Glass is a staple material in countless applications, from the architectural majesty of skyscrapers to the delicate precision of optical instruments. Despite its ubiquitous presence, not all glass is created equal. The question of whether there is a difference in durability among various glass types is crucial for engineers, architects, and consumers alike, as it influences decisions in design, safety, and cost-efficiency. In this article, we will explore the factors that contribute to the durability of different types of glass.
First, we will examine the main types of glass, such as soda-lime glass, borosilicate glass, and laminated glass, each possessing unique characteristics and benefits. Understanding these distinctions is essential for assessing their relative durability. Next, the focus will shift to the manufacturing processes, which play a pivotal role in determining the strength and longevity of glass. Processes such as tempering and annealing alter the internal stress profiles of glass, thus enhancing its durability.
The chemical composition of glass also greatly affects its durability. Additives and impurities can increase resistance to thermal shock, chemical degradation, or mechanical failure. Furthermore, the physical properties of glass, such as density, hardness, and elasticity, are directly linked to its durability. These properties determine how glass behaves under various stressors, such as impact, pressure, and extreme temperatures.
Lastly, we will discuss the applications and usage contexts of different glass types, as the suitability and performance of glass can vary greatly depending on its environment. For example, glass used in coastal buildings requires different durability characteristics compared to glass used in vehicular applications. By examining these subtopics, this article aims to provide a comprehensive understanding of how and why the durability of glass differs among its many forms, guiding the selection process for specific needs and applications.
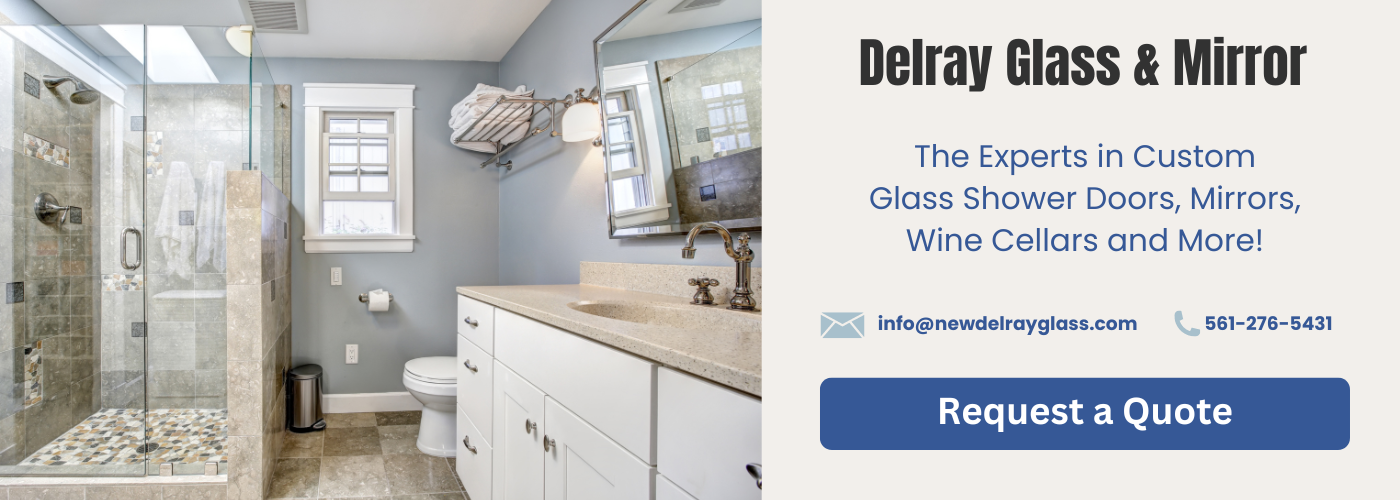
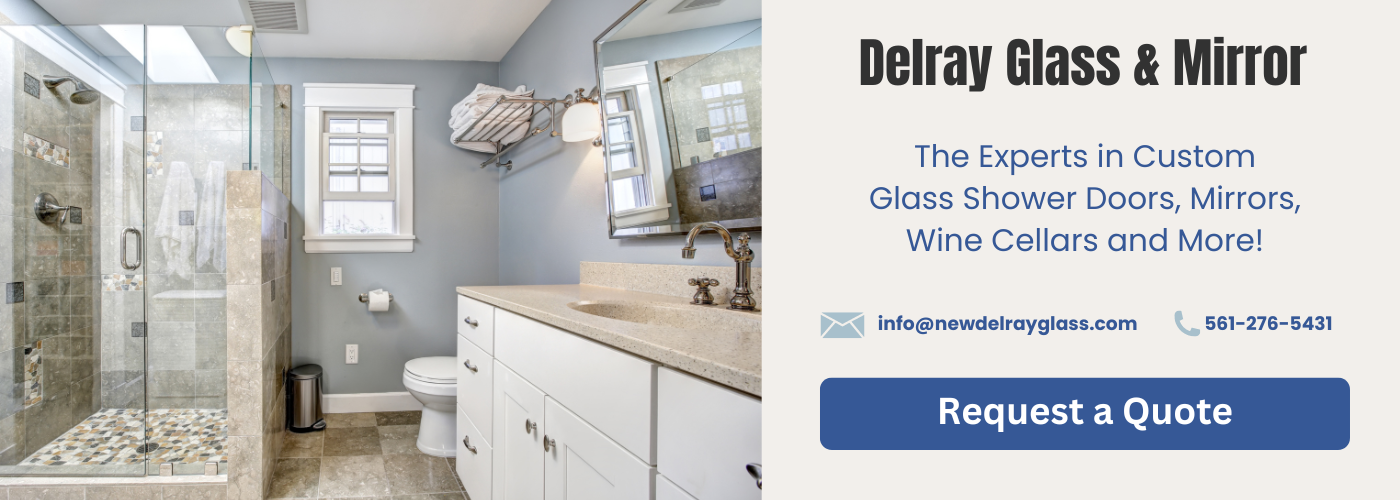
Types of Glass
Glass is a versatile and widely used material that comes in various types, each with distinct properties and applications. The differences in glass types largely stem from their chemical composition and the manufacturing processes used to produce them. Understanding these differences can provide insights into their relative durability and suitability for specific applications.
The most common type of glass is soda-lime glass, which comprises about 90% of all manufactured glass. It is made from silica, soda (sodium carbonate), and lime (calcium carbonate), with small amounts of alumina, magnesium oxide, and other minor additives. This type of glass is used for windows, bottles, and common glassware. Its popularity is due to its optical clarity and general durability, although it is not particularly resistant to high temperatures or chemical exposure.
Another type of glass is borosilicate glass, which is known for its impressive thermal resistance and durability. This glass type contains a significant amount of boron oxide, which allows it to withstand high temperatures and sudden changes in temperature. This makes it ideal for laboratory equipment, cooking ware, and lighting products. Borosilicate glass is also more resistant to chemical corrosion compared to soda-lime glass.
