When undertaking any form of installation, whether it be in a home, office, or industrial environment, ensuring the health and safety of those involved is paramount. Overlooking safety measures can lead to serious injuries or even fatalities, along with potential legal and financial consequences. This importance of safety necessitates a holistic approach, covering everything from the basic use of Personal Protective Equipment (PPE) to more specific precautions like electrical and chemical safety. This article aims to explore the essential health and safety precautions to consider during installation processes to protect all personnel involved.
Firstly, we will delve into the significance of Personal Protective Equipment (PPE), which serves as the first line of defense against potential hazards. Next, the focus will shift to tool and equipment safety, emphasizing the importance of using the right tools in the right way to prevent accidents. Electrical safety is another critical area, especially given the high risks associated with working with or near electrical systems. Chemical safety will also be discussed, highlighting the need for proper handling, storage, and disposal methods to avoid harmful exposures. Lastly, ergonomics and handling safety will be examined to prevent physical strains and injuries that frequently occur from poor handling techniques and ergonomically unsound practices. By covering these subtopics, the article will provide a comprehensive guide to ensuring safety during any installation process.
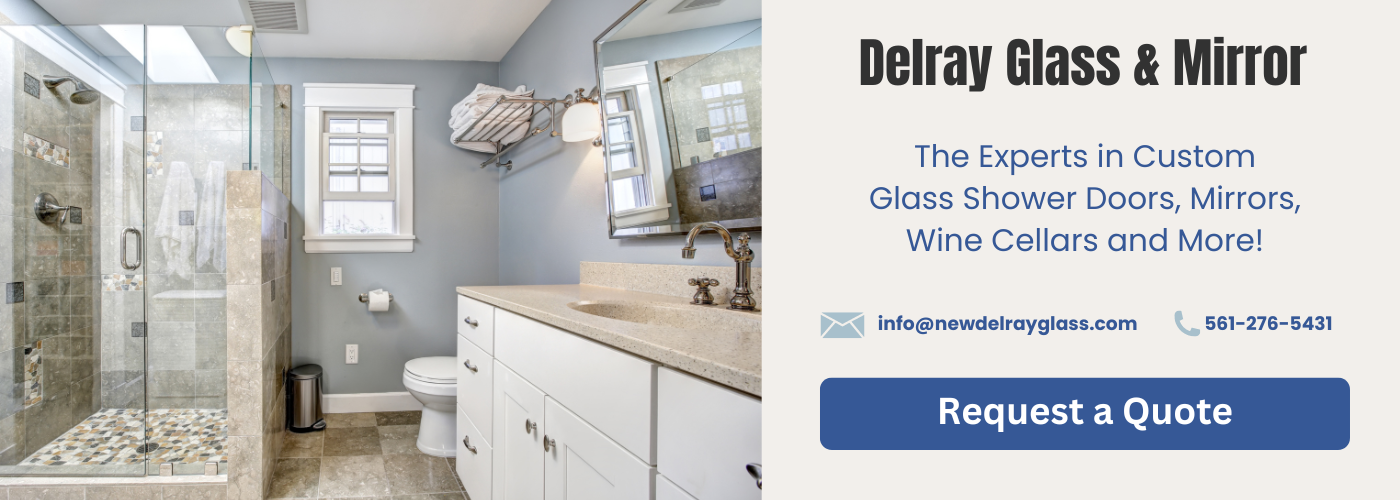
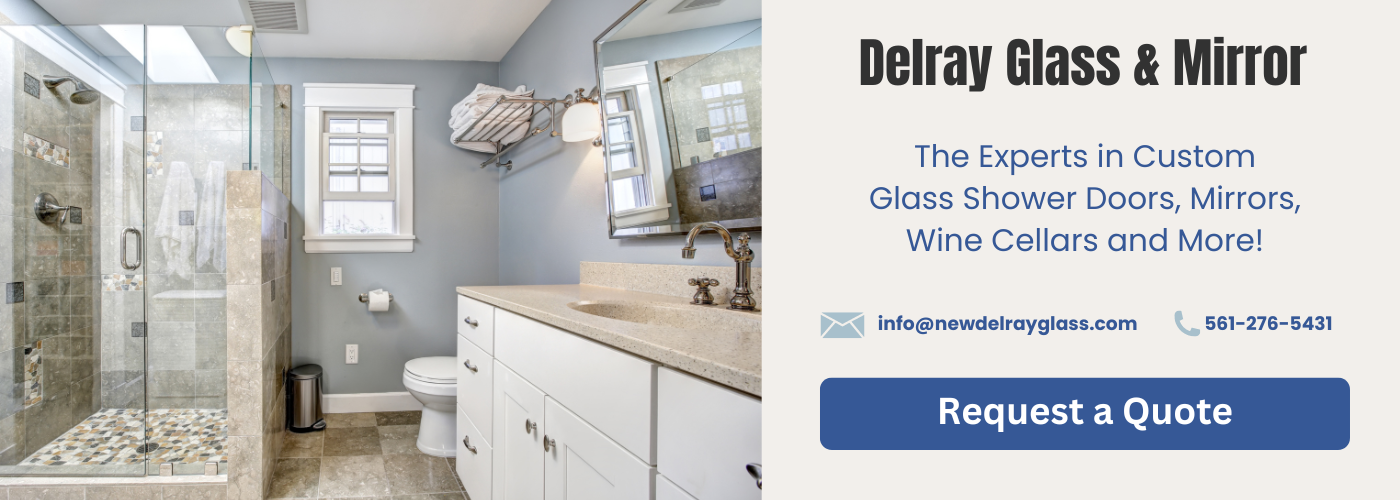
Personal Protective Equipment (PPE)
Personal Protective Equipment (PPE) is crucial for ensuring the health and safety of individuals during the installation of various systems or during construction activities. PPE refers to protective clothing, helmets, goggles, or other garments or equipment designed to protect the wearer’s body from injury or infection. The hazards addressed by protective equipment include physical, electrical, heat, chemicals, biohazards, and airborne particulate matter.
Wearing the correct PPE is essential when performing tasks that could potentially expose workers to risks. For example, helmets are vital for protecting against head injuries, and safety goggles are necessary to shield the eyes from flying particles or harmful substances. Similarly, protective gloves can prevent injuries to the hands from sharp objects, chemicals, or heat.
The importance of PPE extends beyond mere protection from physical injuries; it also plays a critical role in minimizing the risk of long-term health issues caused by exposure to harmful substances or environments. For instance, respiratory protective equipment is crucial for those working in environments with dust, vapors, or hazardous gases.
