Quality control is a critical aspect of any manufacturing process, and the glass sandblasting process is no exception. In this article, we delve into the meticulous steps taken to ensure quality control in glass sandblasting – an intricate process that involves the use of fine grits of sand to create a frosted or etched appearance on glass. This complex procedure requires distinct quality control measures at every stage to guarantee the precision, aesthetics, and durability of the final product.
Initially, we will explore the raw material inspection stage, where the quality of the glass and sand used are thoroughly checked. This step is crucial in ensuring the quality of the end product as the choice of raw materials significantly influences the overall outcome.
Next, we will look into the specific techniques and procedures involved in glass sandblasting. Understanding these techniques is essential to comprehend the quality measures implemented during the process.
Thirdly, we’ll analyze the quality inspection carried out during the sandblasting process. This step ensures that the process is running smoothly and achieving the desired result.
Following that, we’ll discuss the post-sandblasting quality checks and inspection, which is vital to ensure that the finalized product meets the expected quality standards.
Finally, we’ll delve into the maintenance and calibration of sandblasting equipment, an often overlooked but crucial aspect of the process. Regular maintenance and calibration of equipment contribute significantly to the consistent production of high-quality glass sandblasting products.
Join us as we delve into each of these stages in detail, examining the intricate process behind the creation of beautiful, high-quality sandblasted glass.
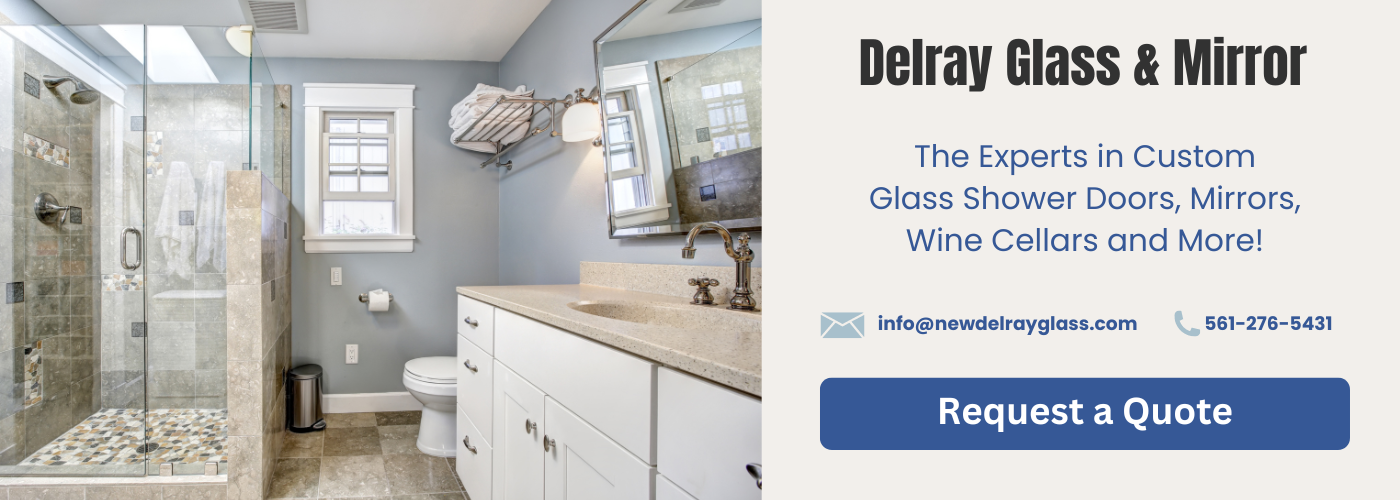
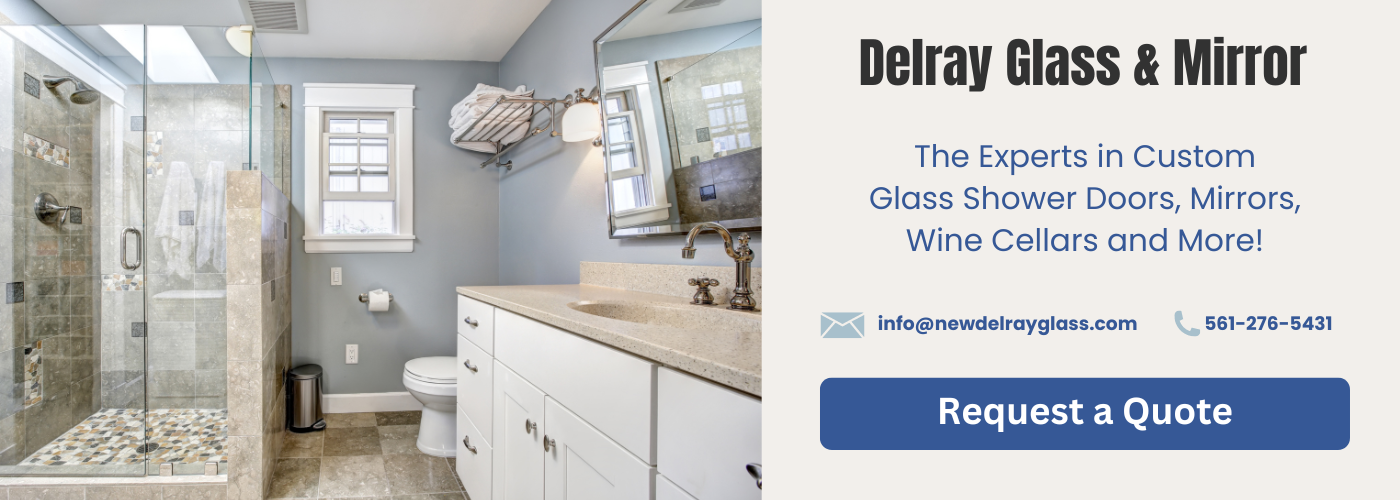
Raw Material Inspection in Glass Sandblasting
The first step in the quality control process of glass sandblasting is the raw material inspection. This step is crucial to ensure that the quality of the final product is not compromised. It involves inspecting the raw materials used in the sandblasting process, which primarily includes the glass and the abrasive materials.
