In the world of glass art and design, sandblasting is a popular technique that can elevate the appearance of a simple glass piece into a unique and beautiful work of art. However, to obtain the perfect frosted finish, the preparation of the glass surface for sandblasting is essential. This article will guide you through the key steps on how to prepare a glass surface for sandblasting, ensuring an optimal outcome for your project.
Firstly, we will help you understand the basics of sandblasting. This will include an overview of what sandblasting is, how it works, and why preparing your glass surface is so important. The second topic focuses on the selection of appropriate sandblasting materials. Choosing the right abrasive medium can significantly impact the final result, and we’ll guide you on making the right choice.
The heart of the article will be dedicated to the cleaning and preparation of the glass surface. This is an essential step, as any impurities or residues left on the glass can affect the sandblasting process and the final result. Next, we will address safety measures during sandblasting. Working with glass and abrasive materials can pose some risks, and knowing how to protect yourself is crucial.
Lastly, we will delve into the techniques for effective sandblasting on glass. We will provide tips, tricks, and techniques to help you achieve the desired finish. From selecting the correct pressure to mastering the sandblasting angle, we aim to equip you with all the necessary knowledge to succeed in your sandblasting projects. Whether you’re a novice or a seasoned professional, this comprehensive guide will help you prepare a glass surface for sandblasting with confidence and precision.
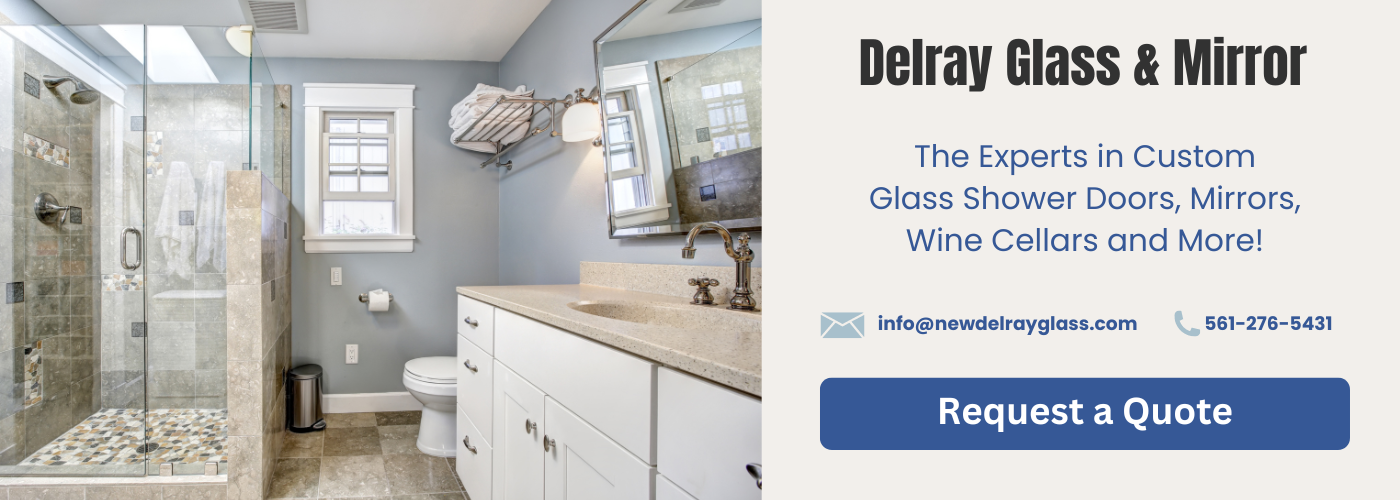
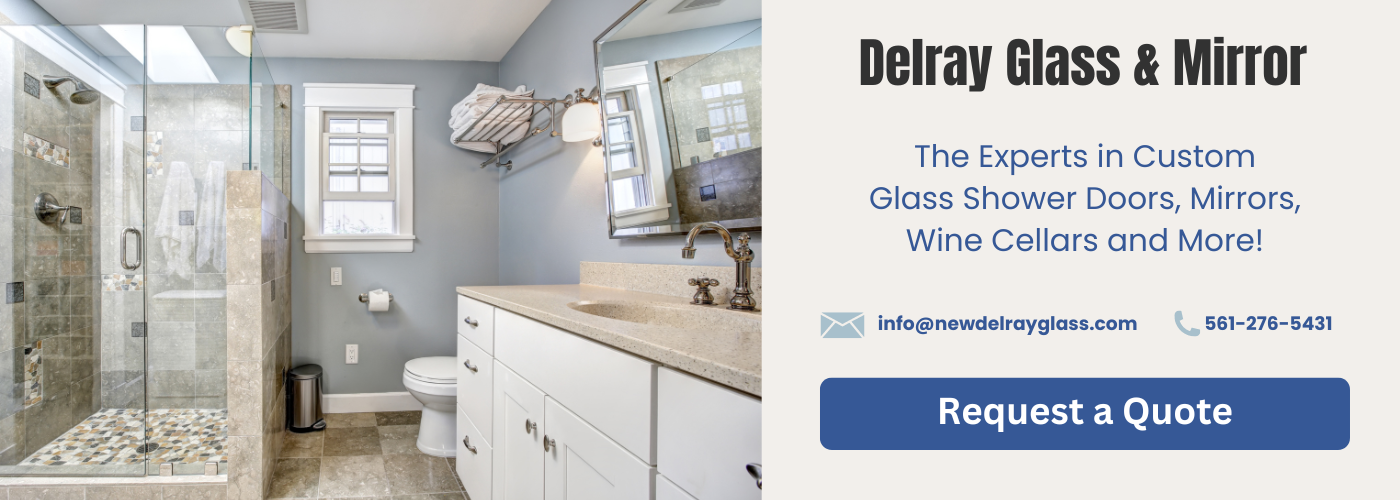
Understanding the Basics of Sandblasting
Before you can effectively prepare a glass surface for sandblasting, you must understand the basic principles of sandblasting itself. Sandblasting, otherwise known as abrasive blasting, is a process used to treat surfaces for a variety of purposes. It involves propelling small, abrasive particles at high speed onto a surface, in this case, glass, in order to modify its properties.
