In the world of maintenance, unexpected breakdowns and malfunctions are inevitable, raising the critical question: What is the turnaround time for emergency repairs or replacements? This article is set to provide comprehensive insight into that question, covering all aspects from understanding the concept to strategies for reducing turnaround time.
The first section, “Understanding the Concept of Emergency Repairs or Replacements,” will serve as an introductory guide to the layman, shedding light on what emergency repairs or replacements are and why they are crucial in maintaining operational efficiency.
Next, we will delve into the “Factors Influencing Turnaround Time for Emergency Repairs or Replacements,” discussing various elements such as the complexity of the issue, availability of parts, and the expertise of the technical team, among others, that play a significant role in defining the timeframe for repairs or replacements.
The third section, “Typical Turnaround Times in Different Industries,” will provide a comparative analysis of how turnaround times vary across different sectors, offering an industry-wise perspective on the subject.
In the fourth section, “The Importance of Rapid Turnaround Time in Emergency Situations,” we will explore the impact of swift response and repair times on business operations, emphasizing why businesses should prioritize reducing turnaround time.
Lastly, we will furnish you with practical “Strategies for Reducing Turnaround Time for Emergency Repairs or Replacements,” providing valuable advice on how to expedite the repair or replacement process to ensure minimal disruption to your operations.
This article promises to be a detailed guide to understanding and managing the turnaround time for emergency repairs or replacements effectively.
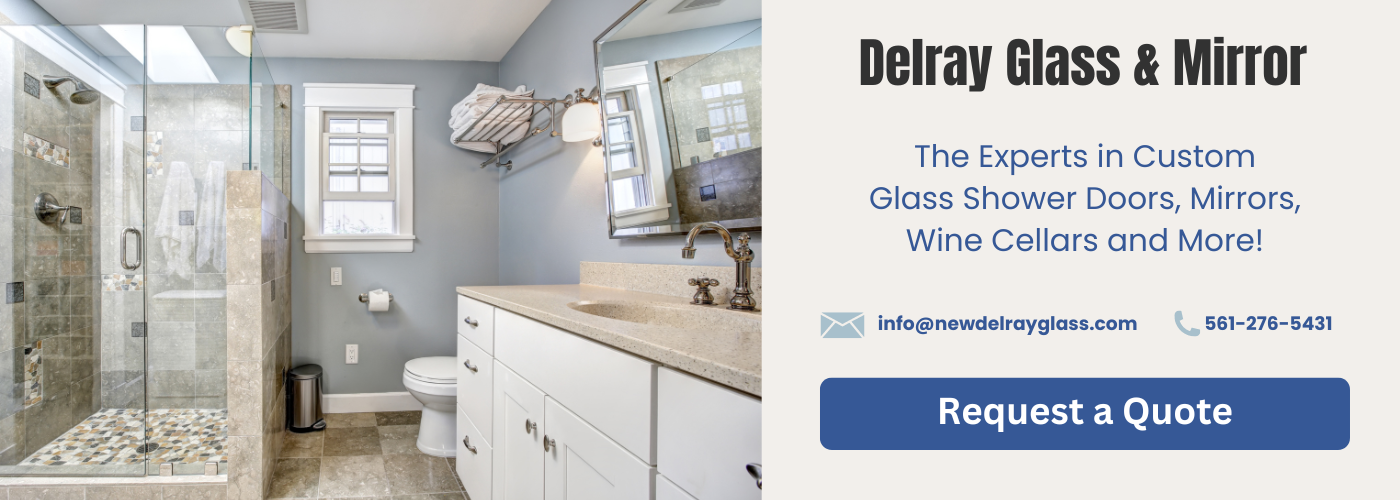
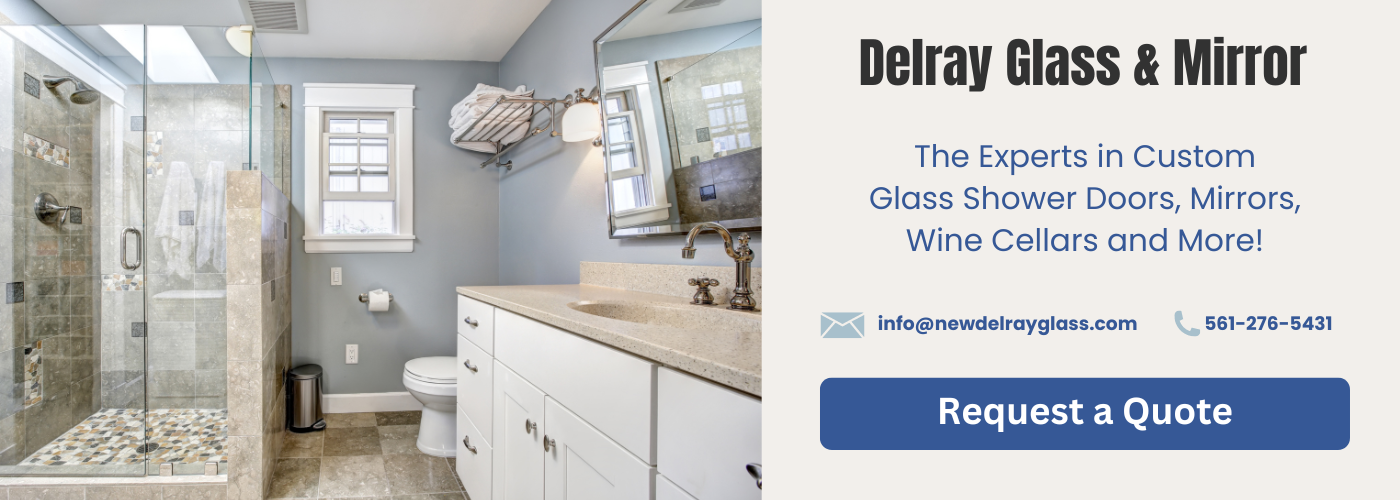
Understanding the Concept of Emergency Repairs or Replacements
Emergency repairs or replacements refer to the process of swiftly fixing or replacing malfunctioning parts, equipment, or systems that have abruptly stopped working. This concept is crucial in several contexts, including industries, households, and public service operations, to ensure minimal disruption to regular activities.
The term ’emergency’ suggests that the repair or replacement needs to be carried out as quickly as possible. This might be due to a total failure of a crucial system, potential safety hazards, or because the faulty equipment is essential to the operation of a business or service. Therefore, the focus shifts from routine maintenance or scheduled replacements to immediate, unplanned interventions.
