In the world of decorative and industrial glass processing, sandblasting is a widely used technique. But what are the thickness specifications for sandblasting glass? This is a question often asked, but seldom addressed in detail. This article will delve into the heart of this matter, shedding light on the intricacies of the sandblasting process, specifically focusing on the critical aspect of glass thickness.
The first section will provide an overview of the sandblasting process, explaining how it works and why it’s used. We’ll then delve into the importance of thickness in sandblasting glass, emphasizing why getting the thickness right is so crucial for achieving the desired results.
Next, we’ll detail the standard thickness specifications for sandblasting glass, which will provide a benchmark for anyone involved in this process. We’ll also explore the factors that can influence these thickness specifications. This includes both inherent properties of the glass and external conditions such as the type of sandblasting equipment used.
Finally, the implications of incorrect thickness in sandblasting glass will be expounded upon, discussing the potential adverse effects and how they can be avoided. This comprehensive analysis will provide a deeper understanding of the complexities involved in the sandblasting process, and highlight the importance of adhering to the right thickness specifications.
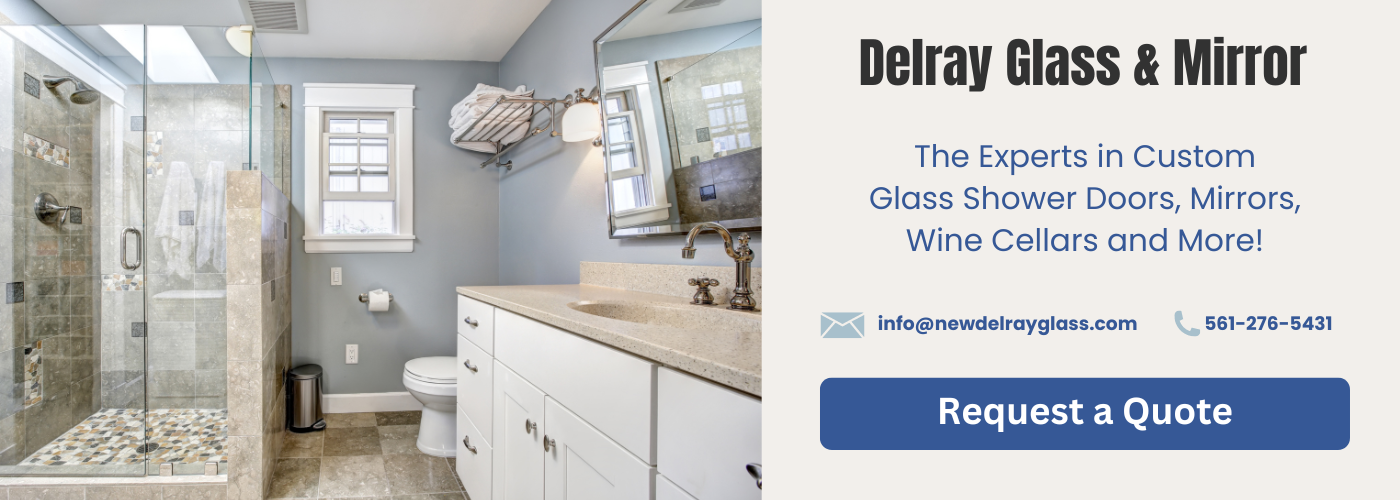
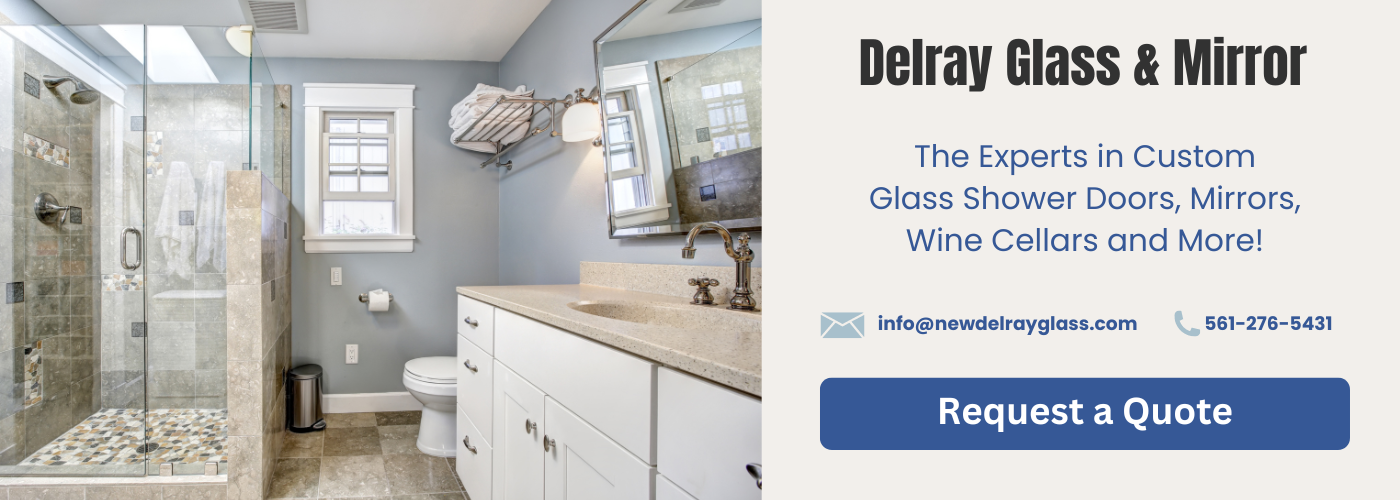
Overview of Sandblasting Glass Process
The sandblasting glass process, also known as abrasive blasting, is a powerful technique used to clean or etch the surface of a glass object. This process involves propelling a stream of abrasive material, such as sand, against the glass surface under high pressure. The end result is a satin finish on the glass, which can be used to create a variety of artistic designs or to prepare the glass surface for other treatments.
The technique has a wide range of applications in both the industrial and artistic domains. In the industrial sector, sandblasting is used to clean large surfaces, remove rust and other impurities, and prepare surfaces for painting or other types of coating. In the artistic world, sandblasting is used to create intricate designs on glass, transforming ordinary pieces into beautiful works of art.
