The manufacturing process of any product often has an impact on the environment, and floating mirrors are no exception. As a crucial component in solar power plants and other industries, these mirrors play a significant role in our transition towards renewable energy. However, it is essential to understand and consider the environmental implications of their production process. This article will delve into the environmental considerations in manufacturing floating mirrors, a topic that holds critical importance in our current age of environmental consciousness.
Our exploration begins with an examination of the materials used in manufacturing floating mirrors and their environmental implications. We will discuss the sourcing of these materials, their lifecycle, and the potential impact each material may have on the environment. As we delve further into the production process, energy consumption becomes a focal point of our discussion. We will consider how much energy is required in the making of these mirrors and its source.
The management of waste and recycling during the production process is another crucial aspect of environmental considerations. It raises questions about the amount of waste produced, how it is handled, and the opportunities for recycling. Similarly, the production process may also lead to carbon emissions and other air quality concerns. We will examine these issues closely, considering how they can be mitigated to reduce harm to the environment.
Lastly, we will focus on water usage during mirror production. As water scarcity becomes an increasingly global concern, understanding the amount of water used in manufacturing processes and its impact on the environment is vital. By exploring these aspects, this article aims to provide a comprehensive understanding of the environmental considerations in the manufacturing of floating mirrors.
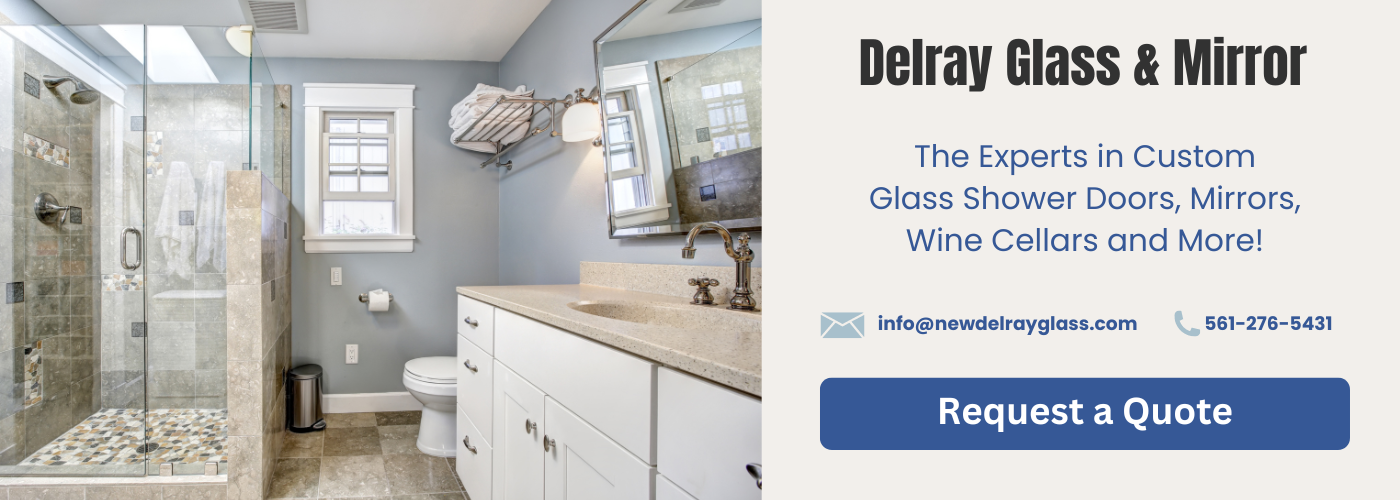
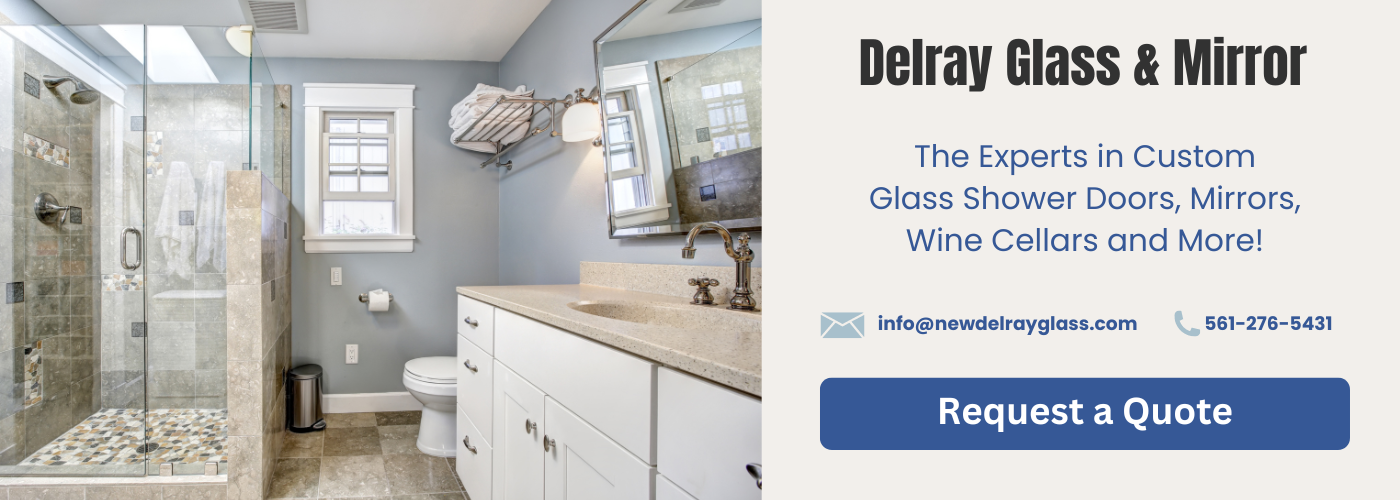
Materials Used in Manufacturing Floating Mirrors and their Environmental Implications
The production of floating mirrors involves the usage of various materials, each of which has a unique set of environmental implications. The primary materials involved in the manufacturing process are glass, metal coatings, and various chemicals. The environmental considerations related to these materials are vast and varied.
