Mirrors are a staple in everyday life, found in everything from bathrooms to art installations. While they play a critical role in both functionality and décor, the production of custom mirrors raises several environmental considerations. As consumers and industries lean towards more sustainable practices, it is crucial to understand the ecological footprint of these reflective objects. This article delves into the environmental impact of custom mirror production, exploring various aspects from the inception of raw materials to the disposal of the final product.
Firstly, the sourcing of raw materials for mirrors, primarily glass and metallic coatings, poses significant environmental challenges. The extraction and processing of these materials can lead to habitat destruction and pollution if not managed responsibly. Secondly, the emissions from the manufacturing process are also a concern, as this involves high energy inputs and can release harmful chemicals into the atmosphere. Thirdly, the overall energy consumption during mirror production is considerable, primarily due to the energy-intensive nature of glass manufacturing and metal coating processes.
Furthermore, waste management is a pivotal issue, as mirror production can generate both solid and chemical waste that may require special handling to mitigate environmental hazards. Lastly, the lifecycle and disposal of mirrors present additional challenges. Mirrors are not biodegradable, and their components can be difficult to recycle, necessitating a closer look at their environmental implications from creation to end of life. By examining these five key environmental considerations, this article aims to shed light on the sustainability challenges of producing custom mirrors and explore potential avenues for improvement.
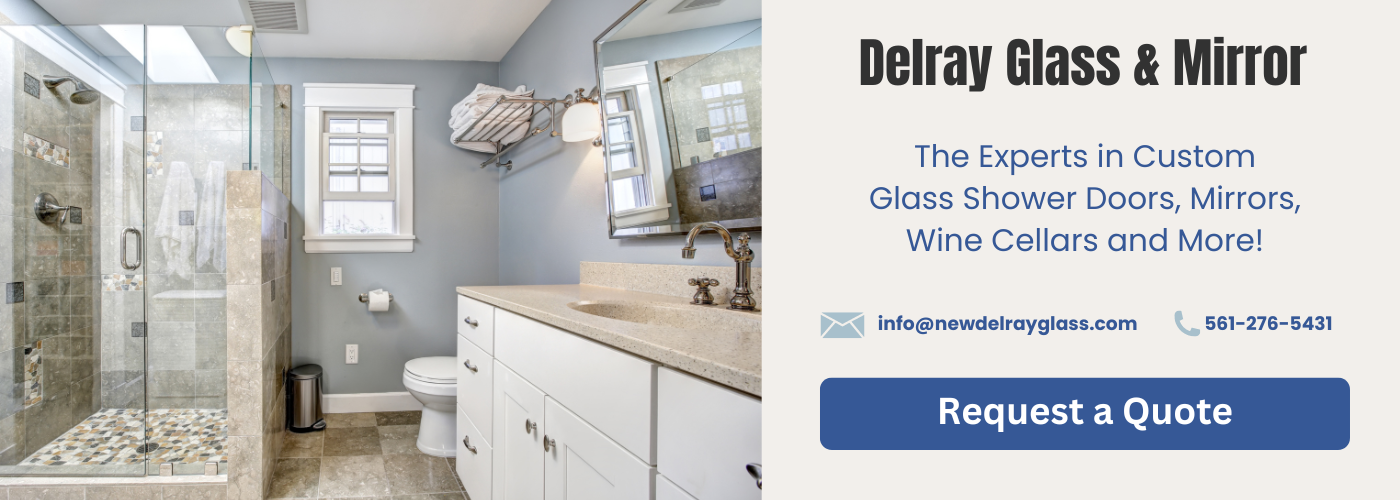
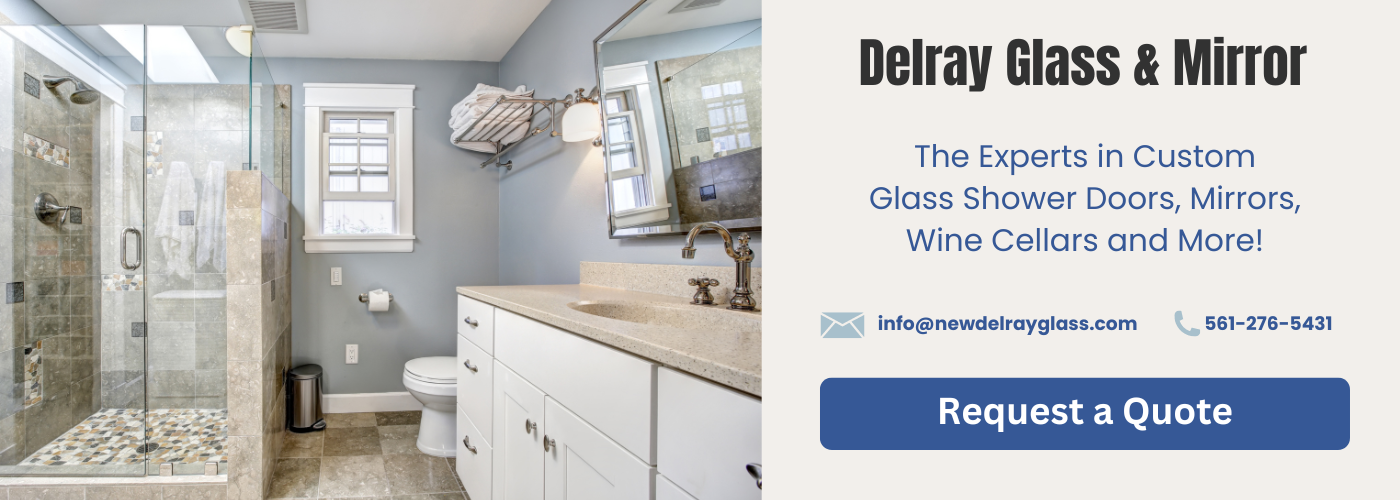
Raw Material Sourcing
Raw material sourcing is a significant environmental consideration in the production of custom mirrors. The process starts with the extraction of silica, the primary component used to make glass, which in itself can be a highly disruptive process to ecosystems. Mining activities can lead to soil erosion, loss of biodiverse habitats, and contamination of water courses with chemicals used in the process.
Moreover, the transportation of these raw materials to manufacturing facilities often involves long distances, typically requiring the use of fossil fuels. This contributes to carbon emissions and thus has a broader impact on global warming and air quality. Additionally, the sourcing of metals like silver or aluminum, which are used to create the reflective surface of mirrors, also poses environmental challenges. These metals are not only limited in supply, posing issues with sustainability, but their extraction can be very energy-intensive and polluting.
