When it comes to remodeling or constructing a bathroom, custom shower glass can add a touch of elegance and openness to the space. However, given its size, weight, and fragility, the shipping and delivery of custom shower glass are critical components that require careful planning and execution. This article explores the intricacies of how custom shower glass is transported from the manufacturer to the customer’s doorstep, ensuring it arrives in pristine condition, ready for installation.
Firstly, we delve into the packaging materials and methods used to protect the glass during transit. The choice of packaging can significantly influence the safety and integrity of the glass, from sturdy wooden crates to cushioning materials. Next, we consider the various transportation modes employed, from local deliveries via trucks to long-distance shipments using freight services. Each mode of transport comes with its considerations and challenges.
Handling and safety procedures are crucial for preventing damage and ensuring the safety of all personnel involved in the shipping process. We’ll look at the training and techniques that are essential for handling such delicate items. Following that, we examine the delivery and installation services often offered by suppliers or third-party contractors, which can vary widely in terms of scope and quality.
Lastly, the article covers insurance and liability aspects, which are paramount in protecting the financial investment of both the buyer and seller. Understanding these facets helps in mitigating risks associated with the transportation and installation of custom shower glass. From the initial packaging to the final installation, each step in the journey of custom shower glass involves meticulous attention to detail to ensure that it enhances a bathroom with its intended aesthetic and functional benefits.
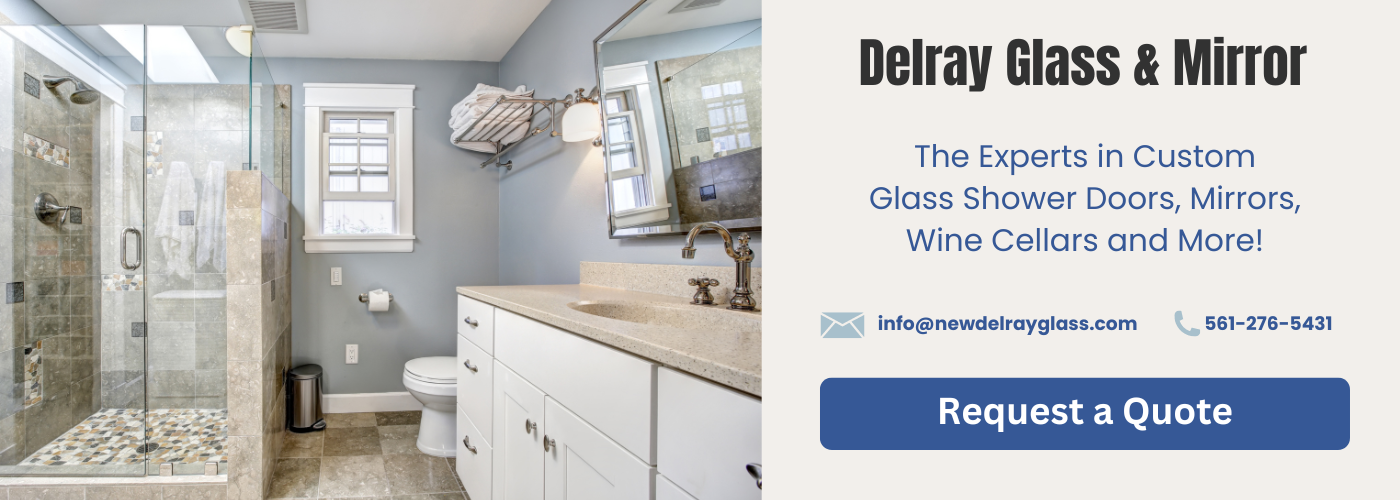
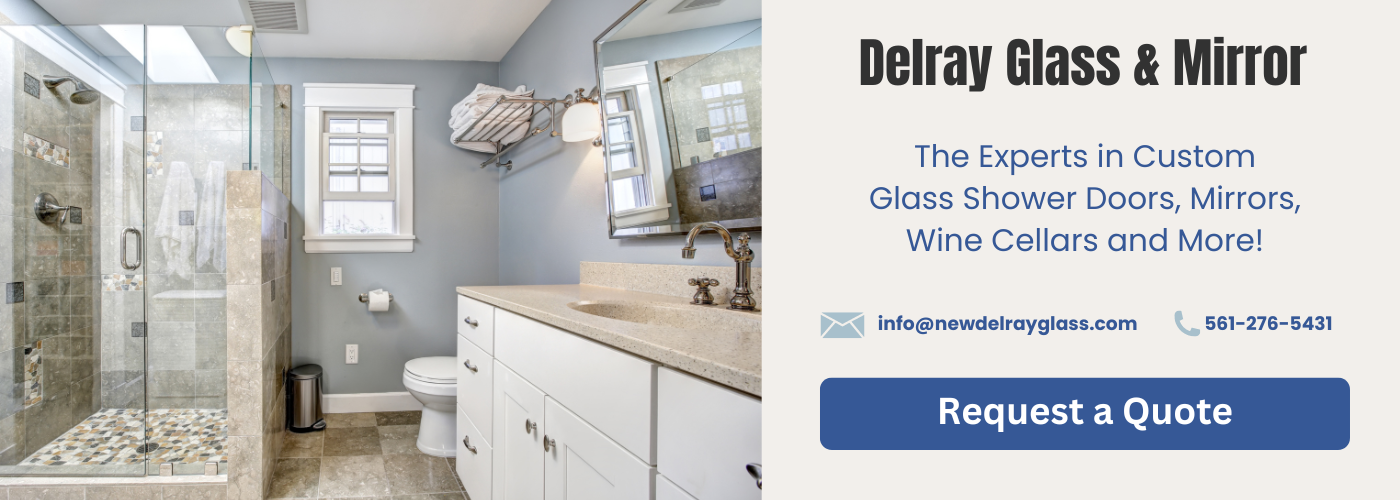
Packaging Materials and Methods
When it comes to the shipment and delivery of custom shower glass, the packaging materials and methods used are crucial to ensure the safety and integrity of the glass during transit. Custom shower glass is particularly vulnerable to impact, scratches, and other forms of damage due to its size, weight, and fragility. Therefore, meticulous attention is given to the packaging process to minimize the risk of damage.