Lead glass, another variety, contains a high percentage of lead oxide, which increases its refractive index and makes it ideal for optical components like lenses and prisms, as well as decorative objects like crystal glassware. The presence of lead imparts a density and clarity that is prized in luxury glass items, though it is less durable when exposed to quick, drastic temperature changes.
Each type of glass has been developed to meet specific needs, and their unique compositions and manufacturing processes influence their durability. Soda-lime glass, while not as durable under high temperatures or chemical exposure, is sufficient for everyday products. Borosilicate glass offers enhanced durability where thermal resistance is necessary, and lead glass provides optical qualities and aesthetic appeal for luxury items. When selecting a type of glass, it is crucial to consider the specific requirements and stresses the glass will need to withstand, ensuring the choice of glass matches its intended use.
Manufacturing Processes
The manufacturing processes of glass significantly impact its durability, making it a crucial aspect to consider when discussing the differences in durability among various glass types. Glass is primarily created through two main processes: float glass process and the rolled glass process. Each process influences the strength, quality, and application of the glass produced.
The float glass process, invented by Sir Alastair Pilkington in the 1950s, involves melting silica sand, soda ash, limestone, and other chemicals and then floating this molten glass on a bed of molten tin. This method produces smooth, uniform, and high-quality glass sheets, which are widely used in windows, doors, and automotive industries. The uniform thickness and smooth surfaces make float glass relatively strong and resistant to environmental stress and thermal shock.
On the other hand, the rolled glass process involves pouring molten glass onto a metal or graphite table and then rolling it into a sheet using a metal roller. This process allows for the creation of glass with varying thickness and textures but can introduce stress points and inconsistencies that may affect the glass’s overall durability.
Additionally, techniques such as tempering and laminating can further enhance the durability of glass made from either process. Tempered glass is treated with controlled thermal or chemical treatments to increase its strength and make it safer, as it shatters into small, blunt pieces that are less likely to cause injury. Laminated glass, which consists of two or more glass layers bonded with an interlayer, also provides added durability and safety, as the interlayer holds the glass in place even when broken.
Understanding these manufacturing processes helps in choosing the right type of glass for specific applications, ensuring that it not only meets aesthetic requirements but also withstands the demands of its environment. Hence, the process of making the glass is just as important as its chemical composition and the type of glass used when considering its durability.