Efforts to minimize the environmental impact of raw material sourcing include using recycled materials wherever possible. For instance, using cullet (recycled broken or waste glass) reduces the need for raw silica. This not only helps in conserving natural resources but also reduces energy consumption since recycled glass melts at a lower temperature compared to raw materials. Furthermore, companies can adopt more responsible sourcing practices by ensuring that their materials are obtained in a way that lessens environmental harm and supports local communities.
In conclusion, the environmental considerations associated with raw material sourcing for custom mirrors are complex and multifacetical. Addressing these challenges requires a concerted effort towards more sustainable mining and processing practices, alongside innovations in recycling and material technology to reduce the overall environmental footprint of mirror production.
Manufacturing Process Emissions
The environmental considerations related to the manufacturing process emissions in custom mirror production are significant and multifaceted. During the production of mirrors, various emissions occur that can have detrimental effects on the environment. These emissions primarily consist of volatile organic compounds (VOCs), particulate matter, and other hazardous air pollutants (HAPs). VOCs are released during the application of coatings and during the curing processes, while particulate matter is often emitted during the handling and processing of raw materials and during abrasive activities like cutting and polishing.
One of the major concerns with these emissions is their impact on air quality. VOCs are known to contribute to the formation of ground-level ozone, a key component of smog, which is a serious health and environmental issue. Particulate matter, on the other hand, can cause respiratory issues in humans and can also affect wildlife and vegetation. Both types of pollutants contribute to the broader problem of air pollution, which is linked to various health problems ranging from respiratory disorders to cardiovascular diseases.
Moreover, the environmental impact of these emissions isn’t limited to the air. Chemicals and other pollutants can also find their way into local water systems through runoff and disposal of waste materials, potentially leading to water pollution. This contamination can affect aquatic life and can make water unsafe for drinking and agricultural use.
To mitigate these environmental impacts, mirror manufacturers can adopt cleaner production technologies, improve waste management strategies, and invest in air pollution control equipment. Additionally, regulatory compliance and adherence to environmental standards are crucial in minimizing the negative effects of manufacturing emissions. By implementing such measures, the industry can significantly reduce its environmental footprint and contribute to a more sustainable future.
