As everyone knows, customization is a meticulous process that demands time, precision, and expertise, especially when it comes to products as delicate as glass shelves. The question often posed by many customers is, “What is the lead time for ordering custom glass shelves?” This article aims to provide a comprehensive answer to that query.
Firstly, we will delve into understanding the concept of lead time in customized production. This will provide a clear picture of what lead time entails and why it is a crucial aspect of any manufacturing process. Next, we will explore the factors that influence the lead time for custom glass shelves. These may range from the complexity of the design to the availability of raw materials, among others.
The third section will illuminate the process of ordering and manufacturing custom glass shelves, offering an insider’s view into the steps that contribute to the final product. This will help customers appreciate the intricacy involved in crafting their custom shelves and why it might take a certain amount of time.
In the fourth segment, we will provide an estimation of the approximate lead time for custom glass shelves. Though this can vary based on numerous factors, a rough timeline can assist in setting realistic expectations. Finally, we will discuss various strategies that can be employed to reduce lead time in custom glass shelf production without compromising on the quality of the final product.
By the end of this article, customers will have a better understanding of the timeline involved in ordering their custom glass shelves, and producers will have insights into managing and potentially reducing lead time.
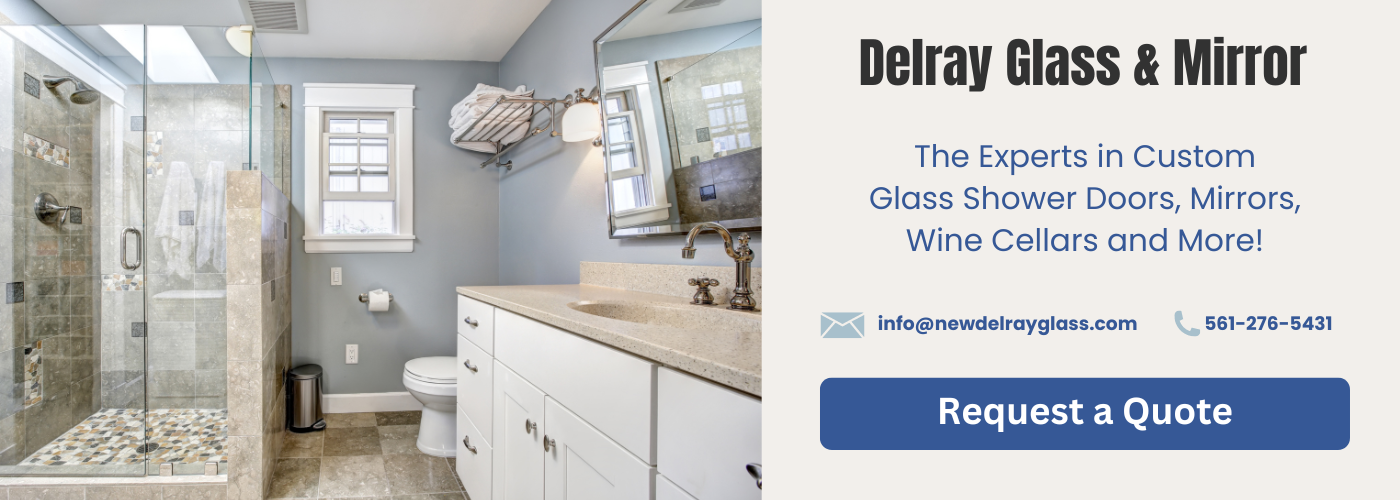
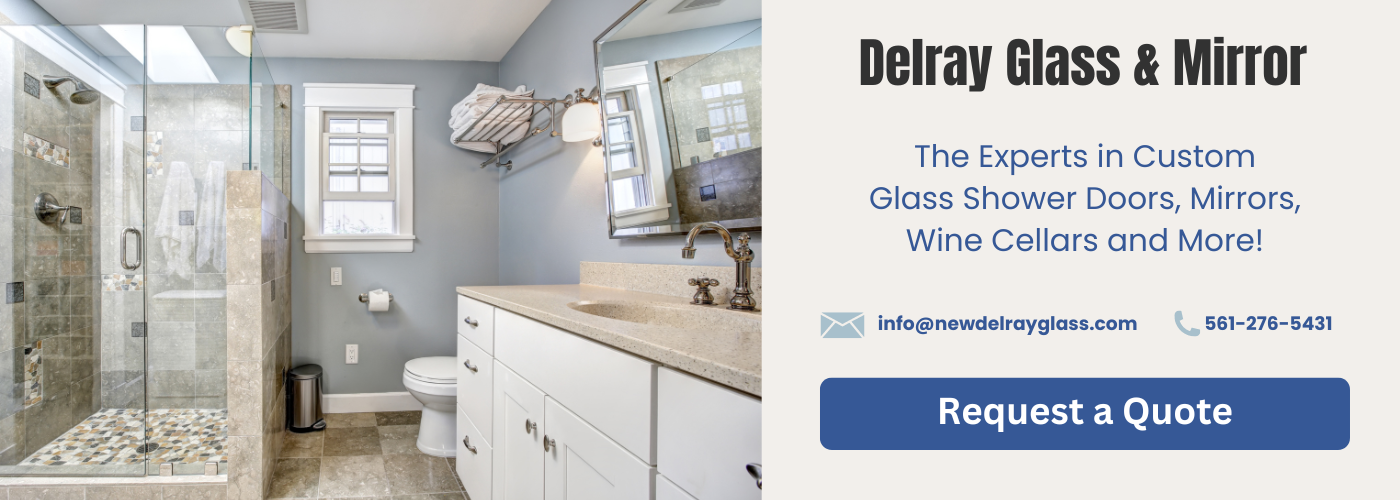
Understanding the Concept of Lead Time in Customized Production
Lead time in customized production, such as the making of custom glass shelves, refers to the total time it takes from the moment the customer places the order until the product is ready for delivery or pickup. It is a crucial concept in the field of manufacturing and supply chain management, giving a clear indication of how long the customer will have to wait for their custom product.
