In the intricate world of manufacturing, the process of glass cutting holds a significant position due to its widespread applications, ranging from construction to electronics, and even in the art niche. However, achieving precision and maintaining quality in glass cutting is an art in itself, requiring sophisticated techniques and rigorous quality assurance processes. This article seeks to explore the fundamental aspects of these quality assurance processes in glass cutting.
Firstly, we will delve into the rudimentary aspects of glass cutting, providing a comprehensive overview of the process and its various facets. This will create a strong foundation for understanding the subsequent topics. The second section will elucidate the importance of quality assurance in glass cutting, underscoring why maintaining high standards is not just beneficial, but essential.
Moving on, we will discuss the different techniques employed for quality assurance in this field. This section will focus on the various methods used by industry professionals to ensure top-notch quality in their glass cutting processes. Following this, we will examine the tools and equipment integral to quality assurance in glass cutting. This will give readers a glimpse of the hardware necessary to achieve precision and maintain quality in this intricate process.
Lastly, we will review case studies and best practices in the realm of quality assurance for glass cutting. This segment will provide real-world examples and industry-leading practices, giving readers valuable insights into the practical application of the principles discussed. By the end of this article, you will have a well-rounded understanding of the quality assurance processes in glass cutting, and the pivotal role they play in various industries.
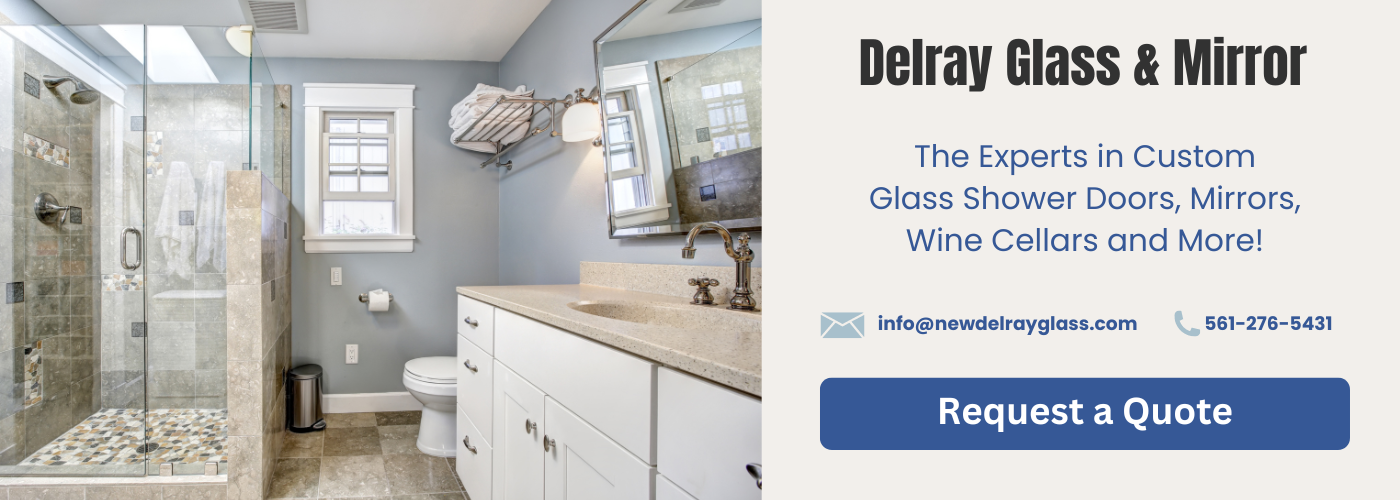
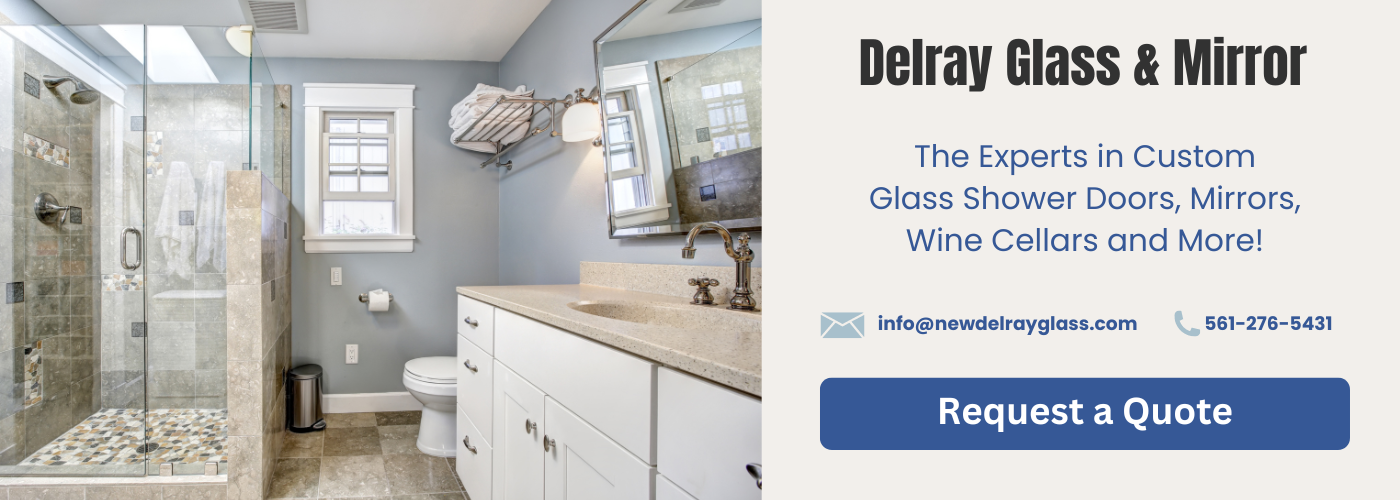
Understanding the Basics of Glass Cutting
Understanding the basics of glass cutting is the first step in the quality assurance process for this material. Glass cutting is a specialized process that requires precision and knowledge of the material. The process involves scoring the glass with a small wheel or diamond, then applying pressure to the glass to break it along the scored line. There are several different methods of glass cutting, each suitable for different types of glass and intended outcomes.