Employers are responsible for providing the appropriate PPE to their employees and ensuring that they are trained on how to use it correctly. Regular training and maintenance are key to ensuring that PPE provides the maximum possible protection. This involves regular inspections and replacement of worn or damaged equipment, as well as ongoing training on the proper use and limitations of the equipment provided.
In conclusion, Personal Protective Equipment is an essential aspect of workplace safety that protects employees from a wide range of hazards during installation processes. Ensuring that all workers are equipped with the appropriate PPE and understand how to use it effectively helps to prevent injuries and maintain a safer working environment.
Tool and Equipment Safety
Tool and equipment safety is a critical aspect of any installation process, especially in industries where the use of heavy machinery and tools is frequent. Ensuring that all tools and equipment are in good working order is the first step towards minimizing the risk of accidents. This includes regular maintenance checks and the immediate repair or replacement of any faulty equipment.
It is also important for workers to be properly trained on the use of each tool and piece of equipment. This training should cover not only the correct way to use the equipment but also the potential risks associated with its use. Workers should be made aware of the importance of using the right tool for the job to prevent misuse, which can lead to accidents.
Additionally, safety measures such as guarding or protective barriers should be used to protect workers from the moving parts of machinery. For tools that pose a high risk, such as those that generate sparks or involve high temperatures, additional precautions should be taken to prevent fire hazards and burns.
Implementing a systematic approach to tool and equipment safety can significantly reduce the likelihood of accidents during the installation process. This approach should include regular safety audits and feedback sessions where workers can discuss potential safety issues and suggest improvements. By fostering an environment where safety is a priority, businesses can ensure that their operations run smoothly and that their employees are protected from harm.
Electrical Safety
Electrical safety is a critical aspect of health and safety precautions during installation processes, especially in environments where electrical systems and components are being installed or maintained. Ensuring electrical safety helps prevent accidents such as electric shocks, burns, and other serious injuries, or even fatalities. It also minimizes the risk of fires caused by faulty electrical equipment or wiring.