The first step in packaging custom shower glass involves wrapping the glass in protective materials. Soft, cushioning materials such as foam wraps or bubble wraps are commonly used to cover the entire surface of the glass. These materials act as a shock absorber, diminishing the impact of vibrations and bumps that may occur during transportation.
After wrapping, the glass is typically secured in a sturdy, wooden crate. These crates are custom-built to fit the dimensions of the glass, ensuring that there is minimal movement inside the crate during shipping. The interior of the crate may also be lined with additional cushioning materials for extra protection. Sometimes, straps or braces are used inside the crate to hold the glass firmly in place, preventing any shifting that could lead to breaks or cracks.
The use of high-quality packaging materials and the application of these meticulous methods are essential for the safe transport of custom shower glass. By investing in superior packaging, manufacturers and shippers can avoid the costs associated with damage and replacement, ensuring that the glass arrives at its destination in pristine condition. This care and attention to detail in the packaging process reflect the value and delicate nature of custom shower glass, making it imperative for companies to adhere to these practices consistently.
Transportation Modes
Transportation modes for custom shower glass play a crucial role in ensuring the safety and timely delivery of these fragile items. Custom shower glass, due to its size and vulnerability to impact, requires careful consideration of transportation methods. Typically, manufacturers and distributors use specialized trucks equipped with secure racks and padding to prevent any movement that could lead to cracks or breaks. These trucks are often fitted with air ride suspensions to decrease the amount of vibration during transit, which is particularly important over long distances.
For international shipments, custom shower glass may be transported by sea or air, which necessitates additional crating and security measures. Sea freight is generally preferred for its cost-effectiveness, especially for bulk orders, but it takes longer and could expose the glass to varying climatic conditions, which necessitates robust packaging and sometimes climate-controlled containers. Air freight, while more expensive, offers a faster and sometimes safer route for delicate items that are needed urgently.
