Sandblasting, a popular technique used in a variety of industries, employs the use of sand to clean or etch a surface. One of the most prevalent applications of sandblasting is in the glass industry, where it’s used to create a smooth or decorative finish on glass surfaces. The type of sand used in glass sandblasting significantly influences the process and its outcome. This article aims to delve deeper into the nature of sandblasting, the types of sand used, and the role of silica sand in this process.
The first part of our exploration focuses on the different types of sand utilized in sandblasting. Not all sands are created equal, and understanding the specific properties of each type can dramatically affect the results of a sandblasting project. The second section discusses the role of silica sand in glass sandblasting, highlighting its importance and prevalence in the industry.
The third part of the article discusses how sand quality impacts sandblasting efficiency. The size, uniformity, and cleanliness of sand particles can significantly influence the effectiveness and speed of sandblasting. In the fourth section, we will discuss the safety concerns associated with different types of sand in sandblasting, as certain types of sand can pose health risks to workers.
Finally, the article will discuss the environmental considerations of sand sources for sandblasting. As sand is a natural resource, its extraction and use need to be managed responsibly to minimize environmental impact. In conclusion, the type of sand used in glass sandblasting is a multifaceted subject that extends beyond mere surface-level understanding.
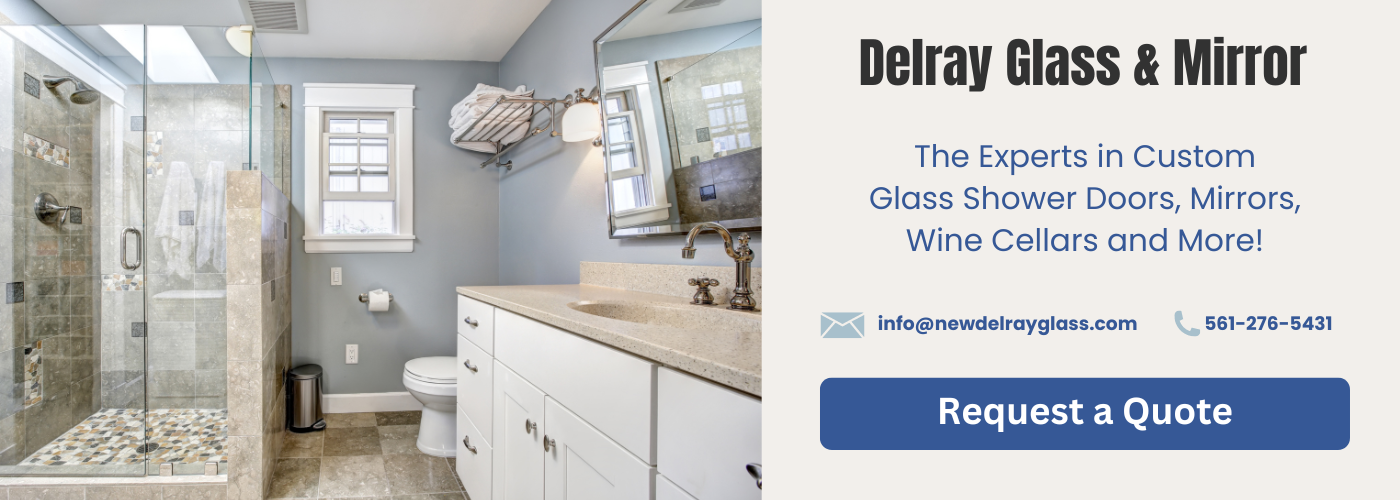
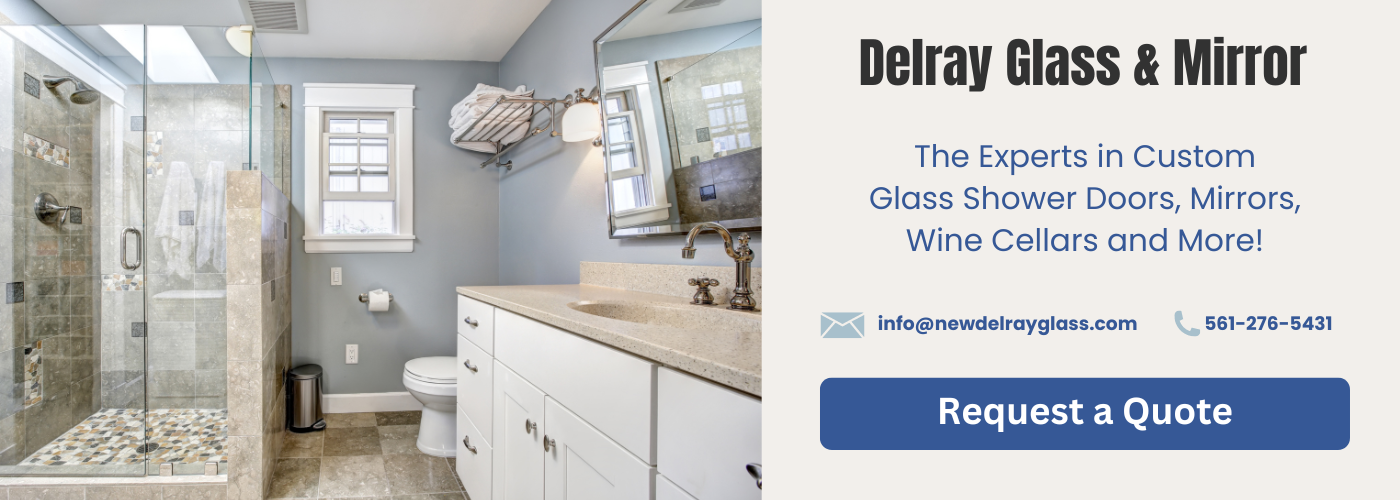
Types of Sand Used in Sandblasting
When it comes to sandblasting, not all sands are created equal. Sandblasting, also known as abrasive blasting, is a process where fine granulated materials are applied at high pressures to a surface. This process is often used to remove paint or other coatings, or to create a specific surface texture. The type of sand used in this process can greatly affect the results.
