In the realm of glass manufacturing, ensuring top-notch quality control is paramount, particularly when it comes to the production of impact resistant glass. This specialized type of glass is designed to withstand substantial force without shattering, making it an integral component in various applications ranging from automotive windshields to high-rise buildings. However, the process of manufacturing this glass demands stringent quality control measures to ensure its robustness and durability.
The first step to ensuring quality in impact resistant glass manufacturing starts with the selection and sourcing of raw materials. It’s crucial to procure high-grade materials that can withstand the rigors of the manufacturing process and the final usage. The manufacturing process itself is another area where strict control measures must be enforced. Every step, from initial melting to final tempering, needs to be meticulously monitored to ensure the glass’s impact resistance.
Quality testing methods play a vital role too. From hardness tests to impact resistance tests, these methods help verify that the finished product meets the required specifications. Adherence to established standards and regulations is a non-negotiable aspect of quality control. Manufacturers must comply with the industry standards and regulatory guidelines to ensure their products are safe and reliable.
Finally, how the impact resistant glass is handled and packaged is another important measure. Even the strongest glass can be rendered useless if it is not properly handled or packaged. This final step in the manufacturing process is a vital part of quality control, ensuring the glass reaches the end user in perfect condition. This article will delve into these five key areas, highlighting the importance of rigorous quality control in the manufacturing of impact resistant glass.
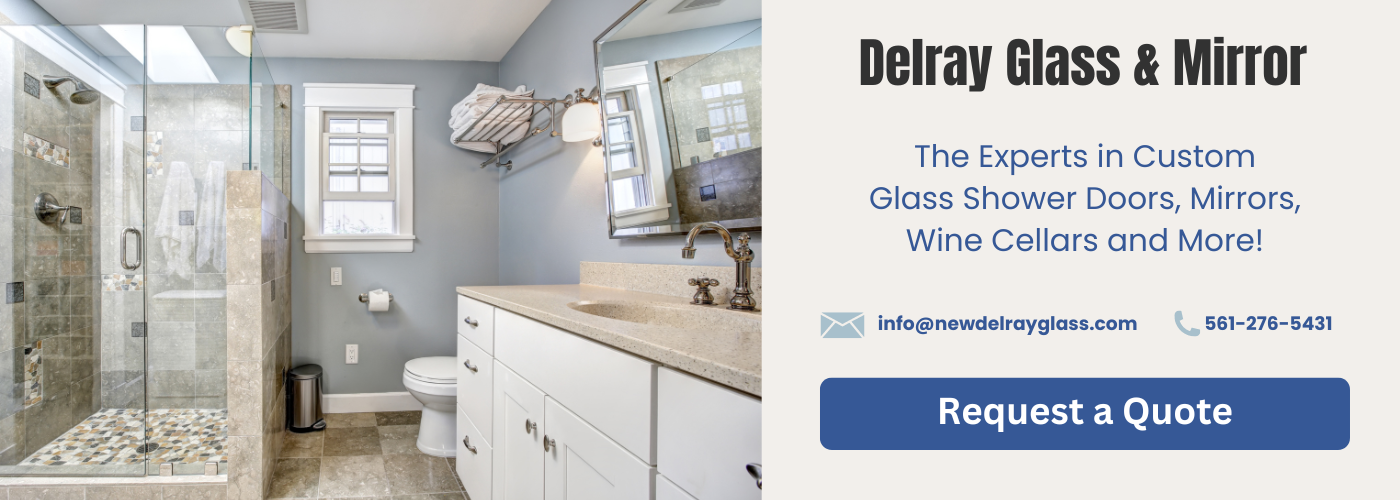
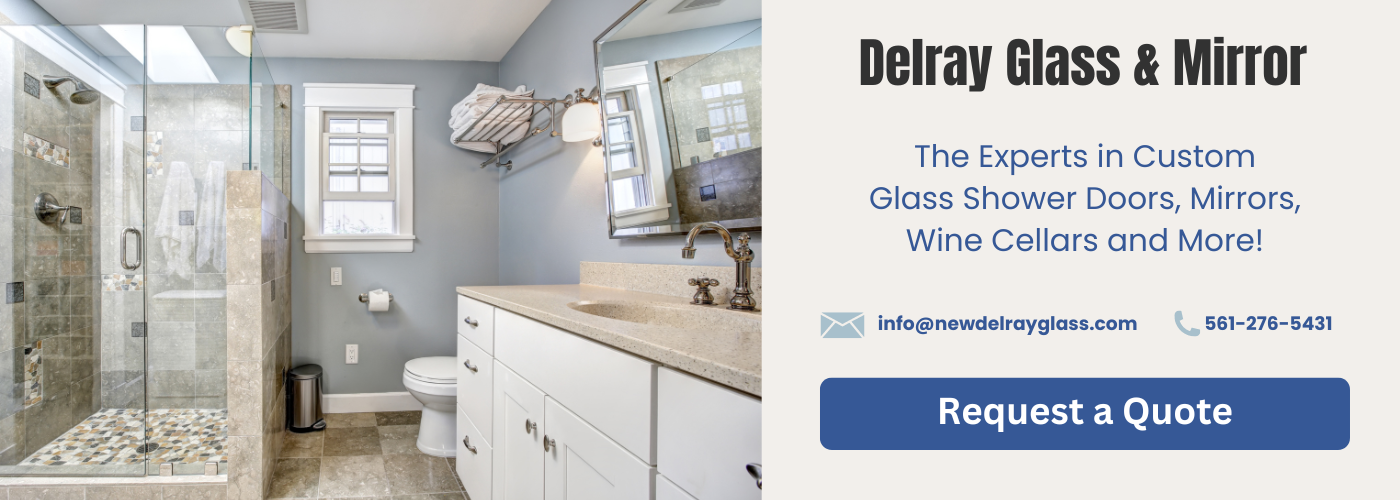
Raw Material Selection and Sourcing for Impact Resistant Glass
Raw Material Selection and Sourcing for Impact Resistant Glass is a crucial aspect of quality control measures when manufacturing this type of glass. The quality of the raw materials plays a significant role in determining the final product’s strength, durability, and impact resistance. Therefore, it’s essential to carefully select and source high-quality raw materials.
