In the realm of manufacturing and precision work, bevel widths play a critical role in shaping and finishing a variety of materials. From metalworking to carpentry, bevel widths help define the detailed contours of a product, and can significantly influence the final aesthetics and functionality of an item. The question thus arises: what types of bevel widths can be requested in custom services? This article aims to explore this query in detail, providing a comprehensive understanding of the subject matter.
The first section of the article, “Understanding Different Types of Bevel Widths,” will delve into the different terminologies and types of bevel widths available, helping readers discern their distinctive characteristics and applications. Following this, “Custom Bevel Width Services: An Overview,” will provide a panoramic view of the services that offer custom bevel widths, including the sectors they cater to and the level of customization they can provide.
Moving forward, the article will tackle “Specifications Required for Custom Bevel Widths,” outlining the information customers need to provide to obtain the desired results. The fourth section, “Factors Influencing the Choice of Bevel Widths,” will delve into considerations such as material type, intended use, and aesthetic preferences that can affect the selection of bevel widths.
Finally, the article will conclude with “Limitations and Challenges in Requesting Custom Bevel Widths,” discussing potential hiccups customers might encounter when requesting customized services. Through this comprehensive exploration, the article aims to equip readers with the knowledge to navigate the world of custom bevel widths effectively.
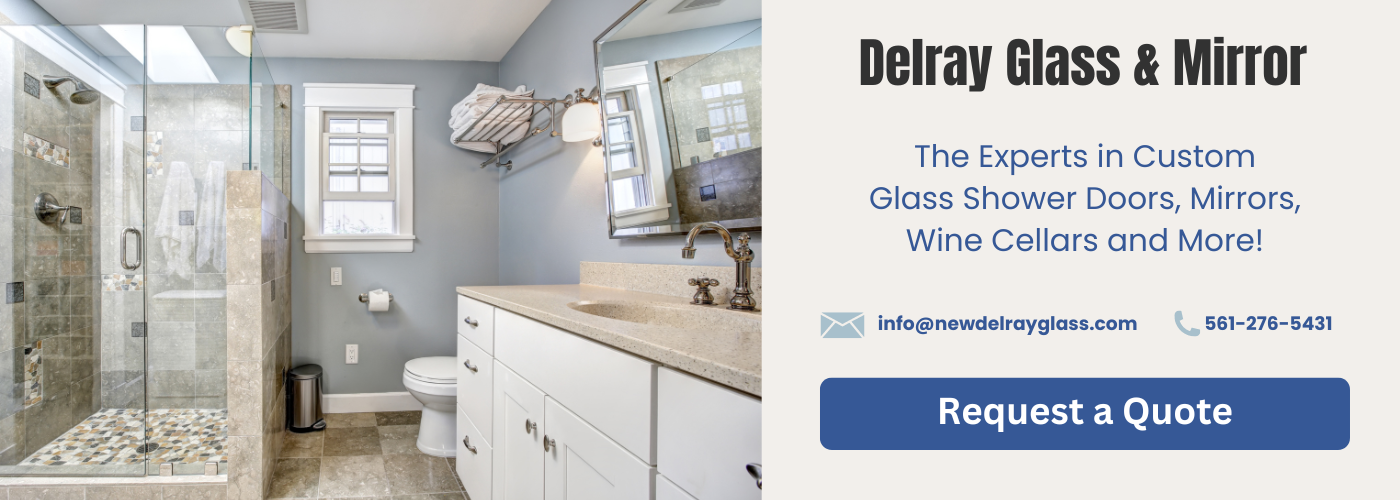
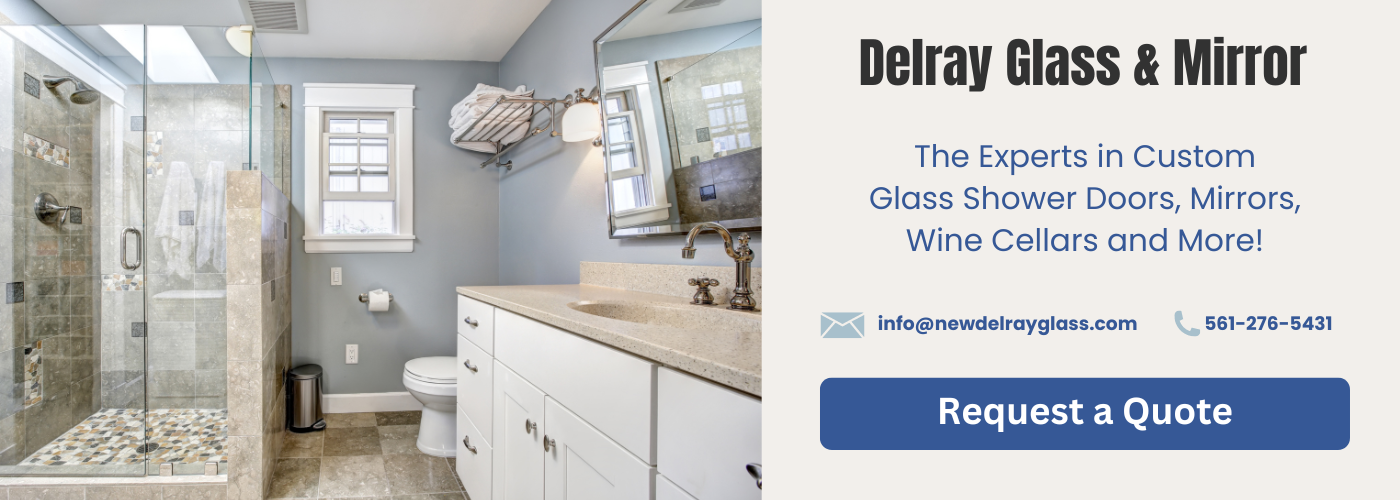
Understanding Different Types of Bevel Widths
In the world of manufacturing and design, the term “bevel” refers to the edge of a structure that is not perpendicular to the faces of the piece. The bevel width, therefore, is the measurement of this edge. Understanding different types of bevel widths is crucial in various industries, especially in fields like construction, where the bevel width can significantly affect a structure’s stability and performance.
