When we think of mirrors, the first image that often comes to mind is a reflective surface that faithfully bounces back our own image. However, the world of custom mirrors is far more versatile, encompassing various types that serve different functional and aesthetic purposes. One intriguing variant is the non-reflective mirror, which may sound contradictory at first. How can a mirror be non-reflective and still be considered a mirror? This question opens up a fascinating discussion about the technology and applications of mirrors designed specifically to reduce glare and reflection. In this article, we will explore the diverse aspects of non-reflective custom mirrors, starting with the range of non-reflective coatings available and their optical properties. We’ll delve into the manufacturing processes that allow for these specialized mirrors to be tailored to specific needs. Additionally, we’ll look at the various applications where non-reflective mirrors are preferred over their glossy counterparts, from artistic installations to functional uses in optical equipment. The cost implications of opting for custom non-reflective mirrors will also be discussed, along with the durability and maintenance considerations that come with choosing such surfaces. This exploration will not only clarify the concept of non-reflective mirrors but also highlight their value and versatility in both everyday and specialized applications.
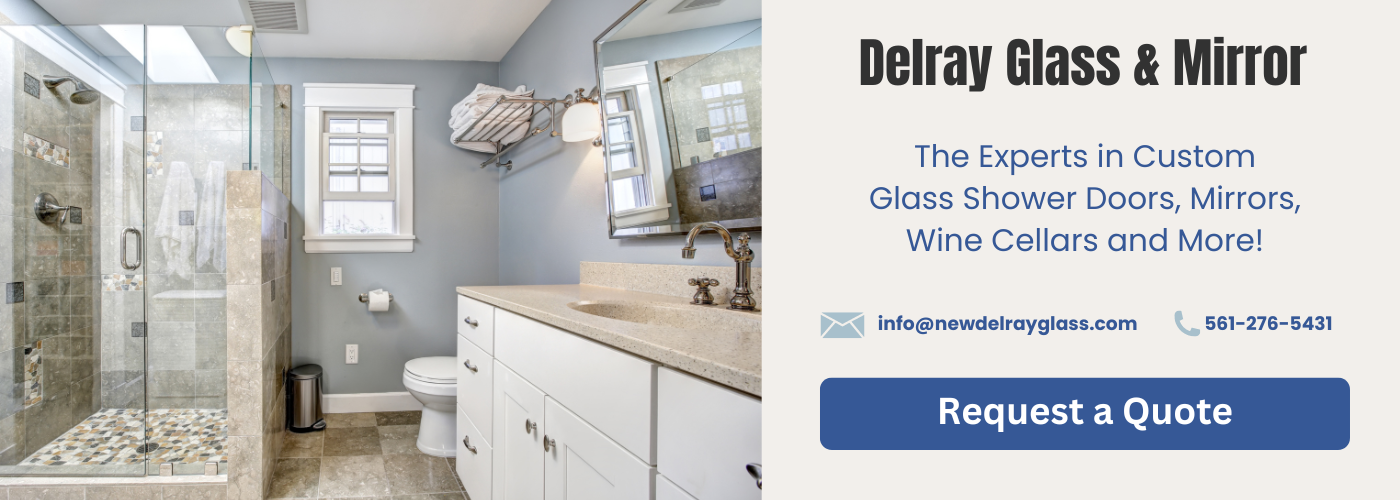
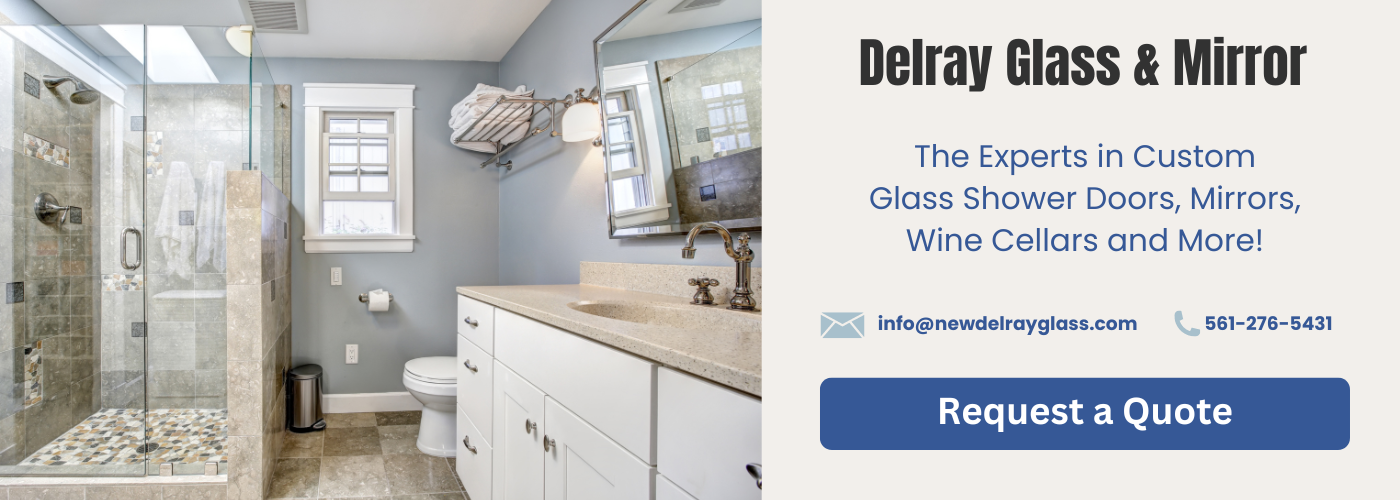
Types of Non-Reflective Coatings
Non-reflective coatings, also known as anti-reflective coatings, are used to reduce glare and reflections on various surfaces, including mirrors. These coatings are particularly beneficial in enhancing the visual clarity and contrast of the reflective surfaces by minimizing the amount of light that reflects off them. The primary purpose of such coatings is to allow more light to pass through the surface, reducing distractions from reflections and making the surface more effective for its intended use.
There are several types of non-reflective coatings, each tailored for specific applications and materials. One common type is the single-layer interference coating, which consists of a single thin layer of a dielectric material. This type is simple but offers limited anti-reflective capabilities and is wavelength-specific. Another type is the multi-layer interference coating, which involves multiple thin layers of different materials. This type is more effective across a broader range of wavelengths and can be engineered to achieve very low reflectivity.
Another category is the graded index coating, which involves a layer whose refractive index gradually changes across its thickness. This type of coating is designed to minimize reflections over a wide range of wavelengths and angles of incidence. Moth-eye coatings, which mimic the nanostructures found on the surface of a moth’s eye, are another innovative type. These structures are excellent at reducing reflections because they gradually bend light into the substrate, minimizing sudden changes in refractive index.
