Glass is an essential component in various sectors, including construction, interior design, and automotive industries. Among the different types of glass, laminated glass stands out for its unique characteristics such as enhanced safety, sound reduction, and UV control. A frequently asked question about laminated glass is, “Can laminated glass be custom cut to any shape?” The simple answer is yes; however, the process involves several intricate procedures, important precautions, and considerations. This article seeks to delve into this topic, providing in-depth knowledge about custom cutting laminated glass.
We will begin by explaining ‘The Process of Custom Cutting Laminated Glass’, providing a step-by-step guide on how laminated glass is shaped to meet specific requirements. Though it’s possible to custom cut laminated glass, there are certain ‘Limitations in Custom Cutting Laminated Glass’ that users should be aware of. This article will further discuss these constraints to give you a clear picture of what can and cannot be achieved.
Cutting laminated glass requires specific tools and techniques. In our section ‘Necessary Tools and Techniques for Cutting Laminated Glass’, we will highlight the essential equipment and methods used in the process. Safety cannot be compromised when handling glass, especially during cutting. Therefore, we will provide a comprehensive guide on ‘Safety Precautions When Cutting Laminated Glass’, ensuring you are well equipped to handle such a task safely.
Finally, we will delve into the ‘Cost Implications of Custom Cutting Laminated Glass’. As with any customized work, there are costs involved, which vary depending on the complexity of the design, size, and other factors. By shedding light on this aspect, we aim to help you make an informed decision regarding custom cutting laminated glass. Whether you are a homeowner, interior designer, or a professional in the construction industry, this article will provide valuable insights into the world of custom cutting laminated glass.
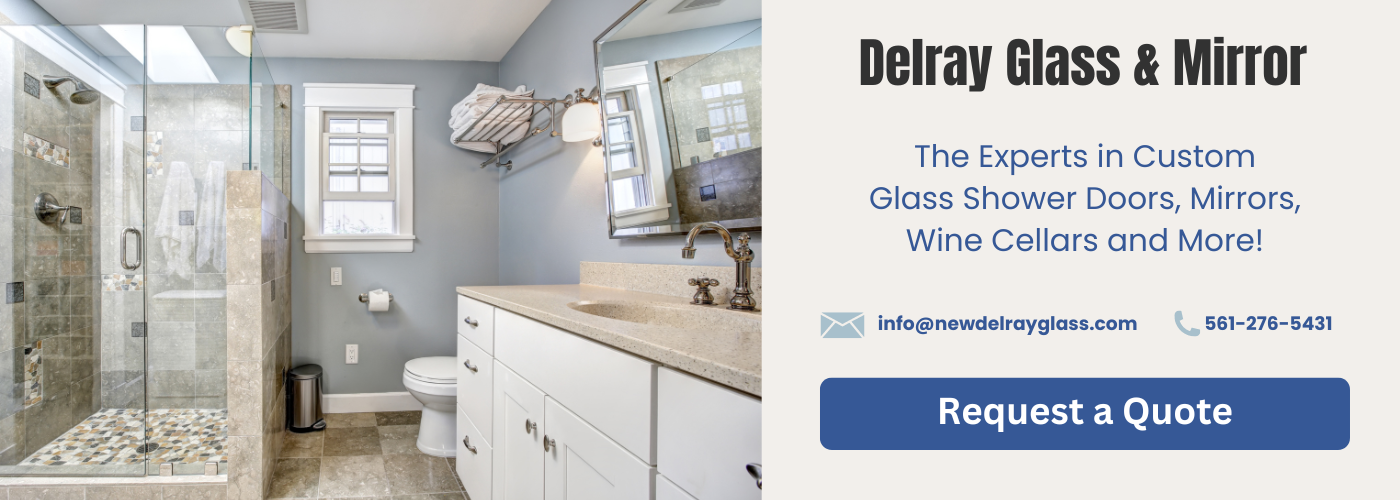
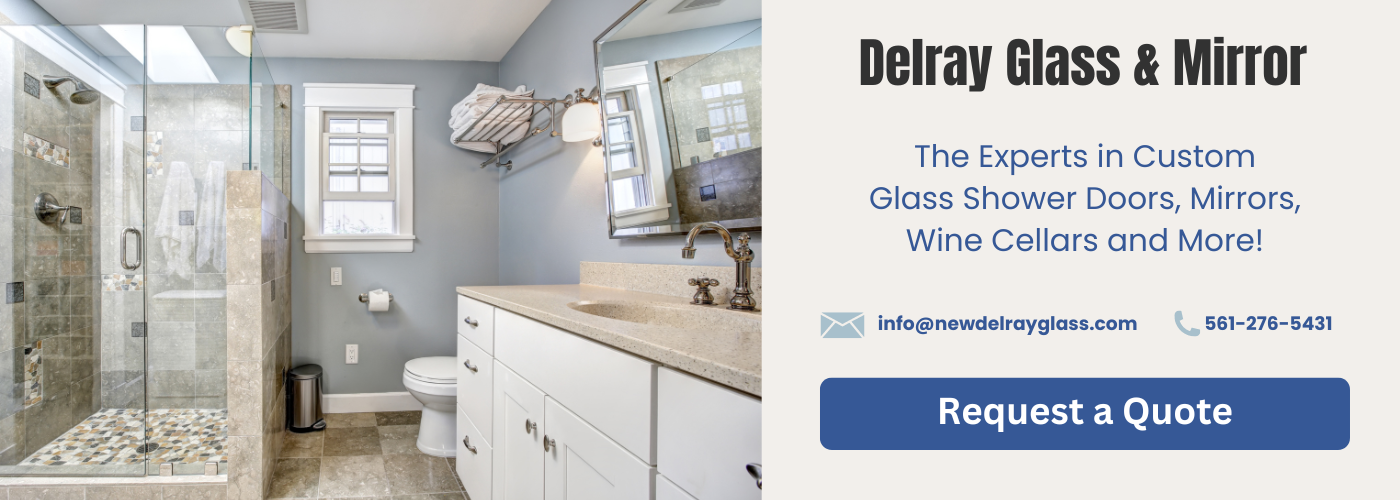
The Process of Custom Cutting Laminated Glass
The process of custom cutting laminated glass is a complex one, requiring precision and skill. Laminated glass, which is made by sandwiching a layer of polyvinyl butyral (PVB) between two layers of glass, is known for its safety features. When cut, it does not shatter into sharp pieces, instead, it tends to stick to the PVB layer. This makes it a preferred choice for applications such as car windshields, skylights, and high-rise buildings.
