In the realm of safety glass, two types commonly stand out: tempered and laminated safety glass. Both of these have unique properties that make them ideal for specific applications, and while they may seem similar, they are inherently different. This article will delve into the world of tempered safety glass and laminated safety glass, exploring their definitions, manufacturing processes, properties, applications, and key differences.
The first section will focus on tempered safety glass, explaining what it is and how it is manufactured. We will then move on to highlight its unique properties and the applications that benefit from these characteristics. The third section will turn the spotlight to laminated safety glass, detailing its definition and manufacturing process, followed by an exploration of its properties and the applications that find it most useful. Lastly, we will put these two types of safety glass side by side, elucidating the key differences that distinguish them from each other.
Whether you are in the construction industry, automotive world, or simply a curious individual, this article will provide valuable insights into tempered and laminated safety glass, helping you understand their roles and importance in our daily lives.
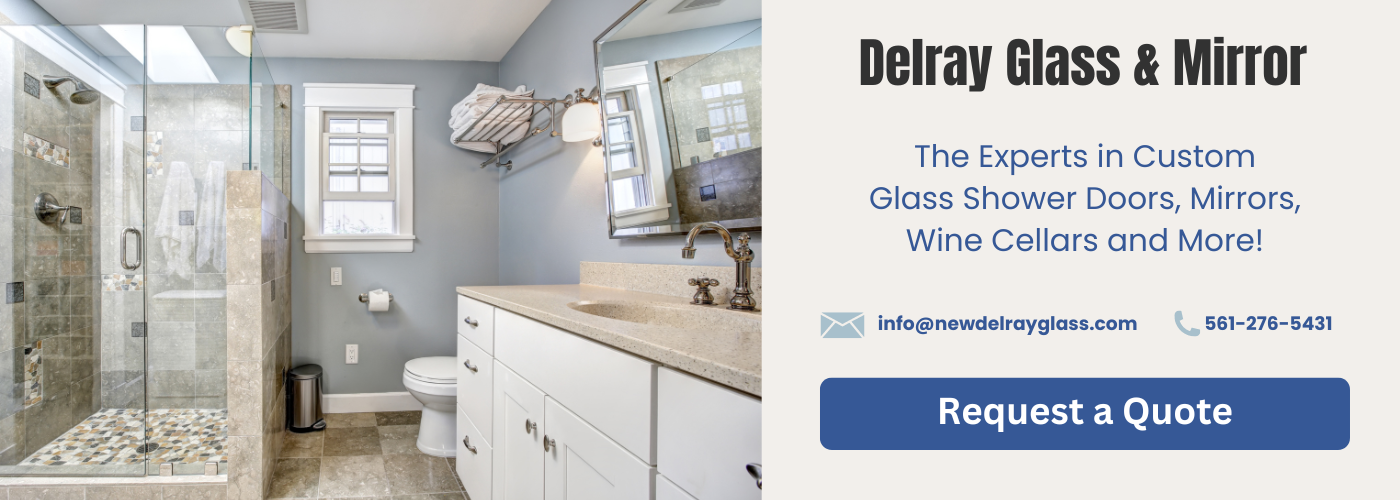
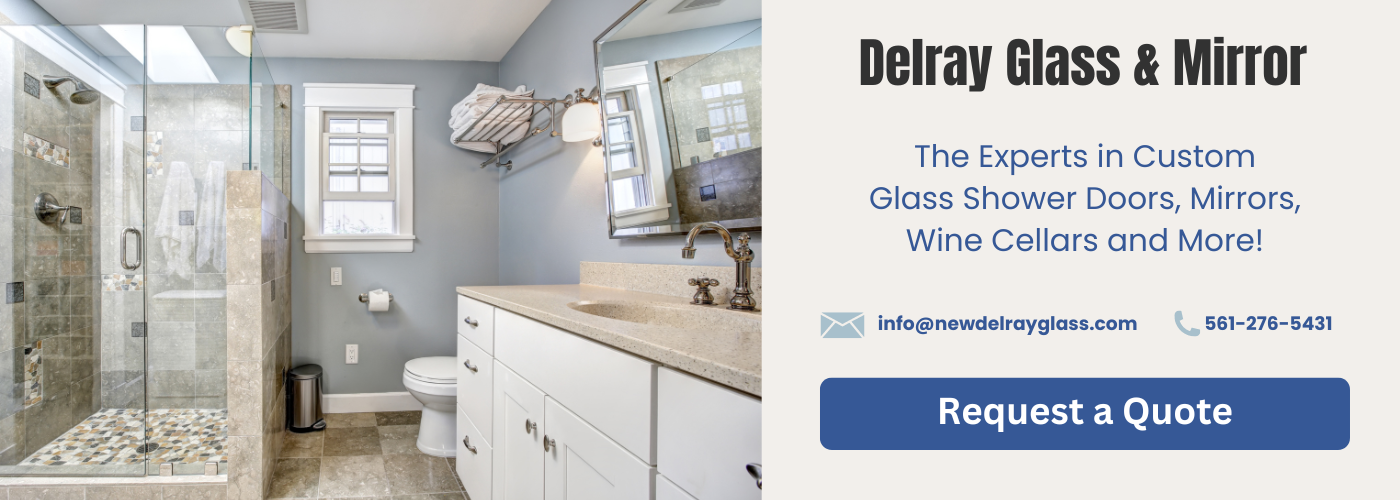
Definition and Manufacturing Process of Tempered Safety Glass
Tempered safety glass, also known as toughened glass, is a type of safety glass that has been processed by controlled thermal or chemical treatments to enhance its strength. The tempering process involves heating the glass to a high temperature and then rapidly cooling it. This process puts the outer surfaces of the glass into compression and the interior into tension, which results in a glass that is stronger and more resistant to breakage.
When tempered safety glass does break, it shatters into small, granular pieces instead of sharp shards, reducing the potential for injury. This is a key aspect that distinguishes it from normal, annealed glass and makes it a preferred choice for applications such as car windows, shower doors, architectural glass doors and tables, refrigerator trays, and mobile screen protectors among others.