Typically, the raw materials for manufacturing impact resistant glass include silica sand, soda ash, limestone, and other components. The quality of these materials can significantly affect the glass’s ability to withstand impacts. For example, impurities in the silica sand can weaken the glass and make it more vulnerable to breakage.
Furthermore, the sourcing of these raw materials also plays a crucial role in the quality control process. Suppliers must be reliable and able to consistently provide high-quality materials. This often involves conducting thorough supplier evaluations and audits, ensuring they meet the required standards and certifications.
In conclusion, raw material selection and sourcing are fundamental steps in the quality control measures for manufacturing impact resistant glass. By ensuring the use of high-quality raw materials from reliable sources, manufacturers can produce durable, high-performing impact resistant glass that meets the needs and expectations of their customers.
Manufacturing Process of Impact Resistant Glass
The manufacturing process of impact resistant glass is a critical aspect in ensuring its quality and durability. This process involves several stages, each of which must be carried out meticulously to produce glass that can withstand high impact forces.
The first stage in the manufacturing process involves melting the raw materials at a very high temperature to form molten glass. This mixture is then cooled rapidly, a process known as quenching, which makes the glass much tougher and more resistant to breakage.
Following this, the glass then undergoes a process called lamination. This involves bonding two or more layers of glass together with a layer of plastic or resin in between. This layer acts as a barrier that helps to absorb and distribute impact forces, reducing the likelihood of the glass shattering upon impact.
The manufacturing process of impact resistant glass also involves heat treatment. This process strengthens the glass, making it more resistant to breakage, and is especially important for glass that will be used in high-stress environments.
Each of these stages in the manufacturing process is crucial in ensuring the quality of the finished product. Any errors or inconsistencies can result in a final product that is less resistant to impact, which is why strict quality control measures are necessary throughout the process. These measures include regular inspections and testing, as well as adherence to industry standards and regulations.