Glass is the main component used in the production of floating mirrors. The process to create glass involves the melting of raw materials like silica sand, soda ash, and limestone. These materials are abundant and readily available, but the extraction process can lead to soil erosion and habitat destruction. Furthermore, the energy-intensive nature of glass manufacturing contributes significantly to greenhouse gas emissions.
Metal coatings, usually made of silver or aluminum, are applied to one side of the glass to create the reflective surface of the mirror. Extraction of these metals often leads to detrimental environmental impacts such as deforestation, water pollution, and loss of biodiversity. In addition, the refinement and coating process consume a substantial amount of energy, contributing further to carbon emissions.
Various chemicals are also used in the production of floating mirrors. These include solvents, sealants, and other compounds essential for the manufacturing process. The improper disposal of these chemicals can lead to water and soil contamination.
In conclusion, the materials used in the manufacturing of floating mirrors have significant environmental implications. It is therefore crucial for manufacturers to adopt sustainable practices. This could involve using recycled materials, optimizing energy use, and ensuring proper waste management to minimize the overall environmental impact.
Energy Consumption in the Production Process of Floating Mirrors
The production process of floating mirrors is a complex and resource-intensive procedure. It involves several stages such as melting, refining, shaping and cooling of the glass. All these procedures demand considerable amounts of energy, which is predominantly sourced from non-renewable resources like coal, natural gas, and oil. The utilization of such energy sources contributes significantly to the global carbon footprint, thereby exacerbating the problem of climate change.
One of the primary concerns with the energy consumption in the production of floating mirrors is the melting process. This stage alone accounts for a significant portion of the total energy consumed. The process involves heating the raw materials to temperatures as high as 1500°C to achieve a molten state. This high energy requirement is met mostly through burning fossil fuels, which results in the release of greenhouse gases into the atmosphere.
Moreover, refining and shaping processes are also energy-intensive. They involve reheating the glass to further enhance its purity and to shape it into a mirror. The subsequent cooling process too consumes energy. It’s crucial to control the cooling rate to avoid introducing stress into the glass, which could cause it to weaken or break.