The choice of transportation mode often depends on the distance, the urgency of delivery, and the budget constraints of the buyer. In all cases, ensuring the integrity of the glass upon arrival is paramount, which makes the collaboration between glass manufacturers, transportation companies, and logistics experts essential to devise the most effective transportation strategy. These professionals must balance speed, cost, and safety to meet the needs of customers while minimizing the risk of damage.
Handling and Safety Procedures
Handling and safety procedures are critical components of the shipping and delivery process for custom shower glass, ensuring that the glass arrives at its destination in perfect condition. Due to its fragility, shower glass requires careful and strategic handling to prevent any damages such as scratches, chips, or breaks, which can occur during transportation.
Firstly, the personnel involved in the handling of custom shower glass are trained in specific techniques designed to safeguard the glass. This includes using the right type of lifting equipment and wearing protective gear such as gloves and goggles to protect both the handlers and the glass. Knowledge of how to properly load and unload the glass is essential, ensuring that the weight is evenly distributed and that the glass is never subjected to undue stress or pressure.
Secondly, during transit, the glass must be securely fastened and supported. Specialized packing materials and restraining systems are used to keep the glass immobile, thereby reducing the risk of movement that could lead to collisions or falls. Adequate spacing between pieces of glass is also crucial to prevent contact that could cause damage.
Furthermore, safety procedures are also in place to deal with unexpected situations such as sharp turns or sudden stops in transportation. These procedures include the use of advanced driving techniques and vehicle modifications that help stabilize the load.
In summary, handling and safety procedures for the shipment and delivery of custom shower glass are meticulously planned and executed to ensure the integrity of the glass from the point of departure to the final destination. These procedures are indispensable for minimizing the risk of damage, thereby saving costs and maintaining customer satisfaction.
Delivery and Installation Services
Delivery and installation services for custom shower glass are crucial components in the process of ensuring that the product reaches the customer in excellent condition and is installed correctly. Custom shower glass is typically delicate and requires careful handling, making the delivery and installation services an integral part of the customer service experience.
The delivery process usually starts with scheduling a delivery date that is convenient for the customer. Companies often use specialized logistics services that have experience in transporting fragile items like glass. During transportation, the glass is securely packed and often crated to prevent any damage.
Once the custom shower glass arrives at its destination, the installation process begins. This is a critical phase as the proper installation of the glass ensures its durability and functionality. Professional installers are usually part of the delivery team. They are trained to handle and install the glass with precision. The installers also ensure that the glass is perfectly aligned and meets all safety standards.
Moreover, during installation, the technicians might provide the customer with maintenance tips and advice on how to care for the glass to ensure it remains in pristine condition. This comprehensive approach to delivery and installation not only enhances customer satisfaction but also reduces the risk of damage and subsequent complaints.
Insurance and Liability
When it comes to the shipping and delivery of custom shower glass, insurance and liability are critical components that ensure both the company and the customer are protected against potential damage or loss during transit. Custom shower glass is a particularly delicate item and requires robust insurance coverage to manage the risks associated with its transportation and handling.
Insurance policies for shipping such items are designed to cover any damage that occurs from the time the glass leaves the manufacturing facility until it is successfully installed in the customer’s home. This insurance is typically borne by the shipping company but the costs are often passed on to the consumer as part of the shipping and handling fees. It’s important for customers to understand the terms of the insurance to know what is covered and what their potential liabilities are.
Liability, on the other hand, pertains to the legal responsibilities that each party holds in the event of damage or accidents. For instance, if the glass is damaged due to improper handling by the delivery team, the company would be liable for replacing or repairing the damaged item. However, if the damage occurs because of customer mishandling after delivery, then the liability may shift to the customer.
For total peace of mind, both parties must carefully review and understand the terms outlined in the insurance and liability clauses before finalizing any shipping arrangements. This ensures any issues that might arise during the shipping and delivery process are addressed promptly and fairly, safeguarding both the interests of the customer and the business.