The manufacturing process of tempered safety glass involves several stages. Initially, the glass is cut to the desired size and shape. Then, it is heated to a very high temperature in a tempering furnace, usually around 620 degrees Celsius. Following the heating process, the glass is rapidly cooled, or quenched, by a blast of air uniformly across its surface. This rapid cooling causes the outer surfaces of the glass to cool and solidify faster than the center, putting the surfaces into compression and the interior into tension.
This process gives tempered safety glass its unique properties and makes it significantly different from laminated safety glass which involves bonding two or more layers of glass together with an interlayer of plastic or resin to enhance its impact resistance.
Properties and Applications of Tempered Safety Glass
The properties of tempered safety glass make it a popular choice in various applications. This type of safety glass is up to five times stronger than ordinary glass, thanks to the rapid heating and cooling process it undergoes during production. The tempering process alters the structure of the glass, making it more resilient to impact, heat, and pressure. When it does break, it shatters into small, dull pieces instead of large, sharp shards, reducing the risk of injury.
Tempered safety glass is commonly used in applications that require strength and safety. You’ll find it in automobile windows, shower doors, and sliding doors, to name a few. It’s also used in buildings for its increased strength and safety features, particularly in areas that are prone to high winds, heavy snow loads, or seismic activity. In consumer electronics, tempered glass is often used as a screen protector for mobile phones and tablets, offering a high degree of scratch and impact resistance.
In summary, the properties of tempered safety glass – its strength, safety, and resistance to heat and pressure – make it an ideal material for use in a wide range of applications. Its ability to shatter into small, harmless pieces upon breaking further enhances its safety profile, making it a preferred choice in environments where the risk of injury from broken glass is a concern.