In recent years, there has been a growing interest in developing more energy-efficient methods for the production of floating mirrors. Some manufacturers are exploring the possibility of using renewable energy sources, such as solar or wind power, to offset the environmental impact of the production process. Efforts are also being made to improve the energy efficiency of the manufacturing equipment and processes. Despite these advancements, the energy consumption in the production process of floating mirrors remains a significant environmental consideration.
Waste Management and Recycling during Floating Mirrors Production
Waste management and recycling are critical components of the floating mirrors production process, particularly because of the environmental implications. The manufacturing process of floating mirrors inevitably produces waste materials. These may include off-cuts of glass and metal, as well as chemical wastes from the coating and cleaning processes. Left unmanaged, these wastes can have detrimental effects on the environment.
Proper waste management involves implementing strategies to minimize waste production, safely dispose of unavoidable wastes, and recycle or reuse waste materials where possible. For instance, glass and metal off-cuts can be melted down and reused in the manufacturing process. This not only reduces the amount of raw materials needed, but also decreases the amount of waste sent to landfill, thereby lessening the environmental impact.
In addition to solid wastes, the production of floating mirrors also generates liquid and gaseous wastes. These often contain chemicals used in the cleaning and coating processes, which can be harmful to both the environment and human health if not properly managed. Therefore, waste management strategies in this regard may include treating these wastes to remove harmful substances before disposal or emission, or implementing processes that recover and reuse these chemicals.
Recycling is another important aspect of waste management in the production of floating mirrors. It involves turning waste materials back into useful materials, thereby reducing the need for new raw materials and the amount of waste that ends up in landfill. This can have significant environmental benefits, as the extraction and processing of raw materials often lead to habitat destruction, soil erosion, and pollution of water bodies.
In conclusion, waste management and recycling play a crucial role in minimizing the environmental impact of floating mirror production. By implementing effective waste management strategies and recycling initiatives, manufacturers can significantly reduce their environmental footprint and contribute to sustainable development.
Carbon Emissions and Air Quality Concerns in Floating Mirrors Manufacturing
Carbon emissions and air quality are major environmental considerations in the manufacturing of floating mirrors. The manufacturing process of these mirrors involves several stages, each of which may contribute to the emission of greenhouse gases and other pollutants.
The raw materials used in the production of floating mirrors often include glass, metals, and various chemicals. The extraction, processing, and transportation of these materials can all lead to significant carbon emissions. For instance, the production of glass involves the heating of silica sand to high temperatures, a process that typically relies on the burning of fossil fuels. Similarly, the extraction and processing of metals can also be energy-intensive and result in substantial carbon emissions.
Furthermore, the manufacturing process itself can have a significant impact on air quality. The use of certain chemicals in the production of floating mirrors can result in the emission of volatile organic compounds (VOCs) and other pollutants. These chemicals can be harmful to both the environment and human health.
Despite these potential impacts, there are ways to reduce the carbon emissions and air quality concerns associated with floating mirror manufacturing. These include the use of renewable energy sources in the production process, the recycling of materials, and the implementation of cleaner production techniques. By considering these factors, it is possible to manufacture floating mirrors in a way that minimises their environmental impact.
Water Usage and its Environmental Impact in the Production of Floating Mirrors
Water usage has an essential role in the production of floating mirrors. It’s used in several stages of the manufacturing process. However, the substantial amount of water required in the production process raises important environmental concerns.
One of the main concerns is the depletion of water resources. The manufacturing of floating mirrors is a water-intensive process, which can significantly strain local water supplies, especially in regions that are already experiencing water scarcity. This is an issue that needs to be addressed by manufacturers, who can look into ways of reducing the amount of water used in the production process or implementing water recycling systems.
Another environmental impact of water usage in the production of floating mirrors is water pollution. Waste water from the production process can contain chemicals and other pollutants that, if not properly treated, can harm local aquatic ecosystems. These pollutants can harm the health of aquatic life and can also make the water unsafe for human consumption.
Therefore, it is essential for manufacturers to implement strict waste water treatment protocols to minimize the environmental impact. This can include using filtration systems to remove solid waste, and chemical treatments to neutralize harmful substances.
In conclusion, water usage is a key environmental consideration in the manufacturing of floating mirrors. Manufacturers need to take steps to minimize water usage and ensure that waste water is properly treated, in order to mitigate the environmental impact.