There are several different types of bevel widths, with each one being suitable for different applications. For instance, narrow bevel widths are often used in fine woodworking and furniture making due to their ability to create precise, delicate joints. On the other hand, wider bevel widths are more common in heavy-duty applications like metalworking and construction, as they provide a more substantial, stronger connection.
Another type of bevel width is the variable-width bevel, which, as the name implies, can vary in width. This type is particularly beneficial when working with materials of varying thickness, as it allows for a consistent angle regardless of the material’s size.
Understanding these different types of bevel widths and their applications is the first step in requesting custom services. By knowing what you need and how it will impact your project, you can make informed decisions and achieve the best results.
Custom Bevel Width Services: An Overview
Custom Bevel Width Services offer a unique solution for various industrial applications. These services are a subcategory of beveling, which is an essential process in welding and metalworking industries. Beveling creates an angled surface to the edge of a workpiece, and the size of this angle is referred to as the ‘bevel width’. It is used to prepare the metal pieces for welding or other processes that require a specific edge shape.
In the realm of custom services, the bevel width can be tailored to suit the specific needs of a project or application. This degree of customization can greatly enhance the efficiency and quality of the final product. The width of the bevel plays a significant role in the strength, stability, and appearance of the welded joint, making it a critical factor in many industrial applications.
The custom bevel width services can cater to a wide range of material types, including various metals and alloys. Whether it’s a small-scale project or a large industrial operation, these services can provide precise beveling solutions. They employ advanced machinery and skilled technicians to ensure the bevel widths are accurate and consistent, thereby ensuring optimal performance of the final product.
To avail of these custom services, one would need to provide the specifications of the required bevel width, the type of material, and other relevant details. The service providers would then use this information to create the desired bevel width, ensuring that it meets the specific needs of the client and the project at hand.
