In the world of interior design and decoration, custom-made pieces play a significant role in adding a unique touch to your space. One such popular custom item is a beveled mirror. However, when it comes to ordering these bespoke pieces, one common question often arises- What is the lead time for ordering a custom beveled mirror? This article aims to shed light on this question and provide you with comprehensive information on the subject.
Firstly, we’ll delve into understanding the concept of lead time in custom orders, which is a crucial aspect in the world of bespoke items. Being aware of how long it might take to get your custom mirror can help you plan your interior design project more efficiently. We’ll then move on to explore the process of creating a custom beveled mirror. Understanding what goes into the creation of your mirror may provide insight into why the lead time can be longer than for standard items.
Next, we will discuss the various factors affecting the lead time for custom beveled mirrors. These can range from the complexity of the design, the availability of materials, to the proficiency of the artisans creating your mirror. This information is essential for setting realistic expectations for delivery times.
We will also look at the average lead time for custom beveled mirrors, based on industry standards and various manufacturers’ timelines. This can give you a rough idea of the waiting period involved in ordering such a mirror.
Lastly, we’ll provide some practical tips on how to reduce the lead time for custom beveled mirror orders. Whether it’s through careful planning, flexible design choices, or working closely with the manufacturer, there are ways to get your mirror quicker.
Through this article, we aim to equip you with the knowledge you need when ordering a custom beveled mirror, ensuring that you are well-prepared for the wait that comes with creating a personalised piece of art.
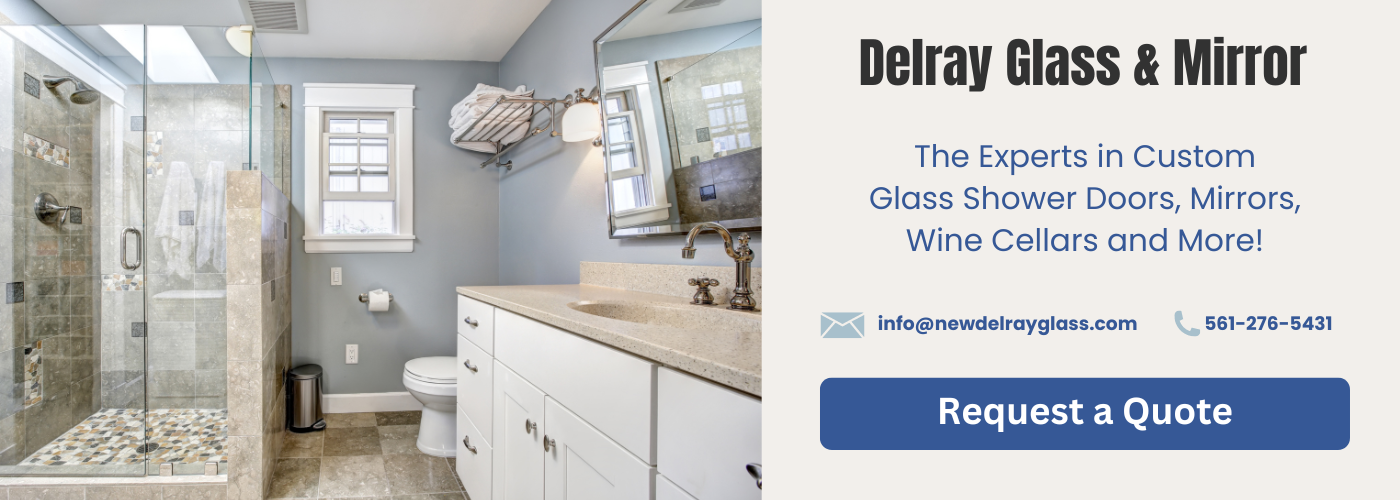
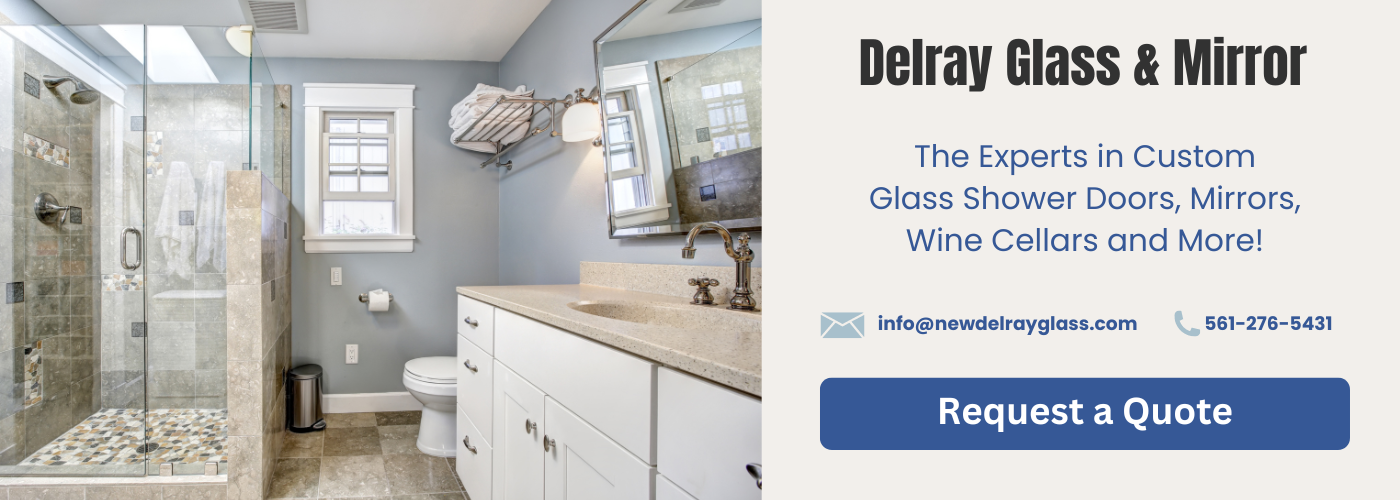
Understanding the Concept of Lead Time in Custom Orders