The process begins with taking accurate measurements of the shape the glass needs to be cut into. This is crucial as any error in measurements can lead to waste of material and increased costs. Once the measurements are taken, the glass is scored using a glass cutter. The scoring should be done on both sides of the glass to ensure a clean cut.
After scoring, the glass is gently broken along the score line. This is done by applying pressure on the glass from underneath the score line. The glass should break easily along the score line. If it does not, it means that the score was not deep enough and the process needs to be repeated.
Next, the PVB layer is cut using a special knife. It is important to cut the PVB layer accurately as it affects the final shape of the glass. Once the PVB layer is cut, the other side of the glass is scored and broken in the same way as the first side.
Finally, the edges of the glass are smoothed using a glass grinder. This removes any sharp edges and ensures that the glass fits perfectly into its intended application. The process of custom cutting laminated glass requires a lot of skill and practice, but when done correctly, it can produce beautiful and safe results.
Limitations in Custom Cutting Laminated Glass
Laminated glass, while versatile and durable, has certain limitations when it comes to custom cutting. The process of custom cutting laminated glass is not as straightforward as cutting regular glass. This is primarily due to the plastic interlayer sandwiched between two layers of glass in laminated glass. The presence of this interlayer can complicate the cutting process and impose certain limitations.
One of the main limitations comes from the complexity of the shapes that can be cut. While it is possible to cut laminated glass into a variety of common shapes, such as rectangles or circles, more complex or intricate shapes may not be feasible. This is because the cutting process needs to be very precise to prevent damage to the glass or the interlayer, and more complex shapes can be harder to cut with such precision.
Another limitation is the thickness of the laminated glass. Thicker laminated glass can be more difficult to cut, and there is a greater risk of cracking or breaking the glass during the cutting process. This is why laminated glass used for custom cutting is often not as thick as regular laminated glass.