The glass to be sandblasted must be thoroughly inspected for any imperfections such as cracks, chips, or scratches. Using a glass piece with such imperfections could lead to breakage during the sandblasting process or result in a final product that is not up to the desired standard. The glass should also be of the correct thickness and dimensions as per the requirements of the end product.
The abrasive material, often sand or other specialized grit, is also inspected for quality. It is essential to ensure that the abrasive material is of the right coarseness or fineness. If the abrasive material is too coarse, it may cause excessive scratching on the glass surface instead of providing a smooth, frosted effect. On the other hand, if it is too fine, it may not produce the desired effect at all.
Thus, the raw material inspection step is crucial in the quality control steps of glass sandblasting. It sets the foundation for the rest of the process, and any issues or inconsistencies identified at this stage can be addressed before moving forward, saving both time and resources.
Specific Techniques and Procedures in Glass Sandblasting
Specific Techniques and Procedures in Glass Sandblasting refer to the methodologies employed in the sandblasting process to ensure the quality and aesthetic value of the glass products. These techniques are pivotal in ensuring that the glass items produced are of the highest quality and meet the desired specifications.
To begin with, the type of abrasive used in the sandblasting process matters a lot. The choice of abrasive material varies depending on the desired finish and the nature of the glass. For instance, smaller and lighter abrasive materials such as crushed glass or aluminum oxide are used for delicate glass materials to achieve fine detail without causing damage. On the other hand, larger and stronger abrasives like silicon carbide are used for tougher glass materials.
The force applied during the sandblasting process is also a key consideration. The pressure needs to be sufficient to remove the desired layer of glass, but not too high to avoid causing damage to the glass item. This requires a highly skilled operator who understands how to accurately adjust and control the sandblasting equipment.
Moreover, the angle at which the abrasive is applied to the glass surface also plays a significant role in the quality of the final product. A direct angle results in a deeper and coarser texture, while a lesser angle gives a lighter and smoother texture.
