Laminated glass is a type of safety glass that holds together when shattered and is widely used in applications where safety, security, and durability are paramount. However, not all laminated glass is created equal. The quality of laminated glass can vary significantly, and it’s crucial that consumers, builders, and other stakeholders understand how to verify the quality of this versatile material. This article delves into the intricate process of verifying the quality of laminated glass.
The first section of our comprehensive guide will explore the various standards and certifications for laminated glass quality. The importance of these certifications cannot be overstated as they provide an assurance that the glass meets specific safety, durability, and performance standards set by recognized bodies.
In the second section, we will delve into the physical inspection methods for laminated glass. Physical inspection is a vital step in assessing the quality of laminated glass as it can reveal defects that may impair the glass’s performance or safety.
Moving on, the third section will detail the testing procedures for laminated glass durability. These tests provide objective data about the glass’s ability to resist different forces, such as impact, pressure, and weather elements.
The fourth section will focus on assessing the optical quality of laminated glass. The optical quality of glass reflects its clarity and transparency, which are crucial factors in many applications.
Lastly, we will evaluate the safety features of laminated glass. Safety is one of the most desirable features of laminated glass and understanding these features is key to making an informed choice.
By understanding these five key areas, you’ll be well-equipped to verify the quality of laminated glass, ensuring that you’re getting a product that’s safe, durable, and meets your specific needs.
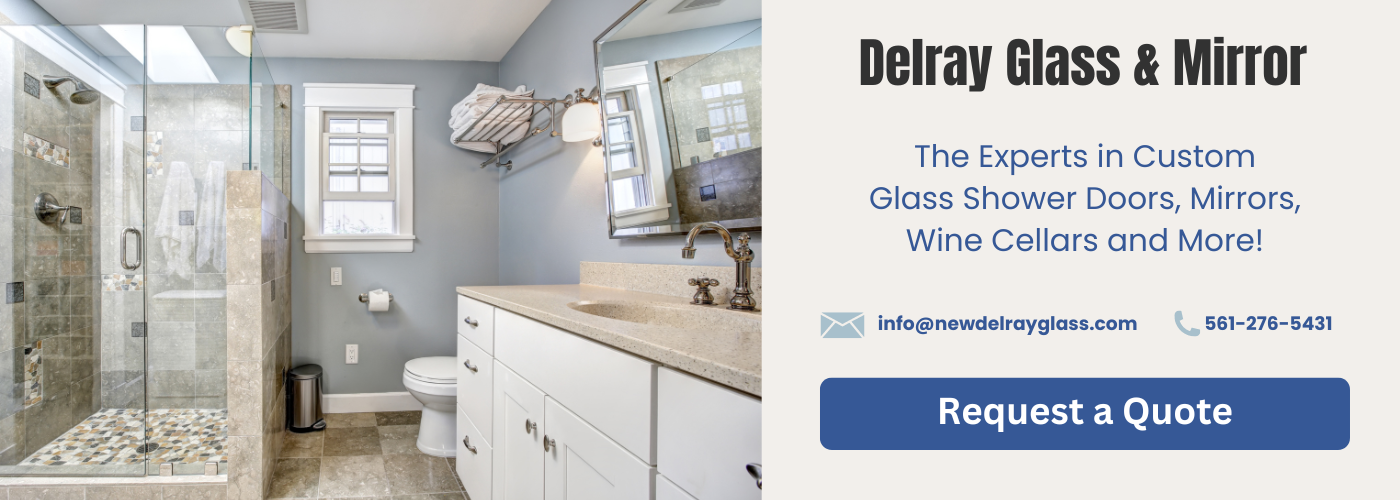
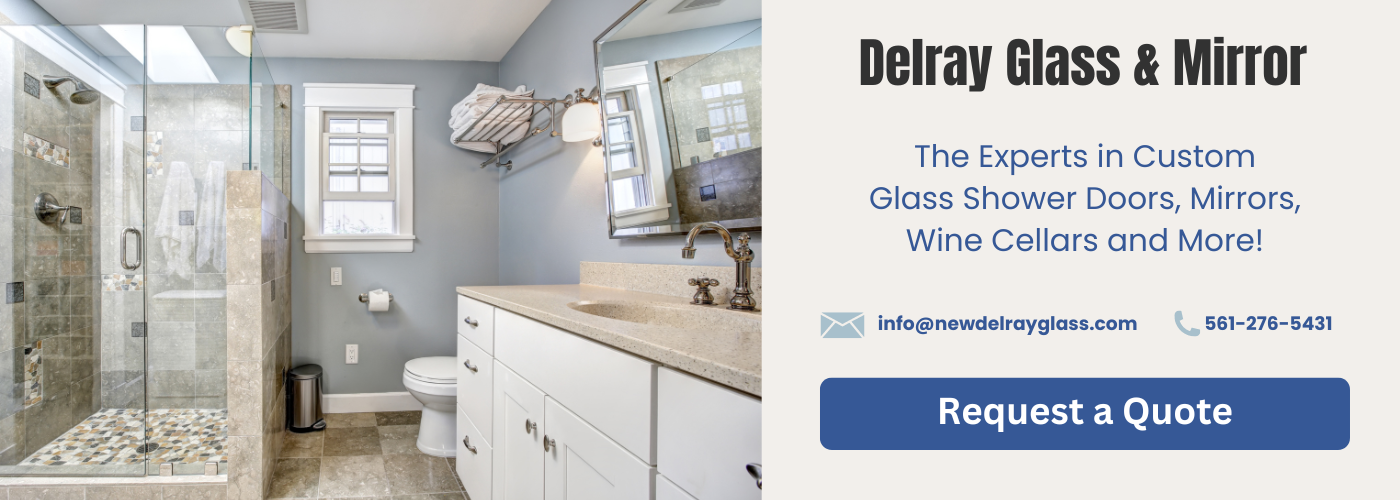
Standards and certifications for laminated glass quality
Standards and certifications play a crucial role in verifying the quality of laminated glass. They provide a benchmark that manufacturers must meet or exceed, ensuring the production of high-quality, safe, and reliable products. Standards and certifications are typically established by recognized international or national organizations, and they cover various aspects such as strength, durability, safety, and optical quality.
