Mirrors, though seemingly simple, are the result of complex manufacturing processes and careful material choice. One of the most intriguing types of mirrors is the floating mirror, aptly named for the unique process by which it is made. A significant factor in the creation of these mirrors is the type of glass used, the most notable being float glass. This article aims to delve into the specifics of the materials and techniques used in floating mirror production, primarily focusing on the question: What types of glass are used for floating mirrors?
The first section of this article will explore the different types of glass commonly employed in mirror-making. It will provide an in-depth understanding of the various kinds and their unique characteristics contributing to the mirror-making process. Following this, we will delve into the specific properties of float glass, a type of glass that’s predominantly used for mirrors. This section will detail the unique features that make float glass an ideal choice for mirror production.
Next, we shall examine the process of manufacturing floating mirrors, highlighting the intricacies of the production process, and how float glass is transformed into a highly reflective, pristine mirror. The fourth section will discuss the advantages and disadvantages of using float glass for mirrors, providing a balanced view of its practicality and potential drawbacks in different settings.
Finally, the article will conclude with a discussion on the alternatives to float glass in mirror production. This section will broaden the perspective by introducing other materials used in mirror production, offering a comprehensive understanding of this fascinating topic. Join us as we reflect on the world of floating mirrors and the materials that bring them to life.
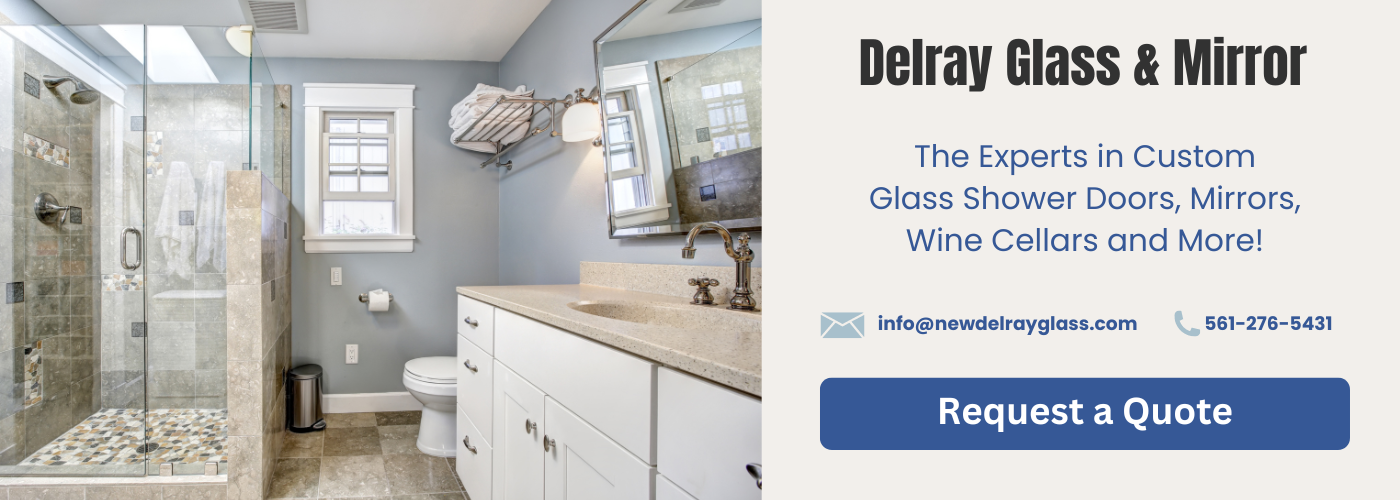
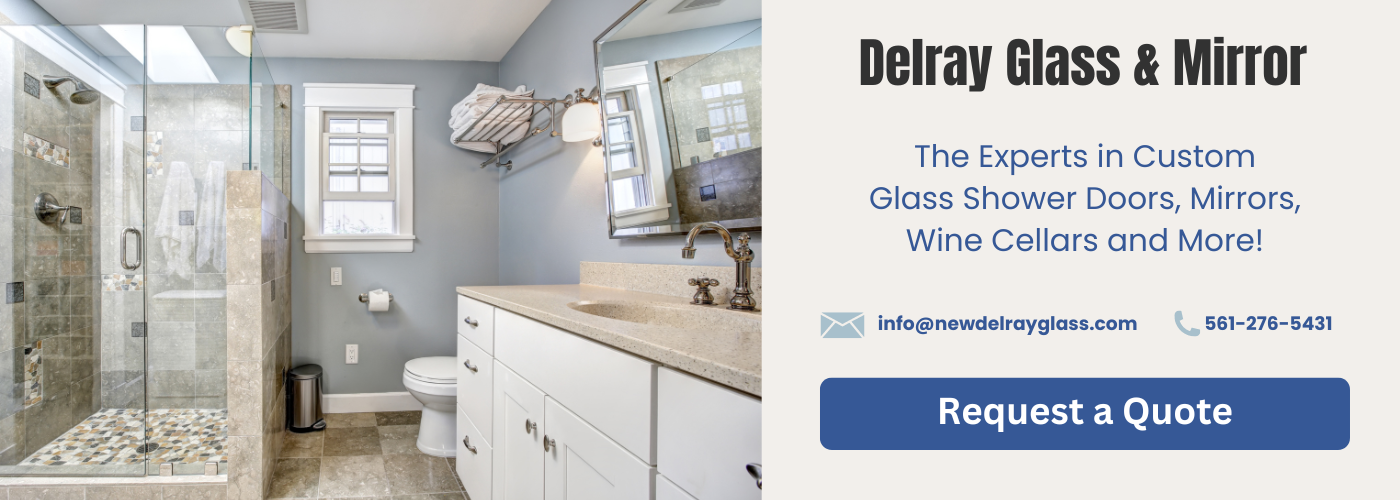
Different Types of Glass Used in Mirror-Making
When discussing the types of glass used for floating mirrors, the first subtopic to consider is the different types of glass used in mirror-making. Mirrors are not just a piece of glass; they are a result of a precise and delicate process that involves several materials. The type of glass used in mirror-making plays a significant role in the mirror’s overall quality, durability, and functionality.