One of the most common types of sand used in sandblasting is silica sand. Silica sand is a type of sand that is made up of tiny, angular particles. These particles are extremely hard and sharp, making them perfect for cutting through hard materials or removing tough coatings. However, while silica sand is effective for sandblasting, it can pose health risks if inhaled, which is why other types of sand are often used as well.
Another popular type of sand used in sandblasting is aluminum oxide. Aluminum oxide is a synthetic material that is extremely hard and durable. It is often used for sandblasting metal surfaces, as it is capable of removing tough coatings without causing damage to the underlying material.
Garnet sand is also commonly used in sandblasting. This type of sand is made up of tiny pieces of garnet, a hard and durable mineral. Garnet sand is often used for sandblasting wood, as it is less likely to cause damage to the wood than other types of sand.
In conclusion, the type of sand used in sandblasting depends on the material being treated and the desired end result. Silica sand, aluminum oxide, and garnet sand are all popular choices, each with their own unique properties and uses.
The Role of Silica Sand in Glass Sandblasting
The role of silica sand in glass sandblasting is crucial. Silica sand is the most commonly used type of sand for sandblasting due to its widespread availability and the ideal characteristics it possesses. It is a type of sand that is widely recognized for its hardness and angular shape, which makes it highly effective in the sandblasting process.
Glass sandblasting is a process that involves propelling small particles of silica sand at high speed towards a glass surface to create a frosted, etched, or carved effect. The process is used to create decorative designs on glass or to remove impurities or rough patches from the surface. The hardness of silica sand makes it capable of carving into the glass without causing it to shatter or break, which is a testament to its efficacy.
The angular shape of silica sand particles also plays a significant role in glass sandblasting. This shape allows the particles to hit the glass at different angles, creating an evenly frosted or etched surface. The consistency in the shape and size of silica sand particles contributes to the uniformity of the final design, ensuring a more professional and aesthetically pleasing result.