However, as with any custom service, there can be limitations and challenges. These can include restrictions on the possible bevel widths that can be achieved, the types of materials that can be handled, and the accuracy and consistency of the beveling process. It’s essential to communicate with the service provider to understand these factors and ensure the custom bevel width services will meet your project’s needs.
Specifications Required for Custom Bevel Widths
The third item on the list, “Specifications Required for Custom Bevel Widths,” is a crucial aspect to understand when requesting custom services related to bevel widths. These specifications are paramount to ensuring the final product meets the specific needs and requirements of the customer. To adequately request a specific bevel width, one must fully understand the desired application, as the bevel width can greatly influence the effectiveness and functionality of the final product.
The specifications required typically include the desired bevel angle, the material thickness, and the type of material. The bevel angle is usually determined based on the specific application. For instance, a wider bevel may be required for thicker materials to ensure a solid joint, while a narrower bevel may be more appropriate for thinner materials.
The material thickness is another critical specification. The thickness of the material often determines the appropriate bevel width. Thicker materials usually require a wider bevel to ensure the bevel reaches the full depth of the material.
Lastly, the type of material can significantly influence the bevel width. Different materials have different properties, such as hardness and brittleness, which can affect the appropriate bevel width. For example, harder materials may require a wider bevel to prevent chipping or cracking.
In conclusion, the specifications required for custom bevel widths are critical to achieving the desired results. Understanding these specifications and how they influence the final product can greatly enhance the effectiveness and quality of the final product.
Factors Influencing the Choice of Bevel Widths
When it comes to the choice of bevel widths in custom services, several factors come into play. The selection of a bevel width is not random, but rather, it is largely influenced by specific needs and requirements.
One of the major factors is the type of material being worked on. Different materials require different bevel widths. For instance, a thicker material may need a wider bevel to ensure a strong joint while thinner materials may require narrower bevels. Another factor to consider is the intended use of the finished product. If the product is meant to bear heavy loads or experience high stress, a wider bevel might be necessary to ensure a more robust joint.
The type of welding process also plays a significant role in the choice of bevel widths. Certain welding processes work better with wider bevels, while others may require a narrower bevel for optimal results. Furthermore, the skill and experience of the welder can also influence the choice of bevel widths. More experienced welders may be able to work with a wider range of bevel widths, providing more flexibility in the design process.
Lastly, cost can influence the choice of bevel widths. Wider bevels require more material to fill the joint and can also increase the time and labor needed for the welding process. Therefore, in a bid to reduce costs, a narrower bevel width may be chosen.
Overall, the choice of bevel widths in custom services is a complex decision that involves considering various factors and requirements.
Limitations and Challenges in Requesting Custom Bevel Widths
When it comes to requesting custom bevel widths, there are certain limitations and challenges that one must be aware of. These limitations can often be attributed to the technical constraints of the machinery and software used in the manufacturing process. The precision of the machinery, the capabilities of the software, and the expertise of the operator can all play a significant role in determining the level of customization that can be achieved.
One significant challenge in requesting custom bevel widths is the potential for increased cost. As the level of customization increases, so too does the complexity of the manufacturing process, which can lead to increased costs. This is particularly true if the custom bevel width requested is outside of the standard ranges typically offered by manufacturers.
Another challenge is the potential for increased lead times. Customizing the bevel width can require additional setup time, and may also require additional testing and quality assurance checks to ensure that the final product meets the customer’s specifications.
It’s also important to consider that not all materials are suitable for all types of bevel widths. Some materials may be too brittle or not strong enough to support a particular bevel width, while others may not produce the desired aesthetic or functional results when shaped into a certain bevel width.
Despite these potential limitations and challenges, with careful planning and understanding of the manufacturing process, it is often possible to achieve the desired custom bevel width. It’s important to communicate clearly with the manufacturer about your requirements and to understand the potential implications of your request, in order to ensure that the final product meets your expectations.