The quality of the cut is determined by a variety of factors, including the skill of the worker, the quality of the tools used, and the type of glass being cut. For instance, tempered glass, which is heat-treated to increase its strength, is more difficult to cut than standard annealed glass. Thus, understanding the properties of different types of glass is crucial to achieving a high-quality cut.
Quality assurance in glass cutting is a systematic approach to ensuring that the finished product meets the desired standards. This includes inspecting the glass before and after cutting, using appropriate tools and techniques, and continually refining the process based on feedback and results. A deep understanding of the basics of glass cutting is crucial for effectively implementing and maintaining these quality assurance processes.
Just as a strong foundation is key to a sturdy building, a comprehensive understanding of the fundamentals of glass cutting is essential to ensure the quality of the final product. It is the bedrock upon which all other quality assurance processes are built, making it an indispensable part of the field.
Importance of Quality Assurance in Glass Cutting
Quality Assurance (QA) plays a pivotal role in the glass cutting industry. It is a proactive process designed to ensure that all glass products meet the predetermined standards of quality, safety, and performance. The focus of QA in glass cutting is to prevent defects, rather than just identifying and correcting them. This ensures that the final product is free from any flaws and defects that might compromise its quality, safety, or function.
The glass cutting process is complex and requires a high level of precision. Any errors in the cutting process can lead to imperfections in the final product, which can then lead to product failure. Therefore, it is of paramount importance that every stage of the glass cutting process is closely monitored and controlled to ensure the highest quality of the final product.
Quality Assurance in glass cutting involves several processes, such as inspecting the raw materials, monitoring the cutting process, and conducting final inspections of the finished product. These processes help to identify any potential issues early on and take corrective action before the product is finalized.
Moreover, regular QA checks help to reduce wastage by minimizing the production of defective products. They also help to boost customer satisfaction by ensuring that the products delivered are of the highest quality. Thus, the importance of Quality Assurance in the glass cutting industry cannot be overstated. It is an integral part of the production process that helps to maintain the high standards of quality that are expected in this industry.