Energy Consumption
Energy consumption is a significant environmental consideration in the production of custom mirrors. The process of manufacturing mirrors typically involves several energy-intensive steps. Firstly, the production of the glass itself requires melting silica sand along with other minerals at high temperatures, which consumes a substantial amount of energy, usually sourced from non-renewable resources like fossil fuels. Additionally, the application of the reflective coating, which is often aluminum or silver, also requires significant energy input. This coating process often involves vacuum deposition techniques that, while effective in creating high-quality reflective surfaces, are energy-intensive.
Moreover, in facilities where custom mirrors are cut to size and finished, additional energy is used to operate machinery such as glass cutters, polishers, and other finishing equipment. Each of these steps not only consumes electricity but can also lead to the generation of heat, which may require more energy to manage through cooling systems in the factory setting.
The high energy consumption associated with mirror production has several environmental impacts, notably the emission of greenhouse gases if the energy used is derived from fossil fuels. This contributes to climate change and global warming. Additionally, the reliance on non-renewable energy sources depletes these limited resources, urging the need for the mirror manufacturing industry to look towards more sustainable energy solutions such as solar or wind power.
To mitigate these impacts, companies can invest in energy-efficient technologies and machinery. Adopting practices such as using recycled glass for producing new mirrors can also help reduce the energy required for initial material production. Furthermore, implementing rigorous energy management systems and considering the energy source are crucial steps towards reducing the overall environmental footprint of custom mirror production. Encouraging the use of renewable energy in manufacturing processes is another effective strategy to address the environmental concerns associated with energy consumption in mirror production.
Waste Management
Waste management is a crucial environmental consideration in the production of custom mirrors. This process involves the handling and disposal of various types of waste materials generated during the manufacturing process. The production of mirrors typically involves cutting and shaping glass, which generates glass scraps and dust. Additionally, mirrors are coated with metallic and chemical layers to enhance their reflective properties, which can lead to the production of hazardous waste.
Effective waste management strategies are essential to minimize the environmental impact of these waste products. This involves implementing recycling protocols for glass scraps, which can be melted down and reused in the production of new glass products. Furthermore, companies must adhere to strict regulations regarding the disposal of hazardous waste to prevent contamination of soil and water resources.
The implementation of advanced waste treatment technologies also plays a significant role in environmental protection. For instance, using filtration systems can reduce the release of harmful chemicals into the atmosphere during the mirror coating process. Moreover, adopting waste-to-energy technologies can convert non-recyclable waste into energy, thus reducing the reliance on landfills.
By focusing on sustainable waste management practices, mirror manufacturers can not only comply with environmental regulations but also contribute to the conservation of natural resources and the overall reduction of their ecological footprint. This is increasingly important as environmental awareness rises and consumers demand more sustainable products.
Product Lifecycle and Disposal
The environmental considerations surrounding the production of custom mirrors extend far beyond the initial phases of sourcing and manufacturing. A significant aspect to consider is the product lifecycle and disposal of these mirrors. Mirrors are composed of materials such as glass and metal coatings, which can be challenging to recycle and dispose of in an environmentally friendly manner.
During the lifecycle of a custom mirror, the durability and longevity of the product play a crucial role in its environmental impact. Mirrors that are designed for longer use reduce the need for frequent replacements, thereby minimizing the demand for raw materials and reducing waste. However, once these mirrors reach the end of their useful life, the disposal process becomes a critical environmental consideration.
The recycling of mirrors is complicated by the fact that they are often made with a combination of glass and a reflective coating. This reflective coating, typically made from metals like silver or aluminum, can contaminate glass batches during recycling and must be separated, which is a complex and costly process. Currently, many mirrors end up in landfills where they contribute to solid waste accumulation because of the difficulties associated with recycling the composite materials they are made from.
To address these challenges, efforts are being made towards developing more sustainable practices in the disposal of mirrors. This includes advances in recycling technologies that can more efficiently separate and recover the materials. Furthermore, some companies are exploring the use of more sustainable materials in mirror production that are easier to recycle or even biodegradable.
Promoting environmental responsibility in the product lifecycle and disposal stages of custom mirrors is essential for reducing their overall environmental impact. By improving recycling technologies and designing mirrors that are both durable and recyclable, we can mitigate the negative effects associated with their disposal and contribute to a more sustainable future.