One of the most common certifications for laminated glass is the ISO 12543, which pertains to the materials and processes involved in its production. This standard certifies that the glass has been made following stringent quality controls, which guarantees its performance and safety.
Another essential standard is the ANSI Z97.1, a safety standard for architectural glazing materials used in buildings. Meeting this standard ensures that the laminated glass is safe for use in construction and has undergone significant impact testing.
Furthermore, the ASTM C1172 standard specifies the quality requirements for the production of laminated architectural flat glass. This includes factors like the lamination process, the interlayer materials used, and the adhesion quality.
To ensure that laminated glass meets these quality standards and certifications, manufacturers often conduct regular audits and inspections. These checks guarantee that the production process is up to par and that the final product will perform as expected. Therefore, when verifying the quality of laminated glass, checking for these standards and certifications is a must.
Physical inspection methods for laminated glass
Physical inspection methods are integral to verifying the quality of laminated glass. This approach primarily involves a detailed examination of the physical attributes of the laminated glass.
One of the most basic physical inspection methods is visual inspection. This involves checking the laminated glass for any noticeable imperfections such as scratches, cracks, bubbles, or defects in the lamination. It’s often the first step in inspection, as it can quickly identify any major issues that could affect the glass’ performance.
Another important inspection method is checking the thickness of the laminated glass. The thickness of the glass and the interlayer can determine its strength and effectiveness. Specialized tools, such as a vernier caliper, can be used to measure the thickness accurately.
Moreover, the edge finish of the glass is also inspected. A quality laminated glass should have a smooth and well-finished edge, as rough or jagged edges can lead to safety issues.
In addition to these, the color and transparency of the glass can also be assessed. Any discoloration or cloudiness can indicate problems with the lamination process or the quality of the materials used.
