In the world of custom design and construction, glass cutting plays a critical role. This unique skill allows us to create everything from personalized windows to intricate glass artwork. However, one question that often arises is: “What is the minimum thickness required for custom glass cutting?” This article aims to provide a comprehensive answer to this question, exploring the intricacies of glass cutting and the factors that determine the minimum thickness required for this delicate process.
Our first stop is understanding the basics of glass cutting. This section will shed light on the process and techniques used in glass cutting, providing a foundation for understanding why thickness matters. Following this, we delve into the different types of glass and their minimum thickness. Given that glass comes in numerous types, each with its own properties and uses, comprehending how these differences affect the minimum thickness required for cutting is crucial.
Next, we explore the various factors that affect the minimum thickness for custom glass cutting. This includes aspects like the type of tools used, the intended use of the glass, and the skills of the person doing the cutting. We also highlight the importance of following the minimum thickness for glass cutting. This is important not only to ensure the success of the project but also to prevent any potential issues like cracking or shattering.
Finally, we will discuss the safety measures in custom glass cutting. As this process involves a fair amount of risk, understanding and implementing safety measures is essential to prevent injuries. Through this comprehensive exploration, we aim to provide a clear answer to what the minimum thickness required for custom glass cutting is, along with a deeper understanding of this fascinating process.
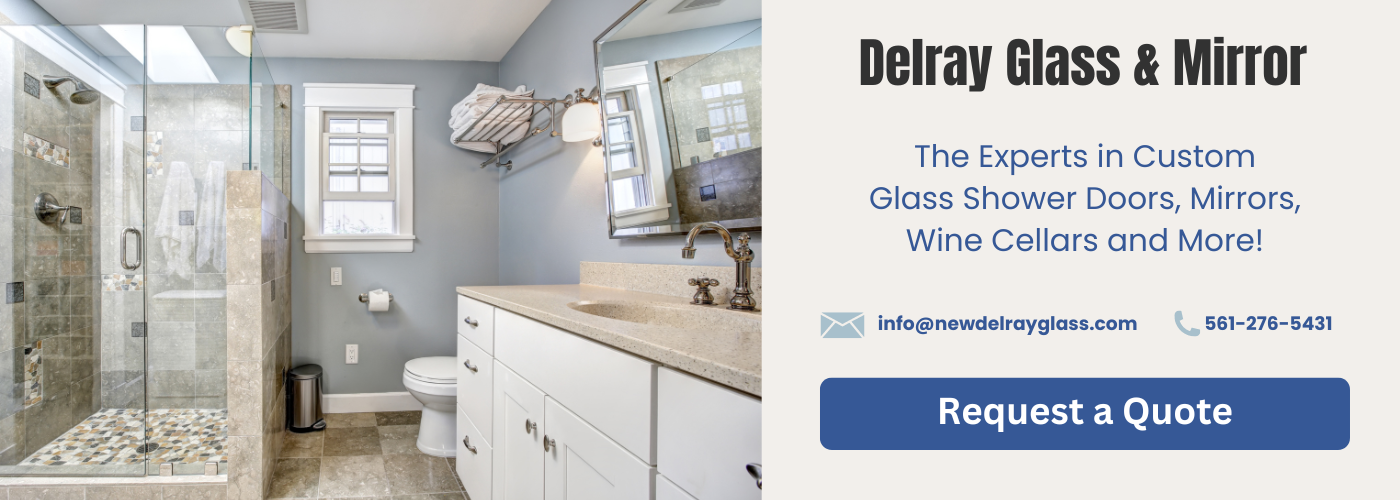
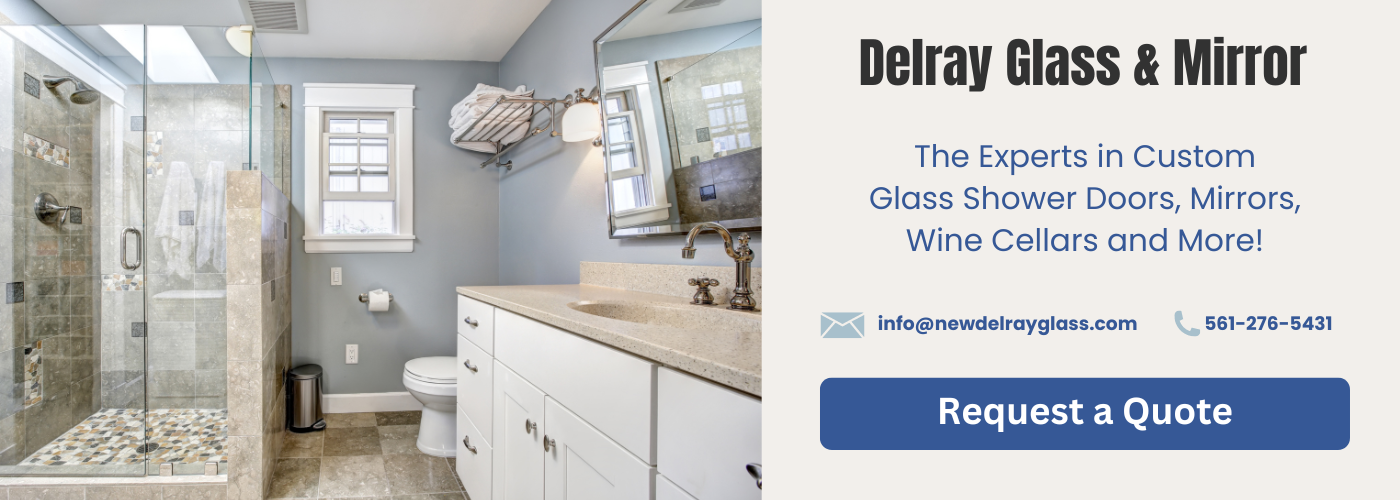
Understanding the Basics of Glass Cutting
The process of custom glass cutting requires a comprehensive understanding of the basics. It starts with the design phase, where the exact measurements and shape of the glass to be cut are determined. The type of glass is also selected at this stage.