Understanding the concept of emergency repairs or replacements also involves appreciating the skills, resources, and logistics needed to execute these tasks. It requires skilled technicians who can diagnose and fix problems quickly and accurately. It also involves having access to necessary spare parts and equipment, and the ability to deliver these to the location of the repair quickly. Furthermore, it necessitates efficient coordination and communication to ensure that the repair or replacement is carried out successfully and safely.
In summary, the concept of emergency repairs or replacements is all about prompt and effective responses to unexpected equipment or system failures. It is a critical aspect of maintenance operations in various fields and has a significant impact on productivity, safety, and service delivery.
Factors Influencing Turnaround Time for Emergency Repairs or Replacements
When it comes to the turnaround time for emergency repairs or replacements, various factors can influence the duration. It’s essential to understand these factors to manage expectations and ensure efficient service during such critical times.
One of the primary factors that can influence turnaround time is the availability of parts or equipment needed for the repair or replacement. If the necessary parts are readily available, the turnaround time can be significantly reduced. However, if they need to be ordered, this can extend the time required to complete the repair or replacement.
Another critical factor is the complexity of the issue. Some repairs or replacements are more complex than others and require more time to complete. This can be due to the nature of the damage or malfunction, the type of equipment involved, or the expertise required to fix the problem.
The expertise and availability of the technicians can also have a significant impact. If the technicians are highly skilled and available for immediate dispatch, the turnaround time can be shortened. Conversely, if the technicians are not available or lack the necessary skills, the turnaround time can be extended.
Moreover, logistical factors such as the location of the repair or replacement can also affect the turnaround time. If the location is remote or difficult to reach, it can take longer for the technicians to arrive and begin their work.
