempered glass that is not only stronger than regular glass but also safer. In the event of breakage, tempered glass shatters into small, blunt pieces that are less likely to cause injury, a property that is highly desirable in shower doors and other household glass elements where human safety is paramount.
Cooling Process (Quenching)
The cooling process, also known as quenching, is a crucial step in the tempering of glass used for shower doors, significantly enhancing its safety properties. After the glass is heated to a temperature of over 600 degrees Celsius, it must be cooled rapidly to achieve the desired characteristics of tempered glass. This rapid cooling is accomplished by blowing air on both surfaces of the glass at a precisely controlled rate.
Quenching causes the outer surfaces of the glass to cool and solidify much faster than the inner part, creating a tension in the glass as the inside remains relatively hotter and more fluid for a short time. This tension results in a balance between the outer layers’ compression and the inner layer’s tension once the glass has completely cooled. This structural change gives tempered glass its strength and its characteristic property of crumbling into small, blunt pieces rather than sharp shards upon breaking. This safety feature significantly reduces the risk of injury in case the glass breaks, making it ideal for use in environments where human safety is paramount, such as in shower doors.
The specifics of the cooling process, such as the temperature of the air and the speed at which it is applied, are carefully controlled to ensure the quality and consistency of the tempered glass. The uniformity of cooling is crucial, as non-uniform cooling can lead to weak spots and an increased likelihood of breakage under stress. Advanced tempering systems often integrate computer controls to monitor and adjust these parameters continuously during the quenching process, ensuring that every piece of glass meets the stringent safety standards required for its use in shower enclosures and other applications.
Safety Features and Standards
When it comes to the manufacturing of glass for shower doors, ensuring safety is paramount. This is addressed in detail under item 4: Safety Features and Standards. Tempered glass, used in shower doors, is engineered to be safer than regular glass by undergoing a series of treatments that enhance its strength and cause it to shatter into small, blunt pieces rather than sharp shards upon breakage.
The process of tempering glass for use in shower doors involves heating the glass to over 600 degrees Celsius and then rapidly cooling it with blasts of air—a technique known as quenching. This treatment creates tension in the glass as the surfaces cool and compress faster than the interior. The end product is much stronger than untreated glass and, importantly, safer in cases where breakage might occur.
In terms of standards, tempered glass for shower doors must meet specific safety regulations and standards set by various organizations. In the United States, for example, such standards are outlined by the American Society for Testing and Materials (ASTM). These standards ensure that the glass, if it does break, will crumble into small granular chunks instead of breaking into jagged shards that can cause serious injuries. Compliance with these standards is not just a legal requirement but also a commitment to consumer safety.
These safety features and adherence to strict standards are critical for minimizing the risk of injury from broken glass in bathroom environments. They are a testament to the advancements in material science and manufacturing techniques that prioritize human safety in everyday products.
Testing and Quality Control
Testing and quality control are crucial steps in the manufacturing process of tempered glass for shower doors, ensuring that the glass meets safety standards and is durable enough for everyday use. This phase of production is where each piece of glass is rigorously tested for its strength and ability to handle impact and thermal stresses.
The process begins with the testing of glass samples from each batch to ensure consistent quality across the production. The samples undergo various tests, such as impact tests, which simulate both small and large forces to check how well the glass can resist breaking. Another common test is the fragmentation test, where the glass is broken under controlled conditions to ensure that it shatters into small, blunt pieces that are less likely to cause injury, which is a defining characteristic of tempered glass.
Additionally, thermal stress tests are conducted to assess the glass’s ability to withstand sudden changes in temperature, which is particularly important for bathroom environments where hot showers can cause significant temperature fluctuations. Quality control teams also routinely check for visual defects and dimensional accuracy to ensure that each piece of glass not only performs well but also fits precisely with the hardware and fixtures of shower doors.
Through these meticulous testing and quality control procedures, manufacturers can guarantee that the tempered glass used in shower doors is safe, reliable, and compliant with international safety standards. This not only helps in protecting end-users but also enhances the manufacturer’s reputation for quality and safety.