The concept of lead time in custom orders is a vital aspect to understand, especially when it comes to ordering a custom beveled mirror. In terms of ordering and manufacturing, lead time refers to the period from the initiation of the process, such as placing an order, to its completion, which is the delivery of the finished product. Lead times can vary significantly depending on a variety of factors, including the complexity of the product, raw materials availability, production capacity, and the efficiency of the manufacturing process.
In the context of custom beveled mirrors, understanding the lead time is crucial because these items are not mass-produced and kept in stock, but rather created to individual specifications. This implies that the mirror has to be designed, the glass cut to size, the edges beveled, and any additional features added. This process takes a certain amount of time, which is the lead time.
The lead time can also be influenced by other factors such as the current workload of the manufacturer, the availability of the necessary materials, and whether the design requires any special or unusual features. Therefore, it is essential to understand the concept of lead time in custom orders to set realistic expectations about when the finished product will be delivered.
The Process of Creating a Custom Beveled Mirror
Creating a custom beveled mirror is a delicate and intricate process that involves a series of steps. It begins with the selection of the right glass material. This choice often depends on the required size, shape, and style of the mirror. High-quality glass is typically used to ensure the best reflection and longevity.
The next step involves cutting the glass into the desired shape and size. This process is usually carried out using advanced machinery to ensure precision and avoid any defects or imperfections. Once the glass is cut, it is then beveled. Beveling is a glass cutting process where the edges of the mirror are cut and polished to a certain angle to give it a decorative look. The beveled edge can vary in size, typically ranging from 1/2 inch to 1 3/4 inches.
After beveling, the mirror is cleaned thoroughly to remove any dust or residues from the cutting process. It is then coated with a silvering solution on one side to create the reflective surface. The silvering process involves several stages, including the application of multiple coats of the silver solution, drying, and finally sealing to prevent tarnishing.