The selection of a non-reflective coating depends on factors such as the substrate material, the operational environment, the required durability, and the specific optical properties needed. Each type of coating has its advantages and is chosen based on the balance between performance requirements and cost constraints. Advances in materials science continue to improve the effectiveness and durability of these coatings, expanding their applications in various industries including optics, automotive, and consumer electronics.
Manufacturing Processes for Custom Mirrors
Custom mirrors, particularly those designed with non-reflective surfaces, are created through specialized manufacturing processes that cater to the specific needs and specifications of the client. These processes involve several key steps, each crucial in ensuring the quality and functionality of the finished product.
The manufacturing process begins with the selection of the base material, which is typically glass or acrylic. The choice of material depends on the application for which the mirror is intended. For instance, acrylic is often chosen for its lightweight properties and shatter resistance, making it suitable for use in environments where safety is a priority.
Once the base material is selected, it undergoes a thorough cleaning process to remove any impurities that might affect the coating’s adherence. After cleaning, the material is ready for the coating process. In the case of non-reflective mirrors, a special anti-reflective (AR) coating is applied. This coating is designed to minimize the amount of light that reflects off the surface of the mirror, reducing glare and allowing for clearer visibility.
The application of the AR coating typically involves advanced techniques such as sputtering or chemical vapor deposition. These methods allow for precise control over the thickness and uniformity of the coating, which is crucial for achieving the desired non-reflective properties. The exact process chosen often depends on the specific requirements of the project, such as the degree of non-reflectivity needed and the environmental conditions in which the mirror will be used.
After the coating process, the mirrors undergo a series of inspections to ensure that they meet the required specifications. Quality control measures include checking for defects in the coating, ensuring the accuracy of the mirror’s dimensions, and verifying that the mirror provides the intended level of reflectivity.
Finally, the mirrors are carefully packed and shipped to the client. Proper packaging is essential to protect the mirrors from damage during transportation, especially given the delicate nature of the non-reflective coatings.
In summary, the manufacturing of custom mirrors with non-reflective surfaces is a detailed and precise process that requires careful consideration of materials, coating techniques, and quality control measures. By understanding and controlling each step of this process, manufacturers can create highly effective non-reflective mirrors tailored to the specific needs of their clients.
