Laminated glass, a prevalent material in a variety of applications, is renowned for its strength, durability, and versatility. A critical factor that influences these properties and its suitability for specific uses is the thickness of the laminated glass. This article will delve into the available thicknesses for laminated glass and how they impact its functionality and performance.
The first section will explore the different types of laminated glass, focusing on how their construction determines their thickness. This will provide a clear understanding of why laminated glass comes in varying thicknesses and what those differences imply.
Next, we will examine the manufacturing process of laminated glass, with emphasis on how manufacturers control the thickness of the final product. Understanding this process will provide insight into the precision and expertise required to produce laminated glass of specific thicknesses.
In the third section, we will discuss the thickness requirements for different uses of laminated glass. Whether it’s for vehicles, buildings, or safety equipment, there are specific thickness guidelines that must be adhered to.
The fourth section will explore how the thickness of laminated glass affects its performance. From its strength to its sound insulation properties, the thickness of laminated glass has a profound impact on its overall performance.
Lastly, we will look at how manufacturers can customize the thickness of laminated glass to meet specific requirements. This adaptability is one of the reasons why laminated glass is a preferred choice in various industries.
Together, these sections will provide a comprehensive understanding of the thicknesses available for laminated glass and how these choices affect its utility and performance.
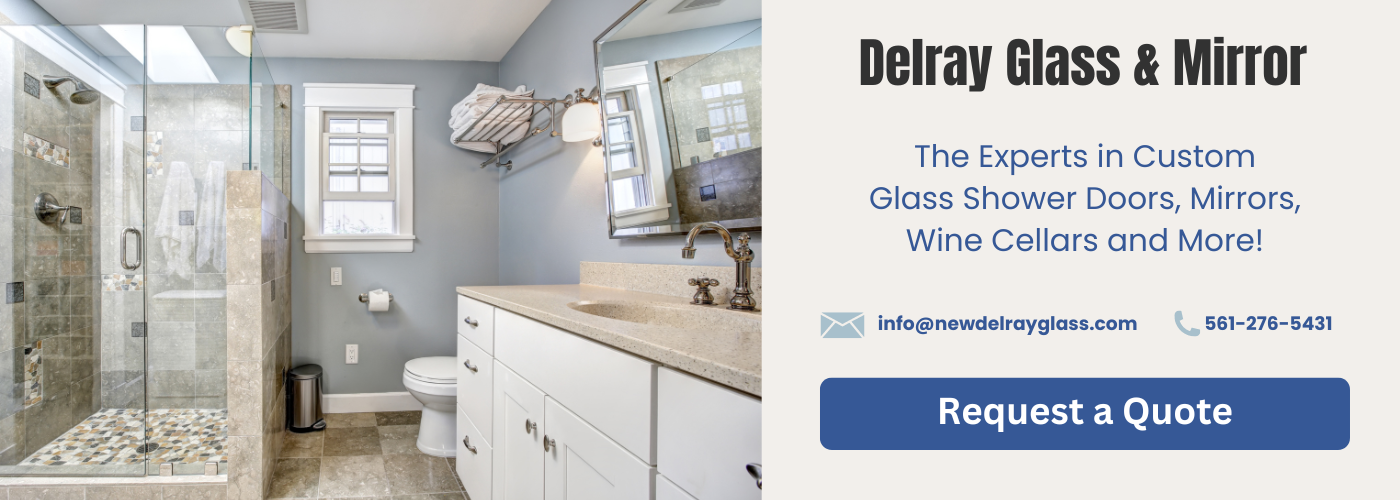
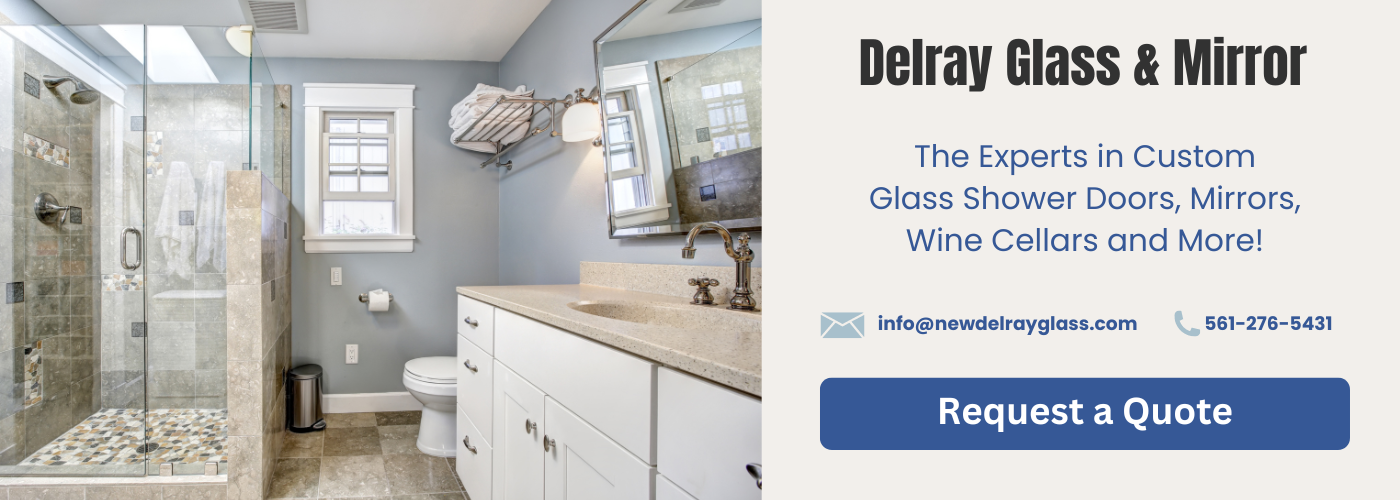
Types of Laminated Glass and Their Thicknesses
Laminated glass is available in a variety of types and thicknesses, tailored to suit a wide range of applications. The thickness of laminated glass is determined by the specific requirements of its intended use. It is composed of layers of glass and interlayers, typically made from polyvinyl butyral (PVB), ethylene-vinyl acetate (EVA), or SentryGlas®. The interlayers contribute to the overall thickness of the laminated glass and also its safety properties.