In conclusion, the turnaround time for emergency repairs or replacements is influenced by a range of factors, including the availability of parts, the complexity of the issue, the expertise and availability of technicians, and logistical factors. Being aware of these factors can help in planning and managing such emergencies more effectively.
Typical Turnaround Times in Different Industries
The turnaround time for emergency repairs or replacements can significantly vary from one industry to another, and understanding this variation is crucial for both service providers and customers alike. Each industry has its own set of standards and expectations when it comes to handling emergencies, and these standards can greatly influence the associated turnaround times.
For instance, in the healthcare industry, where equipment functionality can directly impact patient health, the turnaround time is often expected to be immediate or near-immediate. This often necessitates a dedicated team of maintenance professionals on standby round the clock to handle any emergency repairs or replacements.
On the other hand, in industries like manufacturing or construction, where equipment downtime can lead to significant financial losses, the emphasis is on minimizing the time it takes to get the equipment back up and running. This often involves having spare parts readily available and technicians skilled in rapid diagnostics and repairs. Yet, the expectation is not always for an immediate response like in healthcare, but rather a rapid one that can minimize financial impact.
In the retail sector, the turnaround times for emergency repairs or replacements can be more flexible. This is because, in many cases, the failure of a single piece of equipment may not severely impact the entire operation. However, during peak seasons or during promotional events, the turnaround times may need to be faster to ensure smooth operations and customer satisfaction.
In conclusion, the typical turnaround times in different industries are shaped by the unique needs and challenges of each industry. Understanding these needs and expectations can help service providers deliver more effective and timely solutions, while also helping customers to manage their expectations better.
The Importance of Rapid Turnaround Time in Emergency Situations
Rapid turnaround time in emergency situations is of utmost importance, and this is especially significant in the realm of repairs and replacements. In various sectors, the ability to quickly address and rectify issues can mean the difference between a minor inconvenience and a major disruption. Whether we are talking about a critical manufacturing component, a vital piece of medical equipment, or an essential home appliance, the speed of response can have a profound impact on operations, productivity, and overall service quality.
When a device or piece of equipment breaks down unexpectedly, the consequences can range from costly downtime and lost productivity to safety risks and customer dissatisfaction. For instance, in a manufacturing plant, a malfunctioning machine can halt the entire production line, leading to significant financial losses. Similarly, in a healthcare setting, a broken medical device can compromise patient care and safety.
This is why rapid turnaround time is so crucial in emergency situations. A swift response not only helps mitigate these negative effects but also demonstrates a company’s commitment to service excellence. It reduces the period of interruption, allows for faster recovery, and helps maintain a high level of operational efficiency. Furthermore, it can also enhance a company’s reputation, as customers and clients often judge businesses on how effectively and quickly they respond to emergencies.
In conclusion, the importance of rapid turnaround time in emergency situations cannot be overstated. It is a key performance indicator that reflects a company’s ability to effectively manage unexpected events and ensure continuity of service. Therefore, businesses should strive to improve their turnaround times for emergency repairs and replacements, as this can significantly influence their overall performance and customer satisfaction levels.
Strategies for Reducing Turnaround Time for Emergency Repairs or Replacements
Strategies for Reducing Turnaround Time for Emergency Repairs or Replacements are crucial for any enterprise that relies on machinery, equipment, or systems that may require urgent attention. These strategies are designed to ensure that any disruption caused by a breakdown is minimized, allowing normal operations to resume as quickly as possible.
One key strategy involves proactive maintenance. This means regularly inspecting and maintaining equipment to prevent failures from occurring in the first place. By catching potential issues early, you can often avoid the need for emergency repairs.
Another strategy is to have a robust response plan in place. This typically involves having a dedicated team that is trained to respond quickly and efficiently to emergency situations. It also means having the necessary parts and equipment readily available so that repairs or replacements can be carried out without delay.
Additionally, leveraging technology can also help reduce turnaround times. For example, predictive maintenance technologies can alert you to potential equipment failures before they happen, giving you the chance to address them during scheduled downtime rather than in an emergency situation.
Implementing these strategies can significantly reduce the turnaround time for emergency repairs or replacements, minimizing downtime, and maintaining productivity. It’s about being prepared, proactive, and efficient, ensuring that when emergencies do occur, they’re resolved as quickly as possible.