Physical inspection, while straightforward, requires a keen eye for detail and a thorough understanding of the standards and requirements for laminated glass. While it may not catch all potential issues, it’s a critical step in ensuring the overall quality of the laminated glass.
Testing procedures for laminated glass durability
The durability of laminated glass is a significant quality indicator. This type of glass is often used in situations where safety and durability are paramount, such as in automobile windshields, architectural glass, and even in safety goggles. Therefore, testing the robustness and longevity of laminated glass is critical.
Testing procedures for laminated glass durability typically involve several steps. First of all, the glass is subjected to varying levels of pressure to measure its strength. This can help determine how much force the glass can withstand before it breaks or cracks. This aspect is crucial, especially in applications where the glass may be subjected to impact, such as in vehicles or buildings located in areas prone to natural disasters.
Another part of testing laminated glass durability involves assessing its resistance to environmental factors, such as UV radiation, temperature changes, and moisture. For example, laminated glass should be able to withstand high levels of UV radiation without its layers delaminating or its optical clarity degrading. Similarly, the glass should maintain its structural integrity even when subjected to high or low temperatures and varying levels of humidity.
Lastly, the durability of laminated glass is also tested by assessing its resistance to chemicals. The glass should not corrode or degrade when exposed to common chemicals, ensuring its longevity and usability across various industries.
In conclusion, testing procedures for laminated glass durability is an indispensable part of verifying the quality of this type of glass. These tests ensure that the laminated glass is not only safe to use but also durable and resistant to various environmental and physical factors.
Assessing the optical quality of laminated glass
Assessing the optical quality of laminated glass is an important part of verifying its quality. The optical quality refers to how well the laminated glass transmits light and how clearly objects can be seen through it. This is particularly crucial for applications where a clear view is necessary, such as in automobile windshields or architectural installations.
One of the key measures of optical quality is clarity, or the degree to which the glass is free from distortion and aberrations. High-quality laminated glass should offer a clear, undistorted view. Any imperfections, such as bubbles, streaks, or de-lamination, can affect not only the appearance but also the performance of the glass.
Another important factor in assessing optical quality is the color of the glass. While some degree of color is acceptable and even desirable in certain applications (for instance, tinted glass for sun control), it’s important that the color is consistent and uniform across the entire piece of glass.
Finally, light transmission is another important aspect of optical quality. Laminated glass is typically made of multiple layers of glass and interlayer material, which can affect how much light is able to pass through. High-quality laminated glass should allow a high percentage of visible light to pass through while blocking harmful UV rays.
In conclusion, assessing the optical quality of laminated glass involves looking at several factors, including clarity, color, and light transmission. By carefully examining these aspects, one can determine whether the laminated glass meets the necessary quality standards.
Evaluating the Safety Features of Laminated Glass
Evaluating the safety features of laminated glass is a key aspect of verifying its quality. Laminated glass is renowned for its superior safety characteristics compared to other types of glass due to its construction. This involves bonding two or more layers of glass with an interlayer of polyvinyl butyral (PVB) or ethylene-vinyl acetate (EVA). This process ensures that, if the glass is shattered, it does not break into dangerous shards but sticks to the plastic layer, thus reducing the risk of injury.
One way to evaluate the safety features of laminated glass is to conduct impact tests. These tests measure how the laminated glass responds to different levels of force, which can range from a small object impacting the glass to a human body impact test. The results of these tests can provide insights into the quality and safety of the laminated glass.
Another approach is checking the adhesion between the glass and the interlayer. This can be done through a peel test, which assesses the strength of the bond between the glass and the plastic layer. A strong bond is crucial in ensuring the safety features of the laminated glass, as it ensures that the glass will adhere to the interlayer in the event of breakage.
In sum, evaluating the safety features of laminated glass involves a combination of physical tests and inspections. These methods help determine whether the laminated glass can withstand impacts and whether it remains safe even when shattered. These features are essential in a variety of applications, from automotive windscreens to architectural installations.