In conclusion, the manufacturing process of impact resistant glass is a complex one that requires careful attention to detail. However, when carried out correctly, it produces a product that is incredibly durable and capable of withstanding even the most severe impacts. This makes impact resistant glass an invaluable material in many different industries, including construction, automotive, and security.
Quality Testing Methods for Impact Resistant Glass
Quality Testing Methods for Impact Resistant Glass is a critical component in the manufacturing process of impact resistant glass. This is a subtopic of immense importance in the context of quality control measures, as it directly pertains to the effectiveness and integrity of the finished product.
The procedure involves a series of tests designed to assess the strength, durability and impact resistance of the glass. Some of the most common tests include impact testing, where the glass is subjected to forces that simulate real-world conditions such as high winds, flying debris, and even burglary attempts. This ensures that the glass can withstand such pressures without shattering or compromising its structural integrity.
Another essential test is the durability test, which evaluates the glass’s resilience over time. It involves subjecting the glass to various environmental conditions, including changes in temperature, humidity, and exposure to UV radiation. This helps determine how the glass will perform in the long run, and whether it can maintain its impact resistance properties over time.
The penetration resistance test is another critical quality testing method. This test measures the glass’s resistance to penetration when subjected to high-speed, high-energy impacts. This is crucial in scenarios where the glass needs to prevent or minimize penetration from high-speed projectiles.
In conclusion, quality testing methods for impact resistant glass are integral to the manufacturing process. They ensure that the product meets the necessary safety standards and performs as expected under various conditions. It is through these rigorous testing procedures that manufacturers can guarantee the performance and safety of their impact resistant glass products.
Standards and Regulations for Impact Resistant Glass
Standards and regulations for impact resistant glass play a crucial role in maintaining the quality and safety of the product. These guidelines ensure that all impact resistant glass produced meets a certain level of quality and is safe to use in different applications.
One of the main standards that manufacturers adhere to is the American Society for Testing and Materials (ASTM) standards. The ASTM has set specific standards for impact resistant glass, which include guidelines for the materials used, manufacturing process, and quality testing methods. These standards ensure that all impact resistant glass has been thoroughly tested and meets certain performance requirements.
Additionally, the International Code Council (ICC) also provides regulations for impact resistant glass. These regulations relate primarily to the use of impact resistant glass in buildings and ensure that the glass is safe and durable enough for use in various constructions.
Furthermore, manufacturers must also follow the regulations set by the Consumer Product Safety Commission (CPSC). The CPSC requires that all impact resistant glass meet certain safety standards to protect consumers from potential harm.
In summary, standards and regulations for impact resistant glass are vital in ensuring the product’s quality, durability, safety, and performance. Manufacturers must strictly adhere to these guidelines to ensure that their product is reliable and safe for use. These measures, along with stringent quality control procedures, help to maintain the integrity of impact resistant glass and ensure its effectiveness in various applications.
Handling and Packaging Measures for Impact Resistant Glass
The process of manufacturing impact-resistant glass isn’t complete without implementing effective handling and packaging measures. This is a critical stage in the production process that ensures the finished product reaches the customer in perfect condition, maintaining its impact resistance qualities.
Handling impact resistant glass requires special care. The glass must be handled with suitable equipment and protective gear to prevent any damage that could compromise its integrity. It’s crucial to avoid any scratching, chipping, or breaking of the glass during handling. Any such damage can negatively impact the glass’s resistance to impact, rendering it less effective in its primary function.
When it comes to packaging measures for impact resistant glass, the aim is to ensure the safety of the product during transportation and storage. The glass is typically packed in robust, protective materials that absorb shocks and prevent breakage. In addition, the packaging often includes separators to prevent the glass from rubbing against other pieces, which could lead to scratches or other damage.
The packaging also often includes clear labels indicating the fragile and valuable nature of the contents. This alerts handlers to the need for extra care during transportation and storage. This way, the quality of the impact-resistant glass is maintained from the manufacturing facility to the final installation site.
In conclusion, the handling and packaging measures for impact resistant glass are an integral part of the quality control process in its manufacturing. These measures ensure that the finished product maintains its quality and delivers the expected performance to the end user.