The size of the glass piece can also be a limitation. Larger pieces of laminated glass are more challenging to handle and cut, and there is a higher risk of breakage. It can also be more difficult to transport and install larger pieces of custom cut laminated glass.
Despite these limitations, custom cutting of laminated glass is a popular option for many applications, including safety glazing, sound reduction, and UV protection. With the right tools and techniques, many of these limitations can be overcome.
Necessary Tools and Techniques for Cutting Laminated Glass
Necessary tools and techniques for cutting laminated glass play a significant role in the customization process. Laminated glass, known for its safety features and durability, requires special tools and techniques for custom cutting. Unlike regular glass, laminated glass consists of two glass layers bonded together with a plastic interlayer. This composition makes it more complex to cut and shape.
A glass cutter is the primary tool used in cutting laminated glass. This tool etches a score line on the glass surface, which guides the break in the glass. The process requires a steady hand and precise control to ensure the cut follows the desired path. Once the initial cut is made, the glass is then gently tapped from the underside to run the score line, effectively splitting the glass along the marked path. However, given that laminated glass has a plastic interlayer, a special tool known as a power saw or an angle grinder is used to cut through this layer.
Moreover, pliers and running pliers can also be used in breaking the glass after scoring. Sandpaper is essential after the cutting process to smooth the edges of the glass and prevent injury from sharp edges. Running pliers and breaker/grozer pliers are also crucial tools in the process.
The cutting of laminated glass is a skill that requires training and practice. Techniques such as constant pressure when scoring, clean breaking, and proper handling of the cut glass are necessary to ensure the quality of the final product. Furthermore, understanding the properties of laminated glass, like its tendency to chip and the need for extra care during the cutting process, will help create a custom cut piece with the desired shape and size.
Overall, the necessary tools and techniques for cutting laminated glass are a critical factor in producing custom cut laminated glass. They ensure not just the precision of the cut but also the safety of the person performing the task.
Safety Precautions when Cutting Laminated Glass
Safety precautions are paramount when cutting laminated glass, or any glass for that matter, to avoid accidents and injuries. Being a composite material made of layers of glass with an interlayer of plastic, laminated glass poses unique safety concerns which necessitate careful handling.
First, adequate personal protective equipment (PPE) is crucial. This includes safety goggles to protect the eyes from glass shards and chips, heavy-duty gloves to protect the hands from cuts, and a long-sleeved shirt and pants to protect the skin. In some cases, a face shield may also be necessary to protect against flying debris.
In addition to PPE, the work area should be properly prepared. It should be clean and free of any unnecessary items that could cause accidents. The glass should be placed on a stable, flat surface with adequate lighting. It is also advisable to have a first aid kit readily available.
The cutting tools should be in good condition and used correctly. For example, the glass cutter should be held at the correct angle, and the pressure applied should be neither too light nor too heavy. Also, when breaking the glass after scoring, it should be done carefully to avoid shattering the glass.
Finally, proper disposal of glass waste is essential. Glass shards should be swept up immediately and discarded safely. These precautions, while they may seem tedious, are necessary for preventing accidents and ensuring the safety of the person cutting the laminated glass.
Cost Implications of Custom Cutting Laminated Glass
When it comes to custom cutting laminated glass, one of the key considerations is the cost implications. These costs can significantly vary depending on a range of factors, including the complexity of the desired shape, the size of the glass, and the type of lamination used.
For instance, cutting laminated glass into simple shapes like squares or rectangles may be less expensive than creating intricate or irregular shapes, as the latter requires more time, skill, and potentially specialized equipment. Additionally, larger pieces of glass can be more costly to cut than smaller ones due to the increased risk of breakage and the additional manpower required.
The type of lamination can also influence the cost. High-end laminations that offer additional benefits such as enhanced safety features, UV protection, or improved energy efficiency, can increase the overall cost of the custom cutting process.
It’s important to keep in mind that while custom cutting laminated glass can indeed be more expensive than buying pre-cut pieces, it offers the advantage of getting a piece that perfectly fits your specific needs. Therefore, the additional cost can be viewed as an investment in quality and customization.