There are various types of glass that can be used to make mirrors, including float glass, low-iron glass, and safety glass. Float glass, named for the method used in its production, is the most common type of glass used. It is renowned for its excellent optical qualities, making it ideal for creating clear and distortion-free mirrors.
Low-iron glass, sometimes referred to as ultra-clear glass, is another type of glass used in mirror-making. It provides a higher degree of transparency than float glass, making it an excellent choice for decorative mirrors or applications where maximum clarity is required.
Safety glass, which includes tempered and laminated glass, is also used in mirror-making. This type of glass is designed to break into small, circular pieces instead of sharp shards, making it a safer choice for use in mirrors.
Each type of glass has its own unique properties, advantages, and disadvantages, making the choice of glass crucial in the mirror-making process. The type of glass used ultimately affects the mirror’s quality, longevity, and safety. Therefore, understanding the different types of glass used in mirror-making is an essential aspect when considering the types of glass used for floating mirrors.
Specific Properties of Float Glass for Mirrors
Float glass, also known as annealed glass, is a type of glass that has unique properties making it an ideal choice for mirror production. It is named for the process of its creation, where molten glass is floated on a bed of molten metal, typically tin. This process results in a glass that is perfectly flat and uniform in thickness, properties that are crucial for the creation of mirrors.
The first defining characteristic of float glass is its exceptional flatness. This flatness is critical in mirror production, as any irregularities in the surface of the glass can cause distortions in the reflected image. By using float glass, manufacturers can ensure that their mirrors will provide a true and accurate reflection.
Another key property of float glass is its uniform thickness. In mirror production, a consistent thickness is important for maintaining a consistent reflectivity across the entire surface of the mirror. With float glass, manufacturers can ensure that their mirrors have a consistent thickness, leading to a uniform reflectivity and a high-quality end product.
In addition, float glass is highly versatile. It can be easily cut into different shapes and sizes, making it suitable for a wide range of mirror designs. It can also be treated in various ways, such as by adding a reflective coating or by tinting, to create mirrors with different aesthetic properties.