There are several types of laminated glass, each with different thicknesses. Some of the common types include standard laminated glass, acoustic laminated glass, and safety and security laminated glass. Standard laminated glass commonly comes in thicknesses ranging from 6.38mm to 10.38mm, whereas acoustic laminated glass, designed to reduce noise, is typically thicker – often around 6.5mm to 14.5mm.
Safety and security laminated glass is designed to resist impacts and attempts at forced entry. Its thickness varies considerably depending on its purpose, often starting at around 13.5mm for basic impact resistance, up to 25mm or more for glass that is bullet-resistant or bomb-blast resistant.
It is important to note that the thickness of laminated glass should be chosen based on its application and the specific requirements of the project. For instance, laminated glass used in a high-rise building’s facade would likely need to be thicker and stronger than laminated glass used in a residential window. Therefore, understanding the types of laminated glass and their respective thicknesses can play a crucial role in the success and safety of a project.
Manufacturing Process and Thickness Control in Laminated Glass
The manufacturing process of laminated glass and the control of its thickness is a precise and highly technical operation. Laminated glass is made by sandwiching a layer of polyvinyl butyral (PVB) or ethylene-vinyl acetate (EVA) between two or more layers of glass. The aim of this process is to create a safety glass that holds together when shattered, preventing injury from flying or falling shards.
The control of thickness in this process is crucial. It is determined primarily by the number of layers of glass and type of interlayer used, as well as the specific requirements of the end product. The thickness of the glass layers typically ranges from around 0.6 mm to 25 mm, while the interlayer can range from 0.38 mm to 3.04 mm in thickness.