Applications of Non-Reflective Mirrors
Non-reflective mirrors, also known as anti-reflective or non-glare mirrors, serve numerous purposes across various industries. These specialized mirrors are designed to reduce glare and reflection, making them ideal for applications where excessive light reflection is undesirable. One of the primary uses of non-reflective mirrors is in the automotive industry, where they are used in rearview and side-view mirrors to enhance visibility during daytime and nighttime driving by minimizing the glare from sunlight and headlights.
In the field of optics and photography, non-reflective mirrors are crucial for reducing glare in situations where precise imaging is required. Photographers and cinematographers use these mirrors to prevent unwanted reflections that could spoil the clarity of an image. Similarly, optical instruments such as telescopes and microscopes often incorporate non-reflective mirrors to improve the accuracy and quality of the visual output.
Another significant application of non-reflective mirrors is in architectural and interior design. These mirrors can be used in spaces such as museums, galleries, and retail stores, where controlling light reflection is essential to enhance the visual presentation of artworks or products. By mitigating glare, non-reflective mirrors help in creating a more viewer-friendly environment, allowing for a better appreciation of displayed items.
Moreover, non-reflective mirrors are increasingly being used in electronic displays such as computer monitors, televisions, and digital signage. These applications benefit from reduced glare, which enhances readability and reduces eye strain for users. This is particularly important in environments with harsh lighting conditions or where devices are used for prolonged periods.
In summary, non-reflective mirrors have a wide range of applications that span across various sectors. Their ability to control and reduce glare not only improves functionality but also enhances safety and visual comfort in many practical scenarios. As technology advances, the demand for such specialized mirrors is likely to increase, reflecting their growing importance in both commercial and technical fields.
Cost Implications of Non-Reflective Custom Mirrors
When considering non-reflective custom mirrors, one of the crucial factors to consider is the cost implications. These mirrors, often used for specific technical or aesthetic purposes, involve more complex manufacturing processes compared to standard mirrors. The production of non-reflective mirrors typically requires the application of special coatings or treatments that reduce reflection. These coatings can include various materials such as anti-reflective (AR) films or multilayer dielectric coatings, which are more expensive to fabricate and apply.
The cost of non-reflective custom mirrors is also influenced by the degree of non-reflectivity required and the size and shape of the mirror. For instance, mirrors with higher demands for non-reflectivity, such as those used in certain optical applications or in galleries and museums where glare reduction is crucial, may require multiple layers of coating, further increasing the cost. Additionally, custom shapes and sizes can result in higher production costs due to the specialized equipment and labor required.
Moreover, the development phase of these mirrors can also contribute significantly to the overall cost. Extensive research and development might be necessary to achieve the desired properties, especially for mirrors used in specialized technical fields. This aspect of production not only impacts the initial cost but might also affect the long-term maintenance and durability of the mirrors, potentially leading to higher overall expenses.
In summary, while non-reflective custom mirrors provide essential benefits in various applications, they come with increased financial considerations that must be evaluated when planning projects that require their use. Understanding these cost implications is vital for budget management and determining the feasibility of using these specialized mirrors in both commercial and artistic ventures.
Durability and Maintenance of Non-Reflective Surfaces
Non-reflective surfaces, particularly in the context of custom mirrors, present unique challenges and considerations in terms of durability and maintenance. These surfaces are treated to minimize glare and reflection, which is particularly beneficial in environments where light control is crucial, such as in galleries, museums, or certain industrial applications. However, the very treatments that reduce reflectiveness can also affect the longevity and resilience of the mirror surfaces.
The durability of non-reflective surfaces largely depends on the type of coating applied. Common non-reflective coatings include anti-reflective (AR) and anti-glare (AG) coatings, which are applied using various techniques like spraying, dipping, or vapor deposition. These coatings are generally thin and can be vulnerable to scratches and wear over time, which necessitates careful handling and cleaning practices.
Maintenance of these non-reflective mirrors typically requires the use of soft, non-abrasive cloths and cleaners specifically designed for treated glass to avoid damaging the coatings. Harsh chemicals and rough materials must be avoided to prevent the coatings from degrading. Furthermore, the environment in which the mirrors are used also plays a significant role in their maintenance schedule. High-humidity environments, for example, might necessitate more frequent cleaning and inspection to prevent degradation of the coating due to moisture.
Overall, while non-reflective surfaces on custom mirrors serve a vital function in reducing glare and reflection, they do require a higher level of care to maintain their effectiveness and aesthetic qualities over time. Proper maintenance regimes, paired with an understanding of the specific characteristics of the surface treatments, are essential for ensuring the longevity of these specialized mirrors.