In conclusion, the properties of float glass make it an ideal choice for mirror production. Its exceptional flatness, uniform thickness, and versatility are all crucial for creating mirrors that are both functional and aesthetically pleasing.
Process of Manufacturing Floating Mirrors
The process of manufacturing floating mirrors is incredibly interesting and requires a great deal of precision and expertise. It begins with the production of float glass, which is done by literally floating molten glass on a bed of molten metal – usually tin. This process gives the glass its name and also ensures that it is perfectly flat and smooth, which is essential for mirror production.
Once the float glass has been produced, it is then coated with a reflective material to create the mirror. This is typically done through a process known as sputtering, where a thin layer of metal – usually aluminum or silver – is applied to one side of the glass. The metal layer is extremely thin, often just a few nanometers thick, and it is this that gives the mirror its reflective properties.
After the metal layer has been applied, a protective coating is then added to protect the metal from oxidation and other forms of damage. This is usually a layer of paint or some other form of protective material, and it is applied to the back of the mirror (i.e., the side with the metal coating). Once this protective layer has dried, the mirror is then ready for use.
Overall, the process of manufacturing floating mirrors is a complex one that requires a great deal of skill and precision. It involves several stages, each of which must be completed perfectly to ensure that the final product is of the highest possible quality. However, when done correctly, the result is a mirror that is incredibly clear and reflective, making it perfect for a wide range of applications.
Advantages and Disadvantages of Using Float Glass for Mirrors
Float glass is a type of glass that is highly favored for mirror production due to its flat, smooth surface, and optical clarity. This type of glass is produced through a process called the “float glass process,” which involves floating molten glass on a bed of molten tin. This process ensures the glass has uniform thickness and a flat, distortion-free surface, making it ideal for mirror production.
One of the main advantages of using float glass for mirrors is its superior quality. Float glass offers excellent light transmission and a high degree of optical clarity. This means that mirrors made from float glass can provide clear and accurate reflections, making them ideal for applications where precision is required, such as in bathrooms, dressing rooms, and gyms, among others. Additionally, float glass is highly adaptable and can be easily cut, beveled, or shaped to fit a variety of designs and specifications.
However, using float glass for mirrors also has a few disadvantages. One of the main disadvantages is its fragility. Despite its superior quality and optical clarity, float glass is relatively brittle and can shatter easily, posing a risk of injury. This makes it less suitable for applications where safety is a concern, such as in children’s rooms or public spaces. Additionally, mirrors made from float glass can be quite heavy, making them difficult to install and requiring sturdy wall support.
In conclusion, while float glass offers several advantages in terms of quality and optical clarity, its fragility and weight can also pose challenges in certain applications. Therefore, it is essential to consider these factors when choosing the type of glass for mirror production.
Alternatives to Float Glass in Mirror Production
Alternative materials to float glass in mirror production are increasingly being explored due to various factors such as cost, environmental impact, and specific application requirements. These alternatives can significantly affect the quality, performance, and aesthetic appeal of mirrors.
One such alternative is acrylic, a type of plastic that is lighter and more shatter-resistant than glass. Acrylic mirrors are often used in applications where safety and weight are critical factors, such as in children’s toys, gymnasiums, or in vehicles. However, they are more prone to scratches and don’t offer the same clarity as glass mirrors.
Another option is polycarbonate, a robust and impact-resistant material. Much like acrylic, it’s lighter and safer than glass, but it tends to be more expensive. It’s often used in demanding environments where durability and resistance to breakage are essential, such as in security mirrors or industrial settings.
Aluminium mirrors are another alternative. They consist of a sheet of polished aluminium with a reflective coating. These mirrors are highly durable and resistant to oxidation, making them suitable for outdoor use or in harsh environments.
In conclusion, while float glass remains the standard material for mirror production due to its excellent reflectivity and clarity, there are several viable alternatives available. Each of these alternatives has its own set of advantages and limitations, and the choice between them depends on factors such as cost, application, safety, and aesthetic preferences.