Once the design phase is completed, the actual glass cutting process begins. It’s important to note that glass cutting is a precise craft that requires professional skills and the right tools. A glass cutter, which is a tool specifically designed for this purpose, is used. It scores the surface of the glass along the intended cut line.
The glass is then stressed along the score line, causing it to break cleanly along the line. The edges of the cut glass are then often polished to smooth them and remove any sharp edges. Understanding these basics is crucial for anyone involved in custom glass cutting, as it not only ensures the quality of the final product but also the safety of the persons involved in the process.
The thickness of the glass plays a significant role in the cutting process. Thicker glass usually requires more careful handling and a deeper score line to break correctly. If the glass is too thin, there is a risk of it shattering during the cutting process. Therefore, understanding the minimum thickness required for custom glass cutting is essential.
Different Types of Glass and Their Minimum Thickness
Different types of glasses have different minimum thicknesses suitable for cutting, which is largely dictated by their properties and the purpose they are meant to serve. The thickness of glass plays a critical role in its strength, durability, and functionality. Therefore, understanding the different types of glass and their minimum thickness is essential before proceeding with a custom glass cutting project.
To begin with, there’s annealed glass, often used in windows and picture frames. This type of glass is typically 2mm to 12mm thick. Then we have tempered glass, which is heat-treated for added strength. It is often used in applications that demand safety, such as shower doors, car windows, and glass doors. The minimum thickness for tempered glass is usually 4mm.
Another type is laminated glass, which consists of two or more layers of glass bonded together with a plastic interlayer. Its minimum thickness, inclusive of the interlayer, is typically around 6.4mm. This type of glass is used in applications where safety is paramount, such as in car windshields and high-rise windows.