The process of sandblasting glass involves a few key steps. Firstly, the design to be etched onto the glass is created, either manually or using computer software. This design is then turned into a stencil, which is applied to the surface of the glass. The areas of the glass that are not covered by the stencil will be blasted by the abrasive material, creating the desired design.
In terms of equipment, a sandblasting system typically consists of a pressure generator, an abrasive container, a blasting nozzle, and a work enclosure to contain the released abrasive material. Safety equipment, such as protective clothing and goggles, is also essential due to the potentially hazardous nature of the process.
Understanding the process of sandblasting glass is the first step towards mastering the art and science of this fascinating technique. With the right knowledge, tools, and skills, sandblasting can be used to create a wide range of stunning effects on glass, from simple frosted finishes to intricate, multi-layered designs.
Importance of Thickness in Sandblasting Glass
The importance of thickness in sandblasting glass cannot be overstated. The thickness of the glass being sandblasted plays a pivotal role in determining the outcome of the process. Essentially, it is a key factor that significantly influences the quality, durability, and overall aesthetic appeal of the final product.
In the sandblasting process, the glass is subjected to a high-pressure jet of grit, which can either be sand, aluminum oxide, or glass beads. The abrasive material etches the surface of the glass, creating a frosted, textured appearance. The thickness of the glass affects how the glass responds to this process. Too thin, and the glass may chip, crack, or even shatter under the force of the blasting. On the other hand, if the glass is too thick, it may not achieve the desired level of etching.
Furthermore, the thickness of the glass also has an impact on the level of detail that can be achieved in the design. Thinner glass allows for finer detail, but at the risk of damage to the glass. Thicker glass, while more robust, may not be able to capture the intricacies of a highly detailed design.