The type of abrasive used, the speed at which it’s propelled, and the angle of impact can all be manipulated to achieve different results. On a glass surface, sandblasting can be used to create a frosted effect, to clean the surface, or to prepare it for further treatment such as painting or etching.
Understanding these basics will allow you to make informed decisions during the preparation process. For instance, knowing that the type of abrasive can affect the result helps you choose the right material for your project. The understanding of speed and angle of impact will guide you in setting up your equipment correctly. This knowledge is the foundation that will guide you through the subsequent steps of preparing a glass surface for sandblasting.
Selection of Appropriate Sandblasting Materials
The selection of appropriate sandblasting materials is an integral part of the preparation process for sandblasting a glass surface. This step is crucial because the type and grade of the sandblasting material can significantly affect the final outcome.
There is a variety of materials available for sandblasting purposes, each with its unique properties. For instance, glass beads are often used for their ability to create a smooth, polished finish. On the other hand, aluminum oxide grit is typically chosen for its hardness and cutting ability, making it ideal for etching designs into a glass surface.
The choice of sandblasting material will also depend on the specific requirements of the project. For instance, if you need to remove stubborn impurities from the glass surface, a more abrasive material might be needed. However, if your aim is to create a decorative effect, a softer, less aggressive material could be more appropriate.
It’s also essential to consider the size of the material. A larger grain size will result in a more intense sandblasting effect, while smaller grains will produce a more delicate effect. Therefore, the selection of the appropriate sandblasting material requires careful consideration of the desired outcome, the nature of the glass surface, and the specific requirements of the project.
In summary, the selection of appropriate sandblasting materials is a critical step in preparing a glass surface for sandblasting. It requires a clear understanding of the materials available, their properties, and how they can impact the final result.
Cleaning and Preparing the Glass Surface
Cleaning and preparing the glass surface is a crucial step in the sandblasting process. This step is foundational to the success of the project, as a clean and properly prepared surface will adhere better to the sandblasting materials. This not only ensures a smoother finish but also enhances the longevity of the sandblasted design.
The cleaning process involves removing any dirt, oils, or impurities from the glass surface. This can be done using a simple glass cleaner or a more specialized cleaning solution, depending on the condition of the glass. It’s important to clean the glass thoroughly, as any remaining impurities can interfere with the sandblasting process, potentially leading to uneven results.
Once the glass is clean, the next step is preparing the surface for sandblasting. This may involve applying a stencil or mask to the glass. The design of the stencil will determine the pattern that the sandblasting will follow. It’s important to ensure the stencil adheres properly to the glass surface to prevent any stray sandblasting from damaging the design.
In essence, cleaning and preparing the glass surface is a critical step in sandblasting. By ensuring the glass is clean and the stencil is properly applied, you can set the stage for a successful sandblasting project.
Safety Measures During Sandblasting
Safety measures during sandblasting are an essential part of the overall process of preparing a glass surface for sandblasting. This step is crucial because it ensures that the individual performing the sandblasting can do so without risking injury or harm.
Sandblasting, by its nature, involves the propulsion of small particles at high speed. This can pose a risk of injury, particularly to the eyes and skin. Therefore, it is paramount that proper safety gear is worn during the procedure. This includes gloves, a face shield or safety goggles, and protective clothing.
Additionally, the area in which the sandblasting is taking place must also be prepared to ensure safety. This might involve cordoning off the area to prevent bystanders from getting too close, as well as ensuring that the area is well-ventilated. Poor ventilation can lead to the accumulation of dust and other particles, which can be harmful if inhaled.
Finally, it’s also important to ensure that the sandblasting equipment itself is in good working order. Regular maintenance and checks can prevent malfunctions that could potentially lead to accidents.
In summary, safety measures during sandblasting are a key subtopic when discussing how to prepare a glass surface for sandblasting. They help to ensure that the procedure can be carried out effectively, efficiently, and most importantly, safely.
Techniques for Effective Sandblasting on Glass
Techniques for effective sandblasting on glass are pivotal in ensuring a successful project outcome. It’s not just about the process of sandblasting, but the manner in which it’s done that can make a significant difference. These techniques can vary depending on the nature of the project, the type of glass, and the intended result.
One of the fundamental techniques is controlling the pressure of the sandblasting machine. The right pressure ensures the glass is not damaged during the process. Usually, a lower pressure is recommended when sandblasting glass to prevent any potential harm.
Another important technique is selecting the suitable abrasive. The choice of abrasive can directly influence the final result. Some commonly used abrasives for glass include aluminum oxide and silicon carbide. These materials are effective yet gentle enough to prevent damaging the glass surface.
The technique of sandblasting in a steady, uniform manner is also key. This helps ensure an even finish and prevents any distortions or inconsistencies on the glass surface. It’s crucial to move the sandblasting nozzle consistently and to maintain a uniform distance from the glass surface.
In conclusion, the techniques for effective sandblasting on glass involve a combination of careful pressure control, appropriate abrasive selection, and steady, consistent sandblasting. Combining these techniques can help achieve the best possible results in sandblasting projects involving glass.