Different Techniques for Quality Assurance in Glass Cutting
The quality assurance process for glass cutting involves diverse techniques to ensure the glass is cut precisely and safely. The primary objective of these techniques is to ensure the optimal quality of the final product and to minimize both material waste and potential hazards during the cutting process.
One commonly used technique is the use of computer-controlled technology. This technology aids in making precise cuts while minimizing human error. It also ensures that the glass is cut to the exact specifications, thereby guaranteeing that the final product meets the desired quality standards and customer expectations.
Another technique is the visual inspection of the cut glass. This is often performed by trained quality assurance personnel who meticulously inspect each piece of cut glass for any imperfections such as cracks, chips, or uneven edges. They also verify the accuracy of the dimensions and shapes based on the given specifications.
A third technique involves the use of specialized tools and equipment to test the durability and strength of the cut glass. These tests are designed to mimic the conditions that the glass will be subjected to in its intended environment. Failing these tests indicates that the glass may not stand up to real-world use, and adjustments are then made to the cutting process to improve the product quality.
In conclusion, quality assurance in glass cutting is a comprehensive process that involves a combination of modern technology, visual inspections, and physical tests. These techniques work hand in hand to ensure that the final product meets or even exceeds the required standards. This not only guarantees customer satisfaction but also contributes to the overall efficiency and profitability of the glass cutting industry.
Tools and Equipment Used for Quality Assurance in Glass Cutting
Tools and equipment play an integral role in the quality assurance process for glass cutting. The utilization of the right tools ensures that the glass is cut precisely and accurately, significantly reducing the likelihood of errors or defects. These tools range from traditional hand tools to advanced, computer-controlled machinery.
Manual tools like glass cutters, pliers, and breaking grozers are essential for making precise cuts and modifications. These tools allow for a high degree of control, especially when working with complex designs. However, their effectiveness largely depends on the skill and experience of the operator.
Computer-controlled machinery, on the other hand, provides a higher degree of precision and consistency, especially for large-scale or repetitive cuts. These machines, such as CNC (Computer Numerical Control) glass cutters and waterjet cutters, use digital templates to make exact cuts. This eliminates the possibility of human error and ensures consistent results across multiple pieces of glass.
In addition to cutting tools, quality assurance in glass cutting also involves various inspection and measurement equipment. Tools like vernier calipers and micrometers are used to measure the dimensions of the glass to ensure they meet the specified requirements. Furthermore, optical inspection systems can be used to check for any defects or irregularities in the glass.
Overall, the tools and equipment used for quality assurance in glass cutting are as diverse as they are essential. They play a significant role in ensuring that the final product meets the highest standards of quality and precision. Without them, the quality assurance process would be incomplete and less effective.
Case Studies and Best Practices in Quality Assurance for Glass Cutting
Case studies and best practices in quality assurance for glass cutting provide vital insights and practical examples of how quality assurance processes work in the field. They offer concrete instances of how companies and industries implement quality assurance measures, the challenges they face, and how they overcome them.
In the world of glass cutting, quality assurance is paramount. Glass is a material that requires precision and consistency in its handling. Any deviations or inconsistencies can lead to defects, which can compromise the integrity of the finished product. Therefore, understanding and implementing best practices in quality assurance for glass cutting is vital.
Case studies provide live examples of these practices in action. They detail the methodologies used by companies, their implementation, the monitoring processes, and the results achieved. These can offer invaluable lessons to other businesses in the same field. They provide a roadmap that others can follow or adapt to their specific needs.
Best practices, on the other hand, are tried and tested strategies that have proven to be effective. They represent the most efficient way of achieving quality assurance in glass cutting. These practices can range from the use of specific cutting tools and equipment, adhering to certain safety measures, regular staff training, to systematic inspection and testing procedures.
By studying and implementing these case studies and best practices, businesses involved in glass cutting can ensure a high level of quality assurance. This will not only guarantee the production of high-quality glass products but also enhance the company’s reputation and customer satisfaction.