Therefore, understanding the importance of glass thickness in sandblasting is crucial for achieving optimal results. It affects not only the aesthetic outcome but also the structural integrity and durability of the final product. Consequently, careful consideration and accurate measurement of glass thickness are essential steps in the sandblasting process.
Standard Thickness Specifications for Sandblasting Glass
Standard thickness specifications for sandblasting glass are critical aspects to consider when embarking on any sandblasting project. These specifications play a vital role in determining the outcome of the sandblasting process, impacting both the aesthetic and functional properties of the glass.
Sandblasting involves directing a high-pressure stream of abrasive material (in this case, sand) at the glass surface. The standard thickness of the glass to be sandblasted typically ranges from 3mm to 19mm. However, the thickness can vary depending on the specific requirements of the project.
The thickness of the glass determines the degree of opacity achieved through the sandblasting process. Thinner glass tends to produce a more translucent finish, while thicker glass results in a more opaque appearance. It’s important to note that the sandblasting process does not alter the structural integrity of the glass, regardless of its thickness.
It is also crucial to remember that the thickness specifications can influence the choice of sandblasting equipment and technique. For instance, thicker glass may require a more powerful sandblasting machine and a higher concentration of abrasive material.
In conclusion, understanding the standard thickness specifications for sandblasting glass is critical to achieving the desired results. This knowledge allows for proper planning and execution of the sandblasting process, ensuring a successful project outcome.
Factors Influencing Thickness Specifications for Sandblasting Glass
The factors influencing thickness specifications for sandblasting glass are numerous and varied. These factors play a crucial role in determining the final quality of the sandblasted glass, and hence, it is essential to understand and consider them during the sandblasting process.
One of the principal factors is the intended use of the glass. Different applications require different thicknesses. For example, glass used in architectural applications such as windows or doors may require a different thickness compared to glass used in decorative pieces. The more robust the expected usage, the thicker the glass that may be needed.
The type of glass being used is another significant factor. Different glass types have different properties and thus require different thicknesses when sandblasting. Some glasses are more susceptible to breakage or damage during the sandblasting process and might need a more considerable thickness.
Another factor to consider is the desired visual effect. The thickness of the glass can significantly affect how the final product looks. A thicker glass can result in a more opaque and less translucent finish, while a thinner glass might yield a more translucent finish.
The sandblasting equipment used, including the type of abrasive material, the pressure applied, and the blasting duration, also play a role in determining the thickness specifications. Different equipment settings can lead to different results, and hence, the right configuration needs to be determined based on the specific requirements of each project.
In conclusion, the thickness specifications for sandblasting glass are influenced by a multitude of factors. Understanding these factors is critical to achieving the desired quality and finish in the final product.
Implications of Incorrect Thickness in Sandblasting Glass
The implications of incorrect thickness in sandblasting glass are substantial and can affect both the aesthetics and durability of the finished product. Glass sandblasting is a sophisticated process that demands precision, and the thickness of the glass plays a crucial role in achieving the desired results. When the thickness is not within the acceptable specifications, it can lead to a variety of problems.
Firstly, if the glass is too thin, it may not withstand the pressure of the sandblasting process, leading to breakage or damage. This is not only a waste of materials but can also pose safety risks. On the other hand, if the glass is excessively thick, it may not achieve the desired level of etching or may require more abrasive material and time than necessary, leading to increased costs.
Secondly, the thickness of the glass can also impact the final appearance of the design. Too thin glass may result in an uneven or shallow etching, while too thick glass could lead to an overly deep etching that may distort the design. Both scenarios can lead to unsatisfactory results that do not meet the client’s expectations.
Moreover, incorrect thickness can also affect the longevity of the glass product. Glass that is too thin may be more prone to cracking or chipping in the long run, especially if it is exposed to stress or changes in temperature. Conversely, overly thick glass may be too heavy for certain applications, potentially leading to structural issues.
In conclusion, maintaining the correct thickness in sandblasting glass is vital for ensuring the quality, safety, and longevity of the final product. It requires careful planning, accurate measurements, and meticulous execution to ensure that the thickness specifications are met.