The last stage in the creation of a custom beveled mirror is the quality check. This involves inspecting the mirror for any defects, ensuring the size and shape are correct, and checking the bevel and silvering for consistency and quality.
Throughout this process, every detail matters, and each step must be performed meticulously. This comprehensive process ensures that every custom beveled mirror meets the highest standards of quality and craftsmanship.
Factors Affecting the Lead Time for Custom Beveled Mirrors
The lead time for custom beveled mirrors can be affected by a variety of factors. One of the most significant of these is the complexity of the mirror design. The more intricate and complex the design, the longer it will take to create the mirror. This is because each detail needs to be painstakingly etched onto the mirror’s surface, which can be a time-consuming process.
Another factor that can affect the lead time is the size of the mirror. Larger mirrors take longer to create due to the increased amount of material that needs to be cut and shaped. Moreover, more time is also required for the polishing and beveling process for larger mirrors, contributing to a longer lead time.
The availability of materials can also impact the lead time. If the specific type of glass or other materials required for the custom beveled mirror are not readily available, it may take additional time to source these materials. This can further extend the lead time.
Lastly, the workload of the craftsmen also plays a role. If they are dealing with multiple orders at the same time, it might take longer for them to complete your custom mirror.
In conclusion, the lead time for custom beveled mirrors is influenced by several factors such as the complexity of the design, the size of the mirror, the availability of materials, and the current workload of the craftsmen. Understanding these factors can help customers to have realistic expectations regarding the lead time of their custom mirror orders.
Average Lead Time for Custom Beveled Mirrors
The average lead time for custom beveled mirrors depends on several factors, including the complexity of the design, the size of the mirror, and the manufacturer’s workload at the time of the order. However, on average, it can take anywhere from a few days to several weeks to complete a custom beveled mirror order.
This process begins with the customer providing a detailed description or design of the custom mirror they want. Once the design is finalized, the manufacturer can then begin the process of creating the mirror. This involves cutting the glass to the desired size and shape, beveling the edges, and adding any additional design elements the customer has requested.
The average lead time can be impacted by several factors. For instance, more complex designs will naturally take longer to complete than simpler ones. Similarly, larger mirrors will take more time to produce than smaller ones due to the additional materials and labor required. Additionally, if the manufacturer has a high volume of orders at the time, this could also extend the lead time.
Despite these potential delays, most manufacturers strive to complete custom orders as quickly as possible to satisfy their customers. They understand that lead time is a crucial factor in the customer’s decision-making process and therefore do everything they can to minimize it. However, customers should also be aware that quality work takes time, and rushing the process could result in a less than perfect final product. Therefore, it is always a good idea to plan ahead and order well in advance of when the mirror is needed.
How to Reduce Lead Time for Custom Beveled Mirror Orders
Reducing lead time for custom beveled mirror orders is a critical aspect for both businesses and individual customers. This is primarily because shorter lead times translate to faster delivery, which not only meets customer needs in a timely manner, but can also provide a competitive advantage for businesses in the mirror industry.
There are several strategies to reduce the lead time for custom beveled mirror orders. First, improving the efficiency of the production process can significantly shorten the lead time. This can be achieved by streamlining operations, using advanced technologies, or even simply organizing the work space more effectively to reduce unnecessary movements and tasks.
Secondly, maintaining a good relationship with suppliers is also crucial. Suppliers who are reliable and prompt in their delivery can drastically reduce waiting times for materials, consequently reducing the overall lead time. In addition, placing orders well in advance and maintaining an adequate inventory of raw materials can also aid in minimizing delays.
Finally, effective communication with customers is key. By understanding their needs and expectations, businesses can better plan their production schedule and reduce lead times accordingly. Also, keeping customers informed about the status of their order at all times can help avoid dissatisfaction caused by unexpected delays.
In conclusion, reducing lead time for custom beveled mirror orders involves enhancing efficiency, managing supplier relationships, and maintaining clear communication with customers. Implementing these strategies can result in faster delivery times and higher customer satisfaction.