Understanding lead time is especially important when dealing with custom-made items. This is because customization often involves a more complicated production process compared to mass-produced items. There is a higher level of detail and specificity in the production process, often requiring specialized labor and materials. As such, the lead time for custom items can be significantly longer than for standard items.
When it comes to custom glass shelves, the lead time can vary widely depending on a number of factors. These may include the complexity of the design, the availability of materials, the speed of the manufacturing process, and the capacity of the manufacturer. It’s important for customers to have a clear understanding of the lead time when ordering custom glass shelves, to manage expectations and plan accordingly.
Factors Influencing the Lead Time for Custom Glass Shelves
There are several factors that influence the lead time for custom glass shelves. These factors can vary greatly depending on the specific circumstances of the order, but generally, they can be grouped into a few key categories.
The first and perhaps most significant factor is the complexity of the custom design. More intricate and detailed designs will inevitably require more time to accurately produce. This is because the production process for custom glass shelves involves careful planning and meticulous execution to ensure that the final product matches the customer’s exact specifications. The more complex the design, the longer this process will take.
Another major factor is the quantity of the order. Larger orders will naturally take longer to fill than smaller ones. This is simply a matter of production capacity. The more shelves that need to be made, the more time it will take to produce them all.
The availability of materials is also a significant factor. If the materials required for the custom glass shelves are not readily available, then this could potentially lead to delays in the production process. This factor is particularly relevant in situations where the customer has requested a specific type of glass or a particular color that is not commonly used.
Lastly, the lead time can also be affected by the current workload of the manufacturing facility. If the facility is already operating at full capacity with other orders, then it may take longer for them to start work on the custom glass shelves. This factor can be difficult to predict, as it depends on the demand for custom glass shelves at any given time.