Lastly, there is insulating glass, also known as double-glazing, that is made by sealing two or more plies of glass enclosing a space filled with dehydrated air or a gas. The minimum thickness for each ply of glass in insulating glass is usually 3mm.
As seen, different types of glasses have varied minimum thickness specifications. It is essential to consider these while planning a custom glass cutting project, as the thickness profoundly impacts the structural integrity and safety of the final product.
Factors Affecting the Minimum Thickness for Custom Glass Cutting
The minimum thickness required for custom glass cutting is impacted by a number of factors. These factors can vary from the type of glass, the process of cutting, the tools used, to the desired final product.
Firstly, the type of glass plays a significant role in determining the minimum thickness. Different types of glass have different properties and react differently to the cutting process. For instance, tempered glass requires a greater thickness than annealed glass to withstand the cutting process.
Secondly, the process of cutting itself can affect the thickness. Traditional cutting methods might need thicker glass compared to modern laser cutting techniques that can handle thinner glass. The cutting tool also has an influence, as some tools can cut thin glass without causing breakage, while others might need a certain thickness to function properly.
Lastly, the desired final product is a crucial factor. If the finished product needs to be more durable, a thicker glass would be required. On the other hand, for aesthetic purposes or less functional requirements, thinner glass may be suitable.
Understanding these factors is key to determining the minimum thickness required for custom glass cutting. It ensures not only the successful creation of the desired product but also the safety of the process.
Importance of Following Minimum Thickness for Glass Cutting
The importance of adhering to the minimum thickness when cutting custom glass cannot be overstated. This guideline is not arbitrary; instead, it’s based on practical reasons that ensure the safety and functionality of the end product.
When the thickness of glass is below the recommended minimum, it becomes highly susceptible to breakage. This is because thinner glass is not as strong and is more likely to crack or shatter under pressure, whether during the cutting process, installation, or even during normal use. Not only can this result in a loss of time and resources, but it can also pose a significant safety risk.
Moreover, the minimum thickness also impacts the overall quality of the glass piece. For instance, thinner glass may not provide the same level of clarity or visual appeal as its thicker counterpart. It may also be more prone to scratches and other forms of damage, further reducing its lifespan and aesthetic value.
In addition, some specific applications require glass of a certain thickness. For example, architectural features like glass walls or doors need to be thick enough to withstand daily wear and tear, while still providing the necessary transparency and light transmission. Ignoring the minimum thickness can therefore lead to a product that is unfit for its intended purpose.
In conclusion, the minimum thickness in custom glass cutting is a crucial factor that ensures the durability, safety, and functionality of the end product. It is a standard that should always be adhered to, regardless of the specific type of glass or cutting technique used.
Safety Measures in Custom Glass Cutting
Safety Measures in Custom Glass Cutting is an integral subtopic when discussing the minimum thickness required for custom glass cutting. The thickness of the glass significantly impacts the safety measures that need to be in place during the glass cutting process.
The first thing to consider is the type of glass being cut. Different types of glass have different properties, which affect how they react to being cut. For instance, tempered glass, which is often used in safety applications, is designed to shatter into small, harmless pieces when broken. If this type of glass is cut without taking the appropriate safety measures, it can cause serious harm.
Another safety measure in custom glass cutting is the use of appropriate personal protective equipment (PPE). This includes safety goggles to protect the eyes from flying glass shards, gloves to protect the hands, and in some cases, protective clothing to prevent injury from larger pieces of broken glass.
The equipment used in the glass cutting process must also be taken into account. The blades used to cut glass should be sharp and well-maintained to ensure clean cuts and minimize the risk of the glass cracking or shattering unexpectedly. The work area should be clean and free from clutter to prevent accidents.
Lastly, proper training is a crucial safety measure in custom glass cutting. Workers should be trained on the correct handling and cutting techniques to minimize the risk of accidents and produce the best quality cuts.
In conclusion, while the minimum thickness required for custom glass cutting is crucial, it is equally important to consider the safety measures in place during the process to protect both the workers and the end-users of the glass products.