The manufacturing process involves placing the glass layers and the interlayer into a vacuum bag where air and moisture are removed. The materials are then heated under pressure in an autoclave, which causes the interlayer to melt and bond with the glass layers. The result is a single panel of laminated glass.
The thickness control in laminated glass manufacturing is crucial to the safety and functionality of the end product. Too thin, and the glass may not provide sufficient protection; too thick, and it may not be transparent enough or may be unnecessarily heavy. As such, manufacturers must adhere to strict standards and guidelines when controlling the thickness of laminated glass.
Thickness Requirements for Specific Uses of Laminated Glass
The thickness of laminated glass plays a significant role in determining its suitability for specific applications. In the domain of laminated glass, the thickness requirement is largely dictated by the purpose the glass is intended to serve.
For instance, in architectural applications such as skyscrapers, the thickness of the laminated glass would need to be substantial to ensure the glass’s structural integrity, safety and sound insulation. These types of buildings often require thicker laminated glass, as the glass must withstand high wind loads and potential impact events.
On the other hand, for interior applications like glass doors or partitions in a home or office, the thickness of the laminated glass can be less because the glass doesn’t need to withstand the same level of environmental stress.
However, it’s crucial to understand that meeting thickness requirements alone is not enough when it comes to selecting the appropriate laminated glass for a specific application. Other factors such as glass type, lamination process, and the quality of interlayer materials also contribute to the performance and safety features of the final product.
In summary, the thickness requirements for specific uses of laminated glass vary widely, depending on the application. It’s essential to consult with a glass professional to ensure that the selected laminated glass meets all the requirements necessary for its intended use.
Impact of Thickness on Laminated Glass Performance
The thickness of laminated glass plays a crucial role in its performance. It’s essential to understand that laminated glass is a type of safety glass that holds together when shattered. It’s designed to resist penetration and absorb energy well, which makes it perfect for a wide range of applications.
The thickness of the laminated glass directly impacts its ability to absorb impact. The thicker the glass, the more impact it can withstand. This is why thicker laminated glass is often used in places where higher safety standards are required, such as car windshields, skylights, and high-rise buildings.
However, while thicker glass provides better protection, it also comes with certain drawbacks. For instance, it’s heavier, which can add to the structural load of a building. It’s also less transparent, which may not be ideal for applications where clarity is important. Therefore, when selecting the thickness of laminated glass, it’s important to consider both the safety requirements and the specific needs of the application.
In conclusion, the thickness of laminated glass significantly affects its performance. It’s a vital factor to consider when choosing the right type of laminated glass for a particular application.
Customizing Thickness in Laminated Glass Production
Customizing thickness in laminated glass production is a significant aspect in the glass industry. This process allows manufacturers to produce laminated glass that fits specific dimensions according to the requirements of various applications. The customization of thickness in laminated glass production provides a wide range of possibilities for different industries that use this type of glass.
Laminated glass is used in numerous applications, from automotive windshields to building windows, due to its strength and safety features. The thickness of the glass plays a crucial role in these applications. For instance, in the automotive industry, a specific thickness is needed to ensure the windshield can withstand impact and protect passengers. The same goes for building windows, where thickness can affect the window’s ability to resist wind loads and other pressures.
Customizing the thickness of laminated glass during production can also positively impact its acoustic insulation properties. A thicker laminated glass can provide excellent sound insulation, making it an ideal choice for buildings near busy streets or in noisy environments.
Moreover, the thickness customization in laminated glass production can influence the glass’s energy efficiency. Thicker laminated glass can provide better insulation, helping to keep buildings cool in summer and warm in winter. This can lead to significant energy savings and contribute to the development of more sustainable buildings.
In conclusion, the ability to customize the thickness in laminated glass production is a significant advantage. It allows manufacturers to cater to the specific needs of different industries and applications, making laminated glass a versatile and valuable material.