Understanding these factors can help customers to plan their orders more effectively and set realistic expectations for the lead time.
Process of Ordering and Manufacturing Custom Glass Shelves
The process of ordering and manufacturing custom glass shelves is a detailed and intricate procedure that involves various steps. It starts from the moment the customer places an order, specifying their desired dimensions, type of glass, and other specifications. This is a critical step as it forms the basis for the entire production cycle.
Upon receiving the order, the manufacturer begins by sourcing the required glass materials. Depending on the type of glass specified by the customer, the manufacturer may need to order the glass from a supplier, which adds to the lead time. Once the materials are available, the manufacturing process begins. This involves cutting the glass to the desired dimensions, polishing the edges, and in some cases, tempering the glass for added strength and safety.
The manufacturing process is followed by a quality assurance check, where the shelves are inspected for any flaws or imperfections. If the shelves pass the inspection, they are then packaged and prepared for shipment. The shipping process can also add to the lead time, depending on the location of the customer.
In essence, the process of ordering and manufacturing custom glass shelves involves several stages that each contribute to the overall lead time. Understanding this process can give customers a better idea of what to expect when placing an order, and help them plan accordingly.
Estimating the Approximate Lead Time for Custom Glass Shelves
Estimating the approximate lead time for custom glass shelves is a crucial step in the process of ordering and manufacturing such items. This estimation is important for both the customer and the manufacturer. For the customer, it helps in planning and managing expectations regarding the delivery of the order. For the manufacturer, it aids in streamlining the production process and ensuring timely delivery.
Lead time estimation for custom glass shelves involves several factors. It includes the time taken to draft the design, the actual manufacturing time, and the delivery time. The design phase could take a few days to a week depending on the complexity of the required design and the number of iterations needed to finalize it. The manufacturing phase could take anywhere from a week to a few weeks, based on the complexity of the design, the availability of materials, and the manufacturer’s production capacity. The delivery phase could take a few days to a week, depending on the distance between the manufacturer and the customer.
In general, the lead time can vary greatly, but a rough estimate could be anywhere from a few weeks to a couple of months. It’s important to note that this is just an estimate and the actual lead time can vary based on a variety of factors. Communication with the manufacturer is key to getting a more accurate estimate.
It’s also worth noting that despite the estimated lead time, unforeseen circumstances can cause delays. These could include delays in sourcing materials, production hiccups, or logistical issues. Therefore, when ordering custom glass shelves, it’s always advisable to plan ahead and allow for some flexibility in the delivery timeline.
Strategies to Reduce Lead Time in Custom Glass Shelf Production
The strategies to reduce lead time in custom glass shelf production are manifold and involve various steps in the production process. They exist to ensure that the customer gets their products as quickly as possible without compromising the quality of the shelves.
One of the primary strategies is to streamline the production process. This can be achieved by eliminating unnecessary steps and procedures in the manufacturing process. For example, the use of modern and efficient machinery can significantly cut down the production time. Also, implementing a well-coordinated production schedule that effectively manages the workflow can also help to reduce the lead time.
Another significant strategy is to maintain a good relationship with suppliers. Having a reliable and efficient supply chain is essential to reduce lead times. This includes ensuring that the suppliers deliver the raw materials on time and meet the required quality standards. In the case of custom glass shelves, the quality of the glass and other materials used in the production are crucial in determining the final product’s quality.
Furthermore, efficient inventory management is also a key strategy in reducing lead time. This involves keeping an optimal level of stock to meet the demand without causing delays. It is a delicate balance between not having enough stock, which can lead to production delays, and having too much stock, which can increase the cost.
Lastly, the use of technology can also play a crucial role in reducing the lead time. For example, using software to track the production process in real-time can help identify any potential issues or delays and address them promptly.
In conclusion, the strategies to reduce lead time in custom glass shelf production are all about efficient management of the production process, from the supply chain to inventory management and the use of technology. They aim to deliver a high-quality product to the customer in the shortest possible time.