Chemical Composition
The chemical composition of glass plays a crucial role in determining its durability and suitability for various applications. Different types of glass, such as soda-lime glass, borosilicate glass, and lead glass, all have unique chemical compositions that affect their physical properties and durability.
Soda-lime glass, which is the most common type of glass, is made primarily from silicon dioxide (SiO2), along with sodium oxide (Na2O) from soda ash, and calcium oxide (CaO) from limestone. This type of glass is inexpensive to produce and is commonly used in windows, bottles, and jars. However, it is less resistant to thermal shock and chemical corrosion compared to other types of glass.
Borosilicate glass, on the other hand, contains a significant amount of boron oxide (B2O3) in addition to silicon dioxide and other minor additives. This composition gives borosilicate glass a much higher thermal and chemical resistance, making it ideal for laboratory equipment, cookware, and certain types of lighting fixtures. Due to its durability under extreme conditions, borosilicate glass is often preferred for applications that require a high level of reliability and safety.
Lead glass contains lead oxide (PbO), which increases the glass’s refractive index, making it ideal for optical components such as lenses and prisms, as well as decorative glassware. The presence of lead significantly enhances the glass’s optical properties, but it also requires careful handling and is not suitable for food-related applications due to potential health risks.
In summary, the chemical composition of glass directly affects its durability and the specific applications for which it can be suitably used. Understanding these differences is essential for choosing the right type of glass for specific needs, ensuring both performance and safety are adequately addressed.
Physical Properties
The physical properties of glass play a crucial role in determining its durability. When discussing different types of glass, it is essential to consider how these properties can vary and affect the glass’s performance in various applications. Durability in glass is largely influenced by its physical properties such as hardness, brittleness, and thermal stability.
Firstly, hardness is a significant factor in the durability of glass. Harder glass is more resistant to scratching and abrasion, which is important for items like smartphone screens and eyeglasses. Different types of glass achieve varying levels of hardness through the incorporation of certain chemical elements or through specific manufacturing processes. For example, soda-lime glass is generally less hard compared to borosilicate glass, which contains boron oxide that increases its resistance to thermal shock and improves its hardness.
Brittleness is another physical property that influences glass durability. While glass is generally brittle and can fracture under stress, advancements in materials science have led to the development of more impact-resistant glasses. Techniques such as tempering or laminating help make the glass less prone to shattering. Laminated glass, for instance, includes a layer of plastic between two glass sheets, enhancing its impact resistance and holding it together even when broken.
Thermal stability, or the ability to withstand sudden changes in temperature, is a crucial property for glass used in environments where rapid temperature shifts occur. Thermal stress can cause glass to crack or shatter. Borosilicate glass, due to its low coefficient of thermal expansion, is much more effective at handling thermal stress compared to other types of glass like soda-lime glass. This makes it ideal for applications like laboratory equipment and cookware.
In conclusion, the durability of glass in terms of resisting mechanical and thermal stress is largely dependent on its physical properties. Understanding these properties helps in selecting the right type of glass for specific needs, ensuring both safety and longevity in its everyday use. Whether for architectural applications, daily use objects, or specialized industrial equipment, the physical properties of glass are fundamental to its performance and durability.
Applications and Usage Contexts
The applications and usage contexts of different glass types significantly influence their durability. Glass is not a one-size-fits-all material; its various forms are tailored to meet specific requirements and environments. Understanding how and where a specific type of glass is used can provide insights into its durability and overall performance.
For instance, soda-lime glass is the most common type of glass and is primarily used in windows and bottles. Its widespread use is due to its cost-effectiveness and good enough durability for everyday applications. However, when it comes to environments where higher strength and temperature resistance are required, such as in oven doors or in certain industrial settings, borosilicate glass is preferred due to its superior durability and ability to withstand thermal shocks.
Laminated glass, which includes a layer of plastic between two sheets of glass, offers enhanced safety and durability features. It is often used in car windshields and in buildings where the potential for glass breakage poses a safety risk. The plastic interlayer holds the glass pieces together upon impact, preventing them from shattering and causing harm.
Tempered glass, another highly durable type, is treated through controlled thermal or chemical processes to increase its strength. Its applications include smartphone screens, shower doors, as part and parcel of safety glazing in buildings, and wherever the risk of human impact is high. In the event of breakage, tempered glass crumbles into small, blunt pieces that are less likely to cause injury.
Each glass type is thus tailored to fit its specific usage scenario, with durability being a key consideration influenced by the application. Understanding these applications not only helps in selecting the right type of glass but also in appreciating the advancements in glass technology that cater to varied and increasingly demanding environments.