Definition and Manufacturing Process of Laminated Safety Glass
Laminated safety glass is a type of safety glass that holds together when shattered. In the event of breaking, it is held in place by an interlayer, typically of polyvinic butyral (PVB), between its two or more layers of glass. The interlayer keeps the layers of glass bonded even when broken, and its high strength prevents the glass from breaking up into large sharp pieces. This produces a characteristic “spider web” cracking pattern when the impact is not enough to completely pierce the glass.
The manufacturing process of laminated safety glass involves sandwiching a layer of PVB or another type of interlayer between two layers of glass. This assembly is then passed through a series of rollers to remove any air bubbles and ensure a perfect bond. The resulting sandwich is then heated in an autoclave under pressure to complete the bonding process and ensure that the glass and interlayer are perfectly sealed together.
Laminated safety glass is commonly used in situations where it’s important that the glass, if broken, remains in place. It’s widely applied in automotive windshields and in architectural applications where it’s necessary to prevent shards of glass falling or flying out, like skylights, high-rise buildings, and glass facades. It’s also used in burglary-resistant and bullet-resistant glass applications.
In summary, the laminated safety glass, with its special manufacturing process and properties, provides a critical safety feature in many applications where glass breakage could have severe consequences. It’s different from tempered safety glass, which is also a safety glass, but instead of having an interlayer, tempered glass is made by heat-treating normal glass to increase its strength.
Properties and Applications of Laminated Safety Glass
Laminated safety glass, also known as sandwich glass, is a type of safety glass that holds together when shattered. Its properties are mainly derived from the integration of a plastic interlayer, usually polyvinyl butyral (PVB), between two or more layers of glass. The interlayer keeps the layers of glass bonded even when broken, and its high strength prevents the glass from breaking up into large sharp pieces. This produces a characteristic “spider web” cracking pattern when the impact is not enough to completely pierce the glass.
Laminated safety glass is used in various applications where safety, security, and damage resistance are paramount. For instance, it is used in automobile windshields for its excellent resistance to impact and penetration. The laminated structure prevents shards from flying in case of an accident, protecting the occupants. Additionally, it is used in building windows, patio doors, glass floors and stairs, and even in bulletproof glass, owing to its high-strength and impact-resistance properties.
The properties of laminated safety glass can be customized by altering the number and thickness of the layers used, making it a versatile choice for many applications. It also offers sound insulation and blocks 99% of incoming UV radiation, making it an excellent choice for commercial and residential buildings.
In comparison to tempered safety glass, laminated glass tends to be more durable and provides better security features. While both types of glasses are made to be safer than regular glass, the choice between the two often depends on the specific needs of the application.
Key Differences between Tempered and Laminated Safety Glass
Tempered and laminated safety glasses are two different types of safety glasses, each with their unique characteristics and uses. The key differences between the two mainly lie in their manufacturing process, strength, and how they break.
Tempered safety glass, also known as toughened glass, undergoes a heat treatment process to increase its strength. This process involves heating the glass to a high temperature and then rapidly cooling it. The result is a glass that is four to five times stronger than regular glass. When tempered glass breaks, it shatters into small, blunt pieces, reducing the risk of injury.
On the other hand, laminated safety glass is made by bonding two or more layers of glass together with an interlayer of plastic, usually polyvinyl butyral (PVB). This interlayer holds the glass together when it breaks, preventing it from shattering into large, sharp pieces. This makes laminated glass safer to handle when broken, and also provides a certain level of security as it is harder to penetrate.
While both types of safety glasses are designed to reduce the risk of injury, they are used in different applications. Tempered glass is commonly used in areas where thermal resistance is required, such as in oven doors and fireplace screens. Laminated glass, on the other hand, is often used in car windshields and in buildings where security is a concern.
In summary, the key differences between tempered and laminated safety glass are their manufacturing process, how they break, and their typical applications. Understanding these differences can help one make an informed decision when choosing the right type of safety glass for a specific application.