One of the primary measures in ensuring electrical safety is the strict adherence to electrical codes and standards that are often set by national or international regulatory bodies. These guidelines are designed to ensure that all electrical installations are done safely and competently. It is crucial for workers to be trained and aware of these standards to conduct their work safely.
In addition to complying with standards, the use of proper personal protective equipment (PPE) is essential when dealing with electrical installations. This includes insulated gloves and tools, protective eyewear, and flame-resistant clothing. Such equipment provides a first line of defense against electrical accidents.
Regular maintenance and inspection of electrical equipment and installations are also vital. This ensures that any potential hazards are identified and rectified before they can cause harm. Testing equipment should be used to verify that electrical circuits are de-energized before starting work, and lockout-tagout procedures must be followed to ensure that equipment is safely isolated.
Training and awareness are also key components of electrical safety. Workers should receive regular training on the latest safety practices and emergency procedures related to electrical safety. This education helps them recognize potential electrical hazards and understand the best practices for safe electrical installation and maintenance.
Overall, electrical safety is an integral part of the broader scope of health and safety measures in any installation process, particularly in industries reliant on electrical operations. By implementing strict safety protocols, providing adequate training, and using appropriate protective equipment, the risk of electrical accidents can be significantly reduced.
Chemical Safety
Chemical safety during the installation process is crucial to ensure the health and safety of the workers involved. When handling chemicals, it’s important to understand the potential hazards and implement appropriate safety measures to mitigate risks. Chemicals can pose a variety of health risks, including respiratory issues, skin burns, poisoning, and other serious health problems.
First and foremost, proper training is essential. Workers should be educated on the specific chemicals they will be handling, including understanding Material Safety Data Sheets (MSDS), which provide detailed information on the chemicals, their hazards, and how to handle them safely. This knowledge is vital in preventing accidents and ensuring that workers are prepared to handle chemicals properly.
Personal Protective Equipment (PPE) is another critical aspect of chemical safety. Depending on the chemicals being used, appropriate PPE may include gloves, goggles, face shields, respirators, and protective clothing. These items protect workers from chemical splashes, inhalation of vapors, and direct skin contact with hazardous substances.
Furthermore, proper storage and labeling of chemicals are vital to prevent accidents. Chemicals should be stored in clearly labeled, secure containers in designated areas that comply with relevant safety regulations. This helps in avoiding accidental mixing of incompatible chemicals or the misuse of substances, which can lead to dangerous reactions.
Emergency procedures should also be in place and known to all workers. This includes having accessible eyewash stations, shower facilities, and first aid kits tailored to chemical exposure scenarios. Training workers on emergency response procedures ensures a swift and effective reaction in case of a chemical spill or other accidents, potentially saving lives and reducing harm.
In summary, maintaining high standards of chemical safety during installation projects is essential for protecting workers and preventing accidents. Through education, proper use of PPE, careful handling and storage, and well-planned emergency responses, a safe working environment can be ensured during the handling of hazardous chemicals.
Ergonomics and Handling Safety
Ergonomics and Handling Safety are critical components to consider when discussing health and safety precautions during installation processes. Ergonomics, the study of people’s efficiency in their working environment, primarily focuses on designing work tasks, workspaces, controls, displays, tools, lighting, and equipment to fit the employee’s physical capabilities and limitations. Proper ergonomic practices can significantly reduce the risk of musculoskeletal disorders (MSDs), which include ailments such as carpal tunnel syndrome, tendonitis, and lower back injuries. These are common injuries that can occur in various installation jobs where repetitive motion, heavy lifting, or prolonged standing are involved.
Handling safety, closely related to ergonomics, involves the proper techniques for lifting, holding, and moving materials manually or with assistance from machinery. Training in handling safety is crucial to prevent physical injury. This includes teaching workers how to correctly lift heavy items by using their legs rather than their back, or how to use mechanical aids like dollies, forklifts, or hoists. Awareness and application of handling safety can substantially decrease the risk of injuries associated with physical strain.
In installations that require extensive physical activity, such as in construction or manufacturing, implementing ergonomic solutions and handling safety protocols is essential. This might include adjusting the height of workstations, using tools designed to minimize strain, rotating tasks to reduce the duration of repetitive motions, and providing regular breaks to reduce fatigue. Each of these strategies can help create a safer and more productive work environment. By addressing ergonomics and handling safety, organizations can not only protect their workers from injury but also improve overall job satisfaction and performance.