Lastly, the duration of the sandblasting process is also critical. Overblasting can lead to unnecessary damage to the glass surface, while under blasting may result in incomplete removal of the glass layer. Therefore, timing is essential to achieve the desired results.
In conclusion, the specific techniques and procedures in glass sandblasting are crucial in the quality control steps of the process. They help ensure that the final glass product is of high quality and meets the desired specifications.
Quality Inspection during the Sandblasting Process
Quality Inspection during the Sandblasting Process is an integral subtopic when discussing the quality control steps in the glass sandblasting process. This process is pivotal because it serves as the real-time check that ensures that the sandblasting is progressing as planned and that the quality standards are being met.
During the sandblasting process, the glass is inspected at various stages to ensure that the abrasive material is effectively removing the surface layers without causing any damage to the glass. This process requires meticulous attention to detail because the pressure and the type of abrasive material used can significantly affect the final outcome.
It’s also during this stage that any irregularities or deviations from the expected results are identified. If any faults are discovered, adjustments can be made immediately to correct the issue. This could involve adjusting the pressure of the sandblasting, changing the type of abrasive material used, or even stopping the process altogether if the glass is at risk of being damaged.
In essence, Quality Inspection during the Sandblasting Process plays a crucial role in ensuring the final product’s quality and integrity. It allows for immediate corrective actions and adjustments, ensuring that the final product is of the highest possible quality. This process, therefore, not only guarantees the aesthetic appeal of the glass but also its durability and longevity.
Post-Sandblasting Quality Checks and Inspection
Post-sandblasting quality checks and inspections are a critical part of the glass sandblasting process. This stage ensures that the final product has met all the desired specifications and standards. It is at this point that any defects, inconsistencies, or deviations from the original design are identified and corrected if possible.
In the post-sandblasting quality check, each piece of glass is meticulously examined. The inspection process involves checking the surface finish, ensuring that the sandblasting has been evenly applied and that there are no areas of over or under-sanding. The glass is also inspected for any traces of damage, such as chips or cracks that may have occurred during the sandblasting process.
The post-sandblasting inspection also checks for conformity to the original design specs. Any deviations, whether in thickness, shape, or pattern, are noted. When discrepancies are found, the glass product may be reworked, or in extreme cases, rejected and replaced with a new piece.
The post-sandblasting process is essentially a quality assurance step. It ensures that the final product adheres to the highest standards of quality and meets the expectations of the customer. It is a crucial step in ensuring the integrity and quality of the finished product.
In conclusion, post-sandblasting quality checks and inspections are a vital part of the glass sandblasting process. They ensure that the final product is of the highest quality, free from defects, and accurately reflects the original design specifications.
Maintenance and Calibration of Sandblasting Equipment
Maintenance and Calibration of Sandblasting Equipment is a critical step in the quality control process of glass sandblasting. It is an essential subtopic that deserves attention when discussing the quality control steps in the glass sandblasting process. This phase is responsible for ensuring the overall integrity of the sandblasting process.
Maintenance of sandblasting equipment involves a regular and systematic check of the machines and tools used in the process. This includes, but is not limited to, the regular cleaning of the equipment, replacement of worn-out parts, lubrication of moving parts, and the general upkeep of the machines. Regular maintenance helps to prolong the life of the equipment, prevent unexpected breakdowns, and ensure the efficiency and effectiveness of the sandblasting process.
On the other hand, calibration of the sandblasting equipment ensures that the machines are working at their optimal levels and providing accurate results. During calibration, the output of the equipment is compared against a standard to ensure its accuracy. If any discrepancies are found, adjustments are made to bring the equipment back to its optimal performance. Calibration ensures that the sandblasting process is consistent and reliable, leading to high-quality outputs.
In conclusion, Maintenance and Calibration of Sandblasting Equipment is an essential step in the quality control process of glass sandblasting. It not only ensures the efficiency and effectiveness of the process but also ensures the production of high-quality glass products.