In conclusion, silica sand’s role in glass sandblasting is vital. Its hardness and angular shape, coupled with its widespread availability, make it the most suitable choice for sandblasting. The use of silica sand ensures that the glass surface is treated evenly and with precision, resulting in a finished product with a high-quality appearance.
The Impact of Sand Quality on Sandblasting Efficiency
The quality of sand used in sandblasting plays a pivotal role in determining the efficiency of the process. Sandblasting, also known as abrasive blasting, is a process where fine granulated materials are propelled at high speeds to clean or etch a surface. The quality of the sand used affects both the quality of the finished product and the speed of the operation.
High-quality sand, typically characterized by its uniformity and hardness, allows for a more predictable and efficient sandblasting process. Uniform particles can ensure a consistent, smooth finish on the blasted surface. On the other hand, if the sand particles vary significantly in size, the finish may be uneven, and it might require more time and sand to achieve the desired result.
Furthermore, the hardness of the sand significantly influences the sandblasting efficiency. Harder sands can remove materials more quickly, resulting in a more efficient process. However, it is also important to note that harder sands can cause more wear and tear on the sandblasting equipment, potentially leading to an increase in maintenance costs.
Therefore, choosing the right sand quality is crucial in glass sandblasting. It not only impacts the final product’s appearance but also plays a significant role in the operational efficiency and longevity of the sandblasting equipment.
Safety Concerns Associated with Different Types of Sand in Sandblasting
Safety in any construction or manufacturing process is of paramount importance, and sandblasting is no exception. The item 4, “Safety Concerns Associated with Different Types of Sand in Sandblasting” is a subtopic that has been brought under the spotlight due to the potential health risks associated with the operation.
Sandblasting involves projecting particles at high velocities to clean or etch a surface. The sand used in this process can vary greatly in type and quality, which can lead to different safety concerns. Silica sand, for example, was once widely used in sandblasting. However, it was discovered that the dust created during the sandblasting process could be inhaled and lead to a lung disease called silicosis. As a result, many countries have banned the use of silica sand for sandblasting.
Non-silica sands are now often used in sandblasting to mitigate this risk. However, even these can pose safety concerns if not used properly. For instance, the high velocity at which the sand particles are projected can lead to physical injuries if proper safety gear is not worn. The dust created can also still be harmful if inhaled, leading to respiratory issues.
Careful selection and proper use of sand in sandblasting are therefore crucial in ensuring the safety of the workers involved. Personal protective equipment, such as respirators and protective clothing, is a must. Furthermore, routine monitoring of air quality and regular health check-ups can help in early detection and prevention of potential health issues.
In conclusion, while sandblasting is an effective method for cleaning and etching surfaces, it is important to remember that it comes with safety concerns that need to be addressed. Proper awareness, training, and safety measures can go a long way in ensuring that the process is both effective and safe.
Environmental Considerations of Sand Sources for Sandblasting
When it comes to sandblasting, the environmental considerations of sand sources are crucial. The type of sand used in sandblasting can have significant environmental implications. Primarily, the extraction of sand for sandblasting purposes can lead to habitat destruction and biodiversity loss. Mining of sand, particularly from riverbeds and coastal areas, can disrupt local ecosystems, affecting various plant and animal species.
Another environmental issue associated with sandblasting is the disposal of used sand. After sandblasting, the sand often contains residues of paint, rust, or other contaminants that were removed from the surface being blasted. If this contaminated sand is not properly disposed, it could pollute waterways, soil, and can even cause health hazards.
Furthermore, some types of sand used in sandblasting, such as silica sand, can produce fine dust particles that, when inhaled, can cause serious health issues. These dust particles can also contribute to air pollution. Therefore, it is highly recommended to use alternatives to silica sand in sandblasting, such as crushed glass, steel grit, or walnut shells, which are more environmentally friendly.
In conclusion, while sandblasting is a highly effective technique for cleaning and preparing surfaces, it is essential to consider the environmental impact of the sand sources used in this process. By choosing environmentally friendly alternatives and ensuring proper sand disposal, we can help to minimize the environmental impact of sandblasting.